Полезная информация для изготовления стеклопластика
Стеклопластик это материал, состоящий из двух основных компонентов. Это материал из стекловолокна (стекловолокно, стеклоткань, стекломат), который служит для армирования (усиления) изделия, и смолы, являющейся связующим.
Материалы для изготовления стеклопластика.
Смола
Смола является связующим материалом и поэтому к выбору смолы надо подойти наиболее ответственно, особенно при отсутствии опыта изготовления стеклопластиковых изделий. Если при выборе стеклоткани или стекломата можно довольствоваться рекомендациями специалистов, т.к. этим выбором определяются, в основном, механические свойства готового изделия, то разная смола требует разных технологических процессов.
Для начинающих мы рекомендуем эпоксидную смолу. Эпоксидная смола менее привередлива в работе и имеет большее время застывания и поэтому у вас будет больше времени для исправления возможных ошибок. Эпоксидную смолу также рекомендуется использовать при ремонте изделий (лодок, бамперов…). Она хорошо склеивается с пластиком, деревом, металлом.
Полиэфирная смола, в основном, используется для изготовления цельных деталей
Хотим также напомнить, что на свойства смол и на их рабочие параметры довольно сильно влияют температурные характеристики помещения, в котором производятся работы, и его проветриваемость. Порой для лучшего застывания матрицу с изделием помещают в специальную сушильную камеру. Это помогает значительно ускорить процесс получения готового изделия. Самые прочные изделия изготавливаются в автоклавах под большим давлением и при высокой температуре.
Сама смола достаточно хрупкая, и именно стекломатериал придает ей необходимую прочность и гибкость
Материалы из стекловолокна
Для изготовления стеклопластиков используется стекловолокно, ровинг, стекломат, стеклоткань и другие стекломатериалы.
Самые распространенные это ровинг, стекломат и стеклоткань.
Ровинг
Ровинг это стекловолокно собранное в пучок и намотанное на бобину. Ровинг похож на некрученую стеклонить. Укладка ровинга производится специальным пистолетом, в который, во время работы, подается еще смола и катализатор.
Стекломат
Стекломат состоит из хаотично расположенных волокон, а стеклоткань выглядит как обычная ткань. Наибольшее упрочнение дают стеклоткани. Стекломаты дают меньшую прочность, но они более легки в обработке и по сравнению со стеклотканью лучше повторяют форму матрицы.
Стекломат может быть очень тонким, а бывает толстым, как одеяло. Стекломаты различаются по толщине и плотности, но разделяют их по весу одного квадратного метра материала в граммах: 300, 450, 600. Чем тоньше мат, тем более сложную поверхность он позволяет вывести, с большим количеством граней и резких переходов. Толстый мат (600 или 900) позволяет набрать толщину изделия и добиться необходимой прочности. При создании толстых изделий работа проходит в несколько этапов. Выкладывается несколько листов для получения первого слоя и дается время на застывание. Затем дополнительно, уже на твердую поверхность, укладываются дополнительные листы мата для придания необходимой толщины. Если попытаться уложить сразу все слои, то велика вероятность, что готовое изделие покоробится, стянется.
Стеклоткань
Стеклоткани бывают разной толщины. Стеклоткани также используются для придания жесткости и объема готовому изделию. Как и любая ткань, стеклоткань неодинаково работает при разнонаправленном растяжении. Поэтому для придания необходимой жесткости стеклоткань укладывается под разными углами. Стекловолокно в стеклоткани играет немаловажную роль. Оно должно хорошо пропитываться смолой и удерживать ее между волокнами. На это свойство пропитываемости в стеклоткани влияет наличие в ней и количество парафина. На ответственные изделия желательно выбирать стеклоткани без парафина. Парафин также можно выжигать перед применением.
К слову о прочности. Как это ни странно прозвучит, но чем меньше смолы в стекловолокне (при условии его полной пропитки и отсутствии пузырьков), тем прочнее будет готовое изделие и тем меньше окажется и его вес.
Гелькоут (gelcoat)
Для придания цвета готовой детали , а также для защиты от внешних воздействий используется особый материал гелькоут (gelcoat – гелевое покрытие). Можно сказать, что гелькоут это та-же смола, но с добавлением красителя. Его можно подобрать по цвету или создать свой оттенок колеровочными составами. Кроме того, слой гелькоута увеличивает срок службы изделия, защищает от воздействий окружающей среды и скрывает структуру стеклопластика. Готовое изделие будет иметь ровную (зависит от качества матрицы) поверхность, нужного цвета.
Гелькоуты бывают внутренними и внешними (topcoat).
Внутренний гелькоут наносится первым слоем в матрицу. После того как гелькоут затвердел, укладывается стекловолокно и смола. В этом процессе кроется один важный момент. Если слой гелькута будет в одном месте слишком тонкий, то может случиться следующее: или в этом месте будет просвечивать структура стекловолокна, или гелькоут может вообще отойти и сморщиться. Поэтому крайне важно пользоваться правильными материалами и следовать технологии. Для равномерного нанесения гелькоута часто используют не кисти, а краскопульты. Так удается значительно сократить количество брака и уменьшить расход материала. Но для распыления гелькоут должен быть более жидким, чем для ручного нанесения. В настоящее время в продаже имеются готовые гелькоуты для нанесения кистью и для напыления.
Внешний гелькоут (topcoat) наносится после того, как изделие вынули из матрицы. Здесь он выполняет роль краски. Благодаря присутствию в составе топкоута парафина поверхность после отверждения не остается липкой, хорошо шкурится и полируется. Топкоут можно изготовить самим на базе гелькоута или смолы, добавив раствор парафина в стироле.
Макет и матрица
Для изготовления изделия из стеклопластика первое, что необходимо, – создать его макет. В некоторых случаях макетом может являться уже существующее изделие, которое Вы хотите размножить. Например: бампер автомобиля. Для еще не существующих изделий макет может быть изготовлен различными способами: фанера, пластилин, пенопласт и т. д. От того, насколько правильно сделан макет, будет зависеть качество будущих изделий. Более того, если необходимо, чтобы у детали, которая будет затем создаваться, была идеально ровная поверхность, над ее качеством придется поработать уже на макете. Чем более гладким и ровным будет макет, тем меньше работы потребуется потом, при изготовлении и доведении матрицы.
Еще до создания макета необходимо понять, можно ли изготовить деталь целиком или нет. Дело в том, что при работе со стеклопластиками и другими подобными материалами необходимо, чтобы готовую деталь после застывания можно было вытащить из матрицы, ничего не повредив при этом. Возможно, деталь будет иметь такую форму, что ее придется изготавливать из нескольких частей, а затем скреплять их друг с другом.
Матрица создается по макету. Это самый ответственный момент. Прежде всего макет покрывается тонким слоем воска. Эту процедуру можно сравнить с полировкой автомобиля. После того как макет подготовлен, на него наносится слой специального матричного гелькоута. Это покрытие в дальнейшем позволит вывести поверхность матрицы практически до зеркального блеска. Матричный гелькоут гуще, чем обычный, и ложится более толстым слоем.
После того как встанет этот слой, начинается укладывание стекломатериала. Сначала более тонкого (стекловуаль, …). Он позволит точно повторить все изгибы и контуры макета. Далее желательно дать подсохнуть первому слою. Затем уже можно выложить еще несколько слоев более толстого материала (мат, стеклоткань), но сразу набирать толщину не стоит, иначе матрицу может повести (изогнуть и покоробить). При создании матриц на простые детали можно упростить процедуру.
Если матрица будет разъемной, то при ее изготовлении делаются специальные перегородки вокруг макета, разделяющие его на сегменты. Выложив основной, после его застывания перегородки вынимаются и, обработав кромки первого сегмента матрицы, выкладываются остальные. Для правильного позиционирования сегментов друг относительно друга в первом при формовании делаются специальные ямки. Когда будут формоваться следующие сегменты, эти ямки будут заполнены смолой и стекловолокном, и появятся бугорки. Эти пары и позволят при будущем использовании правильно скрепить различные части матрицы воедино. Для скрепления сегментов матрицы в ребрах всех отдельных частей сверлятся отверстия под крепежные болты.
Для того чтобы матрица была прочной и хорошо держала форму, после ее изготовления, прежде чем вынуть макет, к матрице приформовывают ребра жесткости. В зависимости от ее размеров это может быть прочный стальной каркас или небольшие фанерные или деревянные ребра.
Готовая матрица, если макет был изготовлен аккуратно, может и не потребовать дополнительной обработки, но зачастую приходится выводить поверхности, шлифовать и полировать матрицу до блеска. Только тогда можно получить идеальную деталь. А к кузовным элементам вообще нужно особое внимание.
Затем начинается долгий процесс вощения. Матрицу приходится тщательно натирать воском несколько раз с перерывами. Воск нужно не просто намазывать, а растирать до получения тонкой, гладкой, невидимой пленки. Если этого не сделать, то поверхность готового изделия будет не гладкой, а шершавой.
После, а порой и вместо вощения иногда используют специальные жидкости, которые, высыхая, создают пленочное покрытие, предотвращающее попадание смолы или гелькоута на матрицу, чего никак нельзя допускать. Как нельзя и царапать ее поверхность. В противном случае смола может намертво прирасти к матрице, и тогда процедуру шлифовки, полировки и вощения придется повторять снова. Порой используют особые составы, обработав которыми матрицу можно снимать с нее до 100 изделий, но старый добрый воск всегда остается самым понятным и надежным средством.
Процесс создания матрицы, описанный выше, является довольно распространенным вариантом, используемым в большинстве фирм, но существуют и другие, более сложные технологии.
Собственно, далее можно приступать к изготовлению деталей. Слой гелькоута в принципе не обязателен, но, во-первых, он придает более законченный вид готовому изделию, а будучи цветным, позволяет сэкономить на покраске или вообще от нее отказаться, а во-вторых, он защищает матрицу от стекловолокна, которое на самом деле очень даже абразивно, т. е. царапает.
Технологии
Технологий производства изделий из стекловолокна существует несколько. Стоит сразу оговориться, что эти методы используются и при работе с другими армирующими материалами, такими, как карбон, кевлар, другие тканые материалы и их сочетания.
Ручное (контактное) формование. Этот способ самый простой и дешевый (если не считать затрат на квалифицированную рабочую силу). Пропитка стекловолокна осуществляется валиком или кистью, которые должны быть стойкими к смолам. Волокно или сразу укладывается в форму, или уже после пропитки. Обработка стекловолокна разбивочными валиками способствует лучшему распределению смолы между волокнами. Затем укаточными валиками производят окончательную укатку стеклоткани, выдавливая пузырьки воздуха и равномерно распределяя смолу по всему объему. Крайне важно не допустить, чтобы под слоем стеклоткани оставались пузырьки воздуха. Если изделие застынет с таким браком, это место будет ослаблено вплоть до возможного сквозного продавливания. Такие брачки также могут помешать дальнейшей обработке изделия, потребовать его восстановления или полной замены. В любом случае будут затрачены дополнительные материалы, труд, а также деньги.
Ручной метод может быть несколько механизирован. Существуют смесители, подающие смолу с катализатором через валик, и иные приспособления. Но укатывать все равно приходится своими руками.
Достоинство ручного метода вполне очевидно: просто и дешево. Но любая экономия может иметь и обратную сторону. Качество готовых изделий очень сильно зависит от квалификации рабочих. И условия труда при таком подходе довольно вредные. Кроме того, очень сложно добиться большой производительности. Однако для небольших фирм и малых объемов работы этот метод самый подходящий.
Метод напыления рубленого ровинга. Этот подход куда более технологичен. В нем используется не стекловолокно, а стеклонить, которая подается в измельчитель специального пистолета, где рубится на короткие волокна. Затем пистолет «выплевывает» их вместе с порцией смолы и катализатора. В воздухе все смешивается и наносится на форму. Но после этой процедуры все равно массу необходимо прикатать, чтобы удалить пузырьки. Далее отвердевание происходит как обычно.
Такой способ выглядит очень заманчиво и просто. Казалось бы, стой и поливай из шланга. Но есть один существенный недостаток, из-за которого этот способ не столь популярен, – слишком большой расход смолы. Изделие получается очень тяжелым, и, так как волокна не переплетены друг с другом, механические свойства такого стеклопластика несколько хуже. Кроме того, к вредным парам смол подмешивается взвесь мелких частиц стекла от измельчителя, очень вредных для легких человека.
Метод намотки. Этот специфический метод предназначен для изготовления пустотелых круглых или овальных секционных компонентов, типа труб или резервуаров. Таким образом делаются парусные мачты, удочки, рамы велосипедов, глушители автомобилей и т. д. Стекловолокна пропускаются через ванну со смолой, затем через натяжные валики, служащие для натяжения волокна и удаления излишков смолы. Волокна наматываются на сердечник с необходимым сечением, угол намотки контролируется отношением скорости движения тележки к скорости вращения. Как намотка нитки на шпульку швейной машинки. В результате получаются крепкие и легкие изделия.
Метод препрегов. В данном случае используются не отдельные смола и ткань, а так называемые препреги – предварительно пропитанная смолами стеклоткань. Стекловолокно предварительно пропитывается предкатализированной смолой под высокой температурой и большим давлением. При низких температурах такие заготовки могут храниться недели и даже месяцы. При этом смола в препрегах находится в полутвердом состоянии. При формовании препреги укладываются в матрицу и закрываются вакуумным мешком. После нагрева до 120 -1800°C смола переходит в текучее состояние, и препрег под действием вакуума принимает нужную форму. При дальнейшем повышении температуры смола застывает.
Вся проблема этого метода в необходимости нагревательного оборудования, особенно автоклава. По этой причине изготавливать большие детали очень сложно. Но и плюсы очевидны. Использование вакуума позволяет значительно снизить вероятность появления воздушных пузырьков и существенно сократить долю смолы в готовом изделии.
Существуют и иные технологии – пултрузия, RFI, RTM и др. – практически на все случаи жизни. Выбор той или иной технологии зависит от необходимых объемов, сложности изделия и количества денег.
europolis.ru
Изготовление деталей из стекловолокна и углеволокна в моделизме
Для изготовления крупногабаритных и высоконагруженных частей моделей часто применяются так называемые композиционные материалы, состоящие из «наполнителя» и «связующего». Наполнителем, выполняющим основные силовые функции, обычно является стеклоткань, углеткань ( углеродное волокно) или кевлар (материал из синтетических волокон). В качестве связующего выступают эпоксидные или полиэфирные смолы.
Если для изготовления тонких фюзеляжей радиоуправляемых планеров и многих частей свободнолетающих моделей технология выклейки из композиционных материалов является единственно приемлемой (по соображениям прочности), то в остальных случаях, как правило, есть возможность выбора между композитной и бальзовой конструкцией. Если предстоит разовая работа, то, наверное, стоит отдать предпочтение дереву. Тогда общие трудозатраты и вес модели получаться меньше. В случае же «мелкосерийного производства» лучше овладеть техникой работы с композитом.
Сегодня мы познакомимся с основными приемами выполнения деталей для авиамоделей из композиционных материалов. Сразу отметим, что предлагаемый материал предназначен тем, кто только знакомится с новой для них технологией. Поэтому статья основана на описании упрощенных методик, распространенных среди моделистов «средней руки». При более же профессиональной работе выбор исходных материалов и способы работы с ними настолько специфичны, что в каждом конкретном случае требуют отдельных описаний.
Вначале несколько слов о «сырье». Поскольку тонкостенные детали нередко воспринимают значительные нагрузки, для предотвращения растрескивания связующего в смолы добавляют пластификатор (или при возможности используют специализированные, высокопрочные и не слишком «стеклотвердые») смолы. Чтобы эпоксидку было легче наносить, ее разбавляют растворителем, спиртом или ацетоном. Для тонирования детали можно добавить в смесь типографскую краску или алюминиевую пудру. Неплохие результаты дает и вмешивание в «сырую» смолу художественных масляных красок. Кроме пигментирования, такая краска еще и немного пластифицирует исходную смолу. Стеклоткань, как правило, приходится прокаливать над электрической плиткой или в электродуховке для удаления парафина, которым она пропитывается на заводе.
Прежде всего отметим, что все работы с эпоксидными (да и полиэфирными) смолами нужно проводить в резиновых перчатках в помещении с хорошей вентиляцией. Выклеивание композитных «корок» можно осуществлять как снаружи на болванке, так и внутри, на снятой с нее вогнутой форме (матрице). Болванку можно изготовить из липы, ольхи, плотного пенопласта или бальзы. Ее размеры должны быть меньше размеров детали на толщину будущей «корки». Поверхность следует тщательно зашкурить и загрунтовать.
Затем на матрицу наносится разделительный слой (парафин или полироль для мебели). Стеклоткань нарезается на полосы, которыми можно было бы оклеить болванку без образования складок и «прилачивается» жидкой эпоксидкой. Количество слоев стеклоткани в различных местах детали может варьироваться в зависимости от распределения нагрузок. В случае образования пузырей и вздутий их необходимо сразу же разгладить или прорезать и выдавить из них воздух.
После отверждения смолы «корку» снимают. Если форма матрицы не позволяет этого сделать, деталь разрезают по оси симметрии. При этом, как правило, страдает покрытие болванки, которая будет нуждаться в шпаклевке перед дальнейшим использованием. Недостаток этого способа заключается также в том, что поверхность детали имеет фактуру ткани и требует шпаклевания и вышкуривания.
Для выклеивания деталей по второму способу (матричному) нужно прежде всего изготовить саму «негативную» форму. Обычно она представляет собою толстостенную «скорлупу», выклеенную из стеклоткани.
Если требования к точности детали очень высоки (например, силовые панели обшивки крыла с ламинарным профилем), то матрицу делают в виде массивного «монолита» из гипса, цементного раствора или цемента, смешанного с эпоксидной смолой.
Эталонная модель-болванка должна иметь размеры, совпадающие с внешними обводами детали. Чем лучше будет качество ее поверхности, тем меньше потребуется отделочных работ для каждого изделия в дальнейшем. Обычно методом лакировки с промежуточным полированием стараются довести поверхность до зеркального блеска, чтобы готовые, отформованные в этой матрице детали нуждались только в окраске. В случае же применения тонированной смолы поверхности оказываются полностью готовыми. При изготовлении модели-копии можно воспроизвести имитацию заклепок и расшивки на матрице или еще на эталонной модель-болванке.
Для выклейки матрицы нужно вырезать из толстой фанеры рамку по форме осевого сечения болванки. Надев рамку на болванку, закрепите ее пластилином таким образом, чтобы одна из поверхностей рамки совпадала с плоскостью симметрии болванки. По линии сопряжения выполните из пластилина радиус скругления, равный примерно 2 мм.
Если планируется изготовить монолитную матрицу, на рамку нужно наложить окантовку из досок, имеющих высоту, большую чем половина ширины болванки. На болванку и соответствующие поверхности рамки наносится разделительный слой.
Через несколько часов его нужно натереть до блеска шерстяной тканью. Затем болванка вместе с рамкой оклеиваются стеклотканью. В местах резких прегибов укладывается стекловолокно, пропитанное эпоксидной смолой (его можно получить, разобрав рогожную стеклоткань).
Первый отформованный слой выполняется из стеклоткани толщиной 0,03 мм, затем применяется ткань толщиной 0,2-0,3 мм.
Если же требуется изготовить простую легкую матрицу, а не «монолит», то теперь останется положить лишь несколько усиливающих слоев рогожной стеклоткани. Здесь опять особое внимание нужно обратить на отсутствие пузырей, чтобы дефекты поверхности не передались будущим изделиям.
Для ликвидации пузырей оснастку можно поместить в воздухонепроницаемый мешок (предварительно уложив на нее полиэтиленовую пленку) и откачать из него воздух с помощью вакуумного насоса. Под разряжением форму надо держать до полного отверждения «корки». Если вакуумный мешок не имеет проколов, то для этого достаточно пережать шланг, отключить насос и оставить в таком виде оснастку на 12 часов. В случае изготовления монолитной матрицы всю опалубку заливают гипсовым раствором или эпоксидной смолой с наполнителем (в качестве последнего могут использоваться любые порошкообразные или зернообразные материалы.
После отверждения смолы, болванка с рамкой аккуратно отделяются от полученной формы. Аналогично изготавливается и вторая, симметричная часть матрицы.
При выклеивании корок в полученной матрице применяются те же приемы, что и при ее изготовлении. Первый слой стеклоткани должен иметь толщину 0,02-0,03 мм,
последующие — порядка 0,2 мм. После отверждения смолы «корку» обрезают вровень с краем матрицы, вклеивают шпангоуты (если необходимо) и затем вынимают ее.
Для снижения массы детали часто используют армирование пористым пенопластом, бальзой или слоеные (сендвичевые) конструкции, имеющие дополнительное внутреннее покрытие из тонкой стеклоткани. В этом случае наружное покрытие может быть выполнено из одного слоя стеклоткани толщиной 0,2-0,3 мм. Пенопласт или бальзу нарезают на фрагменты, которым можно было бы придать кривизну пуансона. Пенопласт несложно изогнуть над электроплиткой, а бальзу проще намочить и примотать резиной к болванке до высыхания. Стеклоткань можно пропитывать эпоксидной смолой как в самой форме, так и до размещения в матрице, на какой-либо ровной поверхности (излишки клея снимаются шпателем). Однако пропитанная ткань, особенно тонкая, при укладке имеет тенденцию больше прилипать к перчаткам, чем к пенопласту. Поэтому иногда проще уложить в вакуумный мешок сборку без внутреннего слоя стеклоткани, и «прилачить» его потом. Армирование бальзой имеет то преимущество, что она почти не впитывает в себя связующее.
При склейке между собой тонкостенных корок часто используются промежуточные шпангоуты. В случае же армирования в этом нет необходимости. Эпоксидная смола имеет плохую адгезию к отвержденному стеклопластику. Поэтому соединяемые поверхности нужно зашкуривать крупной наждачной бумагой, а линии стыка оклеивать полосками тонкой стеклоткани. Изнутри на одну из «корок» полезно наклеить отбортовку, которая позволит упростить и увеличить надежность соединения деталей. До момента полного отверждения смолы изделие обматывается скотчем.
При мелкосерийной постройке моделей-копий применяются также различные «гибридные» технологии. Например, внешний слой детали формуется из АВС-пластика и образует внешнюю фактуру поверхности. Далее располагается промежуточный слой тонкого пенопласта. Внутреннее, силовое «покрытие» делается из стеклоткани.
По материалам журнала «Моделизм спорт — хобби»
А. Перфильев
Среди авиамоделистов также популярно изготовление воздушных винтов из композитных материалов применением пресс форм.
clstunt.ru
Стеклопластик технология изготовления
Наверное, именно стеклопластик мы вспоминаем чаще всего, когда речь заходит о тюнинге. Высокая популярность этого материала объясняется просто – легкостью в использовании и обработке. Со стеклопластиком легко научиться обращаться, работу с ним может освоить каждый. При желании, разумеется.
Началом истории стеклопластика считаются 40-е годы прошлого века. Произошло оно от стекловаты, которая была довольно распространена в начале 20 века. Первое применение стеклопластику было найдено в строительстве лодок. Однако, универсальность позволила ему быстро распространиться и в другие сферы, в частности, в автомобилестроение. Чего только не делалось в свое время из стеклопластика, вплоть до специальных бамперных накладок для расчистки снега. Никто не верил, что стеклопластик надежен, однако, время показало обратное. Как выяснилось, при столкновении автомобиля из стеклопластикового волокна и обычного «стандартного» авто железному доставалось гораздо сильнее. Так что прочность и надежность стеклопластика доказана временем и проверена не раз.
Стеклопластик– довольно простой материал, который состоит из стекловолокна,
пропитанного смолой. Различают несколько видов стеклопластика по типу смолы, которая их пропитывает. Тип смолы для пропитки выбирается исходя из многих внешних факторов, которые придется пережить материалу, а также из будущих характеристик того, что из него собираются сделать. Смолы бывают разными. Некоторые способны затвердеть уже при комнатной температуре, а некоторым требуется подогрев. Перед пропиткой стекловолокна смолу перемешивают со специальным катализатором (т.е., отвердителем). Потом берется несколько слоев стекловолокна, которые тщательно пропитываются готовым составом. Благодаря стекловолокну смола не ломается, а получает гибкость и достаточную прочность.
Один из основополагающих моментов в изготовлении стеклопластика для тюнинга своими руками – правильный баланс катализатора и смолы. Небольшое отклонение в технологии изготовления– и дело будет загублено. Например, если с катализатором выйдет перебор, то вы не успеете сделать свою работу – он затвердеет раньше времени. Однако, если катализатора будет слишком мало – то смола не застынет вообще.
На рынке представлено большое количество смол от разных производителей. Казалось бы, смола – простой материал, чем она может различаться? Однако, различия все-таки есть. При выборе смолы очень важно обращать внимание на их свойства. Смолы очень переменчивы в зависимости окружающей среды. Их качества могут улучшаться или ухудшаться в зависимости от температуры воздуха в помещении, проветриваемости помещения и т.д.
Некоторые смолы приходится «подгонять», чтобы они быстрее засыхали. Готовую матрицу с изделием для этого сушат в специальной сушильной камере. Так смола застынет гораздо быстрее. А если уж совсем горит, то при возможности можно использовать автоклав с большой температурой и высоким давлением. Да и прочность конструкции, изготовленной в автоклаве, будет гораздо лучше.
Различаются по своим характеристикам не только сами смолы, но и стекловолокно. Стекловолокно делится на типы в зависимости от толщины и структуры материала. Основные из них – стекломат и стеклоткань. Отличительной чертой стекломата является беспорядочное расположение волокон. У стеклоткани волокна похожи на обыкновенную ткань. Стеклоткань прочнее стекломата, однако, у последнего есть свои преимущества. Стекломат легче «надеть» на матрицу, что значительно облегчает работу с ним.
Есть одна разновидность стекломата, которая отличается особой тонкостью и легкостью – это стекловуаль.Вообще, существует несколько разновидностей стекломата, основным различием между которыми служит толщина и плотность материи. Основным параметром при разделении стекломата на типы является вес одного метра квадратного – 300гр, 45гр, 600гр, 900гр. Самая тонкая стекловуаль имеет вес 32гр на один метр квадратный, что позволяет создавать из нее настоящие тонкие шедевры. Толстый стекломат предназначен для придания изделию прочности и надежности. Для особой прочности изделия из стекломата формируются из нескольких слоев, поэтапно. Согласно технологии изготовления сначала берется несколько листов стекломата и скрепляется, а затем им дают время, чтобы застыть. После этого добираются остальные слои для получения итоговой толщины. Работа в один этап здесь невозможна – большое количество слоев при застывании может принять неправильную форму, стянуться или покоробиться.
Стеклоткань также различается по толщине.Назначение стеклоткани, так же, как и стекломата – прочность и толщина готового изделия. При работе со стеклотканью необходимо учитывать то, что растяжение ее в разные стороны дает различный результат. Поэтому слои стеклоткани обычно накладываются под определенными углами. Стекловолокно обязательно должно быть высококачественным, чтобы пропитывающая его смола хорошо держалась внутри и хорошо впитывалась в саму стеклоткань.
Работа со стеклотканью зачастую подразумевает использование дополнительного материала, предназначенного для того, чтобы итоговая масса готового изделия не была слишком большой. Этот материал – поликор. Состоит он из полиэфирного волокна и содержит в себе микробаллоны. Иногда при работе перемежаются слои стекломата и поликора. Однако, лучшее решение – это армирующие полоски из поликора, делающиеся как вставки в основную ткань конструкции. Такие полоски придадут изделию дополнительную прочность. Еще одним важным фактором в технологии изготовления стеклопластика для тюнинга своими руками является прочность конструкции. Улучшить прочность конструкции поможет небольшое количество смолы между слоями стекломата. Если смола полностью пропитала стекломат и не запузырилась, конечно. Меньшее количество смолы сделает итоговый продукт более легким.
Есть распространенное высказывание о том, что автомобили, кузов которых изготовлен из стекловолокна, невозможно поцарапать. На самом деле, такое высказывание неверно по сути. Стекловолокно царапается, но при этом, не теряется цвет. Весь секрет состоит в технологии создания самого изделия. Зачастую для изготовления своими руками высококачественных изделий из стекловолокна в них как основа закладывается слой гелькоата (то есть, специального покрытия из гелия). Этот слой позволяет не прибегать к покраске готового изделия в дальнейшем. Существует гелькоат различных цветов. Нужный оттенок ему придается при помощи специальных колеров. Слой гелькоата предназначен не только для создания цвета, но и для продления жизни самому материалу. Он является хорошей защитой от любых внешних воздействий. В случае применения гелькоата стекловолокно кладется поверх него.
При работе со слоем гелькоата необходима предельная точность – слой должен быть абсолютно ровным, без утоньшений. Утоньшение может привести к сморщиванию гелькоата и к некачественному внешнему виду готового изделия. Лучше решение для того, чтобы распределить гелькоат ровно – это применение краскопульта. Использование красокпульта позволяет делать более качественную работу, чем использование кисти. Правда, для того, чтобы работать с краскопультом, нужно выбрать более жидкий гелькоат, чем для работы с кистью. В любом случае, от выбора материала зависит многое.
Приступая к работе по изготовлению стеклопластика для тюнинга своими руками нужно позаботиться о двух вещах– его макете и матрице. Без макета, правда, иногда можно обойтись, но особо качественной работы не получится. Частенько вместо макета используются распорки, на которые кладется стеклоткань. Но это не лучшее решение. Если вам нужен хороший результат, то без макета просто не обойтись. Многие умельцы умудряются, правда, изготавливать некоторые стеклопластиковые детали для тюнинга своими руками прямо на авто. Дверные панели, например. Для облегчения себе работы и для скорости ее выполнения панель прилаживается непосредственно на двери автомобиля. Но в данном случае качественная поверхность не так важна, так как стеклопластик будет являться всего лишь основой для дальнейшей работы. Далее панели будут обклеены пористым материалом, кожей и т.д., и все «косяки» будут скрыты. Однако, для того, чтобы сделать деталь кузова, все же нужен макет, а также матрица.
Макеты можно делать из разных материалов – фанеры, пластилина, пенопласта и т.д. Правильный макет – залог дальнейшей успешной работы. Неправильный – сами понимаете. Причем, если вам нужна красивая и ровная поверхность, то работу над этим нужно начать уже на стадии макетирования. Потрудитесь, чтобы макет был ровным и гладким, таким, какой должна быть в идеале ваша деталь. Таким образом, вы избавите себя от дальнейших мучений и внесения поправок.
Перед тем, как приступать к изготовлению макета для тюнинга, нужно сориентироваться – будет деталь делаться целиком или по частям. Основываться здесь нужно на том, насколько возможно будет после изготовления стеклопластиковой детали вытащить ее из матрицы без повреждений. Этот момент очень важен в технологии изготовления. Некоторые детали могут оказаться слишком большими или иметь слишком причудливую форму, так что вытащить их без проблем не получится. В таком случае лучше будет составить эту деталь из нескольких, более мелких, а потом соединить их своими руками.
После того, как работа над макетом завершена, можно приступать к созданию матрицы– основы для будущей детали. И к этому надо отнестись со всей серьезностью. Согласно технологии изготовления необходимо покрыть всю поверхность макета небольшим слоем воска и хорошенько отполировать его. Затем можно наносить матричный гелькоат на поверхность макета. Матричный гелькоат имеет более густую консистенцию, наносится более тонким слоем и ложится легче, чем обыкновенный. Основа из матричного гелькоата позволит добиться идеальной ровности поверхности матрицы.
Затем можно приступать непосредственно к работе со стекловолокном.Технология изготовления стеклопластика для тюнинга своими руками такова: первым слоем обычно укладывается стекловуаль. С ее помощью вы без труда обведете все контуры макета, добиваясь предельной точности. Слой стекловуали должен высохнуть. После этого берется слекломат более толстых размеров и кладется сверху в несколько слоев. Помните о том, что не нужно укладывать сразу все слои (как уже говорилось выше, матрица от этого может испортиться). Лучше вделать работу в несколько этапов, пока не будет достигнута оптимальная толщина материала.
Если вам необходимо сделать разъемную матрицу, то нужно будет соорудить своими руками специальные перегородки, которые разделят макет на несколько сегментов. Сначала кладется основной сегмент, ему нужно будет некоторое время, чтобы застыть. Потом перегородки нужно вытащить. Основной сегмент обрабатывается по краям, затем начинается работа по выкладыванию остальных сегментов. Чтобы правильно расположить при последующей работе все сегменты относительно друг друга, нужно в основном сегменты сделать специальные ямочки. При укладке последующих сегментов, в ямочки будет заливаться смола и стекловолокно, что позволит образоваться выпуклостям. Эти выпуклости послужат для дальнейшего прикрепления деталей матрицы друг к другу. Кроме того, в ребре каждого сегмента матрицы необходимо будет заготовить отверстия для крепежных болтов. После того, как матрица сделана, нужно позаботиться об ее прочности. Для этого служат ребра жесткости, закрепляющиеся на ней. Изготовить ребра жесткости можно из металла (если требуется особо прочная конструкция), из фанеры или дерева. При правильном выполнении технологии и хорошем макете матрица будет готова к дальнейшей работе. Однако, очень часто ее нужно еще раз обработать, чтобы придать идеальный вид. Поверхность матрицы необходимо выровнять при помощи шлифовки.
После того, как поверхность матрицы стала гладкой, придется заняться ее вощением – то есть, тщательной полировкой при помощи воска. Делается это в несколько слоев с небольшими перерывами. Воск наносится тонким слоем на всю поверхность, затем растирается так, чтобы осталась лишь незримая пленочка.
Есть, правда, и другой вариант, который может заменить натирание воском, а может использоваться вместе с ним. Это использование специальных жидкостей, при помощи которых появляется покрытие в виде пленки. Такие жидкости предназначены также для того, чтобы смола или гелькоат не проникли на саму матрицу. В процессе работы с матрицей нужно следить за тем, чтоб поверхность ее не поцарапалась. Это может привести к тому, что смола прирастет к матрице, и вы не сможете продолжать работу. По сути, все придется начинать снова – шлифовать, востить и т.д. Есть такие вещества, которыми можно обработать матрицу и использовать ее потом несколько раз. Но лучше все же выбрать воск – это проверенный и надежный способ.
Помимо создания матрицы, есть и другие варианты работы со стеклопластиком. Правда, до сих пор изготовление матрицы остается самым популярным способом. Однако, новейшие технологии позволяют применять в работе компьютерное моделирование, а также станки с ЧУ, при помощи которых создается матрица или макет любого размера и из любого материала. Однако, у вас вряд ли есть такое оборудование, поэтому если вы делаете тюнинг своими руками, то матрица – единственный вариант.
После того, как матрица закончена, начинается процесс изготовления изделия. Советуем все же сделать первый слой из гелькоата, так как он поможет изделию в итоге принять эффектный внешний облик. Еще один плюс такого слоя – возможность обойтись без покраски в дальнейшем. Слой гелькоата надежно отделяет матрицу от стекловолокна, которое может ее повредить.
Сама работа со стекловолокномпроизводится разными методами. Такие методы, кстати, годятся и для работы с другими подобными материалами, как то: карбон, кевлар и т.д.
Способ первый. Формовка вручную.Данный способ является наиболее распространенным, так как позволяет сэкономить на производстве и добиться максимальной точности. Ручная работа всегда ценится гораздо выше. Полотно стекловолокна пропитывается эпоксидной смолой, для чего используется либо кисть, либо валик. Напомним, что нужно выбирать такой валик (кисть), который выдержит работу со смолой. Можно дать стекловолокну пропитаться, а затем укладывать его в матрицу, а можно вделать это сразу после нанесения смолы. Чтобы смола лучше прошла сквозь волокна, необходимо пройтись по волокну разбивочным валиком. После этого нужно взяться за укаточный валик для окончательной обработки волокна. С помощью него вы сможете выдавить оставшиеся пузырьки из волокна, а также сделать слой смолы более равномерным. Избавление от пузырьков должно производиться своевременно, пока изделие не успело застыть. Пузырьки воздуха – серьезный брак, который может повредить готовую конструкцию. Работать с таким волокном далее не представляется возможным – вся работа пойдет насмарку.
Если вы хотите облегчить себе труд, то можно использовать некоторые простые приспособления, которые помогут в работе. Например, смеситель, который будет автоматически смешивать смолу с катализатором, и наносить ее на валик. Правда, от ручной укатки все равно никуда не деться.
Ручной метод прост и эффективен, но итог его всегда зависит от способностей и квалификации того, кто изготавливал изделие. Здесь важным преимуществом является опыт. К тому же, непосредственный контакт с эпоксидной смолой и другими материалами может нанести вред здоровью, если работать с ними постоянно. Однако, для небольшой компании ручная формовка – лучшее решение.
Способ второй.Напыление рубленного роввинга.В этом способе уже применяются технологические приспособления, автоматизирующие процесс. Работа таким способом ведется не с самим стекловолокном, а со стеклонитями. Стеклонить попадает в измельчитель пистолета, который разрубает ее на небольшие волокна. В пистолет уже заложена смола и катализатор, поэтому внутри все смешивается с рубленными нитями, а затем смесь выходит наружу. Готовая смесь подается из пистолета непосредственно на форму. Однако, и тут без рук не обойтись – прокатка такой ткани обязательна.
При всей кажущейся простоте и выгодности, этот способ имеет свои минусы. Надо сказать, что им пользуются довольно редко, так как при работе тратится большое количество смолы. Как итог – большой вес готового изделия. К тому же, готовое изделие состоит из разрозненных волокон, и, соответственно, является куда менее крепким, чем цельное волокно. Да и сама смесь, выходящая из пистолета, очень вредна для здоровья.
Способ третий – намотка.Этим способом пользуются в тех случаях, когда готовое изделие должно быть круглой или овальной формы (например, при изготовлении различных труб и резервуаров). Способ намотки широко применяется в изготовлении парусных мачт, удочек, велосипедных рам, автомобильных глушителей и т.д.
Стекловолокно попадает в ванну со смолой, затем смесь проходит через натяжные валики, которые вытягивают полотно и выдавливают лишнюю смолу. После чего волокна ткани подаются на сердечник, который их наматывает. Скорость и угол намотки волокна можно регулировать при помощи изменения движения тележки. Процесс очень напоминает то, как в швейной машинке нить наматывается на шпульку. Итог работы третьим способом – высококачественное и прочное изделие.
Способ четвертый. Метод препрегов.Препрегами называют заготовки, состоящие из кусков стеклоткани, которые уже пропитались смолой. Предварительно необходимо провести пропитку стеклоткани предкатализированной смолой. Пропитка должна осуществляться при большой температуре и высоком давлении. Смола достигает полутвердого состояния, и это заготовки способны храниться достаточно долго. Затем препреги кладутся на матрицу, и вся конструкция помещается в вакуумный мешок. Ее необходимо нагреть до 180 градусов, чтобы смола стала мягкой. В условиях вакуума препрега ляжет по необходимой форме. Затем изделие снова нагревают для застывания смолы.
При работе этим способом не обойтись без автоклава. Поэтому такой способ хорошо для изготовления небольших по размерам частей. Однако, большое преимущество этого способа – в вакууме воздушные пузырьки не образуются, а также значительно снижается расход смолы.
Также можно использовать и другие способы, как то: пультрузия, RFI, RTM и т.д. Выбирать способ изготовления нужно на основе того, какое необходимо получить в итоге изделие.
Теперь можно подвести итоги.Работа со стеклопластиком дает большое преимущество в весе. Чтобы сделать конструкцию прочной, зачастую приходится делать ее достаточно толстой, что прибавляет веса. Стеклопластик этим не страдает. Его большое преимущество перед, например, алюминием или сталью – способность принимать исходную форму после воздействия удара. Если, конечно, деталь не разрушилась. Ремонтировать части из стеклопластика гораздо проще. Трещину достаточно заклеить смолой, а затем наложить небольшой кусок из стеклоткани или стекломата. Если деталь подверглась более значительным повреждениям, то ее можно снять и положить на матрицу, чтобы она вновь приняла исходные очертания. Хотя, в таких случаях лучше, все же, изготовить новую деталь. Части из стеклопластика можно «подлатать» и шпаклевкой, шкуркой и водой.
Правда, стеклопластик – материал далеко не из дешевых. К тому же, работать с ним вредно для здоровья, он выделяет токсические вещества. Поэтому нужно быть предельно осторожным. Работа по тюнингу автомобиля из стеклопластика требует обязательного наличия респиратора, который защитит от вредных испарений эпоксидной смолы.
kamaz-stekloplastik.ru
ООО «СТП» — Изделия из стеклопластика
- Главная
- О компании
- Стеклопластиковая продукция
- Изделия из стеклопластика
Изделия из стеклопластика
Для нас не редкость когда клиент, обратившись в нашу компанию с определенной задачей, получает неординарное, на его взгляд, решение, которое позволит ему сэкономить и улучшить качество необходимого ему продукта.
В зависимости от сочетания различных пропорций и материалов возможно получение изделий из стеклопластика разных по своим свойствам, таких как физикомеханические, термостойкость, устойчивость к агрессивным средам (кислоты, щелочи и т.п.), водопоглощение, устойчивость к ультрафиолету, другим атмосферным явлениям и другие.
Также существует множество технологий производства продукции из стеклопластика, основные из них, получившие широкую популярность у производителей, это контактное (ручное) формование, намотка, RTM, SMC и BMC технология.
Каждая из данных технологий имеет разновидности, подвиды и специалисты нашего предприятия выбирают наиболее подходящую технологию для производства необходимого продукта в зависимости от поставленной перед ними задачей и возможностями предприятия при этом стараясь найти золотую середину в пропорциях «цена – качество».
Технологии изготовления изделий из стеклопластика
Существует несколько основных способов изготовления изделий из стеклопластика:
-
Контактное (ручное) формование
-
Напыление
-
Намотка
-
SMC и BMC
-
RTM
-
Инфузия
-
Пултрузия
Контактное формование
Способ изготовления изделий методом контактного (ручного) формования является самым распространенным благодаря низкой стоимости подготовки производства (единственный способ не требующий дорогостоящего оборудования).
Данный способ, в основном применяется для производства штучной и мало серийной продукции.
Процесс изготовления изделий из стеклопластика методом контактного формования происходит в несколько этапов:
-
Нанесение на матрицу (форму) разделительного слоя для избежания прилипания изделия к матрице.
-
Нанесение лицевого (наружного) слоя. Может осуществляться как напылением так и в ручную, кистью. Данный слой имеет высокую стойкость к ультрафиолету, агрессивным, химическим средам и имеет широкую палитру цветов.
-
Формовка стеклопластика (осуществляется при помощи валиков или кистей).
-
Обрезка изделия.
Напыление
Для производства изделий методом напыления требуется специальное оборудование (машина для напыления стекловолокна).
Данный способ изготовления изделий из стеклопластика хорошо применим в серийном, мало серийном производстве изделий и при изготовлении крупно габаритных изделий.
В отличии от метода контактного (ручного) формования, метод напыления не требует подготовки заготовок и смесей, а нанесение материалов на форму происходит при помощи специального оборудования подающего готовую смесь в необходимых пропорциях (пропорции смеси могут регулироваться).
Благодаря выше сказанному, метод напыления значительно эффективней и менее трудоемкий в сравнении с методом контактного (ручного) формования.
SMC и BMC (припреги)
Припрег — это термореактивный (перерабатывается под воздействием температуры 100-170ºС)материал, созданный на основе полиэфирных и венилэфирных смол, состоящий из смолы, наполнителей, низкопрофильных добавок и армирующих волокон.
Для производства продукции из припрегов потребуется гидравлическое, прессовое оборудование (некоторая линейка материалов BMC позволяет использование литьевого оборудования аналогичного ТПА (ТермоПластАвтоматам) и позволяет изготавливать продукцию инжекционным способом), печь для подогрева заготовкииметаллические формы снабженные системой подогрева (жидкостной или электрической) позволяющей равномерно разогревать форму до необходимой температуры.
Процесс производства продукции:
Предварительно подготовленная заготовка подогревается в печи. После подогрева укладывается в разогретую форму и с помощью прессового оборудования (под определенным давлением) происходит смыкание формы и формирование изделия. После полного смыкания, форма некоторое время остается в замкнутом состоянии до полного отвердевания материала под воздействием температуры.
Намотка
Процесс изготовления изделий методом намотки основан на формировании изделия неприрывной нитью стекловолокна, которая в процессе укладки пропитывается связующим.
Изготовление изделий из стеклопластика методом намотки, в основном применяется в массовом (серийном) производстве изделий имеющих округлые, цилиндрические, прямоугольные формы не имеющие сложной структуры.
Для производства изделий методом намотки требуется намоточное оборудование, оправки формирующие структуру изделий и позволяющие легкое снятие изделия.
Производство изделий методом намотки происходит следующим образом: на установленную в станок, вращающуюся оправку, под определенным углом, непрерывно наматывается нить(ти) из стеклоткани. Нить(ти) предварительно пропитываются связующим.
Существует два метода намотки: периодическая и непрерывная.
Каждый из методов разделяется на два способа намотки: перекрестный и прямой.
Оба метода имеют положительные и отрицательные моменты:
-
Периодическая намотка, в сравнении с непрерывной, требует меньше вложений в оборудование и занимает меньшую площадь, но при этом имеет низкую производительность и ограничения по длине изделий.
-
Непрерывная намотка, в сравнении с периодической, требует больших затрат на оборудование и занимает большую площадь производства, но имеет высокую производительность.
stekloplastik.biz
Стекловолокно + эпоксидка. Изготовление лицевых панелей любой формы из стеклопластика
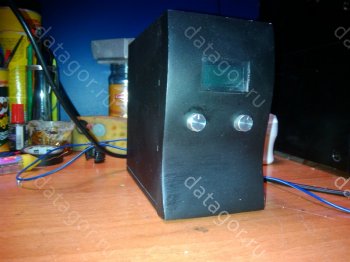
Приветствую жителей и гостей Датагории. Хочу поделиться своим опытом изготовления лицевых панелей из стеклопластика, в данном случае для лабораторного блока питания. Любой панели, для начала, требуется предмет-форма. Так как будущий блок будет из корпуса ATX, скручиваем форму из тех же блоков при помощи саморезов по металлу по размеру будущей панели, а внутри обклеиваем малярным скотчем. Для того чтобы форма не рассыпалась, когда будем доставать, закладываем стекловолоконную шкурку (используется для затирки шпаклёвки у маляров).
Думаю не все читатели данной статьи «заядлые» строители, так что опишу подробно. Для формы можно использовать любую гипсовую штукатурку. Не рекомендую чистый гипс или алебастр, т.к. он очень быстро застывает.
Раствор замешиваем в пропорции одна часть воды плюс три части гипсовой смеси до однородной массы. Аккуратно выкладываем в форму шпателем и разглаживаем до получения нужного вида будущей панели и даём высохнуть примерно сутки. Получается такая конструкция.

Когда всё застыло, достаём из формы нашу заготовку, на неровности и сколы не обращаем внимания. Обклеиваем малярным скотчем и получаем что-то вроде этого:

Четыре отверстия по краям, как на фото, не пригодятся, их пропускаем.
Далее — сам процесс. Берём вот такой ремкомплект: стекловолокно, эпоксидка и затвердитель, что продаётся почти в любом авто-магазине.

Не забываем о технике безопасности: работаем в перчатках, помещение должно хорошо проветриваться (вонь ужасная), готовая смесь смолы с затвердителем нагревается.
Вырезаем заранее стекловолокно чуть больше по размеру, чем наша предмет-форма.

Размешиваем эпоксидку и затвердитель 1:10. Советую замешивать понемногу, быстро сохнет. Итак, раствор замешан. Наливаем на форму и размазываем по всей площади, стараясь не залить края.
Я использовал узкий резиновый шпатель для затирания швов кафельной плитки. Укладываем последовательно все три слоя стекловолокна, аккуратно прижимаем тем же шпателем к форме, сухие места проливаем и разглаживаем. Одного замеса должно хватить.

Дожидаемся полной полимеризации эпоксидки, вставляем вверх ногами в ту форму, в которой мы и приготовили нашу предмет-форму и подрезаем «заподлицо» выглядывающее стекловолокно.
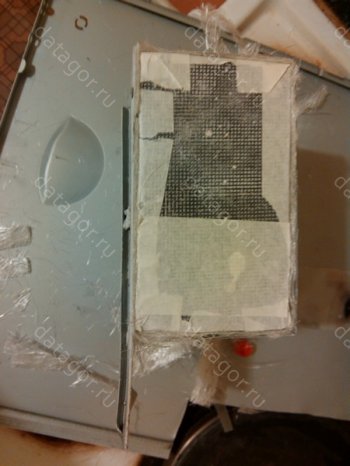
Снова замешиваем эпоксидку и в прямом смысле слова проливаем края, ждём до полного высыхания, сутки не меньше. Получается вот такая заготовка:
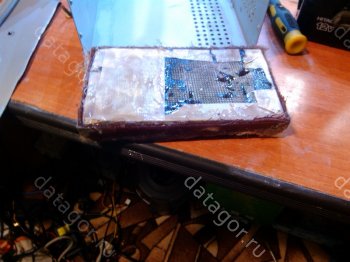
Следующий шаг — грубая обработка. Я использовал «болгаргу» с точильным кругом.

Теперь нужно вытащить вандальским (по-другому не получилось) методом предмет-форму.
Приступаем к выравниванию. Шпаклёвку я использовал универсальную, т.е. по пластмассе и металлу. Замешивается она также как и эпоксидный клей, 1:10.
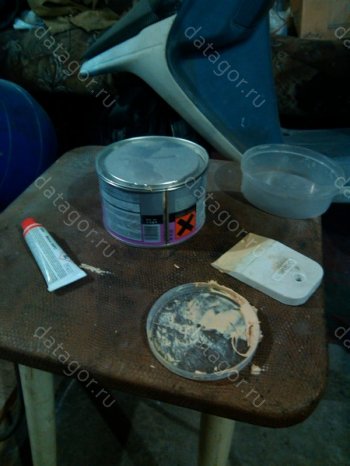
Шпаклюется всё в несколько слоёв, каждому надо давать высохнуть. Перед каждым последующим слоем шкурим, но без фанатизма.
Пришло время окна под дисплей. Вырезаем аккуратно и вставляем оргстекло, по размеру чуть больше, чем используемый дисплей. Шпаклюем.
С нетерпением дожидаемся высыхания шпаклёвки, берём мелкую шкурку (зернистость 500-1000) и доводим нашу панель, насколько это возможно, до идеала.
Для ускорения процесса я использовал шлифовальную насадку на «болгарку».

Получилось, по-моему, не плохо.
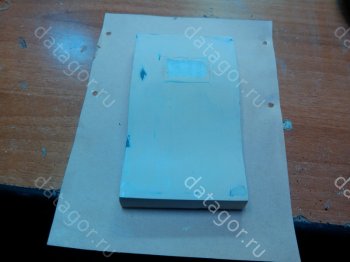
Покраска производится в 5-7 слоёв, иначе будут потёки. Красил обычным баллончиком. Не забываем окно дисплея залепить малярным скотчем.


Крепления панели к корпусу блока, без всяких ухищрений прилепил той же эпоксидкой, получилось надёжно.
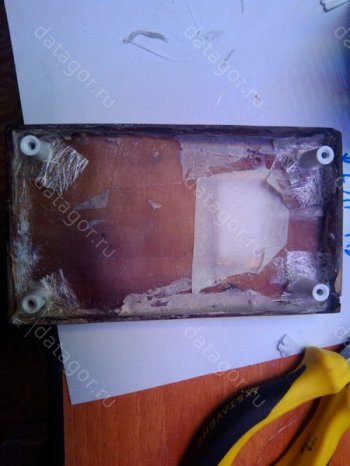
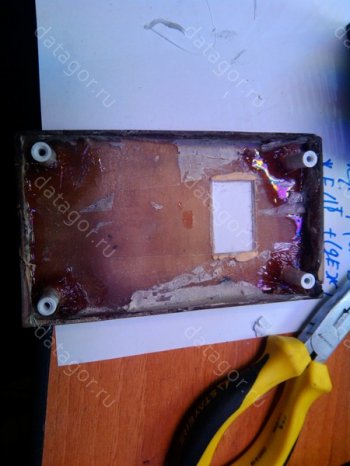
Схему блока питания разбирать не буду. Кому интересно, вот тут подробно «Переделка компьютерного блока питания под зарядное устройство в подробностях»
Крепим все узлы.
И вот что получаем в итоге.

Благодарю за внимание!
Камрад, смотри полезняхи!

Антон (dedtocha)
Анадырь
О себе автор ничего не сообщил.
datagor.ru
Стеклопластик своими руками

Стеклопластик получил широкую известность и популярность как в быту, так и во многих отраслях народного хозяйства. Из этого материала производят и самые простые детали, как например пуговицы и подиума акустической системы, и сложнейшие изделия, например обшивку самолетов. Изделия из стеклопластика можно встретить в автопроизводстве, яхтостроительстве, изготовлении легких самолетов и вертолетов и других сферах промышленного производства.
Из чего состоит стеклопластик?
В состав этого универсального материала входит полиэфирная или эпоксидная смола, которой придают нужную форму особым способом и армируют стеклотканью или стекловолокном. Полиэфирную смолу также можно армировать тканью из углеродных волокон, стекловолокном, кевларовой тканью, стекловатой, стеклотканью, с помощью которых изделие приобретает особую прочность. За неимением этих материалов для армирования можно использовать любую синтетическую ткань: искусственный шелк, нейлон и т.д., но изделия не будут иметь такой прочности, как при использовании стекловолокна или стеклоткани.
Что такое стеклоткань?
Стеклоткань представляет собой плотный материал, состоящий из хаотично расположенных или упорядоченно расположенных нитей, связанных между собой тонким слоем эпоксидной смолы.
Стеклоткань имеет толщину до 12 мм, но обычно ее измеряют в граммах на квадратный метр. Самые распространенные значения: 300, 450, 600, 900 грамм на 1 кв.м.
Стеклоткань отличается по типу, способу изготовления, массе и природе стекловолокна. Самой распространенной является “тафта”, которая имеет клеточную текстуру.
Стекловойлок имеет меньшую сопротивялемость механическим нагрузкам, чем стеклоткань, но, несмотря на это, его удобнее использовать для изготовления сложных форм.
Для серийного производства применяют другой тип волокна: это резаное волокно, имеющее такую же или чуть меньшую длину, как у стекловойлока. Его используют при изготовлении основы.
Особенности и советы по изготовлению формы для изделия из стеклопластика

Детали из стеклопластика своими руками изготовляются методом формовки. Для этого нужна специальная форма, которая бывает охватывающей или охватываемой. Форма должна иметь определенный уклон для удобства вынимания из нее готового изделия. Чем качественнее и ровнее отполирована поверхность стенок формы, тем будет выше качество поверхности формируемого изделия.
Для выполнения формовки изделия нужно произвести ряд подготовительных работ:
- Внутренняя поверхность формы покрывается специальным веществом, способствующим свободному извлечению из нее готовой детали. Сам метод формовки заключается в том, что деталь из стекловолокна укладывается в специальную форму и пропитывается эпоксидной или полиэфирной смолой.
- Для армирования изготавливаемых деталей выбирается определенная стеклоткань в зависимости от ее внешнего вида и способности к сопротивлению действующим нагрузкам.
- Из плотной бумаги изготовляется шаблон, по которому делают разметку и вырезают стеклоткань.
- Полиэфирную смолу выбирают соответственного качества, в зависимости от назначения и эксплуатации детали. Смола содержит в своем составе красители и может отличаться химическим составом. Например, если смола предназначена для нанесения первого слоя, она называется ледяным покрытием.
Формовку деталей можно формировать по-разному, главное, чтобы при этом соблюдались следующие правила:
- стеклоткань в форме должна располагаться равномерно;
- стеклоткань полностью пропитывается полиэфирной смолой, исключая малейшие пузырьки воздуха в пропитке;
- обеспечивается высокая производительность готовой детали для серийного производства.
Рассмотрим для примера технологию производства контактного формования или формования на одной форме. Это самый легкий способ, при котором количество используемого материала уменьшается, но при этом увеличивается потребность в количестве рабочей силы.
Чем аккуратнее и опытнее исполнитель, тем больше готовых деталей получится из исходного материала. Такой способ может применяться для одной и для нескольких одинаковых деталей или небольшой серии. Форма может быть любого размера и, как уже говорилось выше, она бывает охватываемой или охватывающей, зависимо от желаемого результата, при котором больше ценится хороший внешний вид наружной или внутренней поверхности готовой детали.
Форма должна иметь высокие показатели прочности. Ее уклон должен быть не менее 35%. Если формовочная деталь имеет обратный уклон, тогда форма должна быть выполнена из нескольких идеально подогнанных друг к другу частей.
Из какого материала изготовляется форма?
Выбор материала для формы зависит от предназначения производства. Например, форма из гипса применяется для изготовления всего одной детали; стальная форма может использоваться большое количество раз для изготовления нескольких тысяч деталей; а для изготовления деталей мелкими сериями лучше всего изготовить модель, с которой снимается слепок формы. Она будет состоять из слоистого пластика, в состав которого входит стекловолокно и полиэфирная смола. Для укрепления формы профилированный картон или деревянные пластинки погружают в слоистый пластик для образования нервюр. Благодаря этому, в усиленной форме можно изготовить не одну сотню деталей.
Подготовка полотна
Особое внимание нужно обратить на подготовку полотна. Вырезанные полотна нужно поместить во влажное помещение в таком порядке, чтобы их удобно было брать по очереди нанесения слоев. Также необходимо правильно выбрать среди большого количества всевозможных веществ, предназначенных для разделения изделия и формы, именно такое, которое будет соответствовать материалу формы.
Формовка детали
Когда разделительное покрытие нанесено и высушено, можно наносить первый закрывающий слой специальной смолы (иногда с наполнителем), предназначенный для скрытия волокон стеклоткани, которые в результате нанесения смолы стают невидимыми на поверхности детали. Толщина закрывающего слоя не должна превышать 0.4 мм. На слишком толстом слое после высыхания могут возникнуть трещины. Закрывающий слой можно и не накладывать, если наличие видимых волокон стекловолокна не имеет значения. В этом случае сразу наносится толстый слой эпоксидной смолы.
На вертикальных стенках деталей могут возникнуть подтеки. Чтобы этого избежать, в смолу подмешивают специальный наполнитель. Первый нанесенный слой подсушивают до студнеобразного состояния. Если он немного прилипает к пальцам, значит можно накладывать следующий слой.
Смола приготавливается двумя этапами: сразу в часть смолы добавляют ускоритель полимеризации, а потом смешивают с остальной смолой, которая будет использоваться. По необходимости в нее добавляют краситель.
Следующим этапом изготовления стеклопластика своими руками является дозирование и смешивание катализатора, если это необходимо, то есть, рассчитывается количество смолы, которая будет использована в ближайшие 15 минут. Смолу разливают в две одинаковые емкости. В одну емкость добавляют ускоритель, а в другую – катализатор.
Для удобства смесь можно готовить в третьей емкости небольшими равными порциями. Благодаря такому способу, можно избежать повторяющихся неоднократно приготовлений смолы и катализатора небольшими порциями. Чтобы сделать правильную дозировку смолы, ее можно взвесить на весах или использовать дозировочную емкость необходимого объема. Дозировка ускорителя и катализатора определяется с помощью мензурок очень маленькими порциями.
Когда покрывающий слой или первый слой смоляного покрытия станет студенистым, можно приступать к наложению первого слоя стекловолокна. Для этого используют легкий стекловойлок с показателем 300 г/1 кв.м. При наложении каждого слоя стекловолокна необходимо следить за тем, чтобы слой ложился ровно и постепенно, заполнял пустоты и закругления. Иногда при наложении слоев стекловолокна возникают воздушные карманы. Это происходит либо из-за слишком быстрого прижатия, либо из-за неплотного сопряжения острого угла. После укладки стекловолокно пропитывается слоем смолы, который наносится кисточкой или валиком.
Важно помнить, что каждая порция смолы рассчитывается примерно на 15 минут работы. Работая кистью, смолу нужно наносить не мазками, а как при торцевании, похлопывая концом кисти по обрабатываемой поверхности. Когда пропитка эпоксидной смолой будет завершена, нельзя сразу пытаться отделить стекловолокно, так как отдельные волокна при этом могут приподняться и вырваться. После слоя смолы, не дожидаясь его высыхания, накладывают следующий слой стеклоткани.
Чтобы обеспечить высокую механическую прочность, слой стекловолокна и стеклоткани укладывается поочередно. Последним слоем укладывают стекловойлок или специальную отделочную стеклоткань (300 г на 1 кв.м).
Выполняя такую укладку, нужно соблюдать ряд важных правил:
- металлические или полиэтиленовые емкости для накладываемых веществ должны быть чистые;
- смола в емкости должна быть полностью использована перед тем, как емкость будет заполнена новой порцией;
- возникшие воздушные пузыри, неподдающиеся устранению, убираются надрезанием их лезвием бритвы;
- кисти и валики после использования моются с помощью ацетона или трихлорэтилена. Это нужно сделать сразу, так как впоследствии произойдет полная полимеризация смолы, оставшейся на инструментах, и ее уже нельзя будет удалить;
- всю работу необходимо производить в резиновых перчатках, для защиты рук от прямого контакта со смолой;
- рабочее помещение должно иметь хорошую вентиляцию, чтобы вредные пары полистирола не вызвали раздражение слизистых оболочек и глаз;
- ни в коем случае во время работы нельзя тереть глаза, так как стеклянные волокна, случайно попавшие на кожу, могут нечаянно травмировать глаза;
- в рабочем помещении должна быть температура не ниже 20 градусов, оно должно быть защищено от холода, сырости и прямых солнечных лучей;
- во время работы нельзя курить во избежание пожара, так как смолы являются легко воспламеняемыми;
- выемка изделия производится не раньше, чем через 12 часов. Сушильная камера (не выше 60 градусов) или нагрев инфракрасными лучами может сократить этот период времени;
- края изделия после выемки обрезаются и заглаживаются;
- если изделие необходимо покрасить, то прежде этого его нужно зачистить шлифовальной шкуркой, а затем уже нанести полиуретановую краску;
- если детали нужно склеить между собой, то для этого склеиваемую поверхность делают шероховатой, промывают ацетоном, а затем склеивают специальным клеем или пропитанной полиэфирной смолой тесьмой.
Чтобы улучшить качество формовки используют метод давления. Работа выполняется точно так же, как мы уже рассмотрели, но по окончанию изделие в форме придавливают, создавая разрежение между гибкой мембраной и покрытием на форме, либо раздувая эластичный пузырь, помещенный в закрытую форму.
Такие детали будут иметь самое высокое качество, так как при придавливании обеспечивается равномерное распределение смолы. Такой метод применяется для среднесерийного производства.
Чтобы готовое изделие имело высокое качество и приятный внешний вид, формовка во входящих друг в друга формах производится или с очень слабым сжатием, или вообще без него.
Для среднесерийного производства формовка под давлением для входящих друг в друга форм может также производиться с помощью укладки слоя стекловолокна, а сверху него определенного количества смолы. С помощью сжатия обеспечивается равномерное растекание смолы по детали.
Чтобы этот способ можно было применить в крупносерийном производстве, или при производстве основы будущей детали, формы намеренно подогревают. В результате подогрева стеклянные волокна прижимаются к поверхности формы, которая сделана из перфорированного листа. В этом состоянии их пропитывают смолой с помощью краскопульта. После этого форму с нанесенной основой несколько минут подсушивают в камере для сушки. Подсушенный полуфабрикат вынимают из временной формы и помещают в конечную форму, покрывают слоем смолы и сжимают в течение непродолжительного времени. В результате получается готовая деталь.
prostostroy.com
Стеклопластиковый кузов автомобиля | Так делают
С помощью стеклоткани или стекломатов можно создать любую и даже очень сложную форму кузова автомобиля. Кузова из композитных материалов не ржавеют, легко обрабатываются и ремонтируются, обладают исключительной прочностью, способны гасить колебания и просты в изготовлении. Пропитывая стекломат или стеклоткань эпоксидной, полиэфирной или фенолформальдегидной смолой получают стеклопластик. При пропитке стекломатов или стеклоткани фенолформальдегидной смолой получается деталь с высокой температурной устойчивостью и механической прочностью. К тому же у стеклопластиков на этой основе самая низкая стоимость исходного материала. Большую прочность имеют стеклопластики на основе эпоксидных смол, но стоимость их выше.
Изготовление мастер модели.
Прежде чем начать создавать мастер модель, оцените имеющийся подручный материал: ДСП, пластилин, пенопласт, глину, алебастр, гипс. Если есть поблизости глина и песок, можно начинать с них, но наилучшим материалом является скульптурный пластилин. Любые твёрдые поверхности, как застывший гипс или алебастр Вы будете часами шлифовать и спиливать, а пластилин нужно всего лишь поскоблить шпателем или скребком.
Перед началом работ необходимо выровнять площадку. Настил должен быть выровнен по уровню и чем точнее, тем вернее получится мастер модель. На настил устанавливают раму с колесами, а к ним крепится каркас будущего кузова. Каркас изготавливается из любых подручных материалов- фанера, ДСП, пенопласт, монтажная пена. Не забываем уменьшить размер каркаса и оставить место для нанесения пластилина.
Для того чтобы не перекосить кузов в двух взаимно перпендикулярных плоскостях, изготовьте два шаблона. Один с чертёжными размерами вида сверху, другой вида спереди (сзади). Для более точного выравнивания каркаса по высоте используйте гидроуровень.
Далее обмазываем каркас пластилином и формируем будущий кузов автомобиля. Перед Вами широкое поле деятельности: пластилин позволяет срезать слои и образовывать любую поверхность. Заготовьте шаблоны на все криволинейные сечения поверхностей, капот, крыша, двери, облицовка радиатора и т. д. Кроме того, хорошо иметь ровную рейку длиной 3,5…4 м с сечением 20х30 мм. Эта рейка позволит проводить на поверхностях мастер модели лекальные кривые и проверить плавность построенных поверхностей.
Если Вы используете стёкла от серийного автомобиля, а не делаете их на заказ, то установите стёкла на мастер модель. Стекло смачивают водой и устанавливают на мастер модели по предварительно сделанной разметке, которая переносится с чертежа будущего автомобиля на мастер модель.
Так же следует поступить и с серийными приборами освещения, ручками дверей и т.д. по списку, если Вы не собираетесь их изготавливать самостоятельно или делать на заказ. Это позволит избежать многих ошибок проектирования и убережет будущий кузов от многочасовых подгонок нестыкующихся деталей.
Закончив изготовление мастер модели, выверив все ее поверхности и линии, приступают к подготовке ее для изготовления кузова или матрицы. Сделав качественную мастер модель, лучше сделать матрицу, а по ней выклеивать кузов (один, два и более). Стеклопластик позволяет получить качественную поверхности кузова без последующего шлифования.
Прежде чем изготавливать матрицу, необходимо хорошо подготовить поверхность, так как любой выступ и любая впадина точно отобразятся на внутренней поверхности матрицы, а затем и на внешней поверхности кузова. Выровнять поверхности на мастер модели проще, чем на кузове автомобиля, да и лучше эту работу выполнить один раз, а не для каждого экземпляра кузова.
Если Вы изготовили мастер модель из пластилина, то нужно нанести разделительный слой и приступать к выклейке матрицы. Если же мастер модель изготовлена из глины, гипса или алебастра, то необходимо покрасить мастер модель, зачистить и отполировать. После этого необходимо нанести разделительный антиадгезионный слой, для облегчения снятия готовой матрицы. Для получения такого слоя применяют целлофановые, полиэтиленовые, полиамидные и другие полимерные пленки, а также пленкообразующие растворы или полировальные пасты и мастики, которые после высыхания образуют на поверхности тончайшую пленку антиадгезионного слоя.
Вот несколько рецептов самодельных составов для разделительного слоя:
- 2 части воска и 1 часть скипидара. Воск растапливают на водяной бане, затем снимают с огня и вливают скипидар. Проверьте качество состава, если высохший слой можно отполировать, то состав подходящий, в противном случае добавьте скипидар.
- 30% парафина, 30% бензина и 40% мыльной воды
Изготовление матрицы.
Мастер модель готова, приступаем к изготовлению матрицы.
Нам понадобится следующий инструмент:
- Ножницы для раскроя ткани или матов;
- Шпатели различной ширины;
- Кисти с жесткой щетиной;
- Резиновый ролик для прикатки;
- Банки и противни для смолы.
Смолу приготавливают небольшими порциями, так как время до начала отверждения и потери клеящих свойств 40-60 мин. Поэтому Обычно берут 1-2 кг смолы. Смолу готовят согласно инструкции, но предварительно нужно проверить состав на небольшом куске стекломата или стеклоткани, так как клеящие свойства зависят не только от состава и качества смолы, но и от способа соединения слоёв, перемешивания, температуры, влажности окружающей среды и других причин.
Сначала на готовую поверхность наносят, так называемый, декоративный слой (смолы 50% и алюминиевой пудры 50%) толщиной 1 мм и дают ему загустеть до такого состояния, чтобы следы смолы не оставались на пальце («до отлипа»). После этого наносят тонкий слой жидкой смолы и накладывают стеклоткань. Ее прокатывают роликом и обрабатывают жесткой кистью, следя за тем, чтобы не образовывались воздушные пузыри.
Если все же они возникают, то, прорезав пузырь ножницами, «прибивают» его кистью, смоченной смолой.
К первому слою сразу же прикладывают второй спой ткани и «прибивают» его, как и первый. Ни в коем случае нельзя проводить кистью по ткани, так как кисть может потащить за собой ткань и испортить работу.
Если матрица изготавливается из элементов: крылья, двери, капот, крыша, то матрицу нужно сделать разъёмной. Для начала размечаем линии разъёма матрицы, в дальнейшем они станут швами на кузове автомобиля, далее монтируем опалубку разъёма. Делается она из металла, картона или фанеры. В пластилиновую мастер модель опалубка просто втыкается по намеченным линиям, а с твёрдой мастер моделью из глины, гипса или алебастра поступают иначе.
Наклеивают 2-3 слоя стеклоткани на всю мастер модель. Затем, как и на пластилиновой мастер модели, намечают линии разъема матрицы. Разметку следует проводить после полной полимеризации смолы. Затем подготавливают полосы, шириной 80- 100 мм. из металла, фанеры или картона. Один край будущей опалубки вырезают так, чтобы он повторял контуры плоскости, так как его нужно будет ввести в разрез, сделанный для разъема. На полосы наносится, упомянутый выше, разделительный слой. Ножовкой или «болгаркой» разрезают уложенные слои, вводят в зазоры полосы опалубки и дальше проводят выклейку по выше указанной технологии . При раскрое стеклоткани учитывается припуск на плоскости разъема.
Затем, уложив пять-шесть слоев на предыдущие, укрепляют плоскости разъема деревянными брусками. Для этого брусок и отбортованные плоскости стеклоткани попарно смазывают смолой и затем их скрепляют гвоздями, после полной полимеризации смолы борта сверлят и скрепляют болтами и гайками М6 или М8.
Для предотвращения «игры» поверхностей, опалубку укрепляют брусками или накладывают ребра жесткости в виде жгутов стеклоткани, пропитанной смолой. После полимеризации смолы матрицу с мастер модели снимают.
Если разделительный слой был уложен равномерно и без пропусков, элементы матрицы будут сниматься без значительного усилия, нужно только ввести острый предмет в места разъема — отделить кромки стеклоткани от стальных полосок и руками потянуть на себя снимаемый элемент матрицы.
Оголив всю мастер модель проводят контрольную сборку матрицы, затем разбирают ее на элементы.
Выклейка кузова.
Элементы матрицы кузова очищают от разделительного слоя, оставшегося на внутренней поверхности. Затем внутреннюю поверхность шпатлюют и полируют.
Если на внутренней поверхности имеются большие раковины, то шпатлевку лучше производить эпоксидной смолой с наполнителем. Выступы снимают грубым напильником (стеклопластики хорошо обрабатываются), а затем поверхность шлифуют.
Внимательно осмотрев поверхность и убедившись, что на ней нет изъянов, наносят разделительный слой, при этом стараются сделать его как можно тоньше. Разделительный слой обязательно надо отполировать, так как какая поверхность получится на внутренней стороне матрицы, такой же будет и внешняя сторона готовой детали.
На разделительный слой наносят декоративный слой смолы, выдерживают его. Затем наносят жидкий слой, укладывают и прикатывают стекломат или стеклоткань так, чтобы не образовывалось пузырей; первый слой — лицевой слой. Обработав кистью со смолой первый слой, прикатывают второй, за ним — третий и т. д.
Рекомендовать количество слоев трудно, так как толщина композита зависит от толщины стеклоткани. Для того чтобы определить требуемую толщину, лучше всего провести эксперимент на небольших размеров образце. Однако менее 3 мм слой не делают! При использовании кевлара толщина слоя может быть 0,5…1,5 мм.
Уложив последний слой стеклоткани, тщательно прикатывают его резиновым валиком или пропитывают смолой с помощью кисти. После полной полимеризации смолы деталь вынимают из матрицы.
Следует учесть, что избыток смолы приведёт к деформации детали. Опытные мастера советуют наносить новый слой только после полимеризации предыдущего и его зачистки наждачной бумагой.
Если нет времени ждать полимеризации каждого слоя, попробуйте воспользоваться технологией, используемой на промышленном производстве. Деталь, вместе с матрицей помещают в мешок из тонкой мембраны и откачивают воздух. Мембрана плотно обжимает каждый изгиб детали и выдавливает излишки смолы. В таком виде деталь оставляют до полной полимеризации смолы.
Окраска.
Стеклопластик хорошо окрашивается как синтетической, масляной красками, так и нитрокраской. Для этого нужно только обезжирить наружную поверхность, зачистить ее наждачной бумагой, положить один слой грунта, а по нему производить окраску.
Можно предложить и другой метод. В эпоксидную смолу надо добавить 2-3% анилинового красителя. Прежде чем приступить к выклейке панелей с такой смолой, надо выполнить в порядке эксперимента операции окраски на отдельном куске стеклоткани и смолы, так как краска может изменить свой цвет при внесении ее в смолу.
Для первого декоративного слоя следует применять состав: 100 массовых частей смолы ПН-1, 6 частей инициатора и 8 частей ускорителя. Этот слой не только создает блестящую поверхность. но и защищает стекпонаполнитель от воздействия влаги и химикатов.
Окрашенный кузов шлифуют водостойкой мелкозернистой шлифовальной бумагой, полируют пастой или жидкостью для обработки кузова автомобилей.
Кузов из стеклопластика, изготовленный по каркасу автомобиля.
Некоторые конструкторы пришли к выводу, что для изготовления одного образца делать матрицу нецелесообразно.
Существует метод выклейки панелей кузова непосредственно по мастер модели без изготовления матрицы. Было замечено, что стеклоткань, пропитанная смолой и хорошо прикатанная к поверхности мастер модели, повторяет ее рисунок с учетом всех линий кузова. Если при этом последний (наружный) слой сделать декоративным, то фактически готова форма кузова автомобиля, и при соответствующей шпатлевке имеется возможность из этой заготовки изготовить кузов а
takdelayut.ru