назначение, устройство и принцип работы газораспределительного механизма двигателя
Автор Павел Александрович Белоусов На чтение 5 мин. Просмотров 88
Современный двигатель внутреннего сгорания имеет сложную конструкцию, и один из ее основных элементов – газораспределительный механизм (ГРМ). Главное назначение газораспределительного механизма – регулировка своевременной подачи топливно-воздушной смеси в моторные цилиндры и вывод из них отработанных газов за счет периодического открытия и закрытия системы клапанов.
Конструкция ГРМ
Газораспределительный механизм двигателя приводит в движение систему клапанов. В различных моделях автомобилей применяются разные технические решения для обеспечения работы ГРМ, но принцип работы у всех одинаковые и обычный газораспределительный механизм состоит из:
- распределительного вала с установленными на него кулачками;
- системы впускных и выпускных клапанов с тарелочками, закрепленными сухарями;
- рычагов (рокеров) или гидрокомпенсаторов;
- шестерни распределительного вала;
- шестерни коленчатого вала;
- ремня или цепи ГРМ;
- дополнительных шестерней и роликов.
Работа системы клапанов
Каждый клапан оснащается пружиной, которая возвращает его в верхнее (закрытое) положение. Специальный кулачок, расположенный на валу, вращаясь, нажимает на клапан, открывая его в нужный момент. Чтобы пружина не соскользнула, на верхней части клапана делается кольцевая проточка, иногда две или три, в неё вставляется сухарь, к которому прикрепляется тарелка с конусовидным отверстием. Собранный из двух частей сухарь тоже имеет конусную поверхность и надежно удерживает тарелку с пружиной. Собранный таким образом клапан называют «засухаренным».
Распределительный вал
Нажимающие на клапана кулачки заставляет двигаться специальный механизм – привод ГРМ, точнее еще один его компонент – газораспределительный вал, который еще называют распредвалом. Кулачки являются его составной частью, а крепится он на специальных опорных шейках в головке блока цилиндров. В зависимости от расположения кулачков на распредвалу, поочередно открываются нужные для нормальной работы двигателя клапана, в чем и состоит принцип работы ГРМ.
Работа системы валов ГРМ
Распредвал приводится в движение посредством коленчатого вала, на конце которого находится шестерня специально подобранного диаметра. Другая шестерня устанавливается на распределительный вал. Передача крутящего момента от коленчатого вала к распределительному передается стальной цепью или ремнем с зубцами под шестерни, который изготовлен из прочной армированной резины. Работа газораспределительного механизма зависит от правильной установки цепи или ремня. В этом случае все клапана открываются в нужный момент, что позволяет воздушно-топливной смеси заходить в цилиндр, сгорать там и выводить отработанные газы. В этом состоит главный принцип работы газораспределительного механизма.
В зависимости от конструкции нажатие на клапан осуществляется непосредственно кулачком на распределительном валу или через рычаг, называемый рокером, на который воздействует кулачок. Назначение и устройство газораспределительного механизма позволяет открывать нужные клапана в момент наступления нужного такта работы двигателя, что обеспечивает ее бесперебойность. Любое нарушение ведёт к сбою в работе вплоть до поломки силового агрегата.
Проблема термического расширения
Устройство ГРМ обеспечивают нормальную работу двигателя, но при этом возникают определенные проблемы. Это касается термического расширения металла, из которого сделаны клапана, поскольку он подвергается воздействию высоких температур при сгорании топлива. При нагревании он удлиняется и не может плотно закрыть отверстие в цилиндре, что существенно снижает компрессию. Чтобы клапан удлинялся не в цилиндр, а вверх, между тарелкой и кулачком или рокером и кулачком делается тепловой зазор в 0,2 мм. Этот зазор выставляется и проверяется специальным щупом, а регулируется винтом или болтом.
В современных двигателях для борьбы с тепловым расширением используются другие детали газораспределительного механизма – гидрокомпенсаторы. В этом случае регулировка клапанов не потребуется, зазор выставляется и регулируется автоматически. Если гидрокомпенсатры начинают постукивать, это говорит о проблемах в их работе, поскольку они не успевают выбирать зазоры. Основные причины появления такой проблемы – поломка самого гидрокомпенсатора, который подлежит замене, реже засор или плохая работа системы смазки.
Видео: Принцип работы газораспределительного механизма
ГРМ в процессе эксплуатации
Чтобы при работе не возникло проблем, нужно периодически проверять газораспределительный механизм мотора. Нужно при помощи щупа контролировать тепловой зазор между клапаном и рычагом распредвала, а при необходимости производить регулировку.
Поскольку газораспределительный механизм предназначен для согласованной работы всех элементов двигателя, то нужно знать, что если в процессе его работы оборвется приводной ремень, то распределительный и коленчатый валы перестают работать синхронно. При этом распредвал может остановиться в положении, при котором один из клапанов останется полностью открытым и тогда двигающийся вверх поршень неизбежно ударит по клапану, который погнется, что приведет к выходу двигателя из строя и серьезному ремонту.
Чтобы избежать подобной ситуации, необходимо вовремя производить замену приводного ремня ГРМ. Периодичность замены указывается производителем в зависимости от конструктивных особенностей двигателя, но в большинстве случаев это рекомендуется делать при пробеге от 60 до 70 тыс. км. Это достаточно сложная операция, которую делают специалисты на СТО, но если у водителя есть нужные навыки, замену можно сделать и самостоятельно. Цепи ГРМ служат гораздо дольше, замена может потребоваться при пробеге от 300 до 400 тыс. км. Особенность двигателей с цепями: при их растяжении они начинают характерно греметь и позванивать, что позволяет определить необходимость замены.
Назначение газораспределительного механизма двигателя – обеспечить синхронную работу поршневой группы и клапанов.
Газораспределительный механизм (ГРМ) Назначение и характеристика
Устройство газораспределительного механизма
Детали газораспределительного механизма выполняют разные функции:
- Распределительный вал открывает и закрывает клапаны.
- Механизм привода приводит распределительный вал в движение с определенной скоростью.
- Клапаны закрывают и открывают впускные и выпускные каналы.
Главными частями ГРМ являются распределительный вал и клапаны. Кулачковый, или распределительный, вал представляет собой элемент, на котором располагаются кулачки. Он приводится в движение и вращается на подшипниках. В момент такта впуска или выпуска кулачки, расположенные на вале, при вращении надавливают на толкатели клапанов.
Располагается механизм ГРМ на головке блока цилиндров. В ГБЦ имеются распределительный вал и подшипники от него, коромысла, клапаны и толкатели клапанов. Верхняя часть головки закрыта клапанной крышкой, установка которой осуществляется с использованием специальной уплотнительной прокладки.
Функционирование газораспределительного механизма
Работа ГРМ полностью синхронна с зажиганием и топливным впрыском. Проще говоря, в момент нажатия педали газа открывается дроссельная заслонка, впускающая поток воздуха во впускной коллектор. В результате образуется топливно-воздушная смесь. После этого начинает работать газораспределительный механизм.
Клапаны приводятся в действие распределительным валом двигателя. Когда повышается частота вращения коленвала, начинает быстрее вращаться и распредвал, что и повышает частоту открытия и закрытия клапанов. В результате возрастают обороты двигателя и отдача от него.
Объединение коленчатого и распределительного валов дает возможность ДВС сжигать именно то количество воздушно-топливной смеси, которое необходимо для функционирования двигателя в том или ином режиме.
Характеристики ГРМ
- Сопротивление впускного и выпускного трактов, ограничивающее быстроходность и снижающее наполнение на более высоких оборотах. Определяется пропускными сечениями клапанов и патрубков, шероховатостью каналов, их изгибом, настройкой (инерционный наддув). При росте сопротивления пики максимума наполнения сдвигаются в область меньшего числа оборотов, что ограничивает мощность ДВС[2].
- Настройки фаз газораспределения (углы опережения открытия впускных и выпускных клапанов/золотников, углы запаздывания закрытия). Эти настройки позволяют частично компенсировать сопротивление впускных и выпускных трактов, сместив максимум наполнения цилиндров от нулевой частоты вращения (при нулевых углах) до частоты, заданной конструктором. Обычно, максимум наполнения соответствует максимуму крутящего момента. На рисунке представлены кривые, соответствующие VVT (1), тихоходной настройке (2), настройке примерно на 0,5 максимальной частоты вращения (3), и скоростной настройке (4) [3].
- Возможность получения компактной камеры сгорания (минимальных размеров) и низкой температуры в районе догорания топливной смеси (искровые ДВС). Это позволяет иметь меньше всего газов в области гашения пламени (что снижает выбросы), и получить высокую степень сжатия без детонации.
- Простота, дешевизна, надёжность, габариты и масса. Влияют на стоимость и надёжность всего двигателя. Этим характеристикам описанные ниже схемы отвечают в различной степени.
Газораспределительным называется механизм, осуществляющий открытие и закрытие впускных и выпускных клапанов двигателя.
Газораспределительный механизм (ГРМ) служит для своевременного впуска горючей смеси или воздуха в цилиндры двигателя и выпуска из цилиндров отработавших газов. В двигателях автомобилей применяются газораспределительные механизмы с верхним расположением клапанов.
Двигатели автомобилей могут иметь газораспределительные механизмы различных типов (рисунок 1), что зависит от компоновки двигателя и, главным образом, от взаимного расположения коленчатого вала, распределительного вала и впускных и выпускных клапанов. Число распределительных валов зависит от типа двигателя.
Рисунок 1 – Типы газораспределительных механизмов, классифицированных по различным признакам
При верхнем расположении распределительный вал устанавливается в головке цилиндров, где размещены клапаны. Открытие и закрытие клапанов производится непосредственно от распределительного вала через толкатели или рычаги привода клапанов. Привод распределительного вала осуществляется от коленчатого вала с помощью роликовой цепи или зубчатого ремня.
Верхнее расположение распределительного вала упрощает конструкцию двигателя, уменьшает массу и инерционные силы возвратно-поступательно движущихся деталей механизма и обеспечивает высокую надежность и бесшумность его работы про большой частоте вращения коленчатого вала двигателя.
Цепной и ременный приводы распределительного вала также обеспечивают бесшумную работу газораспределительного механизма.
При нижнем расположении распределительный вал устанавливается в блоке цилиндров рядом с коленчатым валом. Открытие и закрытие клапанов производится от распределительного вала через толкатели штанги и коромысла. Привод распределительного вала осуществляется с помощью шестерен от коленчатого вала.
При нижнем расположении распределительного вала усложняется конструкция газораспределительного механизма и двигателя. При этом возрастают инерционные силы возвратно-поступательно движущихся деталей газораспределительного механизма. Число распределительных валов в газораспределительном механизме и число клапанов на один цилиндр зависят от типа двигателя.
Так, при большем числе впускных и выпускных клапанов обеспечивается лучшие наполнение цилиндров горючей смесью и их очистка от отработавших газов. В результате двигатель может развивать большие мощность и крутящий момент. При нечетном числе клапанов на цилиндр число впускных клапанов на один клапан больше, чем выпускных.
Замена газораспределительного механизма
Шкив привода распределительного вала находится за пределами ГБЦ. Для того чтобы не происходили утечки масла, на шейке вала расположен сальник. Цепь ГРМ приводит весь механизм газораспределения в действие и надевается с одной стороны на ведомую звездочку или шкив, а с другой передает усилие от коленчатого вала.
От ременного привода клапанов зависит корректное и неизменное расположение коленчатого и распределительного валов относительно друг друга. Даже небольшие отклонения в положении могут стать причиной того, что ГРМ, двигатель выйдут из строя.
Наиболее надежной считается цепная передача, использующая ролик ГРМ, однако существуют некоторые проблемы с обеспечением необходимого уровня натяжения ремня. Главной проблемой, с которой сталкиваются водители и которая характерна для цепи механизма, становится ее обрыв, нередко являющийся причиной загиба клапанов.
К числу дополнительных элементов механизма можно отнести ролик ГРМ, используемый для натяжения ремня. К минусам цепного привода газораспределительного механизма, помимо риска обрыва, относят еще и высокий уровень шума во время работы и необходимость его смены каждые 50-60 тысяч километров пробега.
В зависимости от конструктивных особенностей двигателя автомобиля и газораспределительного механизма в частности количество приводов и их тип могут меняться.
- Цепной привод. Нескольким ранее данный привод был самым распространенным, однако и сейчас используется в ГРМ дизеля. При такой конструкции распределительный вал располагается в головке блока цилиндров, а в движение приводится посредством цепи, ведущей от шестерни. Минус такого привода – сложный процесс замены ремня, поскольку находится он внутри двигателя с целью обеспечения постоянной смазки.
- Шестеренчатый привод. Устанавливался на двигатели тракторов и некоторых автомобилей. Очень надежный, но при этом крайне сложен в обслуживании.
Распределительный вал такого механизма находится ниже блока цилиндров, благодаря чему шестерня распредвала цепляется за шестерню коленчатого вала. Если привод ГРМ такого типа приходил в негодность, двигатель меняли практически полностью.
- Ременной привод. Самый популярный тип, устанавливается на бензиновые силовые агрегаты в легковых автомобилях.
Ременной привод получил свою популярность за счет своих преимуществ по сравнению с аналогичными видами приводов.
- Несмотря на то что производство таких конструкций сложнее, чем цепных, стоит она значительно дешевле.
- Не требует постоянной смазки, благодаря чему привод был вынесен на внешнюю сторону силового агрегата. Замена и диагностика ГРМ в результате этого значительно облегчились.
- Поскольку в ременном приводе металлические части не взаимодействуют друг с другом, как в цепном, то уровень шума в процессе его работы снизился в разы.
Несмотря на большое количество плюсов, есть у ременного привода и свои минусы. Срок эксплуатации ремня в несколько раз ниже, чем цепи, что становится причиной частой его замены. В случае обрыва ремня с большой вероятностью придется делать ремонт всего двигателя.
Полная замена ремня производится каждые 50-70 тысяч километров пробега автомобиля. Ее могут проводить и чаще в случае повреждения или появления следов расслоения и трещин.
В зависимости от типа ГРМ меняется и сложность процедуры замены ремня. На сегодняшний день в автомобилях используются два типа механизма газораспределения – с двумя (DOHC) или одним (SOHC) распределительными валами.
Для того чтобы провести замену ремня ГРМ типа SOHC, достаточно иметь под рукой новую деталь и набор отверток и ключей.
Сперва снимается защитный чехол с ремня. Крепится он либо на защелки, либо на болты. После снятия чехла открывается доступ к ремню.
Прежде чем ослаблять ремень, выставляются метки ГРМ на шестерне распредвала и коленвале. На коленчатом вале метки размещаются на маховике. Вал проворачивают до тех пор, пока метки ГРМ на корпусе и на маховике не совпадут друг с другом. Если все метки совпали друг с другом, приступают к ослаблению и снятию ремня.
Для того чтобы снять ремень с шестерни коленчатного вала, необходимо демонтировать шкив привода ГРМ. С этой целью автомобиль поднимается домкратом и с него снимается правое колесо что дает доступ к болту шкива. На некоторых из них находятся специальные отверстия, через которые можно зафиксировать коленвал.
Доступ к ремню ГРМ полностью открывается, и можно приступать к его снятию и замене. Новый одевается на шестерни коленвала, затем цепляется за водяной насос и одевается на шестерни распредвала. За натяжной ролик ремень заводят в самую последнюю очередь. После можно возвращать все элементы на место в обратном порядке. Останется только натянуть ремень при помощи натяжителя.
Прежде чем запускать двигатель, желательно провернуть несколько раз коленчатый вал. Делают это для проверки совпадения меток и после проворачивания вала. Только после этого запускается двигатель.
На автомобиле с системой DOHC ремень ГРМ заменяется немного по-другому. Сам принцип смены детали аналогичен вышеописанному, однако доступ к ней у таких машин сложнее, поскольку имеются закрепленные на болтах защитные чехлы.
В процессе совмещения меток стоит помнить о том, что распределительных валов в механизме два, соответственно, метки на обоих должны полностью совпасть.
У таких автомобилей, помимо направляющего ролика, имеется и опорный ролик. Однако, несмотря на наличие второго ролика, ремень заводится за направляющий ролик с натяжителем в самую последнюю очередь.
После того как новый ремень будет установлен, проверяется соответствие меток.
Одновременно с заменой ремня меняются и ролики, поскольку их срок эксплуатации совпадает. Также желательно проверить состояние подшипников жидкостного насоса, чтобы после проведения процедуры установки новых деталей ГРМ выход из строя помпы не стал неприятной неожиданностью.
С поршневым управлением газораспределения
Механизм газораспределения с поршневым управлением впуском и выпуском (он же — оконный газораспределительный механизм) применяется на двухтактных двигателях с кривошипно-камерной продувкой. В нём фазы газораспределения задаются за счёт осуществляемого непосредственно поршнем открытия и закрытия окон в стенке цилиндра.
Впускное окно обычно открывается при положении коленчатого вала, в котором поршень не доходит 40—60° до нижней мёртвой точки (по углу поворота коленвала), а закрывается спустя 40—60° после её прохождения, что даёт достаточно узкую фазу впуска — не более 130—140°.
На высокофорсированных спортивных моторах открытие впускного окна может производиться за 65—70° до НМТ, что расширяет фазу впуска, но при этом работа двигателя на малых и средних оборотах становится неустойчивой, значительно увеличивается непроизводительный расход топлива из-за обратного выброса топливной смеси в атмосферу.
Выпускное окно открывается примерно за 80-85° до достижения поршнем нижней мёртвой точки, а закрывается спустя 80-85° после её прохождения, что даёт длительность фазы выпуска около 160—165°. Фаза продувки имеет длительность около 110…125°.
Симметричность фаз газораспределения при поршневом управлении впуском и выпуском обусловлена тем, что взаимное расположение поршня и окон в стенке цилиндра одинаково как при ходе вверх, так и при ходе вниз. Это является недостатком, поскольку для оптимальной работы двигателя как минимум фаза впуска должна быть асимметрична, что при чистом поршневом управлении газораспределением недостижимо.
В двухтактных двигателях большого объёма (тепловозные, морские, авиационные, танковые) либо на один цилиндр два поршня, движущихся навстречу друг другу, один из которых открывает впускные окна, а второй — выпускные (прямоточная продувка), либо через окна в стенке цилиндра производится только впуск, а выпуск осуществляется с помощью клапана в головке цилиндров (клапанно-щелевая продувка), при этом также достигается более оптимальная продувка.
В роторно-поршневых двигателях также как правило используется управление газораспределением поршнем (ротором), играющим в данном случае роль золотника.[4]
Механизм газораспределения с поршневым управлением впуском и выпуском (он же — оконный газораспределительный механизм) применяется на двухтактных двигателях с кривошипно-камерной продувкой. В нём фазы газораспределения задаются за счёт осуществляемого непосредственно поршнем открытия и закрытия окон в стенке цилиндра.
В двухтактных двигателях большого объёма (тепловозные, морские, авиационные, танковые) либо на один цилиндр два поршня, движущихся навстречу друг другу, один из которых открывает впускные окна, а второй — выпускные (прямоточная продувка), либо через окна в стенке цилиндра производится только впуск, а выпуск осуществляется с помощью клапана в головке цилиндров (клапанно-щелевая продувка), при этом также достигается более оптимальная продувка.
В роторно-поршневых двигателях также как правило используется управление газораспределением поршнем (ротором), играющим в данном случае роль золотника. [4]
С клапанным управлением газораспределением
Управление газораспределением осуществляется при помощи тарельчатых клапанов, как правило имеющих привод от распределительного вала. Эта система наиболее распространена на современных четырёхтактных двигателях, а также мощных двухтактных (с клапанно-щелевой продувкой, имеются только выпускные клапана).
В данной конструкции ГРМ используется клапан, состоящий из тарелки (головки) и стержня (стебля), который служит для открытия и закрытия впускных и выпускных каналов. Главное преимущество тарельчатого клапана, позволившее ему достичь преимущественного распространения в данной области — простота обеспечения герметичности: под воздействием давления в камере сгорания его тарелка плотно прижимается к седлу, поэтому для исключения утечки газов вполне достаточно тщательно притереть эти детали друг к другу, причём усилие, создаваемое давлением в камере сгорания, направлено по оси стержня клапана и не мешает ему перемещаться вдоль направляющей.
При открытии клапана он смещается относительно седла на расстояние, называемое высотой подъёма клапана. При этом открывается определённое проходное сечение, определяемое величиной высоты подъёма, размерами и формой клапана. В большинстве случаев впускные клапана имеют большее проходное сечение, чем выпускные.
Ранее, примерно до 1950-х годов, клапаны обычно изготавливали из обычной углеродистой или низколегированной инструментальной стали (например, хромистой 40Х), однако по мере совершенствования двигателей и повышения их степени форсирования появилась необходимость применения как минимум для выпускных клапанов, температура которых может достигать 600—850 °С, специальных легированных жаростойких сталей, например сильхромовой (40Х10С2М / ЭИ107, 40Х9С2 / ЭСХ8), X45CrNiW189, X53CrMNi219, и т. п.
Впускные клапана обычно имеют температуру не выше 300—400 °С и выполняются из хромистой, хромованадиевой или хромоникелевой сталей. Иногда с целью удешевления из жаростойкой стали изготавливается только тарелка (головка) клапана, а стержень — из обычной инструментальной, также на тарелках выпускных клапанов иногда может производиться дополнительная наплавка слоя твёрдого жаростойкого сплава, повышающего срок службы клапана.
В двигателях с большой тепловой напряжённостью камеры сгорания могут применяться клапана с полыми стержнями, заполненными натрием — при работе двигателя натрий плавится и, испаряясь, улучшает теплоотвод от клапана. В последнее время могут использоваться клапана из титановых сплавов, сочетающие жаростойкость с лёгкостью, что позволяет уменьшить инерцию деталей ГРМ.
Тарелка (головка) клапана может иметь плоскую (Т-образную), выпуклую или тюльпанообразную (обтекаемую, с плавным переходом к стержню) форму. Клапана с выпуклой головкой иногда используются в качестве выпускных благодаря большой жёсткости и лучшей обтекаемости со стороны цилиндра, что особенно актуально в нижнеклапанном моторе.
Тюльпанообразные клапана ранее часто устанавливались на впуске при большом диаметре клапана, так как считалось, что обтекаемая форма головки снижает сопротивление потоку воздуха, но впоследствии, примерно с 1980-х годов, от их использования отказались, так как они не давали значительного эффекта, или даже при той же величине подъёма ухудшали наполнение цилиндров по сравнению с обычными, при большей сложности изготовления.
Головка клапана имеет коническую рабочую поверхность — запорную фаску, плотно притёртую к ответной фаске седла (гнезда) клапана. Фаска на головке клапана выполняется под углом 30° или 45°. Фаска в 45° даёт меньшее проходное сечение при том же подъёме, чем фаска в 30°, однако облегчает центровку клапана в седле и способствует повышению его жёсткости, поэтому 30-градусная фаска применяется ограниченно, обычно на впускных клапанах высокофорсированных и спортивных двигателей.
В некоторых случаях может применяться двойная фаска. Фаска подвергается шлифовке, а затем плотно притирается к седлу (гнезду). На нижнем (хвостовом) конце стержня клапана выполняются кольцевые проточки, предназначенные для крепления тарелок клапанных пружин, обычно осуществляемого при помощи конических сухарей (реже — поперечной шпилькой или на резьбе).
Иногда для повышения срока службы клапана тарелка клапанной пружины оснащается упорным подшипником, допускающим свободное вращение клапана вокруг своей оси при работе двигателя.
Ранее на хвостовой части стержня клапана иногда также выполняли кольцевую выточку под предохранительное кольцо, не дающее клапану провалиться в цилиндр, если лопнет его пружина или произойдёт случайное выпадение сухарей при работе двигателя.[7][8]
Сёдла (гнёзда) клапанов выполняются либо непосредственно в материале блока цилиндров (у нижнеклапанных моторов) или головки цилиндров, либо в виде запрессованных в них отдельных деталей из легированного чугуна, бронзы или жаростойкой стали (только выпускных клапанов, либо и впускных, и выпускных), иногда с наплавкой износостойкого кобальтового сплава типа сормайт.
[7] Обычно седло имеет одну фаску с углом в 45°, или две фаски — верхнюю с углом в 30°, служащую переходом от основной фаски к стенке камеры сгорания, и основную в 45°. Иногда выполняется также нижняя фаска с углом порядка 60°, применение которой снижает сопротивление седла потоку воздуха.
Направляющие втулки клапанов служат для обеспечения их точной посадки в сёдла, изготавливаются из чугуна, алюминиевой бронзы или металлокерамических антифрикционных композиций (бронзографитовой и других).
Для уменьшения расхода масла через зазор между направляющей клапана и его стержнем либо на сам стержень клапана одевается маслоотражательный колпачок из маслостойкой резины, либо на его направляющую устанавливается сальник с кольцевой пружинкой (маслосъёмный колпачок).[7][8]
Клапанные пружины обеспечивают закрытие клапана и его плотную посадку в седло, воспринимают усилия, возникающие при работе ГРМ. При сборке клапанного механизма пружина получает предварительную затяжку, величина которой является важным параметром, влияющим на качество работы двигателя.
Если пружина в засухаренном состоянии не развивает должного усилия, указанного в технической документации — возникают отставание («подвисание») и подскакивание клапана при его закрытии, нарушающие фазы газораспределения и ухудшающие наполнение цилиндров горючей смесью, из-за чего двигатель не будет развивать полной мощности и не обеспечит паспортных динамических характеристик автомобиля.
При полностью закрытом клапане остаточной силы пружины должно хватать для удержания контакта между кулачком распределительного вала и контактирующей с ним деталью ГРМ (толкателем, коромыслом, рокером), что позволяет сохранить заданную конструкторами продолжительность открытия клапана и устранить ударные нагрузки в приводе клапанов, быстро выводящие его из строя.
Как правило, клапанные пружины изготавливаются из легированной высокоуглеродистой стали (марганцовистой, кремнемарганцовистой, хромоникелеванадиевой) холодной навивкой с последующими термообработкой и дробеструйным наклёпом для повышения срока службы.
Иногда применяются по две пружины на клапан, расположенные одна внутри другой, причём наружная и внутренняя пружина имеют разное направление витков для предотвращения заклинивания внутренней пружины витками внешней. Применение таких сдвоенных пружин позволяет несколько уменьшить габариты узла за счёт меньшей общей высоты двух пружин по сравнению с одинарной при том же усилии, а также служит в качестве страховки на случай поломки одной из пружин, тем самым повышая надёжность и безотказность работы двигателя. Также иногда клапанная пружина может устанавливаться не на самом клапане, а в толкателе (пример — дизель ЯАЗ-204).[7]
В очень редких случаях вместо винтовых клапанных пружин могут применяться торсионные в виде работающих на скручивание стержней (некоторые моторы фирмы Panhard, также некоторые мотоциклетные двигатели Honda), плоские, спиральные или витые шпилечные пружины (некоторые мотоциклетные двигатели)[источник не указан 29 дней].
В большинстве случаев в клапанном механизме для управления клапанами используется выполненный из чугуна или легированной стали кулачковый распределительный вал, имеющий опорные шейки, служащие для установки вала в подшипниках его постели, и кулачки с различным профилем, определяющим фазы газораспределения двигателя.
Обычно на один цилиндр приходится по два кулачка распределительного вала (один впускной и один выпускной), однако встречаются и иные варианты. Кроме того, распределительных валов может быть более одного. Привод распределительного вала осуществляется от коленчатого вала двигателя, причём у четырёхтактных моторов его частота обращения равна половине частоты обращения коленчатого вала, а у двухтактных — равна ей.
С золотниковым управлением газораспределением
В двухтактных двигателях
Золотниковое газораспределение было применено ещё на двухтактном газовом двигателе Ленуара, считающемся первым в мире коммерчески успешным двигателем внутреннего сгорания (1859 год). Его газораспределительный механизм с двумя коробчатыми золотниками был полностью скопирован с парораспределительного механизма паровых машин, причём при помощи золотников осуществлялся как впуск газовоздушной рабочей смеси, так и выпуск отработанных газов.
Применение золотникового газораспределения на лёгких двухтактных двигателях современного типа (с кривошипно-камерной продувкой) прослеживается как минимум с 1920-х годов, однако по-настоящему удачная реализация этого принципа была осуществлена лишь в начале 1950-х годов восточногерманским инженером Даниэлем Циммерманом на спортивно-гоночных мотоциклах MZ, а затем в 1960-х — 70-х годах схожие решения стали появляться и на некоторых серийных мотоциклах марок Jawa, Yamaha, Suzuki, Kawasaki и других.
На двухтактных моторах с золотниковым управлением газораспределением для управления впуском используется золотник с приводом от коленчатого вала — вращающийся дискового или цилиндрического (кранового) типа либо имеющий возвратно-поступательное движение пластинчатого типа.
Золотник тем или иным образом осуществляет открывание и закрывание впускного канала двигателя, управляя тем самым длительностью впуска. Благодаря этому удаётся сделать фазу впуска асимметричной относительно НМТ (как правило, начинается за 130—140° до НМТ и заканчивается за 40—50° после) и увеличить её длительность до 180—200°, тем самым улучшив наполнение цилиндра.
Некоторые варианты реализации золотникового управления газораспределением позволяют даже изменять фазы газораспределения непосредственно во время работы двигателя. Выпуском как правило продолжает управлять поршень, открывающий выпускное окно (окна).
С аналогичной целью во впускном тракте двигателя может устанавливаться автоматически срабатывающий на перепад давления клапан лепесткового или мембранного типа (Yamaha и др.).
В начале 1950-х годов на пермском моторостроительном заводе № 19 под руководством В. В. Полякова были разработаны и выпущены небольшой серией двухтактные пятицилиндровые звездообразные авиамоторы ВП-760, ВП-1300 и ВП-2650 с газораспределением установленным в картере вращающимся золотником и продувкой двухступенчатыми поршнями в форме перевёрнутой буквы Т (узкая часть рабочая, широкая — нагнетательная), которые предназначались для применения в легкомоторной авиации. [5][6]
Опыты с газораспределением вращающимся золотником велись в начале 1990-х годов фирмой Lotus применительно к двухтактному автомобильному двигателю с продувкой от приводного компрессора, причём, в отличие от обычного двухтактного двигателя с клапанно-щелевой продувкой, свежий воздух подавался в верхнюю часть цилиндра через золотник, а отработавшие газы удалялись через окна в нижней части цилиндра (у обычного двигателя с клапанно-щелевой продувкой воздух подаётся через окна в средней части цилиндра, а газы удаляются через клапан в головке блока).
Золотник имел вид постоянно вращающегося вокруг своей оси полого цилиндра — ротора — с окнами в стенках, внутри которого располагался также имевший вид полого цилиндра статор с продольной перегородкой, поворот которого относительно ротора, осуществляемый электронной системой, управлял фазами газораспределения.
Такое устройство газораспределения позволило вместо обычно используемого на дизелях с клапанно-щелевой продувкой непосредственного впрыска использовать более дешёвый вариант системы питания, с форсункой низкого давления, распыляющей топливо внутрь золотника, откуда рабочая смесь вдувалась внутрь цилиндра через впускное окно.
В четырёхтактных двигателях
Золотниковое газораспределение с коробчатыми, поршневыми или вращающимися (крановыми) золотниками, так или иначе связанными с распределительным валом и осуществляющими открытие и закрытие впускных и выпускных окон, использовалось на некоторых четырёхтактных двигателях, но не получило широкого распространения из-за целого ряда трудностей на пути практической реализации данного принципа, в частности — проблемы с уплотнением золотников, особенно работающего на выпуск и в силу этого находящегося под большим давлением горячих отработанных газов.
Газораспределение коробчатым золотником, аналогичным золотникам паровых машин, было применено ещё на первом в мире четырёхтактном двигателе внутреннего сгорания, сконструированном Н. Отто (1861 год), и достаточно широко использовалось на тихоходных стационарных двигателях XIX — самого начала XX века.
Управление газораспределением имеющими возвратно-поступательное движение поршневыми золотниками является фактически стандартным на паровых машинах и мощных поршневых насосах, некоторые конструкторы пытались приспособить его и к двигателю внутреннего сгорания, однако без большого успеха — перемещение золотника оказывалось весьма затруднено из-за большого давления газов, создававшего огромную силу трения между золотником и стенками золотниковой коробки, не говоря уже о проблемах с прорывом газов через уплотнения.
Несколько больший успех выпал на долю газораспределительных механизмов с вращающимся (крановым) золотником. Этот вариант газораспределения привлекал конструкторов благодаря бесшумности работы по сравнению с обычными тарельчатыми клапанами (стук которых при работе ГРМ был большой проблемой для двигателей начала XX века), возможности получить потенциально более высокую пропускную способность по сравнению с клапанным газораспределением и упростить ГРМ за счёт использования одного золотника на цилиндр, работающего и на впуск, и на выпуск, или даже одного на каждую пару цилиндров, а также устранить из камеры сгорания один из наиболее опасных очагов детонации — выпускной клапан (что, опять же, было весьма актуально в начале XX века, когда доступное топливо имело очень низкое октановое число).
Первый патент на газораспределение вращающимся золотником был получен британской фирмой Crossley в середине 1880-х годов. Основанные на нём тихоходные газовые двигатели пользовались популярностью в качестве стационарных и выпускались этой фирмой с 1886 по 1902 год.
Пик популярности данной конструкции в автомобильных двигателях пришёлся на начало 1910-х годов, когда, следуя последней моде, свои варианты золотникового газораспределения представил целый ряд фирм, выпускавших дорогостоящие автомобили, таких, как Itala (Италия, 1911), Darraq (Франция, 1912), впоследствии Minerva (Бельгия, 1925).
Сравнительно удачные конструкции двигателей с газораспределением коническим вращающимся золотником создавались британцами Р. Кроссом и Ф. Аспином в 1930-х — 1950-х годах, находили применение на гоночных автомобилях, однако в массовое производство так и не попали, в том числе — из-за нерешённых проблем с уплотнением и смазкой золотника.
В те же годы экспериментировал с золотниковым газораспределением германский инженер Ф. Ванкель в сотрудничестве с фирмами BMW, DVL, Daimler-Benz, Lilienthal и Junkers, однако, не добившись решительного успеха, он переключился на работу над проектом роторно-поршневого двигателя, в чём весьма преуспел.
В 1950-х годах в СССР были построены опытные двигатели с золотниковым газораспределением на базе серийных моторов «Москвич-400» (4-цил.) и ЗИС-120 (6-цил.), имевшие крановые золотники, установленные в головке блока и вращающиеся вокруг оси, параллельной оси коленчатого вала.
По сравнению с нижнеклапанными, двигатели с золотниковым газораспределением имели лучшую наполняемость цилиндров и, соответственно, более высокую удельную мощность — например, на двигателе «Москвича» прибавка в мощности по сравнению с серийным составила 8 %.
Однако при этом ощутимо увеличивался расход масла из-за проблем с уплотнением золотника, двигатель работал с заметным дымлением. Кроме того, в конце такта сжатия и во время рабочего хода поршня золотник испытывал большое трение из-за давления на него уплотняющего башмака, находящегося под давлением выхлопных газов, что значительно повышало потери на трение, а на шестицилиндровом двигателе даже привело к обрыву трёхрядной цепи привода ГРМ в ходе испытаний. Обеспечить требуемый моторесурс двигателям с золотниковым газораспределением так и не удалось.[4]
Примерно тогда же британская фирма Norton выпустила некоторое количество гоночных мотоциклов с золотниковым газораспределением, но в 1954 году полностью прекратила работы в этом направлении.
Необычный автомобильный двигатель с Х-образным расположением цилиндров и газораспределением вращающимися золотниками разработала в середине 1970-х годов компания Esso, которая привлекла к работам Р. Кросса, однако двигатель не показал значительных преимуществ перед традиционными[источник не указан 29 дней].
Разновидностью золотникового иногда считают гильзовое газораспределение, рассмотренное отдельно ниже по тексту.
Золотниковое газораспределение было применено ещё на двухтактном газовом двигателе Ленуара, считающемся первым в мире коммерчески успешным двигателем внутреннего сгорания (1859 год). Его газораспределительный механизм с двумя коробчатыми золотниками был полностью скопирован с парораспределительного механизма паровых машин, причём при помощи золотников осуществлялся как впуск газовоздушной рабочей смеси, так и выпуск отработанных газов.
Управление этапами газораспределения
Современные модели двигателей претерпели значительные изменения, получив новые управляющие системы, в основе которых лежат микропроцессоры – так называемые ЭБУ. В сфере моторостроения основной задачей стало не только увеличение мощности, но и экономичность выпускаемых силовых агрегатов.
Повысить эксплуатационные показатели двигателей, снизив при этом расход топлива, удалось только с использованием систем контроля ГРМ. Двигатель с такими системами не только потребляет меньше топлива, но и не теряет в мощности, благодаря чему их стали использовать повсеместно при производстве автомобилей.
Принцип работы таких систем заключается в том, что они контролируют скорость вращения распределительного вала ГРМ. По сути, клапаны открываются немного раньше за счет того, что распредвал проворачивается в направлении вращения. Собственно, в современных двигателях распределительный вал больше не вращается относительно коленчатого вала с неизменной скоростью.
Основной задачей остается максимально эффективное наполнение цилиндров двигателя в зависимости от выбранного режима его работы. Такие системы отслеживают состояние двигателя и корректируют подачу топливной смеси: к примеру, при холостом ходе ее объемы сводятся практически к минимуму, поскольку топливо в больших количествах не требуется.
Последствия обрыва или ослабления ремня ГРМ
В случае если цепь ГРМ рвется, повышается уровень шума во время работы двигателя. В целом такая неприятность не становится причиной чего-то невыполнимого в плане ремонта, в отличие от ремня газораспределительного механизма. При ослаблении ремня и его перескакивании через один зуб шестерни происходит небольшое нарушение нормального функционирования всех систем и механизмов.
Самый безобидный вариант – это столкновение поршня и клапана. Силы удара будет достаточно для изгиба клапана. Иногда ее хватает для изгиба шатуна или полного разрушения поршня.
Одной из самых серьезных поломок автомобиля является обрыв ремня ГРМ. Двигатель в таком случае придется либо подвергать капитальному ремонту, либо полностью менять.
Обслуживание ремня ГРМ
Уровень натяжения ремня и его общее состояние – один из самых часто проверяемых при техническом обслуживании автомобиля факторов. Периодичность проверки зависит от конкретной марки и модели машины. Процедура контроля натяжения ремня ГРМ: двигатель осматривается, снимается защитный чехол с ремня, после чего последний проверяется на скручивание.
При техобслуживании автомобиля визуальный осмотр ремня доступен даже неопытным автолюбителям. Труднее определить растяжение цепного привода. Если на ремне видны трещины, значительные потертости, нитки корда, замена детали обязательна. Проверить натяжение ремня можно поворотом плоскости пальцами на 90 градусов.
Опытные владельцы машин, обладающие опытом ремонта, проводят замену ремня самостоятельно. Тонкими моментами операции становится совмещение меток шестерней валов (коленчатого, распределительного) с прорезями кожуха привода, определение пригодности натяжных роликов к дальнейшей эксплуатации, правильная регулировка натяжения.
При выборе зубчатого ремня для замены, кроме соответствия размеров, нужно обращать внимание на материал привода. Лучшими считаются ремни из композитных материалов (тяговый слой из арамида, полиэстера, полиамида, наружное покрытие бутадиен-нитрильным каучуком). Такие производители зубчатых ремней как ContiTech, «Бош», Dayco, Habasit гарантируют для своей продукции:
- износостойкость;
- малую шумность;
- высокие показатели эластичности, прочности на разрыв;
- способность работать при повреждениях (незначительных трещинах, потертостях).
Операции измерения теплового зазора, диагностику направляющих втулок (определение зазора между клапанами и втулками) нужно доверить специалистам. Для этого требуется разборка ГРМ, использование специальных измерителей. Обращения в автосервис не избежать при сбоях фаз газораспределения (требующих регулировки), текущих ремонтах седел клапанов, заменах распределительных шестерен, направляющих втулок.
Основные работы:
- проверка стабильности состояния и подтягивание креплений (крепежные работы) опоры двигателя к раме, головки цилиндров и поддона картера к блоку, фланцев впускного и выпускного трубопроводов и других соединений;
- проверка технического состояния или работоспособности (контрольные работы) кривошипно-шатунного и распределительного механизмов;
- регулировочные работы и смазка.
Крепежные работы
Для предотвращения пропуска газов и охлаждающей жидкости через прокладку головки цилиндров необходимо периодически проверять крепление головки ключом с динамометрической рукояткой с определенным усилием и последовательностью. Момент затяжки и последовательность подтягивания гаек устанавливают автомобильные заводы.
Чугунную головку цилиндров крепят, когда двигатель находится в нагретом состоянии, а головку из алюминиевого сплава – в холодном.
Необходимость подтягивания крепления головок из алюминиевого сплава в холодном состоянии объясняется неодинаковым коэффициентом линейного расширения материала болтов и шпилек (сталь) и материала головки (алюминиевый сплав). Поэтому подтягивание гаек на горячем двигателе не обеспечивает после его остывания необходимой плотности прилегания головки цилиндров к блоку.
Затяжку болтов крепления поддона картера во избежание деформации картера, нарушения герметичности проверяют также с соблюдением последовательности, т.е. поочередным подтягиванием диаметрально противоположных болтов.
Контроль состояния КШМ и ГРМ
Техническое состояние этих механизмов можно определять:
- по расходу (угару) масла в эксплуатации и падению давления в системе смазки;
- по изменению давления (компрессии) в цилиндрах двигателя в конце хода сжатия;
- по разрежению во впускном трубопроводе;
- по количеству газов, прорывающихся в картер двигателя;
- по утечке газов (воздуха) из цилиндров;
- наличию стуков в двигателе.
Угар масла в малоизношенном двигателе незначителен и может составлять 0,1-0,25 л/100 км пробега. При значительном общем износе двигателя угар может достигать 1л/100 км и более, что обычно сопровождается сильным дымлением.
Давление в масляной системе двигателя должно быть в пределах, установленных для данного типа двигателя и применяемого сорта масла. Снижение давления масла на малых оборотах коленчатого вала прогретого двигателя указывает на наличие недопустимых износов подшипников двигателя или неисправности в системе смазки.
Падение давления масла по манометру до 0 указывает на неисправность манометра или редукционного клапана.
Повышенное давление в системе смазки может возникнуть в результате большой вязкости или засорения масляной магистрали.
Компрессия служит показателем герметичности цилиндров двигателя и характеризует состояние цилиндров, поршней и клапанов. Герметичность цилиндров может быть определена компрессометром.
Компрессию проверяют после предварительного прогрева двигателя до 70-80 ºС при вывернутых свечах. Установив резиновый наконечник компрессометра в отверстие свечи, провертывают стартером коленчатый вал двигателя на 10-12 оборотов и записывают показания компрессометра. Проверку повторяют 2-3 раза для каждого цилиндра.
Если величина компрессии на 30-40 % ниже нормы, это указывает на наличие неисправностей (поломку или пригорание поршневых колец, негерметичность клапанов или повреждение прокладки головки цилиндров).
Разрежение во впускном трубопроводе двигателя замеряют вакуумметром. Величина разрежения у работающего на установившемся режиме двигателей может изменяться не только от изношенности цилиндро-поршневой группы, но и от состояния деталей газораспределения, установки зажигания и регулировки карбюратора.
Таким образом, данный метод контроля является общим и не позволяет выделить ту или иную неисправность по одному показателю.
Количество газов, прорывающихся в картер двигателя, изменяется в результате неплотности сопряжений цилиндр-поршень-поршневое кольцо, увеличивающейся по мере изнашивания указанных деталей. Количество прорывающихся газов замеряют при полной нагрузке двигателя.
Источник информации Сайт: http://autonotes.info/grm-gazoraspredelitelnyj-mexanizm/
Назначение, устройство и работа ГРМ
Содержание
Введение. 2
1.Назначение, устройство и работа ГРМ… 5
2.Неисправности ГРМ… 10
3.Ремонт стержня клапана правкой. 13
3.1 Хромирование. 16
3.2 Осталивание. 18
3.3 Железнение. 20
3.4 Шлифование. 22
4.Разборка ГРМ… 25
5.Инструмент и оборудование. 27
6.Охрана трада. 28
7.Заключение. 30
8.Список литературы.. 31
Введение
В процессе эксплуатации автомобиля его надежность и другие эксплуатационные качества постоянно снижаются в следствии изнашивания деталей, а так же коррозии и усталость металла, из которого они изготовлены. Что бы продлить срок службы автомобиля и его агрегатов следует своевременно проводить техническое обслуживание.
В Российской Федерации принято планово предупредительная система технического обслуживания, предусматривающая обязательное выполнение с заданной периодичностью определенного комплекта работ. Такое техническое обслуживание направленно на поддержание автомобиля в исправном состоянии. Сущность системы технического обслуживания заключается в том, что этот объем работ выполняется в плановом порядке с целью предотвращения возникновения технических неисправностей
По периодичности, перечню и трудоемкости выполнения работ техническое обслуживание делиться на следующие виды:
1. Ежедневное техническое обслуживание
2. Техническое обслуживание №1
3. Техническое обслуживание №2
4. Сезонное обслуживание
1 Ежедневное техническое обслуживание.
Выполняется перед выездом автомобиля на линию и после и после въезда. Служит для обеспечения технического контроля автомобиля, направленное на обеспечение безопасности и поддержании надежности автомобиля, включает общий контроль, направленный на обеспечение безопасности движения, поддержание надлежащего внешнего вида, заправку топливом, маслом и охлаждающей жидкостью.
2 Техническое обслуживание №1
Во время технического обслуживания №1, выполняют все работы входящие в ежедневное техническое обслуживание, а так же дополнительно проводят:
· Контрольно – диагностические работы;
· Контрольно – крепежные работы;
· Смазочные и очистительные работы.
Контрольно – диагностические работы:
При общей диагностике проверяют люфты рулевого колеса и в шарнирах рулевых тяг при помощи прибора для проверки рулевых управлений. Эффективность действие рабочего стояночного тормоз на стенде. Работу приборов освещения и сигнализации, правильность установки зеркал заднего вида и состояния шин и давления в них при помощи манометра.
Контрольно – крепежные и регулирования работы:
Проверяют крепления двигателя к раме и оборудования к двигателю, проверяют натяжение ремней вентилятора, генератора, компрессора и насоса гидроусилителя. Выявляют в состояние приборов в системе питания и герметичность их соединений. Проверяют действие запорных механизмов, а так же крепления кузова автомобиля к раме, крыльев, подножек. Проверяют состояние рамы, узлов и деталей подвески, сцепного устройства, колеса. Проверяют уровень электролита ваккумуляторной батареи при необходимости доливают дистиллированную воду, так же проверяют крепления контактов с полюсными выводами.
Смазочные и очистительное работы:
Проверяют уровень масла в картарахогрегатов согласно карте смазки, проверяют уровень тормозной жидкости в бачке, прочищаются сапуныкоробки передач и главной передачи. Промываются воздушные фильтра, а так же заменяется масло и масленые фильтра в двигатели.
Назначение, устройство и работа ГРМ
Газораспределительный механизм — механизм своевременного распределения впуска горючей смеси и выпуска отработавших газов в цилиндрах двигателявнутреннегосгорания. Осуществляется путём перекрытия и открытия поршнямипродувочныхоконцилиндров в двухтактныхдвигателях, либо открытия и закрытия впускных и выпускных клапанов в четырехтактных двигателях, имеющих привод от распределительного вала, распредвала и кулачковогомеханизма. Распредвал имеет жёсткую синхронизацию вращения с коленвалом, реализованную с помощью шестерёнчатой, зубчаторемённойилицепнойпередачи.
Основными элементами газораспределительного механизма являются:
· распределительный вал;
· рычаги;
· ремень газораспределительного механизма или цепь;
· клапаны с мощными пружинами впускные и выпускные;
· впускные и выпускные каналы.
Распределительный вал двигателя внутреннего сгорания находится в головке блока цилиндров, а точнее — вдоль ее верхней части. Ключевыми элементами распределительного вала являются кулачки, число которых равно общему количеству впускных и выпускных клапанов. Распределительный вал расположен относительно клапанов таким образом, что каждому клапану соответствует свой кулачок. При вращении вала кулачки поочередно давят на соответствующие клапаны, благодаря чему те своевременно открываются. Когда кулачок перестает давить на клапан распределительный вал вращается с большой скоростью, и давление очень скоротечно, он под воздействием мощной пружины возвращается на место, плотно закрывая отверстие.
В целом распределительный вал с кулачками предназначен для своевременного и согласованного с движением поршней в цилиндрах открытия и закрытия впускных и выпускных клапанов. Иначе говоря, посредством распредвала впускной клапан открывается в самом начале первого такта, когда поршень еще находится в верхней мертвой точке, и закрывается сразу, как только поршень достигнет нижней мертвой точки. Выпускной клапан открывается именно в конце третьего такта, когда поршень находится в НМТ, и закрывается по достижении им ВМТ, то есть когда выхлопные газы будут выдавлены поршнем через отверстие выпускного клапана.
Распределительный вал получает энергию вращения от коленчатого вала, с которым он соединен либо цепью, либо зубчатым ремнем газораспределительного механизма. Для этого на конце распредвала закреплена соответствующая шестерня, а на конце коленчатого вала — зубчатый шкив или звездочка. Например, в автомобиле ВАЗ-2106 используется цепь, а в ВАЗ-2108, «Форд-Эскорт», «Опель — Вектра» — ремень ГРМ.
Чтобы цепь постоянно находилась в требуемом натяжении, применяется натяжитель, установленный в комплекте с башмаком. Если в машине используется ремень ГРМ, то для его натяжения предусмотрен специальный натяжной ролик (рис.1).
Рис.1
Схема ременного привода распределительного вала:
Ремень ГРМ и цепь являются весьма важными деталями. Цепь считается более надежной, но и ремень выдерживает пробег в среднем до 60 000 км. Разрыв ремня ГРМ чреват катастрофическими последствиями для двигателя будут погнуты клапаны и др: придется делать сложный и дорогостоящий капитальный ремонт. Кстати, разрыв ремня ГРМ на водительском сленге называется «встречей поршней с клапанами» в результате чего ломается и то, и другое.
Поэтому, когда вы покупаете подержанный автомобиль, сразу поменяйте в нем ремень ГРМ, даже если продавец будет уверять в том, что «все заменено и все новое». Замена ремня обойдется намного дешевле капитального ремонта двигателя. Тем более что лопнуть ремень может в самое неподходящее время например, в дороге.
Иногда одновременно с ремнем следует заменить и его ролики, которые со временем заметно изнашиваются. Развалившийся ролик приводит к таким же фатальным для двигателя последствиям, как и лопнувший ремень ГРМ.
Иногда из газораспределительного механизма доносится характерный металлический стук. Причиной могут быть износ кулачков распределительного вала, слишком большие зазоры клапанного механизма, поломка клапанных пружин либо износ рычагов. При наличии больших зазоров клапанного механизма их следует отрегулировать, в остальных случаях неисправные запчасти подлежат замене.
Главным критерием, по которому определяют чрезмерное увеличение зазоров у клапанов, является частый металлический стук, хорошо слышимый при работе двигателя на холостых оборотах с малой частотой вращения коленчатого вала. Данная неисправность приводит к повышенному износу торцов стержней клапанов, наконечников стержней или регулировочных шайб, а также потере мощности двигателя, поскольку время пребывания клапанов в открытом положении уменьшается и, как следствие, ухудшается наполняемость цилиндров горючей смесью и полнота их очистки на четвертом такте работы.
Детали клапанного механизма (рис.2):
Если появляются характерные хлопки из карбюратора или из глушителя — значит, зазор у клапанов чересчур маленький и его также необходимо отрегулировать. Такая неисправность является причиной неплотного прилегания клапанов к своим седлам, в результате чего снижается компрессия в цилиндрах и двигатель теряет мощность.
Рис.2
При сильном износе клапанов следует выполнить их притирку к седлам либо вообще заменить.В некоторых случаях цепь газораспределительного механизма работает очень шумно, что, как правило, обусловлено ееудлинением за счет износа шарнирных соединений звеньев. Цепь необходимо натянуть или просто заменить.
Неисправности ГРМ
Основными неисправностями газораспределительного механизма являются:
- нарушение тепловых зазоров клапанов на двигателях с регулируемым зазором;
- износ подшипников, кулачков распределительного вала;
- неисправности гидрокомпенсаторов на двигателях с автоматической регулировкой зазоров;
- снижение упругости и поломка пружин клапанов;
- зависание клапанов;
- износ и удлинение цепи или ремня привода распределительного вала;
- износ зубчатого шкива привода распределительного вала;
- износ маслоотражающих колпачков, стержней клапанов, направляющих втулок;
- нагар на клапанах.
Можно выделить следующие причины неисправностей ГРМ:
- выработка установленного ресурса двигателя и, как следствие, высокий износ конструктивных элементов;
- нарушение правил эксплуатации двигателя, в том числе использование некачественного жидкого, загрязненного масла, применение бензина с высоким содержанием смол, длительная работа двигателя на предельных оборотах.
Самой серьезной неисправностью газораспределительного механизма является т.н. зависание клапанов(рис. 3), которое может привести к серьезным поломкам двигателя. Причин у неисправности две. Применение некачественного бензина, сопровождающееся отложением смол на стержнях клапана. Другой причиной является резонанс, ослабление или поломка пружин клапанов. В этом случае при достижении поршнем верхней мертвой точки клапан не успевает сесть в «седло». К счастью, данная неисправность на современных автомобилях встречается достаточно редко.
Отдельно необходимо сказать о неисправностях гидрокомпенсаторов. При использовании жидкого или сильно загрязненного масла гидрокомпенсатор перестает выполнять свою основную функцию, а именно автоматически компенсировать зазоры в ГРМ. Дальнейшая эксплуатация двигателя может привести к заклиниванию гидрокомпенсаторов.
Нарушение теплового зазора на двигателях с регулируемым зазором может произойти по причине износа подшипников и кулачков распределительного вала, износа зубчатого шкива привода распределительного вала, а также вследствие неправильной регулировки.
Неисправности ГРМ достаточно сложно диагностировать, т.к. сходные внешние признаки могут соответствовать нескольким неисправностям. Зачастую конкретная неисправность устанавливается непосредственным осмотром конструктивных элементов ГРМ со снятием крышки головки блока цилиндров.
Большинство неисправностей газораспределительного механизма приводит к нарушениям фаз газораспределения, при которых двигатель начинает работать нестабильно и не развивает номинальной мощности.
Внешние признаки и соответствующие им неисправности ГРМ:
Признаки | Неисправности |
|
|
|
|
|
|
|
|
|
|
|
|
Читайте также:
Рекомендуемые страницы:
Поиск по сайту
особенности, строение, практичность, ресурс, интервал обслуживания и замены
Добрый день, сегодня мы расскажем, каким ресурсом обладает ремень ГРМ (газораспределительного механизма) двигателя, чем отличается приводная деталь от цепи ГРМ, какой компонент мотора является наиболее практичным и долговечным по ресурсу.

Как правило, подавляющее большинство даже начинающих автолюбителей хотя бы раз в жизни слышали, что такое, а также, для чего предназначен ремень ГРМ или приводной элемент системы газораспределения двигателя. Для тех, кто слышит впервые такое понятие, как ремень ГРМ поясним, что ремень газораспределительного механизма является расходной деталью, призванной соединять коленчатый и распределительный валы силовой установки друг с другом. Справочно заметим, что иногда ремень ГРМ может соединять не один, как обычно, а два распредвала (пример тому система газораспределения DOHC).
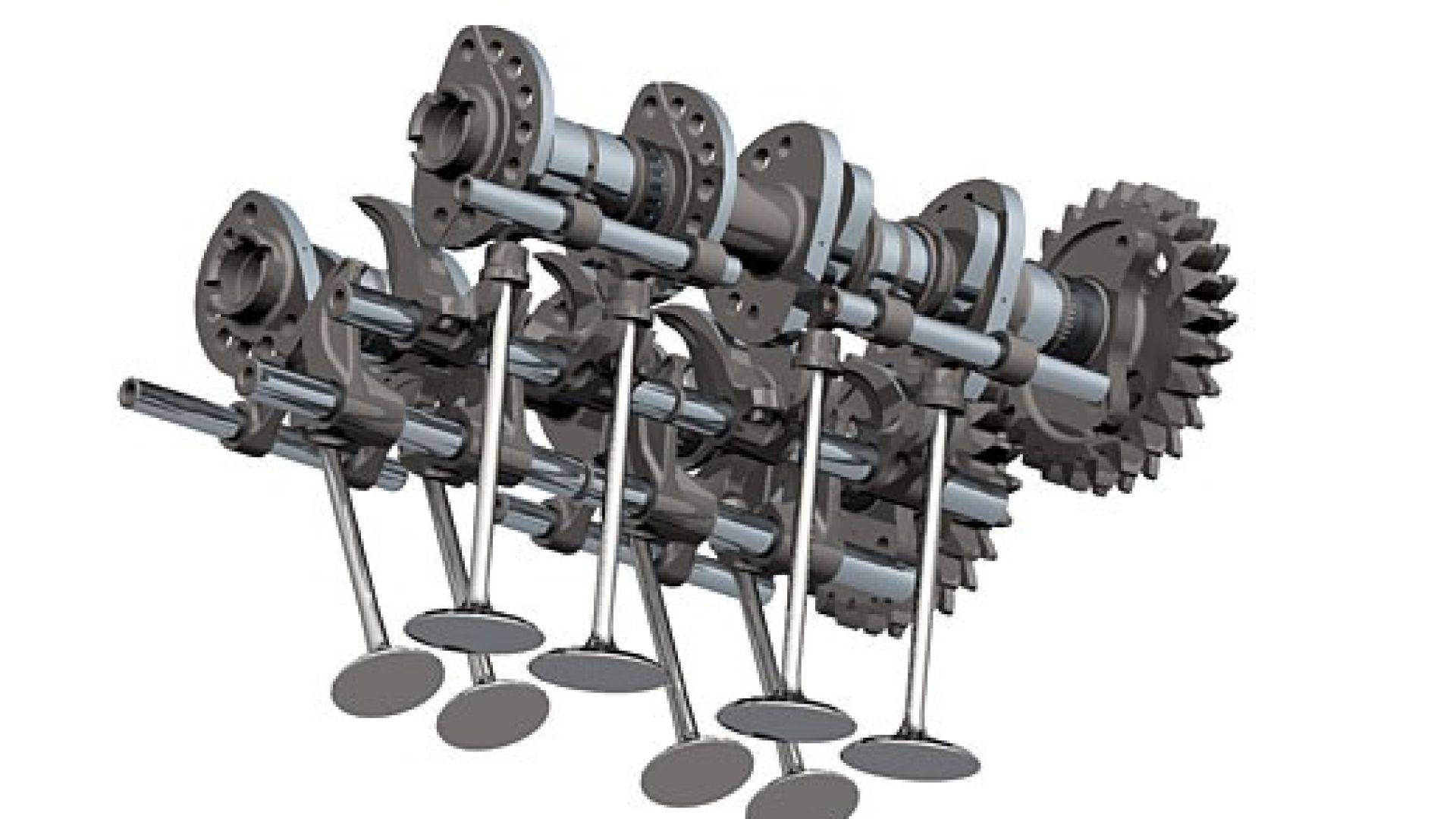
Благодаря коленчатому валу, который приводят в движение поршни, автомобиль трогается с места. Что касается распредвала, то его задача заключается в открытии в нужной последовательности клапанов мотора, для подачи топливной смеси и отвода отработанных газов из камеры сгорания цилиндров. Таким образом, ременная и цепная передачи выполняют одинаковую функцию по синхронизации приводных элементов при помощи их соединения.
Хочется добавить, что в последние годы некоторые автовладельцы достаточно сильно стали ругать ременную передачу за то, что ресурс у такого расходного элемента намного ниже того же цепного привода, причем в разы, да и технология ремня является недоработанной, а также морально устаревшей. Но, так ли это? Почему тогда большинство автопроизводителей до сих пор оснащают свои машины ременной передачей? Значит все же не так все плохо, как утверждают некоторые автовладельцы. Для того чтобы наверняка разобраться в надежности, а также реальном ресурсе ремня ГРМ, необходимо детально рассмотреть все положительные, а также отрицательные стороны, которыми обладает расходный элемент двигателя, что мы сейчас и сделаем.
1. ОСОБЕННОСТИ И ПРЕИМУЩЕСТВА РЕМЕННОГО ПРИВОДА ГРМ
Главной отличительной особенностью ремня от цепи системы газораспределения мотора является тип используемого материала и расположение расходной детали. Ремень ГРМ конструктивно всегда располагается снаружи двигателя под защитным кожухом, а цепь наоборот внутри силовой установки.
Кроме того, для цепи необходима специальная смазка в виде высококачественного моторного масла, в котором она функционирует, а ремню никакая смазка не нужна. Это, что касается основных отличий приводных деталей. А чтобы разрушить миф о ненадежности ремня механизма газораспределения стоит рассмотреть положительные стороны, которыми обладает расходная деталь двигателя.
Преимущества ременной передачи силовой установки:
—
Уровень шума: является самой сильной стороной ременной передачи, так как благодаря специальному материалу, роликам и натяжителям, работа ременного привода осуществляется практически беззвучно по сравнению с цепью, причем эффект будет заметен на любом типе мотора.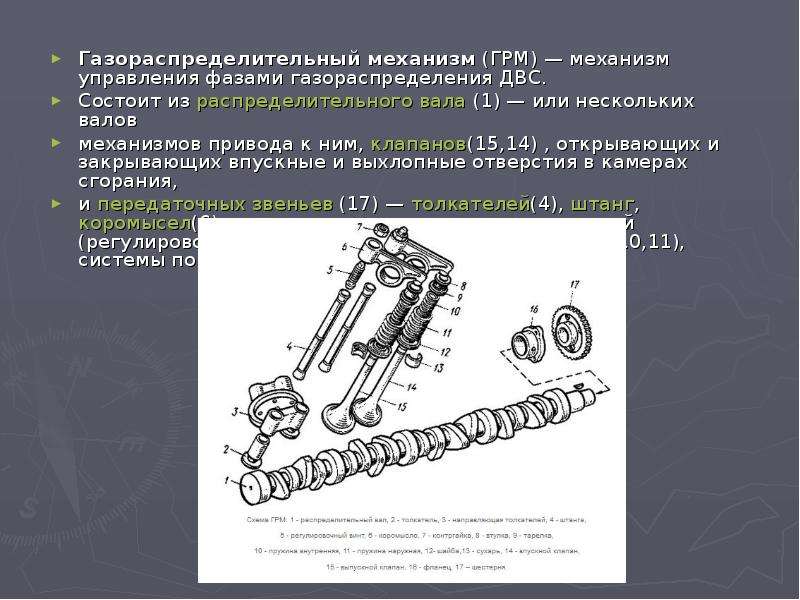
— Стоимость деталей: по этим показателям, ременная передача автовладельцу обходится примерно в 2 раза дешевле, чем цепь и все что с ней связано. Дешевле ремень ГРМ, потому что на него уходит меньше затрат при производстве, а также в дальнейшем во время установки с регулировкой, то есть стоимость работ по замене, также менее затратная для автовладельца. В том случае, даже если мы будем менять приводной ремень каждые 60 тысяч километров пробега, то это все равно выйдет дешевле, чем 1 раз сменить цепь на пробеге в 250 тысяч километров.
— Экономия пространства в моторном отсеке: происходит именно благодаря установленной ременной передаче в двигателе. По сравнению с цепным двигателем, ременной мотор примерно на 10-15 процентов занимает меньше места в отсеке за счет того, что силовая установка по своим размерам получается более компактней. А все из-за того, что цепная передача располагается внутри мотора, постоянно функционируя в масле и для нее необходимо еще дополнительно изготавливать специальную клапанную крышку, блок и поддон, которые намного массивнее, чем в ременных двигателях. Все это нужно для того, чтобы надежно спрятать цепь внутри двс. Вот поэтому, как ни крути, но силовая установка получается более объемной. Что касается ремня, который расположен снаружи, то ему нужен только защитный пластиковый или алюминиевый чехол и ролики.
— Качество моторного масла: является ключевым параметром для оптимальной и долговечной работы цепного двигателя. Система газораспределения, работающая на цепи крайне требовательна к качеству масла и если не обращать внимание на этот пункт, то срок службы механизма может сократиться примерно на 25 процентов, что является весьма существенно. Вот поэтому менять моторное масло в цепных силовых установках, нужно как можно чаще, например, 1 раз в 8-10 тысяч километров пробега. Что касается ремня ГРМ, то он совершенно не требователен к горюче-смазочным материалам, так как работает в воздухе и ни каким образом не контактирует со смазкой. Однако, для ремня важен четкий интервал замены, чтобы не было его обрывов.
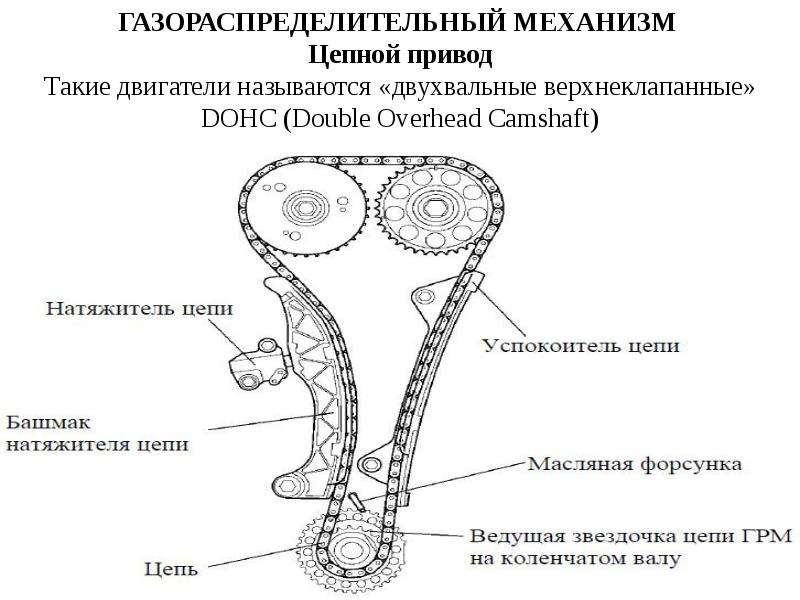
— Простота обслуживания: является залогом ременных моторов. Как утверждает большинство специалистов по обслуживанию и ремонту транспортных средств, ремень системы газораспределения не только дешевле менять, но и намного проще, чем цепь, так как не нужно разбирать двигатель, а также сливать моторное масло.
— Легко настраивать и проверять: благодаря открытому расположению ременной передачи, диагностику расходного элемента двигателя проводить намного проще, чем той же цепи. Кроме того, ремень достаточно просто настраивается, то есть натягивается при надобности.
Таким образом, как видим ременной привод системы газораспределения обладает массой положительных моментов и утверждать, что такой механизм полностью себя изжил или морально устарел мягко говоря не этично. Что касается долговечности и надежности ремня ГРМ, то во многом эти параметры зависят от качества материала, из которого изготавливается расходный элемент, а также от технологии производства.
2. НАДЕЖНОСТЬ, РЕСУРС И НЕДОСТАТКИ РЕМНЯ ГРМ
Ресурс любого узла автомобиля, в особенности деталей двигателя является основным показателем надежности и долговечности. Во многом ресурс ремня конечно же зависит от качества материала, из которого он изготовлен расходный элемент, но нельзя забывать еще про натяжное оборудование (ролики, виброгасители), которое обеспечивает оптимальное функционирование ременной передачи системы газораспределения. Большинство производителей ремней ГРМ и натяжных компонентов, не указывают через сколько менять расходные элементы, однако такая информация всегда имеется в технической документации на автомобиль.
Если отталкиваться от информации, которая указывается в мануале на автомобиль, то средний пробег, рекомендуемый для замены ремня ГРМ составляет 90-100 тысяч километров. Хотя на некоторых иномарках, особенно немецких и японских данный пробег может составлять в районе 120-150 тысяч километров.

От чего зависит долговечность ремня ГРМ? Срок службы расходного компонента мотора непосредственно зависит от постепенного растяжения и образования мелких надрывов на ремне в процессе его эксплуатации. Хотя если честно, то некоторые модели ремней ГРМ способны ходить и до 200 тысяч километров, то это не касается натяжных и опорных роликов, их предел не более 120 тысяч километров пробега. Что будет с ремнем, если его вообще не менять? В том случае, если ремень не меняется, то зачастую в таких ситуациях происходит его обрыв со всеми вытекающими последствиями, вплоть до согнутых клапанов и как следствие капремонт двигателя.
Что относится к натяжному оборудованию и для чего оно нужно? Как мы отметили ранее, натяжное оборудование обеспечивает оптимальное функционирование ремня ГРМ системы газораспределения. К такому оборудованию зачастую относятся опорный подшипник с пластиковой защитой, на который опирается ремень во время работы и натяжной ролик внешне похожий на опорный, только находится на специальном креплении, позволяющем натягивать приводной ремень, то есть, как бы держит его в натянутом состоянии и не дает провисать, чтобы не было перескока на зуб шестерни.
Чтобы ремень ГРМ функционировал долго и надежно, опорный и натяжной ролики обязаны быть высочайшего качества. В подавляющем большинстве немецких, американских, японских и прочих иномарках ролики достаточно надежные и способны отходить столько же сколько сам ремень, но не дольше его. В том случае, когда один из роликов выходит из строя, так как зачастую они просто протираются, то у водителя имеется еще запас хода в 100-120 километров, чтобы дотянуть до станции технического обслуживания.
Таким образом, при плановой замене ремня ГРМ меняется не только гибкий элемент, но и ролики, причем это обязательно требование любого производителя. Справочно заметим, что порой косвенной причиной предстоящей замены ремня и роликов становится повышенный шум во время работы мотора со стороны расходных компонентов газораспределительной системы двигателя. Как правило, шумят именно ролики (подшипники).
Что касается отечественных автомобилей, на примере Лада Веста/Иксрей, то заводской или оригинальный ремень ГРМ обладает ресурсом в 70-80 тысяч километров пробега. К сожалению, в ВАЗах не все так здорово, как кажется с первого взгляда. Сами ремни ходят довольно долго, но вот ролики являются большой проблемой системы газораспределения.
Опорный и натяжной ролики российского производства выходят из строя порой уже на 40-50 тысяч километров пробега, причем банально их просто заклинивает. Однако это не всегда касается оригинальных, то есть заводских элементов, они-то регламентный ресурс практически выдерживают. Малый срок службы имеют ролики сторонних производителей, которые часто устанавливаются дилерами на 6-ом по счету ТО, когда меняется ремень ГРМ и натяжное оборудование.
Поэтому, если мы стали обладателем автомобиля отечественного автопрома, то по опираясь на рекомендации большинства специалистов по обслуживанию и ремонту транспортных средств, лучше менять ремень ГРМ и натяжное оборудование на 60-65 тысячах километров пробега и не рисковать, потому что “дружественную” встречу с клапанами еще никто не отменял. Причем крайне важно устанавливать только оригинальные расходные детали, желательно импортного изготовителя, так как в данной ситуации экономить не в коем случае нельзя. От себя лично заметим, что непонятно, почему до сих пор российские производители не смогли научится делать качественные запасные части, в особенности детали системы газораспределения.
Видео: «Ремень ГРМ: особенности, практичность, ресурс, интервал обслуживания и замены»
В заключении отметим, что при правильной эксплуатации и своевременном обслуживании ремня ГРМ с натяжным оборудованием системы газораспределения силовой установки, проблем, связанных обрывом или растяжением ременной передачи возникать не должно. Также справочно заметим, что в случае обнаружения посторонних звуков со стороны элементов ременной передачи, особенно опорного и/или натяжного роликов во время работы двигателя, то рекомендуется незамедлительно обратиться на станцию технического обслуживания для проверки компонентов механизма газораспределения и возможной замены его деталей.
БЛАГОДАРИМ ВАС ЗА ВНИМАНИЕ. ПОДПИСЫВАЙТЕСЬ НА НАШИ НОВОСТИ. ДЕЛИТЕСЬ С ДРУЗЬЯМИ.
Системы изменения фаз ГРМ: типы и особенности работы
Известно, что продолжительность цикла открытия и закрытия клапана и оптимальные его значения зависят от режима работы мотора. Система автоматического управления ГРМ, с одной стороны, способствует лучшей работе мотора в режиме холостого хода, увеличению мощности и крутящего момента двигателя, а с другой стороны, позволяет снизить уровень токсичности отработавших газов и обеспечить их рециркуляцию. При этом система изменения фаз ГРМ оптимизирует работу двигателя без внедрения каких-либо конструктивных изменений. Современные моторы помимо системы автоматического управления фазами ГРМ могут оснащаться также и системой отключения цилиндров, которая позволяет снизить расход топлива и уменьшить токсичность выхлопа при неполной нагрузке на мотор. Изменение фаз ГРМ может осуществляться или поворотом распредвала, или с помощью кулачков разнообразного профиля, или же варьированием высоты подъема клапана.
В современном автомобилестроении чаще всего для изменения фаз применяется схема изменения поворота распредвала. Такую схему можно встретить, например, на автомобилях BMW, она называется Vanos (Double Vanos), на машинах марки Toyota (VVT-i или Dual VVT-i). Разработчики Honda применяют систему VTC (Variable Timing Control). На машинах концерна Volkswagen AG используется традиционная и хорошо знакомая всем система изменения фаз ГРМ – VVT (Variable Valve Timing) с гидроуправляемыми муфтами (по одной муфте на каждый распредвал).
От Single VANOS к Duble VANOSСистему VANOS (Variable Nockenwellen Steuerung) создали разработчики из BMW совместно со специалистами компании Continental Teves. Принцип работы системы: изменение положения распредвала относительно коленвала, за счет чего и осуществляется регулировка фаз ГРМ. Первое поколение системы VANOS использовалось с начала 90-х годов. Отличительная особенность Single VANOS в том, что относительно коленвала регулируется только положение впускного распредвала. Такое решение позволило увеличить крутящий момент мотора в режиме низких оборотов, улучшило наполняемость цилиндров, стабилизировало работу холостого хода, а также способствовало снижению расхода топлива. С середины 90-х годов разработчики BMW внедрили систему Double VANOS, которая позволила регулировать положение двух распредвалов, и это благотворно отразилось и на крутящем моменте двигателя, и на его мощности. При этом при работе системы Double VANOS удалось реализовать процесс дожига небольшой части выхлопных газов (в зависимости от режима работы мотора они направляются обратно в выпускной коллектор), что также улучшило экологические показатели автомобилей. Слабое место системы – уплотнительные кольца поршней, которые зачастую приходят в негодность в условиях перепада температур и перестают обеспечивать герметичность системы.
Такие гидроуправляемые муфты соединены с системой смазки силового агрегата. Работой всего узла «руководит» блок управления двигателя, который формирует свои команды на основе анализа данных о частоте работы коленвала, нагрузках на него, изменениях температурного режима. Блок управления посылает соответствующий сигнал, и масло из системы смазки двигателя поступает в муфты, а они поворачивают распредвалы с учетом полученных команд.
В системах, в которых используются кулачки различного профиля, изменение фаз ГРМ осуществляется за счет ступенчатого изменения продолжительности открытия и высоты подъема клапана. Подобные системы применяются в двигателях автомобилей Honda (VTEC), Mitsubishi (MIVEC) и других. Например, в двигателе VTEC на каждые два клапана распредвала приходится по три кулачка – два малых и один большой. Малые кулачки запускают в работу пару впускных клапанов в режиме невысоких оборотов коленвала. Задача большого кулачка – перемещать свободное коромысло в холостом режиме. Высота подъема клапанов минимальна, а фаза ГРМ имеет небольшую продолжительность. Переключение с одного режима работы на другой осуществляется бесступенчато за счет системы управления, оснащенной блокирующим механизмом с гидравлическим приводом. При этом переключение происходит всякий раз, когда коленвал достигает заданной частоты вращения. Увеличение хода клапанов и, как следствие, увеличение фазы осуществляются за счет совместной работы малых и большого кулачков, которые, будучи соединенными стопорным штифтом, подают усилие на впускные клапаны. Отметим, что такая «кулачковая» система имеет ряд объективных недостатков – бесступенчатую смену режимов, а также сложную с конструктивной точки зрения схему блокировки.
Если говорить о более эффективных решениях для изменения фаз ГРМ, стоит упомянуть систему регулирования высоты подъема клапанов. И здесь стоит говорить о разработке BMW – системе Valvetronic, первой в своем роде системе управления фаз газораспределения с использованием регулировки высоты подъема клапана. Причем Valvetronic работает только на впускных клапанах. Принцип работы такой системы основан на кинематической схеме, именно она позволяет изменять ход клапана. Эксцентриковый вал работает от электродвигателя через червячную передачу. Вал изменяет положение промежуточного рычага, который направляет коромысло по заданной траектории, по соответствующей траектории перемещается и клапан. При этом высота подъема клапана изменяется непрерывно (в зависимости от режима работы мотора).
И хотя система изменения фаз газораспределения – это весьма надежный и долговечный узел, его эксплуатация во многом зависит от качества моторного масла и соблюдения интервалов его замены. Наличие в масле примесей, а также использование масла ненадлежащей вязкости могут оказать негативное воздействие на работу системы.
К числу наиболее типичных неполадок в работе системы изменения фаз ГРМ можно отнести неполадки в муфте распредвала впускных клапанов, которые проявляются в виде стука от верхней части мотора, возникающего после «холодного» пуска. Сильный шум от привода системы может указывать также на неполное включение стопорного штифта привода системы изменения фаз газораспределения.
Valvetronic – залог экологичной работы
В ответ на ужесточение экологических норм и в поисках решений для снижения токсичности выхлопа автомобиля разработчики BMW создали систему Valvetronic. Ее стали внедрять в первой половине 2000-х. Конструктивной особенностью Valvetronic стало отсутствие дроссельной заслонки, которая, как известно, способствует увеличению расхода топлива и повышения токсичности выхлопа. Разработчики предложили альтернативу – механизм, который позволяет поднимать клапан в ограниченном диапазоне. Работа Valvetronic обеспечивает снижение расхода топлива даже в режиме интенсивной работы мотор, приятным бонусом стало увеличение динамики хода автомобиля, а также его приемистость.
Как заменить ремень ГРМ | Gates Europe
Перед установкой нового ремня ГРМ рекомендуем ответить себе на следующие вопросы:
- Вы заменяете ремень ГРМ, потому что старый порвался или в рамках общего технического обслуживания?
- Если старый ремень порвался, сохранил ли двигатель работоспособность?
- Приходилось ли вам раньше устанавливать ремень ГРМ на этот двигатель?
- Есть ли у вас инструкции по установке и знакомы ли вы с требованиями по натяжению, которые даны в руководстве по обслуживанию автомобиля?
- У вас есть необходимые инструменты?
Очень важно, как вы ответите на эти вопросы. Если старый ремень порвался, двигатель мог получить повреждения, которые должны быть устранены перед установкой нового ремня.
Подсказки на упаковке помогут выполнить работу на отлично
Замена ремня ГРМ — это сложная работа, для которой требуются специальные инструменты. Такие инструменты предназначены для разных случаев применения. На упаковку нашего товара нанесена информация о том, какие инструменты следует использовать для правильной установки ремней ГРМ. Спросите своего поставщика о том, какие инструменты от компании Gates есть в его ассортименте.
Вы профессионал, поэтому знаете, что порядок установки ремня ГРМ отличается на разных двигателях. Поэтому мы вкладываем инструкции по работе с конкретным видом двигателя в большинство коробок с нашей продукцией.
Более того, в наших технических бюллетенях есть описание сложных случаев с приводами и описание некоторых нерешенных проблем. На коробках от ремней ГРМ тоже указывается номер доступного бюллетеня с полезной информацией. Ознакомиться или скачать все наши технические бюллетени можно здесь.
В большинстве случаев при замене изношенного ремня ГРМ все остальные металлические компоненты привода тоже следует заменить. Оптимальным решением является полный комплект для ременного привода ГРМ. Эффективнее заменить натяжитель и направляющие ролики, и даже водяной насос, когда двигатель уже демонтирован. Ознакомьтесь с нашим онлайн-каталогом, чтобы найти подходящий для вашего случая комплект для ременного привода ГРМ или комплект для ременного привода с водяным насосом.
Вы также найдете пошаговое описание процедуры установки ремней ГРМ. Предложенные далее указания являются общими рекомендациями. Внимательно ознакомьтесь с инструкциями производителя транспортного средства или с нашими инструкциями по конкретной модели двигателя, вложенными в коробку.
Как установить ремень ГРМ за 8 простых шагов
ШАГ 1
- Убедитесь, что установочные метки тщательно совмещены.
- Указатель коленвала находится в ВМТ.
- Ротор распределителя находится на одной прямой с меткой на корпусе распределителя.
- Стрелка на шкиве распределительного вала совмещена с меткой на блоке двигателя.
ШАГ 2
Наденьте новый ремень на шкивы, но будьте осторожны и не прилагайте к нему усилий. Никогда не устанавливайте бывший в употреблении ремень, поскольку параметры натяжения рассчитаны для нового ремня.
ШАГ 3
Медленно освободите регулировочный болт натяжителя, чтобы он мог отойти до упора в ремень. Будьте внимательны при освобождении натяжителя для его возврата на место. Не допускайте жесткого удара по ремню. Убедитесь, что пружина натяжителя занимает нужное положение.
При отсутствии натяжителя с нажимной пружиной натяните ремень в соответствии с рекомендациями производителя автомобиля.
ШАГ 4
Проверните коленчатый вал (в обычном направлении вращения) не менее чем на два полных оборота для того, чтобы равномерно распределить натяжение ремня и дать возможность зубцам точно разместиться в выемках шкива.
ШАГ 5
Отпустите натяжитель и повторите натяжение ремня в соответствии с рекомендациями производителя автомобиля. Если привод оснащен неподвижным натяжителем, проверьте натяжение при помощи акустического тестера Gates STT-1. Затяните регулировочный и шарнирный болт натяжителя до рекомендованных производителем значений момента затяжки.
ШАГ 6
Установите на место все детали, которые были демонтированы. Установите обратно крышку ремня ГРМ. Затяните все болты до рекомендованных производителем значений момента затяжки.
ШАГ 7
Восстановите соединение минусового провода батареи.
ШАГ 8
Запустите двигатель, проверьте опережение зажигания и осуществите необходимые регулировки.
Система хронометража— это … Что такое система хронометража?
система синхронизации — См. Микропроцессорная система синхронизации зажигания… Словарь автомобильных терминов
Система синхронизации зажигания — См. Микропроцессорная система синхронизации зажигания… Словарь автомобильных терминов
электронная система опережения зажигания — (EST) Электронный блок управления двигателем определяет опережение зажигания. Это заменяет вакуумный или центробежный механизм в распределителе и использует компьютер для увеличения или уменьшения времени зажигания… Словарь автомобильных терминов
компьютеризированная система определения рыночного времени — компьютерная система, которая собирает большие объемы торговых данных в поисках моделей и тенденций для выработки рекомендаций по покупке и продаже.Bloomberg Financial Dictionary… Финансовые и коммерческие термины
микропроцессорная система синхронизации зажигания — (MSTS) См. Карту системы зажигания… Словарь автомобильных терминов
Ремень привода ГРМ — Информацию о других ремнях см. В разделе Ремень (значения). Ремень ГРМ Timi… Википедия
синхронизация — Один из важных факторов в двигателе внутреннего сгорания (топливо, воздух, правильная пропорция смеси, время сжатия, искра).Когда поршень находится в такте сжатия, оба клапана должны быть закрыты. Если один или несколько открыты, фазы газораспределения…… Словарь автомобильных терминов
система — упорядоченное, взаимосвязанное, сложное расположение частей. См. Гидроаккумуляторная система система фильтрации воздуха система реакции нагнетания воздуха воздушная система сигнализация система защиты от погружений антиблокировочная система тормозная система антишумовая система… Словарь автомобильных терминов
Временная метка — на шкиве под углом 6 ° до ВМТ.Метка синхронизации — это индикатор, используемый для установки синхронизации системы зажигания двигателя, обычно находящийся на шкиве коленчатого вала (как показано на рисунке) или маховике, являющемся наибольшим радиусом вращения у коленчатого вала…… Wikipedia
Запас по времени — это выражение разницы между фактическим изменением сигнала и самым поздним временем, в которое сигнал может измениться для правильной работы схемы. Он используется в разработке цифровой электроники.На этом изображении нижний…… Wikipedia
Timing Advance — (TA) ist ein Wert, der im GSM Standard zur Synchronization zwischen Uplink und Downlink verwendet wird. Der Wert gibt (in Bitdauern von ca. 3,7 μs) den Zeitversatz an, um den eine Mobilstation früher senden muss, damit unter Berücksichtigung… Deutsch Wikipedia
Brower Timing Systems
Связаться с нами Поддержка Загрузки Запчасти Ремонт / Гарантия Исправление проблем политика конфиденциальности Инструкции по использованию черного ящика Система RL Система TCI Черный ящик Вертикальный прыжок Связаться с нами Поддержка Загрузки Запчасти Ремонт / Гарантия Исправление проблем политика конфиденциальности Инструкции по использованию черного ящика Система RL Система TCI Черный ящик Вертикальный прыжокrctiming.com — Круги
Транспондер Системы синхронизации
ср получить довольно много писем о времени транспондера системы, поэтому эта страница была создана, чтобы дать некоторая информация, которую может найти клуб / трек полезно.
Три компании производят системы, предназначенные для автоматического время / счет радиоуправляемые машины, доступны другие системы но предназначены для личного использования или в миниатюрном масштабе (min-z так далее).
AMB были лидером рынка в этом секторе с начало 80-х, когда они изобрели компьютер для измерения времени а затем система синхронизации транспондера для модели автомобилей, теперь они производят системы для всех видов спорта (на их сайте есть история).
г. Система 20 (названа так, потому что он может насчитать двадцать автомобилей) был представлен в в начале 90-х они больше не производятся, но доступны на вторичном рынке.В базовая система может насчитывать 10 автомобилей, но с дополнительным коробка может насчитать 20, многие ранее проданные системы AMB (модели 8300/8800) мог быть переделан использовать систему 20 транспондеров и многие из них системы все еще используются сегодня. Только аккумуляторная транспондеры были доступны для системы 20, а клуб / трек обычно состоит из двух наборов (один на текущую гонку и набор для раздачи на следующий), конечно, некоторые водители забывают вернуть транспондеры, вызывающие проблемы.
AMBrc системы были введены в 2000 году для заменить популярную System 20 на новую систему введена возможность иметь персональные транспондеры а также раздаточные аккумуляторы (Система 20 транспондеры не будут работать в системах AMBrc или наоборот).Теперь каждый водитель может иметь транспондер, постоянно установленный в их машине питание от бортовой электроники (3-й канал или разъем аккумулятора), устраняя необходимость взять и вернуть трек / клуб.
AMBrc3 декодеров были представлены в середине 2006 г. и использовать те же «красные» транспондеры как система AMBrc.Передняя часть устройства имеет ЖК-экран, две кнопки для редактирования настроек, разъем для наушников и разъем USB A, отключен в настоящее время. Сзади там розетка, подключение 10/100 ethernet (RJ45), RS232, вспомогательное и контурное коаксиальное соединение. Декодеры AMBrc3 не имеют соединения USB B, вместо этого сетевое соединение Ethernet 10/100 предоставлен; это означает, что декодер должен питаться от отдельного сетевого адаптера.Этот многие пользователи AMBrc могут рассматривать как обратный шаг, но я считаю, что требования к мощности нового декодера слишком хороши для USB. Ethernet имеет свои преимущества перед USB, однако более безопасное соединение (не выпадет, если компьютер переходит в режим энергосбережения) и позволяет для подключения до четырех компьютеров к в то же время.Ethernet также позволяет декодеру работать независимо от компьютера для загрузки время круга через сервис AMB mylaps live, просто подключите декодер к ADSL / кабельному маршрутизатору, введите имя пользователя / пароль mylaps и ваш прочь, удивительный!
Apart из моих кругов в прямом эфире мало что практическая разница между AMBrc / AMBrc3 декодеры, но последние функции будут полезно для тех, кому нужен результат «жить» в Интернете.
Хронит произвел систему, очень похожую на AMB, но их больше нет.
КО Propo выпустили две системы на рынок, работает с автомобилями Mini-Z и использует сигналы, излучаемые приемным устройством на посчитайте машины.Другая система использует транспондер агрегаты (именуемые TD-1), работающие от бесплатного прорезь в автомагнитоле. Для смены транспондера установлено количество разных кристаллов, поэтому система требует участия водителя и большая коллекция кристаллов, если они не необходимо возвращать после каждой гонки.
А транспондерная система — существенная покупка, убедитесь, что система, которую вы хотите купить, подходит для вашей цели, посещение другого трек может быть хорошей идеей, чтобы увидеть систему быть использованным.
MOBATIME — Мы синхронизируем мир — Глобальный веб-сайт
перейти к содержанию- Продукты Назад
Товары
- Серверы времени
- Мастер Часы
- Аналоговые часы
- Цифровые часы
- Специальные часы
- Движения
- Аксессуары
- Программного обеспечения
- PTP Grandmaster Clocks
- PTP Slave Clocks
- NTP Time Servers
- Network Master Clocks
- DTS 4806.masterclock
- DTS 4802.masterclock
- DTS 4801.masterclock
- Compu Time Center CTC
- EuroTime Center ETC
- HN 60
- Аналоговые внутренние часы
- Цифровые часы 9016 Аналоговые часы на открытом воздухе Наружные часы
- Фасадные часы
- Цветочные часы
- SAM / SEM 100
- СЕРИЯ 190
- NBU 190
- GU 192
- FU 192
- QU 192 9000
- NU NU 90 SYN
- SEI 40
- SAM 40 / SEM 40
- SAN 40 / SEN 40
- DMU 140
- DMU 160
- DMU 350
- MW10 / MWS 10
- 000 MW20
- MW20
- MW20 Распределение времени 90 213 Бустеры
- Контроллеры часов
- Распределители
- Аудио-часы
- Интерфейсы
- Реле
- Портативный носитель данных
- Приемники временного кода
- MOBA-NMS (программное обеспечение для управления сетью) 902
- ДТС 4160.grandmaster
- DTS 4160.grandmaster i
- DTS 4150.grandmaster
- DTS 4148.grandmaster
- DTS 4210.timecenter
- DTS 4020.timebridge
- Swift Timing Systems — первая и единственная система отсчета времени с одноразовым чипом Laredo!
- Большой или маленький, мы делаем все — 5 км, 10 км, полумарафоны, полные марафоны, цветные забеги, грязевые забеги, гонки на горном велосипеде, велосипедные шоссейные гонки, триатлоны, дуатлоны и гонки по пересеченной местности.Благодаря новейшему оборудованию Swift Timing Systems позаботится о том, чтобы ваша гонка стала главным событием. Независимо от того, что нужно вашей гонке, звоните в Swift Timing Systems!
- Джонни Масиас — (956) 645-1848
- Орландо Бустаманте — (956) 319-2653
- 9259 DTS
DTS — SWIFT TIMING
НЕ ВАЖНО, НАСКОЛЬКО ВАШЕ СОБЫТИЕ, МЫ МОЖЕМ ПОЛУЧИТЬ БОЛЬШОЕ ЧУВСТВО ГОНКИ …
Jaguar Innovative Chip Timing, Custom Trusses (15 ‘, 21’ or 27 ‘), Barricades, Safety Traffic Конусы и многое другое. Забронируйте нас сегодня!
Одноразовые чипы RFID
ЛУЧШЕЕ ОБОРУДОВАНИЕ, ПРОГРАММНОЕ ОБЕСПЕЧЕНИЕ И ЧИПЫ RFID. НЕ ТРЕБУЕТСЯ ЦИФРОВОЙ ИЛИ РАМПЫ !!!!!!
Верхние или боковые антенны
Индивидуальный чип для любой гонки
Платиновый считыватель Jaguar
Гоночный киоск для быстрых результатов
Гоночные часы
Jaguar Announcer — Результаты в реальном времени
Устройство чтения резервных копий Jaguar TomCat
Конусы движения
Велосипедные крепления
______________________________________________________________________________________________________________________
_______________________________________________________________________________________________________________________
Время / система
.: т / с т / с Карман для Vogue Легко .: Т / С Т / С «Время / система» .: :
.: 10-12-2020:
[].: :
mindmanager 7:
.: : 2021.
.,. —
3-. Время / система 2020. 2020. .
Время / система. , г.
.