Коленчатый вал — Википедия
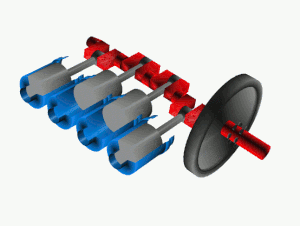
Коленчатый вал — деталь (или узел деталей в случае составного вала) сложной формы, имеющая шейки для крепления шатунов, от которых воспринимает усилия и преобразует их в крутящий момент. Составная часть кривошипно-шатунного механизма (КШМ).
Впервые столь важную механическую деталь как коленчатый вал описал и сконструировал средневековый учёный Аль-Джазари в Османской империи в 13 веке. В 1206 году в трактате «Китаб фи марифат аль-хиял аль-хандасийя» (Книга знаний об остроумных механических устройствах) описан механизм вала.
- Коренная шейка — опора вала, лежащая в коренном подшипнике, размещённом в картере двигателя.
- Шатунная шейка — опора, при помощи которой вал связывается с шатунами (для смазки шатунных подшипников имеются масляные каналы).
- Щёки — связывают коренные и шатунные шейки.
- Задняя выходная часть вала (хвостовик) — часть вала соединяющаяся с маховиком или массивной шестернёй отбора основной части мощности.
- Противовесы — обеспечивают разгрузку коренных подшипников от центробежных сил инерции первого порядка неуравновешенных масс кривошипа и нижней части шатуна.
Определяются как результат расчётов, причём часть размеров задаётся исходя из выбранной компоновки. Например, количество шатунных шеек определяется в зависимости от числа цилиндров. В многорядных двигателях (V, W, X-образных, звездообразных) одна шатунная шейка воспринимает нагрузки сразу нескольких шатунов (или одного центрального, соединённого с прицепными). Коленчатый вал воспринимает крутящий момент, имеющий переменное значение, а следовательно, работает на скручивание и должен иметь достаточный запас прочности (обычно 2,5) по усталостному напряжению на сдвиг.
Стальные валы (чаще всего) имеют невысокое внутреннее демпфирование крутильных колебаний, что в некоторых случаях угрожает валу разрушением из-за резонанса при прохождении опасной зоны по числу оборотов. Поэтому валы такие снабжают демпферами крутильных колебаний, расположенными на переднем носке вала.
Кроме усталостной прочности, коленвалы должны иметь определённую площадь шеек, задающую контактное давление подшипников скольжения или качения. Максимальное контактное давление и скорость скольжения для антифрикционных материалов может быть несколько повышено при высокой твёрдости шеек и высококачественной смазке. Превышение их выше допустимых ведёт к выплавке/растрескиванию антифрикционного слоя или питтингу роликов (подшипники качения).
Диаметр шатунных шеек (исходя из упомянутых соображений) может быть увеличен косым разъёмом шатуна (что увеличивает его трудоёмкость и стоимость), длину же можно увеличить либо за счёт коренных шеек (что увеличивает контактное давление), либо увеличением расстояния между цилиндрами (что ведёт к увеличению габаритов и массы двигателя). В последние десятилетия, в связи с появлением новых высопрочных антифрикционных сплавов и высококачественных масел, длину шеек валов (а вместе с ним — и межцилиндровое расстояние) конструкторы сокращают.
Материал и технология изготовления заготовок коленчатых валов[править | править код]
Материал и технология изготовления зачастую тесно увязаны между собой. В данном случае, стальные валы (с целью достижения наивысшей прочности и вязкости) получают ковкой, чугунные (материал ковке не поддаётся) — литьём.
Стальные коленчатые валы[править | править код]
Коленчатые валы изготовляют из углеродистых, хромомарганцевых, хромоникельмолибденовых, и других сталей, а также из специальных высокопрочных чугунов. Наибольшее применение находят стали марок 45, 45Х, 45Г2, 50Г, а для тяжело нагруженных коленчатых валов дизелей — 40ХНМА, 18ХНВА и др
[1]. Преимуществом стальных валов является наивысшая прочность, возможность получения высокой твёрдости шеек азотированием, чугунные валы — дешевле.Выбор стали определяется поверхностной твёрдостью шеек, которую нужно получить. Твёрдость около 60 HRC (необходимая для применения роликовых подшипников) может быть получена, как правило, только химико-термической обработкой (цементация, азотирование, цианирование). Для этих целей годятся, как правило, малоуглеродистые хромоникелевые или хромоникельмолибденовые стали (12ХН3А, 18ХНВА, 20ХНМА, причём для валов средних и крупных размеров требуется большее легирование дорогостоящим молибденом. Однако в последнее время для этого стали употреблять дешёвые стали регламентированной прокаливаемости, позволяющие получить высокую твёрдость при сохранении вязкости сердцевины. Меньшая твёрдость, достаточная для надёжной работы подшипников скольжения, может быть получена закалкой ТВЧ как среднеуглеродистых сталей, так и серого или высокпрочного чугуна (45..55 HRC).
Заготовки стальных коленчатых валов средних размеров в крупносерийном и массовом производстве изготовляют ковкой в закрытых штампах на молотах или прессах, при этом процесс получения заготовки проходит несколько операций. После предварительной и окончательной ковки коленчатого вала в штампах производят обрезку облоя на обрезном прессе и горячую правку в штампе под молотом.
В связи с высокими требованиями механической прочности вала большое значение имеет расположение волокон материала при получении заготовки во избежание их перерезания при последующей механической обработке. Для этого применяют штампы со специальными гибочными ручьями. После штамповки перед механической обработкой, заготовки валов подвергают термической обработке — нормализация — и затем очистке от окалины травлением или обработкой на дробеметной машине.
Крупноразмерные коленчатые валы, такие как судовые, а также коленвалы двигателей с туннельным картером являются разборными, и соединяются на болтах. Коленвалы могут устанавливаться не только на подшипниках скольжения, но и на роликовых (шатунные и коренные), шариковых (коренные в маломощных моторах). В этих случаях и к точности изготовления, и к твёрдости предъявляются более высокие требования. Такие валы поэтому всегда изготовляют стальными.
Чугунные коленчатые валы[править | править код]
Литые коленчатые валы изготовляют обычно из высокопрочного чугуна, модифицированного магнием. Полученные методом прецизионного литья (в оболочковых формах) валы по сравнению со «штампованными» имеют ряд преимуществ, в том числе высокий коэффициент использования металла и хорошее демпфирование крутильных колебаний, позволяющее часто отказаться от внешнего демпфера на переднем носке вала. В литых заготовках можно получить и ряд внутренних полостей при отливке[2].
Припуск на обработку шеек чугунных валов составляет не более 2,5 мм на сторону при отклонениях по 5-7-му классам точности. Меньшее колебание припуска и меньшая начальная неуравновешенность благоприятно сказываются на эксплуатации инструмента и «оборудования», особенно в автоматизированном производстве.
Правку валов производят после нормализации в горячем состоянии в штампе на прессе после выемки заготовки из печи без дополнительного подогрева.
Масляные отверстия в коленвалах соединяют обычно соседние коренную и шатунную шейку, и выполняются сверлением. Отверстия в щёках при этом зачеканиваются либо закрываются пробками на резьбе.
Механическая обработка коленчатых валов[править | править код]
Сложность конструктивной формы коленчатого вала, его недостаточная жесткость, высокие требования к точности обрабатываемых поверхностей вызывают особые требования к выбору методов базирования, закрепления и обработки вала, а также последовательности, сочетания операций и выбору оборудования. Основными базами коленчатого вала являются опорные поверхности коренных шеек. Однако далеко не на всех операциях обработки можно использовать их в качестве технологических. Поэтому в некоторых случаях технологическими базами выбирают поверхности центровых отверстий. В связи со сравнительно небольшой жесткостью вала на ряде операций при обработке его в центрах в качестве дополнительных технологических баз используют наружные поверхности предварительно обработанных шеек.
При обработке шатунных шеек, которые в соответствии с требованиями технических условий должны иметь необходимую угловую координацию, опорной технологической базой являются специально фрезерованные площадки на щеках[3]. По окончании изготовления коленчатые валы обычно подвергают динамической балансировке в сборе с маховиком (автомобильные двигатели).
В большинстве случаев коленчатые валы предусматривают возможность их перешлифовки на ремонтный размер (обычно 4-6 размеров, ранее было до 8). В этом случае коленвалы шлифуют вращающимся наждачным кругом, причём вал проворачивается вокруг осей базирования. Конечно, эти оси для коренных и шатунных шеек не совпадают, что требует перестановки. При перешлифовке требуется соблюсти межцентровое состояние, и согласно инструкции, валы после шлифовки подлежат повторной динамической балансировке. Чаще всего это не выполняют, потому отремонтированные двигатели часто дают большую вибрацию. При шлифовании важно соблюсти форму галтелей, и ни в коем случае не прижечь их. Неправильная обработка галтелей часто приводит к разрушению коленчатого вала.
Термическая и химико-термическая обработка валов[править | править код]
Коленчатые валы для увеличения прочности и износостойкости шеек подвергают термической, а иногда и химико-термической обработке: закалка ТВЧ, азотирование, закалка поверхностного слоя (стали регламентируемой прокаливаемости 55ПП, 60ПП). Получаемая твёрдость зависит от количества углерода (закалка ТВЧ, обычно не более 50..55 HRC), либо вида ХТО (азотирование даёт твёрдость 60 HRC и выше)[1]. Глубина закалённого слоя шеек позволяет обычно использовать 4-6 промежуточных ремонтных размеров шеек вала, азотированные валы не шлифуют. Вероятность задира шейки с ростом твёрдости значительно снижается.
При ремонте коленчатых валов используются также методы напыления, в том числе — плазменного. При этом твёрдость поверхностного слоя может повышаться даже выше заводских значений (для закалки ТВЧ), а заводские диаметры шеек восстанавливают до нулевого размера.
При эксплуатации из-за разных причин могут наблюдаться такие неисправности:
- износ вала по коренным или шатунным шейкам;
- изгиб;
- разрушение вала[4];
- износ посадочных поверхностей под маховик, сальник (сальники), переднюю шестерню.
При износе шеек выше допустимого или незначительном изгибе, устранимом перешлифовкой, коленчатый вал обрабатывают под следующий ремонтный размер. Однако при больших задирах (например, при выплавлении вкладышей с проворотом) иногда перешлифовывают «через размер», т.е. сразу на 2 размера. Все коренные шейки, а также все шатунные шлифуют в один размер — например, коренные могут быть 2-го ремонтного размера, а шатунные 3-го, в любой комбинации размеров. Коленчатые валы с подшипниками качения и азотированные перешлифовке не подлежат.
Однако руководства по армейскому полевому ремонту (двигатели боевых машин) обычно предписывают индивидуальный ремонт, поэтому шатунные/коренные шейки могут иметь разный диаметр после шлифовки, и даже не иметь стандартного ремонтного размера(!). Вкладыши при этом растачиваются парами, используются заготовки с минимальным внутренним диаметром. Плюсом является наивысшая скорость починки и унификация запчастей (вкладыши).
Разрушение вала происходит от усталостных трещин[4], возникающих иногда из-за прижога галтелей при шлифовке. Трещины развиваются в некачественном материале (волосовины, неметаллические включения, флокены, отпускная хрупкость) либо при превышении расчётных величин крутильных колебаний (ошибки при проектировании, самостоятельная форсировка по числу оборотов дизеля). Возможна поломка по причине превышения числа оборотов, отказе демпфера, заклинивания поршня[5]. Сломанный вал ремонту не подлежит. При износе посадочных поверхностей могут применяться электрохимическая обработка, плазменная или электродуговая наплавка поверхностей, а также другие решения.
- Кулаев Д. Х. Динамика кривошипно-ползунного механизма с зазорами в шатунных подшипниках // Научный журнал НИУ ИТМО. Серия «Холодильная техника и кондиционирование». — 2009. — ISSN 2310-1148.
ru.wikipedia.org
Материалы для коленчатого вала
Для изготовления коленчатых валов применяются стали 45, 45А, 40Х, 20Г2 и 50Г. В дизелях, работающих с давлением наддува рк ^ 0,15 Мн/м2 (1,5 кГ/см2), для коленчатых валов используют высоколегированные стали 18ХНМА, 18ХНВА и 40ХНМА с повышенными пределами текучести и прочности.
Обычно коленчатые валы изготовляют ковкой. В последнее время стали применять литые коленчатые валы из высокопрочного чугуна, модифицированного магнием, перлитного ковкого чугуна, легированного никельмолибдено-вого чугуна.
Наибольшее применение для литых коленчатых валов получил высокопрочный ВЧ 50-1,5 (НВ 187—255) и перлитовый чугун.
Литые коленчатые валы имеют следующие преимущества по сравнению с коваными: меньший расходметалла,сокращениечисла операцийпримеханическойобработке,возможность придания оптимальных форм в отношении распределения металла и повышения усталостной прочности.
Литые коленчатые валы из чугуна обладают лучшей способностью гашения крутильных колебаний.
Литые чугунные валы обладают меньшей прочностью (особенно на изгиб), чем штампованные стальные валы. Поэтому у чугунных валов увеличивают диаметры шатунных и коренных шеек, толщину щек и радиусы галтелей. Чугунные коленчатые валы изготовляют полноопорными. Шейки чугунных валов имеют высокую износостойкость, что позволяет применять подшипники из свинцовистой бронзы.
Масса обработанного литого коленчатого вала на 10—15% меньше массы кованого.
После ковки коленчатые валы отжигают или нормализуют для снятия внутренних напряжений и понижения твердости до НВ 163—269,чтобы облегчитьмеханическую обработку.После механической обработки коленчатые валы перед шлифованием подвергают вторичной термической обработке (закалка и отпуск), что значительно улучшает их механические свойства и повышает поверхностную твердость шеек. Обычно вторичная термическая обработка производится с нагревом т. в. ч. (токами высокой частоты).
Глубина закаленного слоя должна быть не менее 3—4 м.и, чтобы после перешлифования шеек коленчатого вала под ремонтные размеры толщина закаленного слоя была не менее 1 мм. Твердость шеек коленчатого вала из стали 50Г HRC52—62, а из стали 45Г2 — HRC48—50.
maestria.ru
Коленвал Википедия
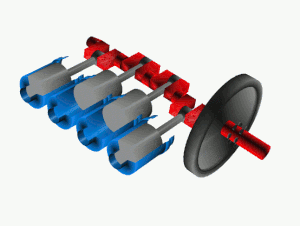
Коленчатый вал — деталь (или узел деталей в случае составного вала) сложной формы, имеющая шейки для крепления шатунов, от которых воспринимает усилия и преобразует их в крутящий момент. Составная часть кривошипно-шатунного механизма (КШМ).
История[ | ]
Впервые столь важную механическую деталь как коленчатый вал описал и сконструировал средневековый учёный Аль-Джазари в Османской империи в 13 веке. В 1206 году в трактате «Китаб фи марифат аль-хиял аль-хандасийя» (Книга знаний об остроумных механических устройствах) описан механизм вала.
Основные элементы коленчатого вала[ | ]
- Коренная шейка — опора вала, лежащая в коренном подшипнике, размещённом в картере двигателя.
- Шатунная шейка — опора, при помощи которой вал связывается с шатунами (для смазки шатунных подшипников имеются масляные каналы).
- Щёки — связывают коренные и шатунные шейки.
- Передняя выходная часть вала (носок) — часть вала на которой крепится зубчатое колесо или шкив отбора мощности для привода газораспределительного механизма (ГРМ) и различных вспомогательных узлов, систем и агрегатов.
- Задняя выходная часть вала (хвостовик) — часть вала соединяющаяся с маховиком или массивной шестернёй отбора основной части мощности.
- Противовесы — обеспечивают разгрузку коренных подшипников от центробежных сил инерции первого порядка неуравновешенных масс кривошипа и нижней части шатуна.
Размеры коленчатых валов[ | ]
Определяются как результат расчётов, причём часть размеров задаётся исходя из выбранной компоновки. Например, количество шатунных шеек определяется в зависимости от числа цилиндров. В многорядных двигателях (V, W, X-образных, звездообразных) одна шатунная шейка воспринимает нагрузки сразу нескольких шатунов (или одного центрального, соединённого с прицепными). Коленчатый вал воспринимает крутящий момент, имеющий переменное значение, а следовательно, работает на скручивание и должен иметь достаточный запас прочности (обычно 2,5) по усталостному напряжению на сдвиг.
Стальные валы (чаще всего) имеют невысокое внутреннее демпфирование крутильных колебаний, что
ru-wiki.ru
Материалы для изготовления коленчатых и прокатных валов
Литые коленчатые валы имеют преимущества по сравнению с валами из кованой стали. Они обеспечивают экономию металла, снижение трудоемкости, сокращение технологического цикла. Большие возможности имеются в отношении совершенствования конструкции литого вала.
Сплавы, применяемые для коленчатых валов, можно разделить на содержащие в своей структуре графит (чугуны, графитизированная сталь) и не содержащие графит (углеродистая и легированная стали). Сплавы первой группы более износостойки. Поточность производственного процесса легче осуществлять при изготовлении чугунных валов.
Перлитный ковкий чугун как материал для изготовления коленчатых валов, занимает в зарубежном производстве второе место после стали. Это объясняется, в частности, ускоренным отжигом ковкого чугуна за счет добавки к жидкому чугуну висмута и бора. Для прокатных валов и тормозных барабанов чугун с шаровидным графитом не имеет больших преимуществ перед другими чугунами вследствие пониженной теплопроводности.
Стали для валков холодной прокатки 9X2, 9Х2МФ и другие имеют высокую сопротивляемость сухому трению. Для валков горячей прокатки используют стали 60ХН, 55Х и др.
Если за «1» принять стоимость вала, изготовленного из высококачественного чугуна с пластинчатым графитом без термообработки, то стоимость вала из перлитного ковкого чугуна будет 2,5…3,0; из чугуна с шаровидным графитом без термообработки — 1,25, а с термообработкой — 1,5; из углеродистой стали — 2,5; из легированной хромистой стали — 2,8; из графитизированной стали — 3,0…3,3; из низкоуглеродистой легированной стали с нитроцементацией-2,9…3,2.


Схемы установок для испытаний на гидроабразивный износ:
а — машина ПВ-12М: 1 — электродвигатель; 2 -диск ротора; 3 — конический бак; 4 — винтовой механизм; б — машина УГИ-8М с зажимными дисками: 1 — электродвигатель мощностью 1,5 кВт; 2 — защитный диск; 3 — зажимной диск; 4 — резиновый диск; 5 — диск с образцами; б — стягивающие болты; 7 — втулки для крепления образцов; 8 — испытываемые образцы; 9 — гидроабразивная эмульсия (смесь воды с песком)
Углеродистая сталь уступает чугунам с шаровидным графитом:
- при почти одинаковых механических свойствах стали и чугуна плавка и разливка чугуна проще;
- в чугунах образуется меньше трещин;
- износостойкость валов, изготовленных из чугуна без термообработки, не ниже, чем валов из углеродистой стали, шейки которых закалены ТВЧ.
Графитизированная сталь, в структуре которой имеются включения графита, по свойствам близка к чугуну с шаровидным графитом, обладая, однако, более высокими механическими свойствами. Из модифицированных чугунов с пластинчатым графитом, имеющих меньший модуль упругости, можно изготовлять коленчатые валы, менее чувствительные к нарушению правильности осевой линии, чем стальные валы. Этим чугунам свойственны высокие динамические характеристики материала.
Чугун с шаровидным графитом и металлической основой из пластинчатого или зернистого перлита — наиболее распространенный материал для изготовления коленчатых валов двигателей автомобилей, тракторов, комбайнов, тепловозов и др.
Основной операцией термообработки коленчатых валов является старение.
Многообразие условий работы пар трения и явления фрикционной анизотропии затрудняют выбор оптимальных износостойких структур и литейных сплавов, обеспечивающих надежную и длительную работу деталям машин и механизмов. Однако теоретические и экспериментальные работы, выполненные в Беларуси и за рубежом, позволяют обосновать общие рекомендации по выбору износостойких материалов для ряда деталей и конкретных случаев эксплуатации и разработать более износостойкие изделия.
Металлическая матрица в чугунах должна быть прочным основанием для твердых карбидов, предотвращающим их микроскопическое выкрашивание и растрескивание при абразивном изнашивании в процессе эксплуатации литых заготовок. Наличие в мартенситной структуре до 15 % аустенита не снижает износостойкость. Отливки из белого чугуна с аустенитной или мартенситной структурой металлической основы обладают высокой абразивной износостойкостью, плохо обрабатываются резанием, особенно при наличии карбидов; они имеют низкую пластичность.
Для неприработанных поверхностей удельная нагрузка нелинейно влияет на износ, причем в большей мере для поверхностей с малой площадью контакта. Износ в случае сухого трения часто происходит при высоких температурах, что требует придания фрикционным сплавам повышенной термической стойкости.
Высокой износостойкостью при сухом трении обладают чугуны ЧГ6СЗШ, ЧГ7Х4, ЧХ28Д2, ЧН19ХЗШ, ЧЮ22Ш и др., выпускаемые для отливок со специальными свойствами в соответствии с требованиями ГОСТ 7769-82. В отливках из легированного чугуна с шаровидным графитом включения его должны быть шаровидной формы. Допускаются включения пластинчатой и вермикулярной формы — не более 20 % от общего количества. Высокохромистые чугуны ЧХ22С, ЧХ23Н и 4Х28Д2 подвергают термической обработке для снятия внутренних напряжений в отливках.
Литые детали для работы при ударно-абразивном и гидроабразивном износе. Такие детали изготовляют из экономнолегированных питейных углеродистых и марганцовистых сталей и хромистого чугуна ЧХ16М2. Это износостойкие литые детали гидромашин, перекачивающих абразивные смеси; футеровки дробилок, катки и другие детали угле- и рудоразмольных мельниц; ковши пескометов; склизы, течки и лопатки дробеметных импеллеров; менее ответственные детали из низколегированных чугунов и сталей, подвергаемых нормализации по режимам, приведенным в таблице.
Высокую ударную вязкость (не менее 2 Дж/см2) имеют чугуны ЧНП20Д2Ш и ЧН19ХЗШ, используемые для изготовления деталей насосов, гидротурбин, выпускных коллекторов. У экономнолегированных стапей 30XMЛ и 30XHMЛ она более 30 Дж/см2. Для выплавки экономно- легированных молибденом и никелем литейных сталей на БМЗ используются совмещенная технология плавки, включающая загрузку в 100-тонные печи ДСПБ-1200 никельсодержащих (ГИАП-16) и алюмомо- нибденкобальтовых (АКМ) катализаторов в смеси с известняком с последующей загрузкой на них металлосодержащих компонентов шихты. В таблице приведены химические составы и механические свойства серийных и опытной литейных сталей. Составы шихты для выплавки сталей даны в таблице
Совмещенная технология выплавки стали типа 30XHMЛ обеспечивает требуемый уровень легирования никелем и молибденом при достаточно высокой степени их усвоения (78 и 89 % соответственно). Легирование углеродистой стали никелем и молибденом обеспечивает требуемую хладостойкость сталей в отливках большегрузных автомобилей «БелАЗ».
Химические составы и свойства углеродистых сталей
Содержание элементов, % | Механические свойства отливок | |||||||||
Сталь | Si | Мп | Сг | Ni | Мо | а„, МПа | 8,% | KCU, Дж/см2 | ||
С | +20 °С | -20 °С | ||||||||
40Л | 0,37… 0,45 | 0,2… 0,52 | 0,4… 0,9 | Менее 0,3 | Менее 0,3 | Более 530 | Более 14 | Более 29 | Не рег- ламен- тиру- ется | |
35XM | 0,3… 0,4 | 0,2… 0,4 | 0,4… 0,9 | 0,8… 1,1 | Менее 0,3 | 0,2… 0,3 | Более 600 | Более 12 | Более 30 | ft |
Применяемая на машине М200 фирмы «Юнит Риг» | 0,35 | 0,28 | 1,33 | 0,20 | 0,5… 2,0 | 0,2… 0,5 | 600… 800 | 10… 20 | 30… 50 | 8,0… 20 |
Опытная ЗОХНМЛ | 0,3 | 0,35… 0,45 | 0,5… 0,6 | 0,5… 0,7 | 1,3… 1,5 | 0,3… 0,4 | 690… 790 | 12… 20 | 30… 45 | 7,0… 20 |
75ХНМФЛ* | 0,75 | 0,3 | 0,52 | 0,8 | 0,96 | 0,5 | Более 720 | Более 12 | Более 25 | 7,0… 15 |
Фазовый состав хромомарганцевоникелевых сталей
Сталь | Фазовый состав, % | Параметр а*, нм | (Да / а)-103, рад | Микротвердость Н | ||||||
5-феррит | У | ОЦК** | ГЦК*’ | ОЦК” | ГЦК” | 5-феррит | Y | |||
05Х18Г2Н5Т | 62 | 7 | 31 | 0,2868 | 0,3591 | 9,3 | 4,8 | 261 | 332 | — |
05Х18Г2Н5АТ | — | Следы | 100 | — | 0,3594 | — | 5,0 | — | — | 304 |
05Х18Г10Н5МЗФ | — | 32 | 68 | — | 0,3602 | 4,6 | 3,5 | 277 | — | 293 |
05Х18Г10Н5МЗАФ | — | 6 | 94 | — | 0,3612 | — | 3,1 | 282 | — | 263 |
Параметр решетки.
* ОЦК, ГЦК — фазы кристаллической решетки.
Распределение фаз и легирующих элементов в Cr-Mn-Ni-сталях
Состояние металла | Сод Ф | ержание аз, % | Содержание легирующих элементов в фазах, % | |||||||||||||
Сталь | мар | 5- | Мп | Сг | Ni | Ti, Мо | ||||||||||
тен сит | фер- рит | у- фаза | 5 | У | К* | 5 | У | К* | 5 | У | К* | 5 | У | К* | ||
05Х18Г2Н5Т | Деформи рованный | 71 | 7 | 22 | 1,08 | 2,1 | 1,15 | 20,0 | 16,0 | 1,25 | 4,4 | 7,2 | 1,65 | 0,20 | 0,20 | 1,0 |
Литой (центр) | 62 | 7 | 31 | 1,75 | 2,1 | 1,20 | 21,0 | 15,0 | 1,35 | 3,7 | 7,9 | 2,20 | 0,20 | 0,20 | 1,0 | |
05Х18Г2Н5АТ | Деформи рованный | — | — | 100 | — | 2,2 | — | — | 16,0 | — | — | 8,9 | — | — | 0,15 | — |
Литой (центр) | — | Сле ды | 100 | 1,90 | 2,5 | 1,30 | 18,0 | 14,0 | 1,30 | 3,0 | 8,1 | 2,70 | 0,15 | 0,15 | 1,0 | |
05Х18Г10Н5МЗФ | Деформи рованный | — | 32 | 68 | 7,90 | 9,2 | 1,15 | 21,0 | 17,0 | 1,25 | 3,8 | 6,2 | 1,65 | 3,60 | 2,25 | 1,60 |
Литой (центр) | — | 32 | 68 | 8,0 | 9,3 | 1,15 | 21,0 | 17,0 | 1,25 | 3,5 | 6,3 | 1,80 | 3,80 | 2,20 | 1,75 | |
05Х18Г10Н5МЗАФ | Деформи рованный | — | 8 | 92 | 8,0 | 9,2 | 1,15 | 19,0 | 17,0 | 1,15 | 4,2 | 6,8 | 1,60 | 4,00 | 2,50 | 1,60 |
Литой (центр) | — | 6 | 94 | 7,0 | 9,5 | 1,35 | 19,0 | 16,0 | 1,20 | 4,2 | 9,3 | 2,20 | 3,90 | 2,30 | 1,70 |
* К — коэффициент распределения легирующего элемента: К
Cmax I Cmin, ГДе Стах И
Cmin — максимальное иминимальное содержание элемента соответственно.
Состав шихты при выплавке углеродистых сталей
Материалы шихты | Масса, кг | |
Сталь 40Л | Сталь ЗОХНМЛ | |
Возврат литейного производства | 1600…2500 | 2000 |
Пакеты стальные | 3500…4500 | 4165 |
Ферромарганец | 40…70 | 60 |
Ферросилиций | 30…70 | 40 |
Феррохром | 70…80 | 75 |
Катализаторы АКМ | — | 200 |
Катализаторы ГИАП-16 | — | 500 |
Изменение химического состава стали ЗОХНМЛ в процессе плавки
Период плавки стали ЗОХНМЛ | Содержание легирующих элементов, % | Усвоение, % | ||
Ni | Мо | Ni | Мо | |
Расплавление шихты | 0,9 | 0,25 | 50 | 64 |
Раскисление | 1,4 | 0,32 | 77 | 82 |
В готовой стали | 1,41 | 0,35 | 78 | 89 |
При больших нагрузках, высоких скоростях и корродирующем охлаждении плиты направляющих, а также подушек в прокатных клетях и агломерационных установках, интенсивный износ снижает точность и качество прокатки, приводит к простоям установок и высоким расходам на ремонт.
Фирма «CORTS» широко в мире заменяет неупрочненные, с упрочненной поверхностью и цементируемые изнашиваемые плиты и планки другими плитами и планками из специальной стали марок «CORTS-g» и «CORTS-g-Stainless». Такие плиты и планки обеспечивают более высокую надежность и долговечность работы прокатного и агломерационного оборудования.
Выбор оптимальных технологических способов повышения износо- стойкости и предотвращения образования повреждений на рабочих поверхностях пар трения зависит не только от условий их контактирования, но и от химсостава и структуры используемых металлов и сплавов. К важным факторам, определяющим сопротивление металлических сплавов изнашиванию, являются свойства, взаимное расположение, количественное соотношение и характер связи отдельных составляющих структуры.
Известно, что двухфазные хромомарганцевые стали типа «микродуплекс» с мелким зерном (до 5 мкм) имеют недостаточно высокую пластичность, особенно при температурах около 850…900 °С. Эти стали склонны к хрупкому разрушению и обладают низкой термостойкокостью. Присутствие в составе сталей азота и титана увеличивает ликвацию марганца, хрома и никеля. Основные легирующие элементы этих сталей по возрастанию склонности к ликвации можно расположить в следующий ряд: Ti, Мn, Сг, Мо и Ni. Характеристики структуры и свойств ряда двухфазных сталей по результатам исследований приведены в
Для изготовления износостойких деталей разработаны литейные сверхпластичные стали и Fe-Cr-Mn-Al-Ti-N-C-сплавы с карбонит- ридным упрочнением.
В металлургической промышленности освоены Fe-Cr-Ni-Ti-C-стали (например, сталь 08Х17Н61), (DU 21) — для деталей оснастки, и безни- никелевые стали для производства холоднокатанного листа по ГОСТ 5632- 72. Это стали ферритного класса марок 08X17Т и 08X18Т (DU 77), выплавляемые в соответствии с ТУ 14-1-4017—85 и используемые в продовольственном и текстильном машиностроении для получения деталей методами штамповки, вытяжки, гибки и сварки. Ударная вязкость сталей 20…60 Дж/см2. Предложена также сложнолегированная хромоникельалюминиевая сталь с повышенными упругопластическими свойствами и низким содержанием никеля.
Износостойкие сплавы на основе Ni3Al являются типичными полу-хрупкими материалами. Повысить их механические свойства можно посредством легирования такими элементами, как молибден, тантал, медь. Сложнолегированные сплавы на основе Ni3Al могут быть использованы в качестве конструкционных для работы при повышенных температурах. Однако данные по трещиностойкости не только сложных сплавов, но и просто легированного Ni3Al отсутствуют.


chiefengineer.ru
Что такое коленчатый вал? Назначение и особенности конструкции
ДВС состоит из нескольких узлов и механизмов. Один из самых важных – кривошипно-шатунный. Он включает в себя поршни, шатуны, кольца, а также коленчатый вал. О функциях и устройстве последнего – далее.
Назначение
Для чего нужен коленвал? Данный механизм служит для преобразования движений поршня в энергию кручения. Иными словами, узел передает силу сжатия, что образовалась после такта воспламенения смеси в камере, на маховик, а далее на колеса авто посредством диска сцепления и КПП.
Так как ДВС всех автомобилей четырехтактные, каждый поршень в определенный момент будет находиться в одном из таких положений:
- Впрыск смеси.
- Сжатие.
- Рабочий ход.
- Выпуск отработанных газов.
После такта сжатия, поршень начинает двигать шейки коленчатого вала. В результате последний проворачивается. Энергия от вращения идет на маховик.
Читайте также: Как работает двигатель внутреннего сгорания
Что такое коленвал? Это деталь КШМ, которая принимает на себя кинетическую энергию и преобразует ее во вращательную. Помимо КПП, энергия поступает на шкив генератора, компрессора кондиционера, гидроусилителя и прочего навесного оборудования. В том числе при вращении коленвала работает водяной насос, циркулируя охлаждающую жидкость в системе. Различие в том, что на трансмиссию энергия передается через заднюю часть вала. А навесное оборудование и ГРМ приводится в действие через переднюю его часть.
Требования
Мы уже знаем, для чего нужен данный узел. Так как он является основной кривошипно-шатунного механизма, к нему предъявляются особые требования. Вал должен выдерживать колоссальные нагрузки во время работы ДВС. Поэтому изготавливается он из высокопрочных сплавов и чугуна с добавлением молибдена и хрома.
Высокие требования предъявляются не только к составу, но и технологии изготовления механизма. На обычных ДВС коленвал изготавливается методом чугунного литья. А вот для форсированных, спортивных авто, вал должен быть кованым. Изготавливаются такие механизмы из особых сплавов. Данный коленчатый вал имеет более меньший вес, что позволяет увеличить мощность ДВС и его КПД. Почему такие валы не изготавливаются повсеместно? Ответ кроется в стоимости изготовления. Технология, по которой выполняются кованые валы, сложная и дорогая. Это значительно увеличит конечную стоимость ДВС и самого автомобиля.
Расположение, особенности конструкции
Коленчатый вал установлен под блоком цилиндров, внутри картера ДВС. При таком расположении механизм находится в масляной ванне (за счет чего обеспечивается смазка, рассмотрим позже). Но есть и исключения. Это оппозитные ДВС автомобилей «Порш» и «Субару». В этих авто цилиндры располагаются горизонтально, а потому коленвал находится между рядами цилиндров, в центре ДВС. Такая конфигурация привлекательна тем, что автомобиль имеет более низкий центр тяжести, а сам ДВС более компактный и хорошо отбалансирован.
Конфигурация колен, их число и расположение зависит от:
- Порядка работы цилиндров.
- Количества цилиндров в ДВС.
В устройство коленчатого вала входят:
- Опорные шейки. Выполняют опорную функцию. Данные шейки располагаются на главной оси вала.
- Шатунные шейки. Их особенность в том, что они смещены относительно вала. К шатунным шейкам крепятся шатуны. Именно через эти шейки передается толкательное усилие от поршней на коленчатый вал.
- Щеки. Для чего нужны они? Их функция – соединить шатунные и коренные шейки.
- Балансиры. Служат для исключения колебаний вала при его вращении.
- «Носок». Это передняя часть вала, что выступает за картер ДВС. На этом участке крепится шкив, благодаря которому вращается ремень ГРМ и ремни навесных агрегатов.
- Хвостовик. Это задняя часть вала. На хвостовике закреплен маховик. Именно он передает крутящий момент на коробку передач посредством ведомого диска сцепления.
- Сальники. Всего их два – передний и задний. Сальники служат для уплотнения соединений и предотвращают течь масла через хвостовик и «носок» вала.
- Подшипники. Служат для легкого вращения вала. Всего их несколько. Это подшипники хвостовика и «носка» коленвала.
О системе смазки
Так как вкладыши являются подшипниками скольжения, им требуется смазка. Она осуществляется под давлением. К опоре коренного подшипника вала обеспечивается подача смазки от общей магистрали. Масло подается под давлением.
Неисправности
Проблемы, возникающие с данным механизмом, проявляются в виде:
Основным условием сохранения заложенного производителем ресурса вала является своевременная замена масла и правильный его подбор по типу и вязкости. Среди основных неисправностей стоит выделить:
- Течь переднего и заднего сальника. Происходит по причине повышенных вибраций и засыхания самого материала. Со временем сальник становится менее упругим и пропускает через себя часть масла. Последнее попадает на внешнюю часть блока цилиндров, картер, КПП.
- Износ подшипников коленчатого вала в месте «носка» и хвостовика.
- Механическое повреждение вала. Это может быть трещина, сколы или изгибы механизма. Происходит по причине высокой кратковременной нагрузки и при проворачивании вкладышей. В случае трещин и изгибов вал является неремонтопригодным.
- Задиры на шейках (вкладышах). Это могут быть повреждения как коренных, так и шатунных вкладышей. Проблема решается путем их замены или шлифовки (зачастую выбирается первый вариант).
- Деформация посадочного места шкива.
Для замены или ремонта данного узла необходим демонтаж и полная разборка двигателя. Операция сложная, требующая опыта и наличия специальных инструментов. Сборка ДВС должна производиться в строгой последовательности, с соблюдением всех моментов затяжек болтовых соединений.
Читайте также: Что такое распредвал в автомобиле
В случае шлифовки, специалистом стачивается некоторая часть металла с механизма. А чтобы нивелировать зазор, который образовался после шлифования, подбираются вкладыши ремонтного размера. Обычно коленвал может растачиваться до четырех раз. Но условием расточки является абсолютная целостность механизма.
Заключение
Мы рассмотрели, что такое коленвал. Данный механизм является самым нагруженным среди прочих, поэтому к нему предъявляются особые требования при изготовлении. Ремонт вала целесообразен, но не всегда. При существенных дефектах он подлежит замене. Максимальный ресурс механизма может составить 4 пробега до капремонта ДВС, но только при условии своевременной замены масла, фильтров и работы ДВС с должным уровнем смазки.
Понравилась статья? Поделитесь в соц. сетях:
www.cars-life.org
Коленчатый вал ДВС
Коленчатый вал двигателя (коленвал) – деталь, которая принимает и затем преобразует усилие от шатуна в крутящий момент. Коленчатый вал испытывает периодические нагрузки, которые возникают от сил давления газов в результате сгорания топливно-воздушной смеси в камере сгорания, которые далее передаются на него через связку шатуна и поршня. Дополнительными силами воздействия на коленчатый вал является инерция, которая возникает в результате движения и вращения масс.
Материалом изготовления коленчатого вала становится сталь или высокопрочный чугун. Коленвал имеет коренные и шатунные шейки, которые соединяются щеками. Указанные щеки отвечают за то, чтобы сбалансировать механизм. Противовесом является продолжение щеки, которое находится в противоположном от шатунной шейки направлении. Противовес создан для того, чтобы уравнять вес шатунов и поршней. Так достигается необходимая плавность в процессе работы ДВС.
Коренные и шатунные шейки осуществляют вращение в специальных подшипниках скольжения, которые представляют собой разъемные тонкостенные вкладыши, изготовленные из стальной ленты, на которую дополнительно нанесен антифрикционный слой.
Шатунные шейки представляют собой опорную поверхность для каждого отдельного шатуна. Наибольшую нагрузку в конструкции коленвала испытывает место перехода от коренной или шатунной шейки к щеке. Для предотвращения того, чтобы коленчатый вал двигателя перемещался по оси, применяется упорный подшипник скольжения. Указанный подшипник устанавливают на средней или крайней коренной шейке коленвала.
Шейки и щеки коленчатого вала имеют высверленные внутри отверстия. Данные отверстия необходимы для подачи моторного масла, которое поступает под давлением к каждой отдельной шейке коленвала. Так реализован индивидуальный подвод смазки к каждой опоре коренной шейки от общей магистрали системы смазки. Моторное масло по каналам в щеках попадает к шатунным шейкам.
Мощность с коленчатого вала снимается с его заднего конца. Данный участок называется хвостовиком. Именно в этой части закреплен маховик, через который крутящий момент двигателя передается на коробку передач (КПП).Передний конец коленчатого вала называется носком коленвала, где располагаются места установки следующих элементов:
Коленвал испытывает постоянное воздействие, которое можно сравнить с тем, что его условно закручивает и раскручивает с определенной периодичностью. Результатом становится появление колебаний. По этой причине значительное число ДВС на носке коленвала имеют такой элемент, который получил название гаситель крутильных колебаний.
Данное решение конструктивно представляет собой два диска и упругий эластичный материал для их соединения, которым может быть резина, вязкая силиконовая или масляная жидкость, пружинное соединение и т.п. Основной задачей гасителя крутильных колебаний становится активное поглощение вибраций коленчатого вала, которое достигается благодаря наличию внутреннего трения.
Читайте также
Функции датчика коленчатого вала
Основные признаки, по которым можно самому определить проблемы с датчиком положения коленчатого вала ДПКВ. Причины сбоев, поломок, самостоятельная проверка.
krutimotor.ru
КОНСТРУКТИВНЫЕ И ТЕХНОЛОГИЧЕСКИЕ ОСОБЕННОСТИ КОЛЕНЧАТЫХ ВАЛОВ
Коленчатые валы бывают: составные, кованные, литые, цельные и изготавливаются из стали и чугуна. Например чугунные коленчатые валы в автомобильных двигателях стали применять с 1960 года. Высокопрочные чугуны по ГОСТ 7293-85 делятся на два класса: перлитные (ВЧ 45-0; ВЧ 50-1,5; ВЧ60-2) и ферритные (ВЧ40-0 ВЧ40-6). Коленчатый вал изготовляют горячей штамповкой из легированной стали (двигатели автомобилей ЗИЛ-130,МАЗ-5335,КамАЗ-5320 и др.) или отливаются из высокопрочного чугуна (двигатели автомобилей семейства ГАЗ, ВАЗ и др.) вместе с противовесами или без них. Коленчатый вал двигателей ЯМЗ-236, ЯМЗ-238 изготовлены из стали 50Г. В процессе изготовления вал подвергается термической обработке и отпуску до твердости 229-269 НВ, а поверхности шатунных и коренных шеек и шейки под сальники для повышения износостойкости подвергаются закалке с нагревом токами высокой частоты.(глубина закаленного слоя для коренных и шатунных шеек составляет 3,0-4,0 мм, а на шейках под сальник 1,0-2,0 мм; и твердость после закалки 52-62 HRC) .Коленчатые валы двигателей КамАЗ-740 изготавливаются горячей штамповкой из стали 42 ХМФА-Ш. В коленчатых валах широко применяется высокооловянные сталеалюминевые вкладыши вызвано тем, что они обладают повышенным сопротивлением усталости, хорошими противозадирными свойствами и коррозийной стойкостью, что увеличивает надежность двигателя. [1].
Виды и составные части коленчатых валов
На большинстве автомобильных двигателей применяют полно опорные коленчатые валы, т.е. каждая шатунная шейка расположена между двумя коренными. Таким образом, полно опорный вал имеет коренных шеек на одну больше чем шатунных. Полно опорные валы двигателей (Зил-130, КамАз-740, ВАЗ-2108) отличаются большой жесткостью, что повышает работоспособность КШМ. В машиностроении на автомобильных двигателях получили применение еще и неполно опорные коленчатые валы. В отличии от полно опорного коленчатого вала здесь шесть шатунных шеек и четыре коренных. Такие коленчатые валы устанавливаются на двигателя автомобилей ГАЗ-52-04. Например на легковых автомобилях семейства ВАЗ устанавливаются литые, чугунные, пяти опорные коленчатые валы (предусмотрена возможность пере шлифовки шеек коленчатого вала при ремонте с уменьшением диаметра на 0,25; 0,5; 0,75; и 1мм) с использованием двухслойных вкладышей, хорошо работающих в двигателях с большой частотой вращения коленчатого вала и большими нагрузками. Такой коленчатый вал показан на (рис 1.1.1) [1].
Рисунок 1.1.1 — Коленчатый вал двигателя автомобиля ВАЗ-2108
Коленчатые валы имеют еще свое различие по своей форме и строению. Форма коленчатого вала зависит от числа и расположения цилиндров, порядка работы и тактности двигателя. Например, рабочий цикл в однорядном четырехцилиндровом и шестицилиндровом двигателе совершается за два оборота коленчатого вала, т.е. за поворот вала на 720. Колена коленчатого вала расположены в трех плоскостях под углом 120.Шестицилиндровый V-образный двигатель располагает колена коленчатого вала в трех плоскостях под углом 120 одно к другому также как и в восьмицилиндровом V-образном двигателе но под углом 90. Форма. На рисунке 1.1.2 приведен полно опорный коленчатый вал двигателя автомобиля ЗИЛ-130. Коленчатый вал этого двигателя выполнен по крестообразной схеме (если смотреть с торца вала). Первая и четвертая шатунные шейки коленчатого вала направлены в разные стороны и лежат в одной плоскости. Вторая и третья шейки направлены в разные стороны, лежат в одной плоскости, но перпендикулярной первой. Перекрытие шеек составляет 22мм (перекрытие шеек применяется для повышения жесткости и надежности коленчатого вала). Диаметр шатунной шейки 65,5 мм, а коренной 74 мм. Данный коленчатый вал состоит из следующих частей: коренные 7 и шатунные 3 шейки, щеки 8, противовесы 4, передний конец 1 и задний конец (хвостовик) с маслоотражателем 5, маслосгонной резьбой и фланцем 6 для крепления маховика [9].
Рисунок 1.1.2 — Коленчатый вал двигателя автомобиля ЗИЛ-130
На рисунке 1.1.3 приведен коленчатый вал двигателя ЯМЗ-236. Характерной конструктивной особенностью двигателя ЯМЗ-236 являются развитые по диаметру, но относительно короткие коренные и удлиненные шатунные шейки, что является закрепленной пары шатунов на общую шейку. Коленчатый вал данного дизеля не имеет фланцев для крепления маховиков, также как и коленчатый вал двигателя КамАз-740. Вкладыши коренных подшипников трехслойные, с рабочим слоем из свинцовистой бронзы. Диаметр шатунной шейки 88 мм, а коренной 110 мм. Коленчатый вал двигателя ЯМЗ-236 имеет, три шатунные шейки 3, расположенные под углом 120, и четыре коренные шейки
Рисунок 1.1.3 — Коленчатый вал двигателя ЯМЗ-236
На рисунке 1.1.4 приведен коленчатый вал двигателя автомобиля КамАЗ-740. В данном коленчатом вале в шатунных имеются грязеуловительные полости 2, для дополнительной центробежной очистки масла. Грязеуловительные полости устанавливаются на коленчатых валах у большинства дизельных двигателей. Коленчатый вал данного дизеля не имеет фланцев для крепления маховиков, также как и коленчатый вал двигателя ЯМЗ-236. Шатунные шейки коленчатого вала располагаются так, чтобы одноименные такты (например, такты расширения) в различных цилиндрах двигателя проходили через равные промежутки (по углу поворота коленчатого вала) а силы инерции, возникающие в цилиндрах, взаимно. Если расположение колен коленчатого вала не обеспечивает взаимного уравновешивания сил инерции и создаваемых ими моментов, то на таких коленчатых валах устанавливают противовесы или оборудуют двигатели специальными уравновешивающими механизмами. Диаметр шатунной шейки 80 мм а коренной 95 мм. От осевого смешения коленчатые валы дизелей удерживаются двумя парами упорных полуколец из бронзы или сталеалюминия установленных в выточках задней коренной опоры.
Рисунок 1.1.4 — Коленчатый вал двигателя КамАЗ-740
www.autoezda.com