REMSA, отзывы и подробная информация о производителе
Испанская фирма REMSA была создана в 1975 году. Ее специализация – производство барабанных и дисковых тормозных колодок. Основное производство располагается в испанском городе Корелла, а завод, который специализируется на выпуске барабанных колодок, находится в Мадриде. На сегодняшний день испанская компания входит в крупный концерн LUCAS-TRW, поэтому многие запчасти торговой марки LUCAS также производятся на заводах REMSA .
Тормозные колодки REMSA для дисковых и барабанных тормозных механизмов. Продукция фирмы отличается высокой надежностью и качеством изготовления. Производит колодки для автомобилей всего мира. Обеспечивают уверенное и надежное торможение в самых тяжелых условиях. Колодки не создают шума при торможении благодаря противошумным накладкам. Препятствуют чрезмерному износу тормозного диска или барабана и благодаря накладкам из безасбестового фрикционного материала имеют большой ресурс работы. Колодки показали себя надежным спутником автомобиля и незаменимым гарантом безопасности.
Тормозные колодки REMSA выгодно отличает от аналогичных запасных частей других производителей сбалансированное сочетание качества и цены. Если говорить о стоимости изделий испанской фирмы, то ее продукцию можно смело назвать бюджетной. Благодаря такой ценовой политике, доля присутствия REMSA на рынке постоянно увеличивается, а запчасти этой торговой марки доступны далеко за пределами Европы, например, в Америке.
Каталог реализован на всем известной программе TecDoc. Подбор осуществляется или по марке, моделе, двигателю, или по кроссу номеров других производителей, включая оригинальному.
Следует обратить внимание на то, что в номерах REMSA могут быть разночтения. Раньше фирме хватало пяти цифр в номере, но, скорее всего, из-за расширения ассортимента понадобилась шестая цифра. Поэтому, вам может попасться в прайсах номер 649 02, а новый номер 0649 02. В номере может присутствовать точка, и это тоже правильно и не должно смущать. Она то появляется в артикуле, то исчезает.
Кстати, к вопросу о том, почему номер разделен точкой. Первые четыре цифры определяют размеры колодки, так скажем в плоскости, а вторая половина артикула после точки указывает на наличие или отсутствие датчика, толщину и т.п. В большинстве случаев колодки с одинаковым началом взаимозаменяемы. Более тонкую можно установить вместо толстой, датчик можно откусить и выбросить.
Информация о производителе REMSA
REMSAАВТОЗАПЧАСТИ ДЛЯ ИНОМАРОК REMSA
КиберМаркет по продаже ЗАПЧАСТЕЙ ДЛЯ ИНОМАРОК VIN-CODE.ORG предлагает КОЛОДКИ, ТОРМОЗНЫЕ ДИСКИ, БАРАБАНЫ компании REMSA
Основанная в 1975 году, компания REMSA входит в концерн TRW. Компания REMSA сегодня является одним из лидеров по производству тормозных колодок в мире. Компания представляет на рынке самый широкий выбор дисковых и барабанных тормозных колодок, которые доступны по цене при очень высоком качестве. За своё 30-летние существование REMSA имеет 8 производственных компаний по всему миру (6 в Европе и 2 в Северной Америке). Филиалы и представительства компании расположены в Испании (Madrid, Pamplona, Corella, Olvega, Eufrisa), Мексике (Monterrey), Англии, Америке (Chicago). Компания имеет привилегированные позиции на мировом рынке, особенно в Европе, где является ведущим поставщиком на aftermarket и в Северной Америке, где за последние годы отмечается значительный рост.
Производя более, чем 70 млн. изделий в год REMSA, как один из лидеров по производству фрикционных материалов в мире, предлагает не только самые последние «ноу-хау» в этой области, но и самый большой ассортимент. Ассортиментный ряд компании, а это более 1600 позиций, включает все марки автомобилей, сделанные в Европе, Америке, Японии, Корее и Австралии. Помимо дисковых колодок, REMSA предлагает барабанные колодки. Вся продукция, включая материалы, из которых она изготовлена, полностью производятся на заводах компании.
Рейтинг любой компании, кроме известных составляющих — технического совершенства и высокого качества продукции, зависит также и от способности компании влиять на технический прогресс в своем «секторе». Поэтому
Благодаря новому производственному процессу на фабриках REMSA под кодовым названием HPT (Обработка Высокого давления), все колодки REMSA обжигают электрической горячей стальной пластиной при температуре 650С под давлением пресса силой 10.000 N. Таким образом, процесс обжига, гарантирует, что вся поверхность колодки запрессована равномерно:
- HPT означает чрезвычайно высокую температуру и давление, чтобы обжечь поверхности колодок на 1 — 2 мм глубиной, что позволит увеличить тормозные способности колодок;
- HPT означает безопасность, потому что избегает процесса кристаллизации, типичного для материалов трения, теряющих тормозные характеристики при полезном использовании продукта.
В последнее время возросли запросы клиентов, и все больше внимания уделяется степени износа колодок. Проводятся многочисленные лабораторные испытания и дорожные тесты, нацеленные на получение нового фрикционного материала с длительным сроком службы и минимальной склонностью к износу. Технология PROTECNO сводит к минимуму износ фрикционного материала, т.к. в основе разработки лежит высокое качество сырья, благодаря которому повышается чувствительность тормозной системы во всем диапазоне скоростей и замедление износа колодок при работе во всем диапазоне температур.
DISCOVERY IV (LA) | 3.0 4×4 30HD0D 340 л.с. бензин | 2009 — наст |
DISCOVERY IV (LA) | 3.0 SDV6 4×4 30DDTX 256 л.с. Дизель | 2009 — наст |
DISCOVERY IV (LA) | 3.0 TD 4×4 306DT 211 л.с. Дизель | 2009 — наст |
DISCOVERY IV (LA) | 3.0 TD 4×4 306DT 245 л.с. Дизель | 2009 — наст |
DISCOVERY IV (LA) | 3.0 TD 4×4 30DDTX 211 л.с. Дизель | 2009 — наст |
DISCOVERY IV (LA) | 5.0 V8 4×4 508PN 375 л.с. бензин | 2009 — наст |
DISCOVERY IV (LA) | V8 HSE 508PN 375 л.с. бензин | 2009 — наст |
LR4 IV (LA) | 3.0 4×4 30HD0D 340 л.с. бензин | 2009 — наст |
LR4 IV (LA) | 3.0 SDV6 4×4 30DDTX 256 л.с. Дизель | 2009 — наст |
LR4 IV (LA) | 3.0 TD 4×4 306DT 211 л.с. Дизель | 2009 — наст |
LR4 IV (LA) | 3.0 TD 4×4 306DT 245 л.с. Дизель | 2009 — наст |
LR4 IV (LA) | 3.0 TD 4×4 30DDTX 211 л.с. Дизель | 2009 — наст |
LR4 IV (LA) | 5.0 V8 4×4 508PN 375 л.с. бензин | 2009 — наст |
LR4 IV (LA) | V8 HSE 508PN 375 л.с. бензин | 2009 — наст |
RANGE ROVER SPORT (LS) | 3.0 TD 4×4 30DDTX 245 л.с. Дизель | 2005 — 2013 |
RANGE ROVER SPORT (LS) | 2005 — 2013 | |
RANGE ROVER SPORT (LS) | 3.0 TD V6 4×4 30DDTX 211 л.с. Дизель | 2005 — 2013 |
RANGE ROVER SPORT (LS) | 3.6 TD 8 4×4 368DT 272 л.с. Дизель | 2005 — 2013 |
RANGE ROVER SPORT (LS) | 5.0 V8 4×4 508PN 375 л.с. бензин | 2005 — 2013 |
RANGE ROVER SPORT (LS) | 5.0 V8 4×4 508PS 510 л.с. бензин | 2005 — 2013 |
RANGE ROVER SPORT (LS) | V8 HN HSE 508PN 375 л.с. бензин | 2005 — 2013 |
RANGE ROVER SPORT (LS) | V8 SC HSE 508PS 510 л.с. бензин | 2005 — 2013 |
RANGE ROVER SPORT (LW) | 3.0 4×4 30HD0D 340 л.с. бензин | 2013 — наст |
RANGE ROVER SPORT (LW) | 3.0 TD 4×4 30DDTX 211 л.с. Дизель | 2013 — наст |
RANGE ROVER SPORT (LW) | 3.0 TD 4×4 30DDTX 249 л.с. Дизель | 2013 — наст |
RANGE ROVER SPORT (LW) | 3.0 TD 4×4 30DDTX 258 л.с. Дизель | 2013 — наст |
Бренды и производители автозапчастей — REMSA
REMSA
Испания
Компания REMSA была основана в 1975 году в Испании и первоначально была ориентирована на удовлетворение потребностей внутреннего испанского рынка. С момента основания компания занималась выпуском тормозных колодок. Спустя некоторое время компания вошла в состав концерна TRW. Это позволило обрести новые рынки сбыта и превратиться в одного из мировых лидеров в области производства тормозных колодок. Сегодня компания REMSA имеет в своем составе 8 производственных компаний, расположенных во всем мире: 6 находится в Европе и 2 в Северной Америке. Плюс к этому компания имеет развитую дистрибьюторскую сеть: филиалы и представительства компании расположены в Испании Мексике, Англии, США. В Европе компания считается ведущим поставщиком продукции на рынок aftermarket, предлагая высокое качество при сравнительно низкой цене. В настоящий момент компания REMSA производит около 70 млн. единиц изделий в год. В ассортименте присутствует более 1600 позиций. Вся продукция поставляется для легковых автомобилей европейского, японского и американского производства и полностью соответствует требованиям автопроизводителей. Ассортимент тормозных колодок REMSA включает ко всему прочему и оборудование их оригинальными аксессуарами. Основное направление деятельности компании остается прежним — производство фрикционныъх материалов, дисковых тормозных колодок и барабанных тормозных колодок. Качество обусловлено использованием в производстве последних научных достижений в области фрикционных материалов и собственных ноу-хау. REMSA вкладывает большие инвестиции в конструкторские разработки и конечное тестирование продукции. Тормозные колодки работают в жестких условиях под влиянием перепадов температур, влажности, влиянии агрессивных средств, пыли и грязи. Это предъявляет к фрикционным материалам повышенные требования. Поэтому конструкторы REMSA постоянно работают над усовершенствованием своей продукции. Новая разработка PROTECNO обеспечивает самый высокий уровень КПД тормозных сил. Коэффициент трения всегда остается стабильным при любых изменениях температур, что и является гарантией надежности, безопасности и качества тормозных колодок REMSA. Технология PROTECNO, применяемая в изделиях компании, сводит износ фрикционного материала к минимуму, так как в основе лежит высокое качество сырья. Чувствительность тормозной системы во всем диапазоне скоростей повышается, а износ колодок при работе во всем диапазоне температур снижается. Конструкторы компании особое внимание уделили предотвращению появления посторонних шумов во время эксплуатации колодок (скрипа и т.д.), вибрации, визга тормозов. При использовании тормозных колодок REMSA тормозной путь сокращается на 7,4 %. При производстве тормозных колодок REMSA используется специальный процесс обжига, что ускоряет притирание поверхности колодки к тормозному диску. Стоит сказать, что компания перешла на безасбестовое производство фрикционных материалов. При всех высоких качественных характеристиках тормозных колодок компании REMSA, надежности и долговечности, продукция REMSA отличается невысокой ценой, что является ее дополнительным конкурентным преимуществом. Вся продукция соответствует положениям жесткого стандарта Е-90, который предъявляется к фрикционным материалам, принятым сейчас в ЕЭС.
Ссылка на сайт производителяКаталог Remsa online
Remsa — одна из самых популярных марок вторичного рынка тормозных колодок. Фирма производит не только тормозные дисковые колодки, барабанные колодки, но и диски. Однако тормозные диски продаются не слишком активно.
Барабанные накладки можно приобрести в комплекте с новыми пружинами и болтами. Номер имеет написание xxxx.xx. В продаже ещё можно встретить завалявшиеся детали с тремя цифрами в первой части или с пробелом между группами цифр вместо точки. Цвет упаковки также менялся. Серый сменился на красно-черный.
Первые четыре цифры номера отвечают за форму колодок. Пара после точки — толщина, задняя поверхность, другие незначительные различия. Если не получается найти нужный артикул, обычно можно заменить его другим, если первая часть номера совпадает.
Перейти в каталог Ремса онлайн
Официальный TecDoc
На онлайн-каталог Ремса ведет ссылка с официального сайта производителя remsa.com (пункт меню — catalogues)
Подбор колодок Ремса не очень удобен в использовании, потому что немного долго грузится, а бывает не загружается вовсе, останавливаясь на 5%, 15%. После того, как он запустится, проблем не бывает. Для смены языка и установки установки русского в правом верхнем углу есть есть кнопка Configuracion. Открываем форму, меняем Espaniol на Ruso, подтверждаем выбор (Guardar), и ищем каталожные номера.
Каталог реализован на всем известной программе TecDoc. Подбор осуществляется или по марке, моделе, двигателю, или по кроссу номеров других производителей, включая оригинальному.
Следует обратить внимание на то, что в номерах Ремса могут быть разночтения. Раньше фирме хватало пяти цифр в номере, но, скорее всего, из-за расширения ассортимента понадобилась шестая цифра. Поэтому, вам может попасться в прайсах номер 649 02, а новый номер 0649 02. В номере может присутствовать точка, и это тоже правильно и не должно смущать. Она то появляется в артикуле, то исчезает.
Кстати, к вопросу о том, почему номер разделен точкой. Первые четыре цифры определяют размеры колодки, так скажем в плоскости, а вторая половина артикула после точки указывает на наличие или отсутствие датчика, толщину и т.п. В большинстве случаев колодки с одинаковым началом взаимозаменяемы. Более тонкую можно установить вместо толстой, датчик можно откусить и выбросить.
Более известная торговая марка Lucas, теперь TRW, заказывает часть своей продукции в Испании, на заводе Remsa.
REMSA — тормозные колодки и диски — автозапчасти
REMSA
Испания
Он-лайн каталог: webshop-cs.tecdoc.net/remsa/home.jsp
REMSA — история компании :
Remsa (РЕМСА) — компания основана в 1975 году в Испании. В настоящее время входит в концерн TRW.
Remsa сегодня является одним из лидеров по производству тормозных колодок в мире.
Компания представляет на рынке самый широкий выбор дисковых и барабанных тормозных колодок, обладающих прекрасным соотношением цены и качества.
Компании Remsa принадлежат 8 производственных компаний по всему миру (6 в Европе и 2 в Северной Америке). Филиалы и представительства компании расположены в Испании, Мексике, Великобритании, США.
Компания имеет привилегированные позиции на мировом рынке, особенно в Европе, где является ведущим поставщиком на вторичном рынки, и в Северной Америке, где за последние годы отмечается значительный рост.
Производя более 70 миллионов изделий в год Remsa, как один из лидеров по производству фрикционных материалов в мире, предлагает не только самые последние «ноу-хау» в этой области, но и самый большой ассортимент.
Ассортиментный ряд компании, а это более 1600 позиций, включает все марки автомобилей, сделанные в Европе, Америке, Японии, Корее и Австралии.
Помимо дисковых колодок, Remsa предлагает барабанные колодки. Вся продукция, включая материалы, из которых она изготовлена, полностью производятся на заводах компании.
Remsa расходует много средств на конструкторские разработки, прикладную науку и проведение сравнительных тестов. И это дает значительные результаты и преимущества перед конкурентами.
Новая разработка PROTECNO — результат множества различных тестов и испытаний — обеспечивает самый высокий уровень КПД тормозных сил.
Благодаря этой новой разработке, коэффициент трения остается стабильным по всем диапазоне температур (от 100 до 500 °С), что гарантирует высокий уровень безопасности и комфорта.
Программа по увеличению комфорта нацелена на сокращение различных неблагоприятных моментов: вибрация, визг и скрип тормозов.
Тормозной путь уменьшился на 7,4 %. А используемый в производстве тормозных колодок Remsa процесс обжига ускорят притирание поверхности колодки к тормозному диску.
Обжиг — процесс, суть которого заключается в воздействии высоких температур (650 °С) на поверхность колодок. В результате чего сухой газ, возникший в процессе производства и оставшийся во фрикционном материале, испаряется.
В последнее время возросли запросы клиентов, и все больше внимания уделяется степени износа колодок. Проводятся многочисленные лабораторные испытания и дорожные тесты, нацеленные на получение нового фрикционного материала с длительным сроком службы и минимальной склонностью к износу.
Технология PROTECNO сводит к минимальному износу фрикционного материала, т.к. в основе разработки лежит высокое качество сырья, благодаря которому повышается чувствительность тормозной системы во всем диапазоне скоростей и замедление износа колодок при работе во всем диапазоне температур.
ДеКАРС предлагает следующую продукцию REMSA: |
![]() |
— тормозные диски
— комплекты тормозных колодок
— ремкомплекты для тормозных колодок
— главные и рабочие тормозные цилиндры
— главные и рабочие цилиндры сцепления
— тормозные суппорты
— тросы ручного тормоза и сцепления
— тормозные шланги |
|
Если при поиске нужной детали у Вас возникли проблемы, она отсутствует в предложенном ассортименте или Вы не уверены в правильности выбора, используйте «VIN-запрос».
Мы обязательно подберем необходимые Вам запчасти!
Также Вы можете воспользоваться формой «ЭКСПРЕСС-ЗАПРОС» на главной странице нашего интернет-магазина и указать Ваши предпочтения.
Другие производители деталей тормозных систем:
Производство Brembo, часть 2: изучаем завод суппортов
В прошлый раз мы побывали на фабрике, которая занимается производством тормозных дисков Brembo. Теперь пришло время отправиться в городок Курно в предместье Бергамо. Здесь находится не только штаб-квартира известного на весь мир производителя тормозов, но и его завод по выпуску суппортов. Смотрим своими глазами на процесс производства.
Напомним, что компания Brembo является предприятием полного цикла, начиная от металлургического производства и заканчивая упаковкой продукции для афтермаркета. У него вообще нет внешних поставщиков: в Brembo абсолютно все делают и контролируют сами. Собственно, это одна из главных причин высочайшего уровня качества и мирового признания компании.
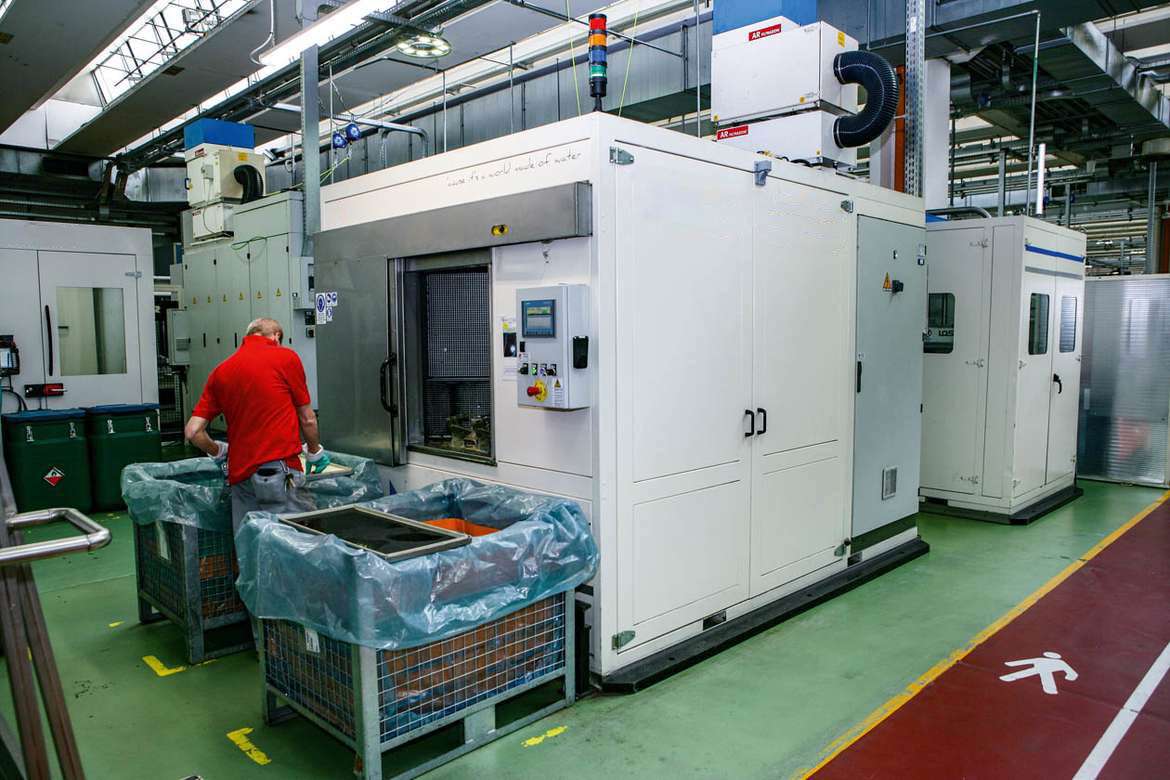
Что касается суппортов, то с точки зрения технологии производства корпуса они делятся на два вида: составные и моноблочные.. Композитный двусоставной суппорт обрабатывается на одном станке и затем собирается в единое целое при помощи болтов. Для моноблочного суппорта нужно уже два станка: на одном обрабатываются наружные части, на другом — внутренние. Основная проблема в том, чтобы качественно обработать места, куда будут установлены поршни. Специально для этого был разработан робот, который может выполнить подобную работу.
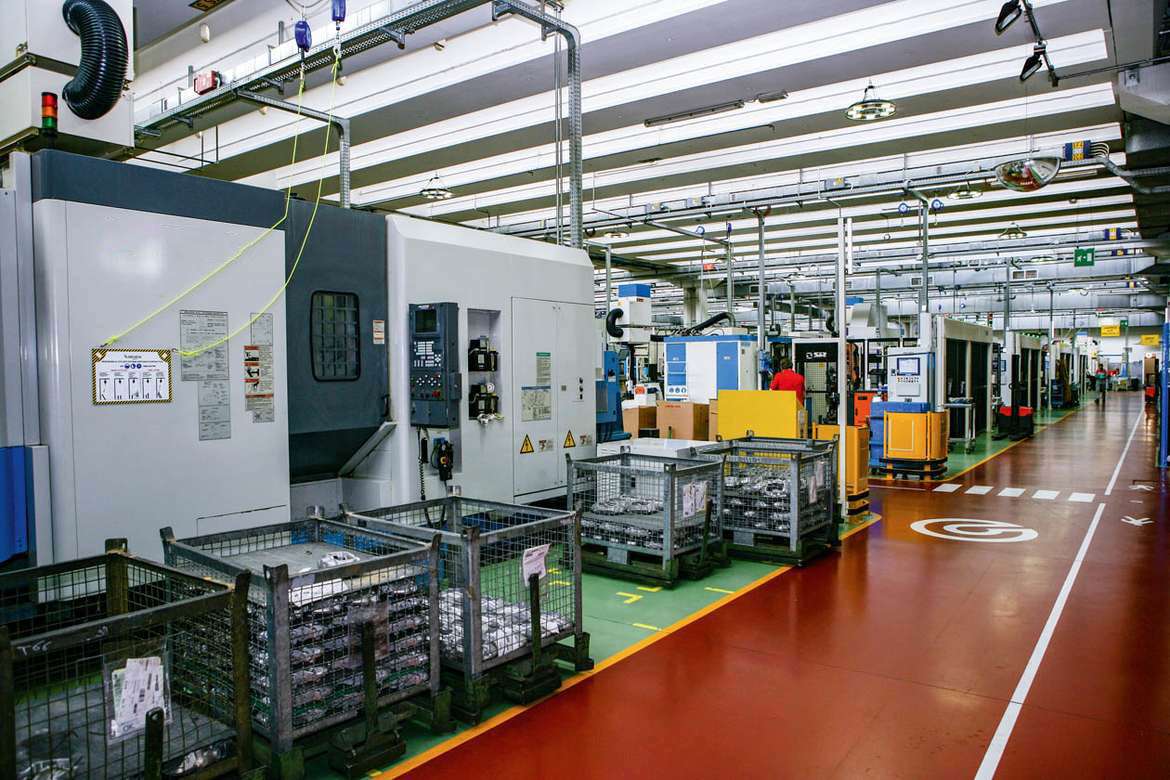
Кстати, вся линия по обработке суппортов полностью автоматизирована, то есть работает вообще без оператора. В начале линии располагается робот, который замеряет все размеры заготовки суппорта в трехмерном измерении. Это нужно для того, чтобы внести корректировки в дальнейшую обработку конкретной заготовки. Раньше этим занимался оператор, теперь же он только загружает заготовки на линию, а далее все автоматически делает машина.В ближайшее время даже процесс загрузки предполагается автоматизировать. Робот будет контролировать уровень загрузки линии и заполнять ее при необходимости.
Производство суппортов работает 24 часа в сутки в три смены. Начинают в 6:00 в понедельник и заканчивают в 18:00 в субботу. Воскресенье — выходной
После обработки заготовок сразу идет зона контроля, где помимо автоматической сверки на линии осуществляется и выборочный контроль качества сотрудником компании. Затем все заготовки суппортов моются под высоким давлением и помещают на специальную раму, чтобы отправить на анодирование.
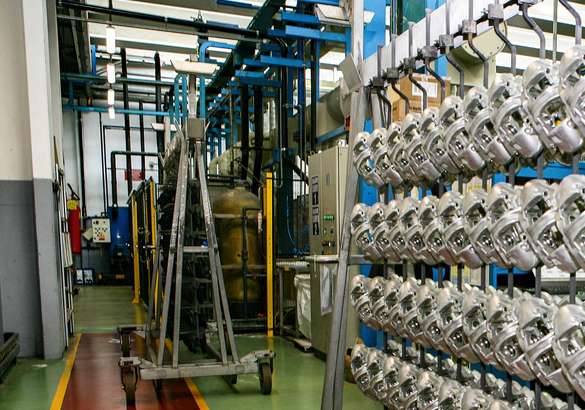
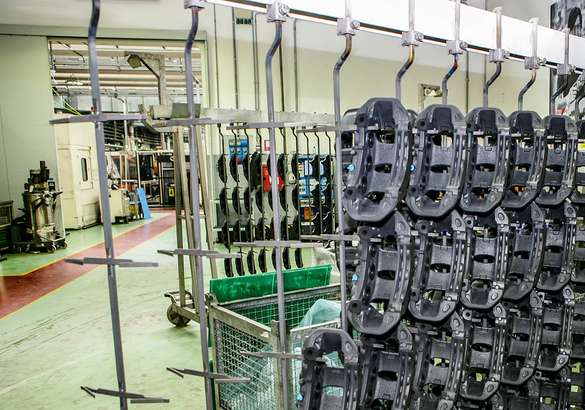
Анодирование — это процесс получения оксидной пленки, которая выполняет защитные функции, в частности оберегает изделие от коррозии и внешних воздействий (соли, реагентов, гидравлических жидкостей), а также придает конечному продукту эстетический вид.
Интересно, что окрашивание в базовые цвета в ходе анодирования сопровождается фирменным процессом фиксации краски, благодаря которому цвет суппорта сохраняется весь срок его службы. Как именно это делается, компания Brembo хранит в секрете.
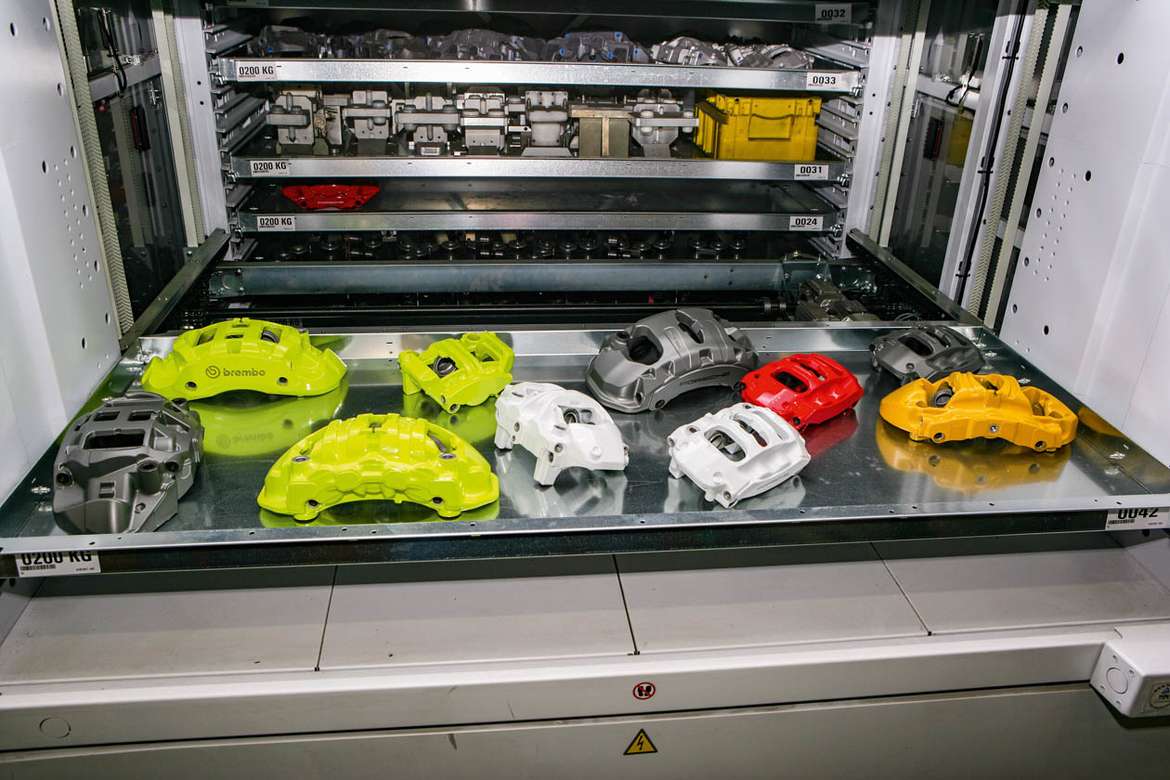
Базовая окраска — 80% суппортов красится в черный цвет, в серый и тёмно-серый — 19%, 1% — голубой цвет для одного заказчика — Maserati.
Линия порошкового окрашивания
На предприятии находится отдельная специальная линия порошкового окрашивания суппортов. Здесь окрашивают суппорта, например, для одного известного немецкого автомобильного бренда. Само собой, линия полностью автоматизированная, все операции делают роботы.
В зеленый цвет Brembo красит суппорты для только для гибридных версий
После окрашивания и сушки на суппорт наносится логотип — Brembo или компании-заказчика, в соответствии с коммерческим договором. Интересный момент: машина для нанесения логотипа использует всего четыре цвета. Логотип в четырех цветах наносится только для М-серии BMW.
На этом конкретном производстве выпускается около 2,5 миллиона суппортов в год.
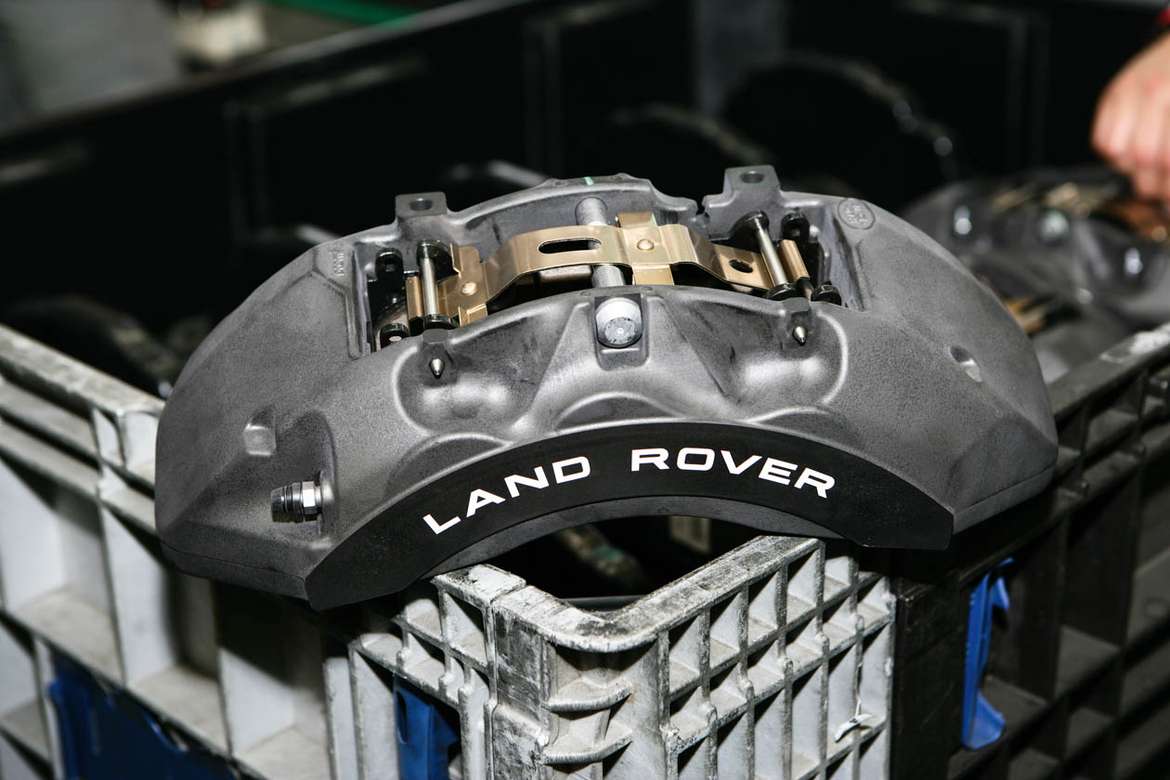
Цех производства тормозных колодок
Производство колодок расположено в отдельном цехе.
Линия по изготовлению тормозных колодок, в отличие от механической обработки дисков или суппортов, не такое эффектное и, в силу самого технологического процесса, достаточно закрытое от глаз производство. В одной части варится фрикционная смесь, которая поступает в формы, находящиеся в другой, нижней части линии. Там, после нанесения смеси на подготовленные специальным образом для лучшей адгезии металлические каркасы, колодки формуют под давлением. Затем их отправляют в печь, где проходит процесс запекания для того, чтобы все компоненты фрикционной смеси соединились воедино. Далее те колодки, для которых предусмотрено спецификацией, отправляются на специальную термическую обработку – скорчинг. В финале готовые колодки ожидает покраска и маркировка.
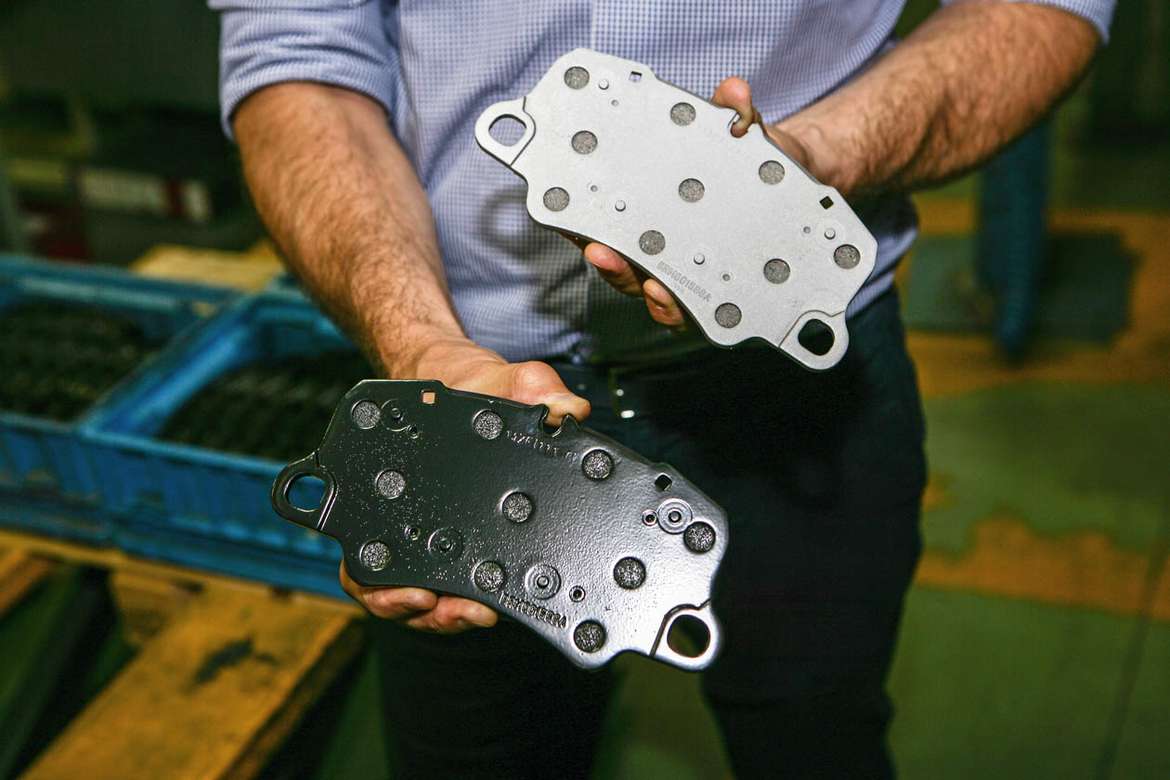
Рецепты фрикционных смесей у Brembo свои. Компания закупает порядка трехсот различных компонентов, которые используются для приготовления 40 различных рецептур смеси.
Стоит обратить внимание, что многие автопроизводители сотрудничают не с одним поставщиком колодок, потому, согласно контрактам, в суппортах Brembo при поставке на конвейер могут стоять тормозные колодки и других производителей.
Сборочный цех
Здесь же, в Курно, находится центральная сборочная линия суппортов, на которой изучают и улучшают все процессы сборки, чтобы в дальнейшем перенести опыт на другие производственные площадки Brembo.
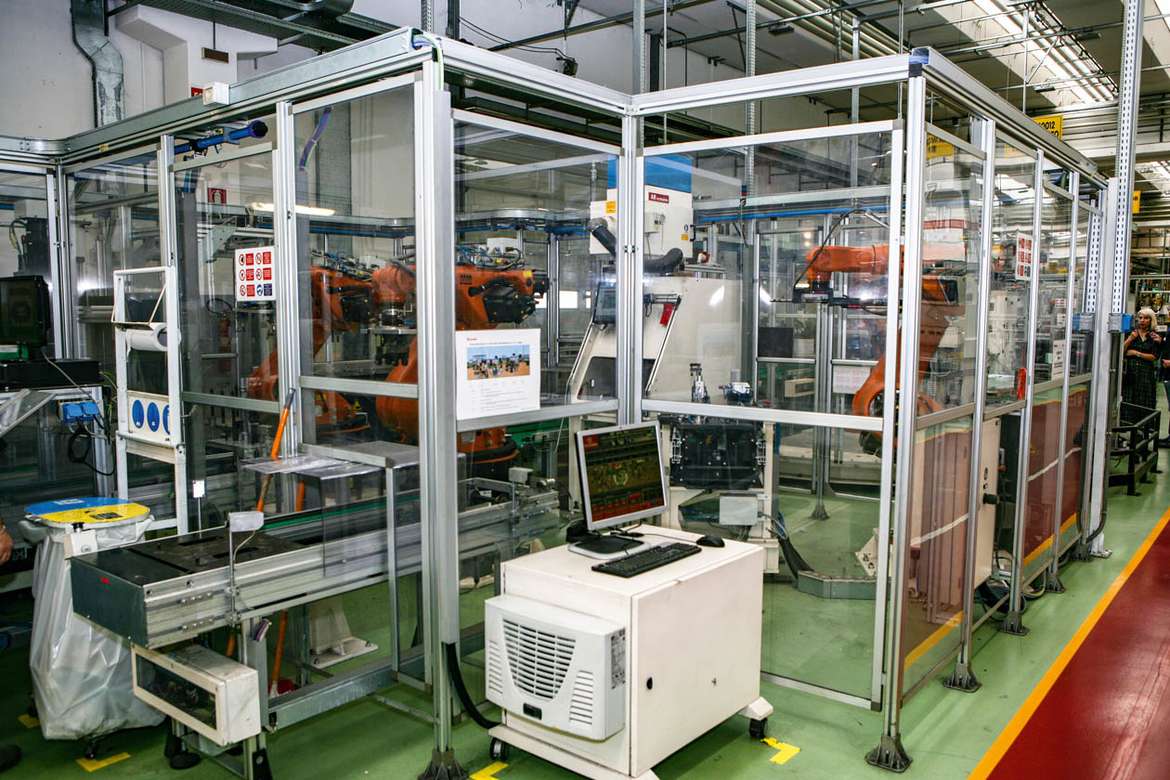
Сборка начинается с установки в суппорт штуцеров для прокачки тормозной системы, а далее лазером наносятся данные (серийный номер, номер партии, дата производства и т. д.), по которым в дальнейшем можно отследить всю историю производства конкретного суппорта.
На следующем этапе суппорт попадает на проверочный стенд, где в тормозной контур под давлением через установленные на первом этапе штуцеры подается воздух. Как только суппорт прошел тестирование и проверку, робот наносит в отверстия для тормозных поршней небольшое количество смазки, после чего суппорт отправляется на установку манжет, поршней, пыльников и прочих компонентов.
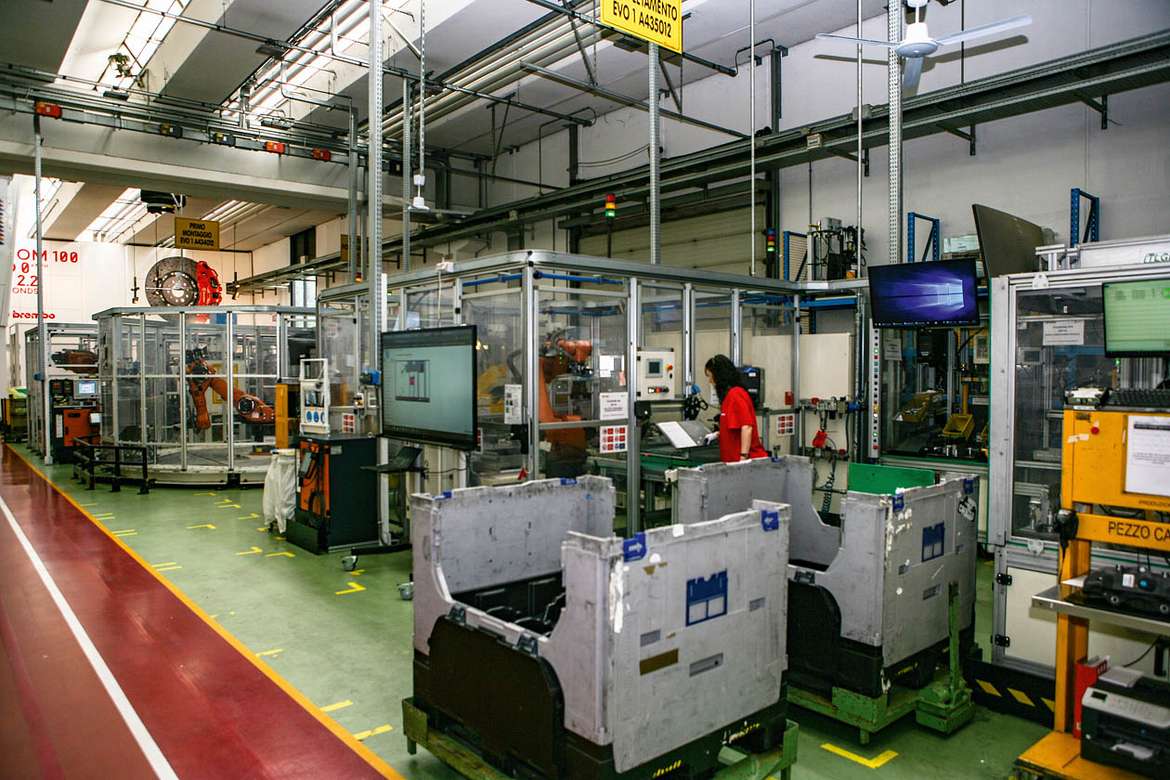
Далее суппорт попадает на стенд, где испытывается на высокое давление и деформацию. Его тестируют под давлением 200 бар, после чего проверяют все параметры на наличие деформаций и повреждений. Если все хорошо, то суппорт попадает на вакуумный тест.
Ну а затем идет уже финальная сборка, когда устанавливаются пружины, направляющие пальцы и остальные детали. Оператор только контролирует подачу комплектующих на линию, а установка осуществляется роботами. На финальном этапе суппорты упаковывают и отправляют клиенту.
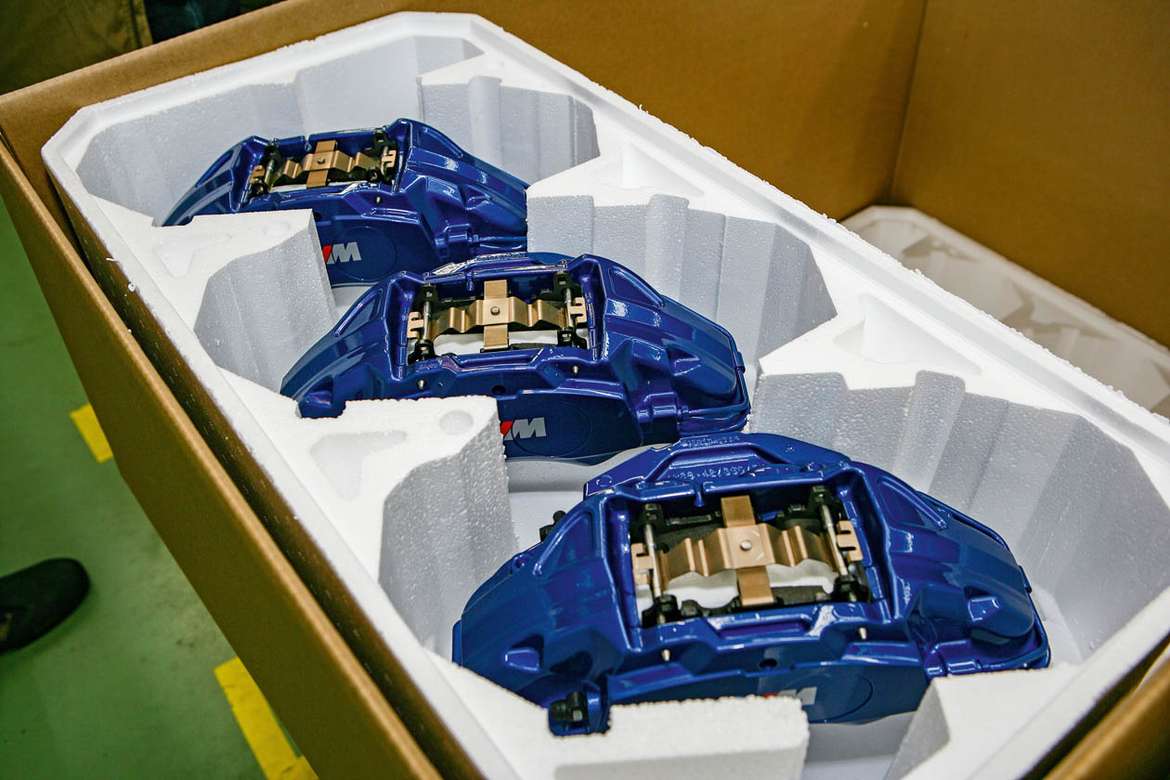

Программа «Индустрия 4.0»
Все производственные линии подсоединены к единой сети и базе данных Brembo. В режиме онлайн можно отследить каждое изделие, на какой производственной стадии оно находится. Данные на мониторе отображаются в реальном времени. После регистрации суппорта все сведения по нему попадают в базу данных и отслеживаются программой.
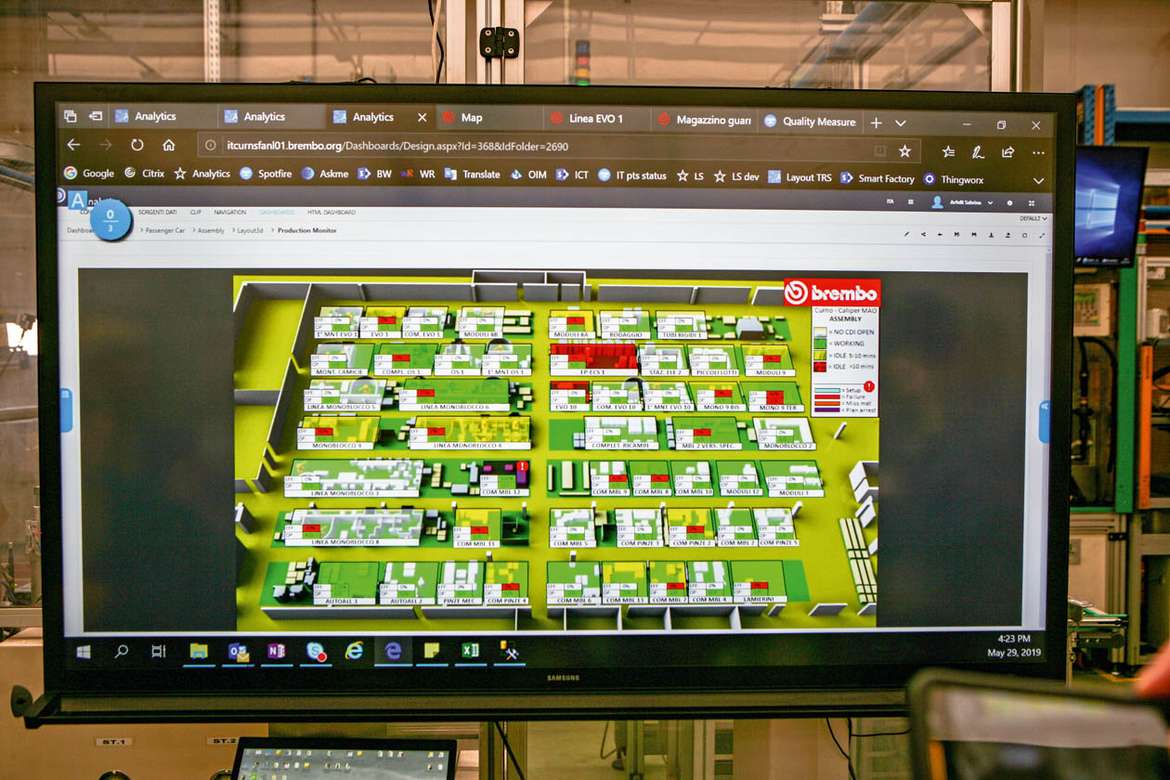
Также программа «Индустрия 4.0» позволяет видеть, какое количество деталей на данный момент находится на конкретной линии, какой артикул сейчас производится, какое количество изготовлено в текущую смену, текущее состояние линии и т.д. Это инструмент, который позволяет полностью следить за процессом производства, получая и анализируя детальную информацию по продуктам.
В дальнейшем на базе программы планируется внедрение интерактивной видеоинструкции для подготовки производственного персонала, где будут пошагово показаны все этапы производства.

Испытательный центр Brembo
В знаменитом технологическом парке Kilometro Rosso, в городке Стеццано, также расположенном недалеко от Бергамо, находится испытательный департамент Brembo. Это тестовая площадка для всех видов транспорта — от мотоциклов до грузовых автомобилей. Обычно процесс происходит следующим образом: сюда доставляются транспортные средства, на которые устанавливаются различные тормозные системы, и затем проводится цикл всевозможных испытаний, чтобы в дальнейшем разработать наиболее эффективные и подходящие под требования тормозные механизмы.
На испытания попадают как предпроизводственные прототипы автомобилей, так и серийные образцы, которым требуется усовершенствование тормозной системы. Например, новый суппорт с улучшенной системой охлаждения или 10-поршневые суппорта с карбон-керамическими дисками и плавающей центральной частью для «заряженных» версий автомобилей премиум-класса.
Здесь же находится передовая лаборатория Brembo Mehatronic Lab, про которую можно без преувеличения сказать, что здесь занимаются будущим торможения.
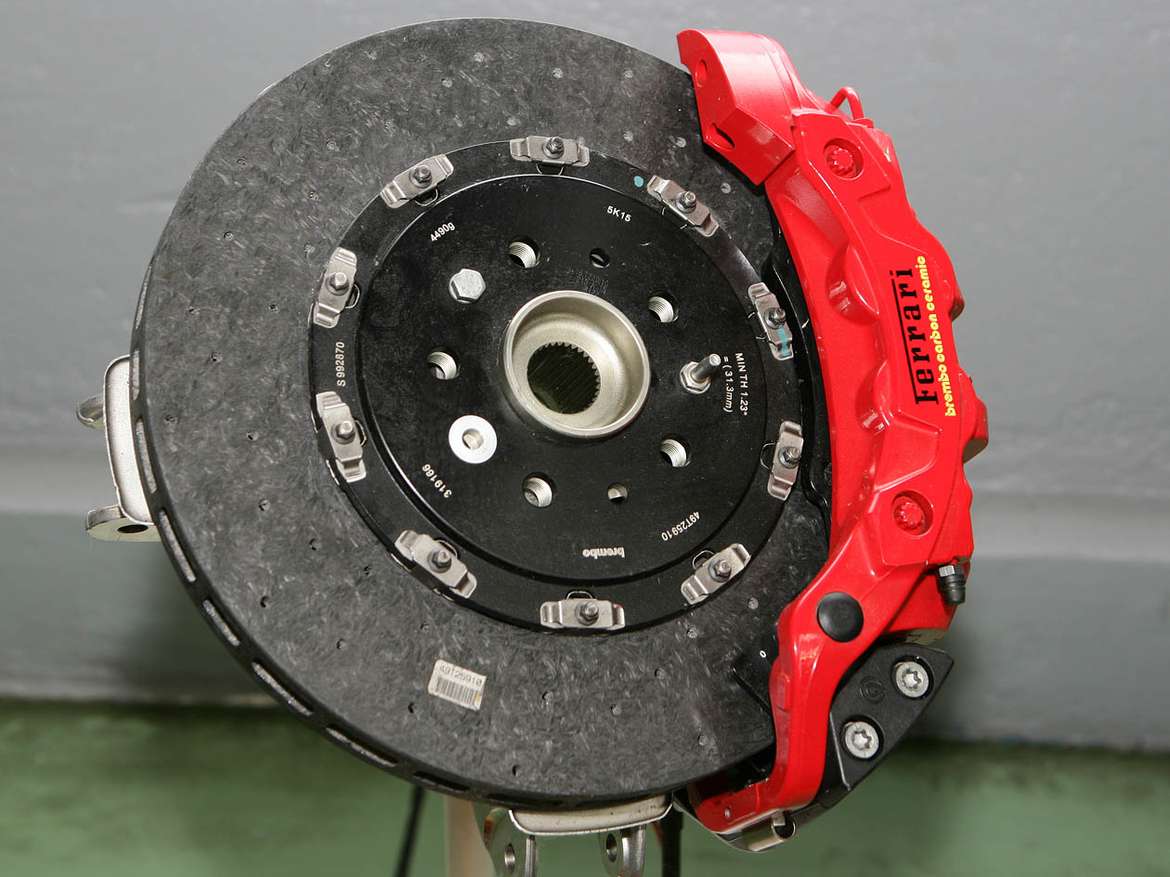