Антикоррозийная защита трубопроводов, резервуаров и труб под горючие жидкости
Курс повышения квалификации по программе Антикоррозийная защита трубопроводов, резервуаров и труб под горючие жидкости предназначена для знакомства с современной теорией коррозии, методами коррозионных испытаний и средствами защиты трубопроводов, резервуаров и труб под горючие жидкости; развития практических навыков коррозионных исследований и выбору средств антикоррозионной защиты трубопроводов, резервуаров и труб под горючие жидкости.
Тип программы: программа повышения квалификации.
Срок освоения программы: 72 часа.
Форма обучения: очная, очно-заочная (дистанционная).
Категория слушателей: руководители и специалисты
Цель реализации программы повышения квалификации: совершенствование и (или) получение новых компетенций, необходимых выполнения работ по антикоррозийной защите трубопроводов, резервуаров и труб под горючие жидкости.
Получаемые знания
- термины и определения, касающиеся проблемы коррозии материалов;
- основные виды коррозионных разрушений и причины их образования;
- коррозионностойкие металлические и неметаллические материалы, материалы, применяемые в качестве защитных покрытий;
- контроль качества защитных покрытий;
- основные требования нормативных документов в области противокоррозионной защиты основные требования нормативных документов в области защиты трубопроводов, резервуаров и труб под горючие жидкости;
- технические характеристики средств противокоррозионной защиты трубопроводов, резервуаров и труб под горючие жидкости;
- правила учета результатов обследования трубопроводов, резервуаров и труб под горючие жидкости и ведения соответствующей документации.
Учебный план
-
Теоретические основы коррозии металлов.
- Основные виды коррозии и коррозионных разрушений.
- Коррозия стальных резервуаров для хранения нефти и нефтепродуктов.
- Защита от коррозии внутренней поверхности стальных резервуаров.
- Защита от коррозии наружной поверхности стальных резервуаров.
- Технология работ по созданию систем защиты от коррозии внутренней поверхности стальных резервуаров.
- Методы коррозионных испытаний и коррозионностойкие материалы для трубопроводов, резервуаров и труб под горючие жидкости.
- Антикоррозионная защита конструкций и аппаратуры нефтегазовых производств.
8 лучших антикоррозийных средств для автомобиля — Рейтинг 2020 года (Топ 8)
Конечно, Кентервильское привидение коррозии уже не так сильно пугает владельцев даже бюджетных автомобилей – одна только протравка фосфатирующим грунтом при окраске на заводе дает многое. Если, конечно, речь не идет об УАЗовском «Патриоте» — тот своей склонностью гнить уже на стоянке автосалона известен печально, и не зря – автору, например, хорошо знаком человек, умудрившийся успеть дважды поменять всю машину по гарантии из-за вылезавшей уже спустя полгода сквозной (!) коррозии. Но и не новых автомобилей у нас на дорогах много, да и не одними только защитными свойствами отличаются современные антикоры – многие составы имеют еще и приличные шумоизоляционные свойства, если правильно нанесены. Так что популярность антикоров все равно не особо снижается.
Но проблема в том, что разных составов и форм в автомагазинах много, и не все они либо эффективны в принципе, либо мало подходят для самостоятельного применения. Тогда что именно выбирать? Попробуем разобраться.
Рейтинг лучших антикоррозийных средств для автомобиля
Какой антикор выбрать?
Основных применений у антикоррозийных средств два, соответственно и требования к обоим группам очень сильно различаются.
Антикоры для днища и колесных арок подвергаются постоянному абразивному воздействию песка и ударам.
Стойкость к соли очень важна – зимой днище и арки будут обрастать слоем дорожной грязи, то есть противогололедные реагенты будут действовать на покрытие очень длительное время. Разрушающийся в подобных условиях антикор надолго машину не защитит.
Такие антикоры в основном рассчитаны на нанесение специальными пистолетами для высоковязких составов. Это позволяет быстро наносить слой нужной толщины, вспенивать его для улучшения шумоизоляции. Но проникает в микропоры и ржавчину густая мастика очень плохо – то есть наносить подобный состав нужно либо на чистое, еще не имеющее повреждений днище нового автомобиля, или предварительно удалить либо обработать химически имеющиеся следы коррозии.
А вот антикоры для скрытых полостей, наоборот, очень текучи – их задача проникать в самые труднодоступные места, ведь глазами проконтролировать нанесение антикора, в отличие от обработки днища, тут проблематично. Текучесть позволяет антикорам для скрытых полостей отлично проникать и в трещины, микропоры краски, пропитывать ржавчину – поэтому в их состав можно вводить очень эффективные ингибиторы коррозии. Но и высыхать антикор должен быстро, оставляя прочную пленку – иначе, стекая вниз, как «Мовиль» или тот же «Раст-стоп», он будет со временем все больше «оголять» защиту.
Хорошо подготовить скрытые полости к обработке нелегко – это не днище, которое хоть пескоструем можно драть до чистого металла. Поэтому к антикору предъявляются еще и высокие требования по вытеснению воды, солевых растворов – проникая в микротрещины и ржавый слой, антикор обязан вытеснить причину коррозии, а не «запечатать» ее собой, иначе металл продолжит гнить.
В любом случае не забывайте о прочтении инструкции и о качестве подготовки: ничто так не портит результат антикоррозийной обработки, как несоблюдение требований производителя к применению антикора или грубые ошибки в подготовке автомобиля.
Услуги по антикоррозийной обработке емкостей » КАМ-КЛЮЧ
Емкости в резервуарном парке предприятия стоят весьма дорого. По этой причине за их состоянием нужно внимательно следить. С целью увеличения их эксплуатационного срока, применяются специальные лакокрасочные покрытия, защищающие от коррозийных процессов. Они максимально надежно защищают все базовые части вместилищ жидкостей с внутренней и наружной стороны (крышу, стенку, днище, кессон) от разрушения и внешних негативных факторов. Компания «Кам-Ключ» успешно завершила более десятка тендеров на услуги по антикоррозийной обработке емкостей, это видно в нашем портфолио.
В работе наши специалисты применяют качественные средства и специализированное передовое оборудование. Способ проведения антикоррозийной обработки резервуаров нефтепродуктов и других жидкостей зависит от следующих факторов:
- Условий эксплуатации конструкции;
- Климата местности;
- Воздействия внешних факторов: осадков, ветра, ультрафиолета и т.д.;
- Вида хранимого продукта (агрессивность содержимого и его паров). Согласно перечисленным особенностям наши специалисты составляют проект, в котором указывается технология, применяемые средства и срок эксплуатации защитного покрытия. Также в проекте прописывается подготовка поверхности конструкции, спецоборудование, которое будет использоваться и методы контроля качества.
Достоинства материалов, используемых нашими специалистами работе
- Большой выбор производителей противокоррозийных средств;
- Длительный срок защиты от образования ржавчины;
- Конкурентная стоимость;
- Высокое качество.
Плюсы антикоррозийной обработки резервуаров нефтепродуктов и других емкостей
- Снижается риск возникновения аварийных ситуаций по причине потери прочностных качеств конструкцией: истончаются стенки от того, что на них образуется ржавчина.
- Увеличивается длительность срока службы емкости за счет того, то процесс коррозии замедляется.
Внешняя антикоррозийная обработка резервуаров нефтепродуктов, воды и других жидкостей
Внешняя АКЗ предусматривает нанесение одного из нижеперечисленных антикоррозийных составов:
- Эмаль, получаемая методом высокотемпературного антикора. В нее добавлены наполнители и присадки.
- Лак – покрытие, основанное на ПВХ смоле.
- Грунтовочный состав, который наносится первым слоем на подготовленную к покраске поверхность. Предназначен для создания надежной адгезии верхних кроющих слоев.
- Краска, основанная на синтезе сложных спиртов, многоосновных кислот и на полимерах.
- Грунт-эмаль материал сополимера, в котором присутствуют различные добавки.
- Комбинированное покрытие.
Из-за внушительных габаритов конструкции ёмкостей для жидкостей часто нанесение покрытия проводится с применением технологии распыления (бывает воздушное и безвоздушное) и с эксплуатацией специализированного пневмоинструмента. Перед нанесением материала, защищающего от образования ржавчины, поверхность очищается и обезжиривается. Благодаря предварительной подготовке обеспечивается сцепляемость защитного материала и металла. После антикоррозийной обработки за цистерной не нужно ухаживать. Достаточно только контролировать ее состояние, желательно, ограничить взаимодействие покрытия с агрессивной средой.
Внутренняя АКЗ емкостей
Обработка с целью защиты от образования ржавчины в емкости осуществляется аналогичной наружной, но антикоррозийных слоев больше. Причиной этому является содержимое вместилищ жидкостей: в них часто содержится агрессивная среда для металлоконструкций.
Как наносится противокоррозионное покрытие на внутреннюю поверхность емкости
В первую очередь специалисты нашей компании сливают жидкость, находящуюся в вместилище жидкости. Потому зачищают внутреннюю поверхность бака: выполняют дегазацию и обезжиривают. После осуществляется обработка песком из пескоструя. Затем наносятся моющие жидкости для наиболее тщательной очистки и смываются водой. Когда емкость высохнет, наносится антикоррозийное покрытие. Чтобы поверхность высохла быстрее, ее высушивают высокомощными пылесосами. Финальный слой сушится минимум сутки.
Если антикоррозийная обработка емкости для воды или другой жидкости была проведена с несоблюдением технологии, то металл начнет, либо продолжит разрушаться. Из-за ржавчины стенки начнут утончаться, в последствии появляются дыры, и цистерна утратит свою герметичность: содержимое просочится через них. В этом случае придется демонтировать старую конструкцию и устанавливать новый резервуар, наносить на него тоже противокоррозионный материал.
Подземная защита
Если конструкция углублена в землю, риски ее разрушения увеличиваются. По этой причине необходимо более надежно защитить днище с помощью многослойной гидроизоляции. Также применив электрохимический метод антикора, который предусматривает подключение ко дну конструкции электрически: подключается проектор либо проекторные устройства.
Преимущества сотрудничества с нашей компанией
К основным положительным сторонам нашей компании можно отнести:
- профессионализм и опыт наших сотрудников в АКЗ;
- антикор покрытиями высокого качества;
- эксплуатацию передовой техники;
- быстрое и качественное выполнение работ опытными профессионалами;
- конкурентные цены.
Цены на услуги по антикоррозийной обработке емкостей
Цена услуги зависит от необходимости эксплуатации спецтехники, используемых материалов, параметров конструкции и ее общего состояния. Связаться с менеджерами нашей компании, чтобы узнать стоимость и заказать антикоррозийную обработку цистерны или другой емкости, оформив заявку на сайте либо позвонив по телефону. Консультанты ответят на интересующие вопросы, оформят заказ услуги, помогут со знанием дела подобрать материал для антикора, рассчитают смету и с другими смежными вопросами.
Оформить заказ
Все, что вы хотели знать об антифризах
Что такое антифриз?
Антифриз – жидкость для охлаждающей системы двигателя. Автомобили могли бы ездить и на воде в системе охлаждения, как они когда-то и делали. Но вода, к сожалению, уступает антифризу по всем химическим свойствам: температуре замерзания и кипения, стойкости к образованию накипи и коррозии в системе охлаждения. Вода не может выполнить всех защитных функций, которые выполняет антифриз. В составе антифриза обычно присутствуют двухатомный спирт – этиленгликоль, вода и антикоррозийные, антивспенивающие и стабилизирующие присадки (ингибиторы).
Что лучше антифриз или тосол?
Тосол – это всего лишь название одного из антифризов. Тосол был создан в советское время, а поскольку торговую марку «Тосол» не зарегистрировали, то со временем название стало нарицательным. И поэтому вопросы «что заливать тосол или антифриз?» или «что лучше тосол или антифриз?», просто некорректные, так как тосол и есть по своей сути антифриз. Таким образом мнение, что отечественным автомобилям подходит только тосол, тоже не верно.
Виды и характеристики антифризов
Стандартов для производства антифризов много. Они характеризируют продукт по параметрам: плотность, температура начала кристаллизации, воздействие на металл, влияние на резиновые детали. Однако эти стандарты не включают в себя сведения о составе, количестве присадок и цвете жидкости.
Помимо общепринятых стандартов, некоторые производители автомобилей разработали свои спецификации с дополнительными требованиями. Так, Volkswagen использует маркировку G11, G12 и т.д.Поэтому выбирать антифриз по цвету неразумно. У разных производителей одинаковый по составляющим компонентам антифриз бывает разного цвета.

LAVR не исключение. В нашей линейке есть 2 вида антифризов – G11 и G12+:
- G11 (Ln1705, Ln1706) – охлаждающая жидкость гибридного типа. В основе состава данного антифриза находится моноэтиленгликоль и пакет антикоррозийных присадок. Жидкость образует защитную пленку на всей поверхности охлаждающей системы, что обеспечивает максимальную защиту всех узлов системы, увеличивая ресурс работы помпы, радиатора, насоса, резиновых уплотнителей. Срок службы данного антифриза – 3 года (или 150000 км).
- G12+ (Ln1709, Ln1710) – охлаждающая жидкость карбоксилатного типа (Organic Acid Technology). Жидкость не образует пленку на всей поверхности охлаждающей системы, а воздействует только на пораженные ржавчиной участки. Срок службы данного антифриза – 5 лет (или 250000 км).
Как слить антифриз из системы охлаждения?
Когда срок службы охлаждающей жидкости подходит к концу, стоит заранее задуматься о замене. Определить состояние антифриза можно даже визуально. Если он стал белым или мутным, то это явный признак потери свойств препарата. Если антифриз стал рыжим или с красным оттенком, то в жидкости присутствует ржавчина. Такой антифриз стоит немедленно заменить. Если в охлаждающей жидкости появились пена, осадок или хлопья, необходимо не только заменить антифриз, но и проверить всю систему охлаждения. Для профилактики подобных проблем мы советуем делать промывку системы охлаждения при каждой замене охлаждающей жидкости
Существует несколько вариантов, чем можно сделать промывку системы охлаждения в зависимости от степени загрязнения.
- Использовать Синтетическую промывку LAVR (Ln1107) в случае небольших загрязнений или для профилактики. Она заливается прямо в старый антифриз перед его заменой. Походит для любых систем охлаждения и эффективно удаляет загрязнения.
- Использовать Классическую промывку LAVR (Ln1103) в случае средних и сильных загрязнений системы охлаждения. Данная промывка является концентрированной и заливается в систему без антифриза, разбавляется дистиллированной водой и прогоняется по системе. Также подходит для всех систем охлаждения.
- Использовать Набор «Полная очистка системы охлаждения» LAVR (Ln1106) в случае серьезных проблем с загрязнением системы охлаждения. Двухэтапная система позволяет полностью избавиться от комбинированных загрязнений (известковых и коррозийных).
Подробные инструкции по применению препаратов на страницах продуктов и на упаковках.
Чтобы слить старый антифриз, передняя часть авто должна быть ниже задней, так антифриз быстрее стечет. Затем поворачиваем пробку расширительного бачка, спускаем излишки давления. Без давления антифриз быстро остынет. Открываем пробку полностью, когда до нее можно дотронуться рукой. Далее открываем слив радиатора (иного нужно отсоединить патрубок от радиатора) и сливаем жидкость.
Конструкции двигателей, как вы понимаете, существуют разные. И у каждого конкретного мотора есть своя специфика слива и замены охлаждающей жидкости. Универсальной технологии нет. Поэтому рекомендуем вам предварительно изучить вопрос замены жидкости именно для вашего автомобиля.
Какой антифриз заливать?
Сколько и какой антифриз лить – один из самых распространенных вопросов. Тип антифриза подбирается, исходя из марки и модели автомобиля. Как правило производители указывают какой антифриз лучше заливать в конкретную машину. Как уже говорили, цвет в этом случае не имеет значения. Поэтому вопрос «Можно ли смешивать антифризы разных цветов?» также спорный поскольку мы не знаем разные это антифризы по составу или одинаковые.
Куда и сколько заливать антифриза?
После удаления старой жидкости охлаждения и промывки системы, встает вопрос, как нужно правильно заливать антифриз? Порядок действий следующий:
- Закрываем сливное отверстие на радиаторе или монтируем обратно патрубок.
Заливаем новый антифриз в расширительный бачок, либо, если модель разборная, то в горловину радиатора заливается свежая жидкость. Важно залить антифриз не в омывательный бачок. Он чаще всего находится рядом с расширительным и похож на него внешне.
- Лить охлаждающую жидкость нужно равномерно, без спешки и остановок, чтобы исключить попадания воздуха в систему охлаждения, иначе придется долго прокачивать антифриз по системе.
- При заливе также важно следить за уровнем антифриза в бачке и радиаторе. Нижняя отметка для радиатора. Максимальная — для расширительного бачка, поскольку антифриз в дальнейшем разойдется по системе и его станет в бачке меньше.
- После стравливаем воздух из системы. Чаще всего на блоке цилиндров двигателя есть кран-винт, которым это делается.
- Далее автомобиль заводится на 5-10 мин, глушится и проверяется уровень антифриза в бачке.
Можно ли смешивать антифризы при доливе?
Доливать антифриз в систему можно только при наличии у жидкостей одинакового состава. Цвет при этом может отличаться (красный, зеленый, желтый). Как мы уже говорили цвет не имеет значения. Однако лучше для доливки брать антифриз одного производителя, поскольку разница в ингибиторах может отличаться. Что будет если смешать антифризы разных типов? Использование разных охлаждающих жидкостей чревато выпадением осадка, который начнет засорять тонкие трубки радиатора и другие элементы системы охлаждения.
Как часто менять антифриз?
Антифриз меняется согласно своему сроку эксплуатации. Например, антифриз LAVR G11 имеет срок службы до 3 лет (или 150000 км), а LAVR G12+ — до 5 лет (или 250000 км).
Антикоррозионная жидкость для ржавых поверхностей DINITROL ML 5л
DINITROL ML 5л
- ML — антикоррозионная жидкость на масляно-восковой основе с очень высокой проникающей и влаговытесняющей способностью в сварных соединениях, микротрещинах и т.
д.
- В состав материала входят специальные пленкообразователи, растворители и уникальные ингибиторы коррозии, обеспечивающие надежную защиту металла от коррозии.
- Материал останавливает начавшийся процесс коррозии.
- Срок службы защитной пленки ML в скрытых полостях, при однослойном покрытии до 1-го года!
- DINITROL ML не оказывает вредного воздействия на лакокрасочные покрытия автомобиля,
- Он обладает хорошей адгезией к практически любым поверхностям, после испарения растворителей не проводит электричество и имеет нейтральный запах.
Область применения:
- DINITROL ML применяется для антикоррозийной обработки скрытых полостей автомобилей: двери, пороги, стойки, усилители и т.д., а также сварных соединений и мест с начавшейся коррозией.
- Рекомендуется наносить как грунтовочный слой перед нанесением более густых антикоррозионных материалов на днище и колесных арках.
- Материал предназначен для б/у автомобилей.
Метод нанесения материала:
- DINITROL ML наносится распылением, натиранием или с аэрозоля.
- Для распыления используется безвоздушный или воздушный метод.
- Наносить так, чтобы материал мог проникать в сварные швы, стыки, трещины и т.д.
- DINITROL ML наносится при комнатной температуре (16 ÷ 20°C).
Поверхности должны быть чистыми, сухими и не иметь следов смазки, масла и пыли. - Для обработки труднодоступных поверхностей используйте специально предназначенную для этого насадку.
Удаление материала ML.
- Пленка материала легко удаляется при помощи White Spirit или щелочных моющих средств.
Жидкость для удаления ржавчины | Коррозия X ™
Описание
Жидкость для удаления ржавчины Corrosion X — это высокоэффективная формула, которая полностью устраняет наросты ржавчины, которые могут возникнуть на железных и стальных поверхностях. Несмотря на эти характеристики, он остается безопасным для тех, кто работает или находится в непосредственной близости от него. Он не выделяет чрезмерных испарений и полностью безопасен для окружающей среды, что позволяет легко утилизировать его.
Несмотря на эти впечатляющие характеристики по самой ржавчине, эта антикоррозийная жидкость остается безвредной. Инертен по отношению к другим необходимым материалам, таким как медь, латунь, пластик, винил и резина. Вы можете даже применить это решение на окрашенных поверхностях для удаления проблемной «кровоточащей ржавчины».
Эта быстрая и простая формула позволяет вам либо работать с использованием тематического приложения с губкой. Или ткань для создания ванны для удаления ржавчины, идеально подходящей для стойкой или устойчивой коррозии, которая может распространяться и / или стареть.
Предупреждение — этот продукт предназначен для использования специально обученными специалистами и не предназначен для использования на цветных металлах.
Использование жидкости для удаления ржавчины Corrosion X ™
• Типичные области применения этого продукта включают удаление ржавчины с автомобилей и мотоциклов, а также грузовых автомобилей и лодок.
• Вы можете использовать это для удаления ржавчины с промышленного оборудования, а также любых инструментов.
• Общая реставрация металлических деталей.
Преимущества
• Нет вредных вредных выбросов.
• Не содержит растворителей любого вида.
• Не содержит кислотных компонентов любого вида.
• Безвреден для кожи и всех, кто с ней обращается.
• Негорючий, без элементов VOC.
• Не реагирует с краской автомобиля.
• Безопасно использовать на проводке.
Совместимость
Обратите внимание, что после удаления ржавчины с ваших инструментов очень важно обработать металлическую поверхность раствором защитного покрытия, такого как Corrosion X ™ или Xtreme Clean ™. Это предотвратит появление ржавчины на поверхности. Для достижения наилучших результатов сначала нейтрализуйте и промойте очищенную металлическую поверхность.
Технические данные для удаления ржавчины
Срок поставки
Со склада.
Объединенное Королевство. 1-2 рабочих дня на материке
Для получения дополнительной информации об удалении ржавчины, пожалуйста, посетите корпоративный сайт.
Смотрите наши сварщики тепла hawo
Гипермир » Антикоррозийная обработка автомобиля
Антикоррозийное покрытие используется для защиты поверхностей автомобиля от разъедания ржавчиной. Оно продлевает сохранность металла и внешнего вида автомобиля. Процедуру обработки следует делать хотя бы раз в 3 года.
Какие существуют виды обработки.
Есть два вида средств, используемых для этой цели. Выбор их зависит от места нанесения покрытия. Битумной мастикой, изготовленной из синтетических смол, пользуются для защиты металла от ударов и других повреждений. Антикоррозийными средствами являются также материалы, основой которых являются каучук и ПВХ. Они более долговечны, но применяют их в основном на машиностроительных заводах.
Внутренние поверхности автомобиля обрабатываются антикоррозийными составами, которые изготовлены на масляной основе, а также на основе воска. После обработки такими средствами остается тонкая пленка, которая защищает от попадания влаги и коррозии.
Выбор материалов и средств для антикоррозийной обработки автомобиля.
Делая обработку всего кузова машины, нежелательно покупать аэрозольные баллончики с антикоррозийным средством. Обычно они используются для небольших ремонтов, так как в этих средствах мало защитных компонентов. Для того, чтобы обработать кузов самостоятельно, применяется такое средство, как антикор. Оно обычно продается в тарах разного объема. Нужно с вниманием отнестись к данным на упаковке: чье производство, срок годности, состав , как применять средство. Также определиться, какая часть авто будет обрабатываться: полностью автомобиль или части скрытых, внешних деталей. Соответственно этому подбирается тип средства и еще: в составе его в обязательно должны быть вытеснители жидкости. Без их наличия эффект препарата будет гораздо ниже.
Как подготовить антикор самостоятельно.
Для покрытия днища берется выбранное антикоррозийное средство, добавляется пушечная смазка (сто граммов на один литр средства) и пластилин (одна упаковка на пять литров), все перемешивается и нагревается на водяной бане.
Для обработки внутренних плоскостей кузова используются баллончики с антикоррозийным препаратом.
В салоне машины средство наносится только на пол из – за большей уязвимости к коррозии. Перед покраской машины обязательно нужно обработать антикоррозийной смесью всю ее поверхность хотя бы в один слой.
Переодически подвергая автомобиль такой обработке, авто прослужит вам несколько десятилетий.
В магазине Гипермир вы можете купить средства от коррозии.
Типы и советы по выбору рецептуры покрытия
TAGS : Ингибиторы коррозии в покрытиях
Хотя само покрытие играет важную роль в защите от коррозии, использование жидких ингибиторов коррозии помогает и значительно улучшает это свойство.
Эти агенты можно использовать отдельно, например, в прозрачных лаках, или в сочетании с различными антикоррозийными пигментами. Эта синергия улучшает коррозионную стойкость краски и даже позволяет:
- Уменьшить количество антикоррозионных пигментов
- Обеспечивает отличные результаты и является альтернативой вопросам снижения затрат и защиты окружающей среды.
Но, прежде чем переходить к ингибиторам коррозии, давайте сначала разберемся с явлением коррозии.
Коррозия покрытий
Коррозия — это окислительно-восстановительная реакция в присутствии электролита, приводящая к порче металла. Обычно для черных металлов, таких как железо и сталь, коррозия также называется «ржавчиной» .
Проводимость электролита имеет решающее значение: чем выше проводимость, тем быстрее коррозия
Вот почему в соленой воде ржавчина развивается быстрее, чем в чистой.
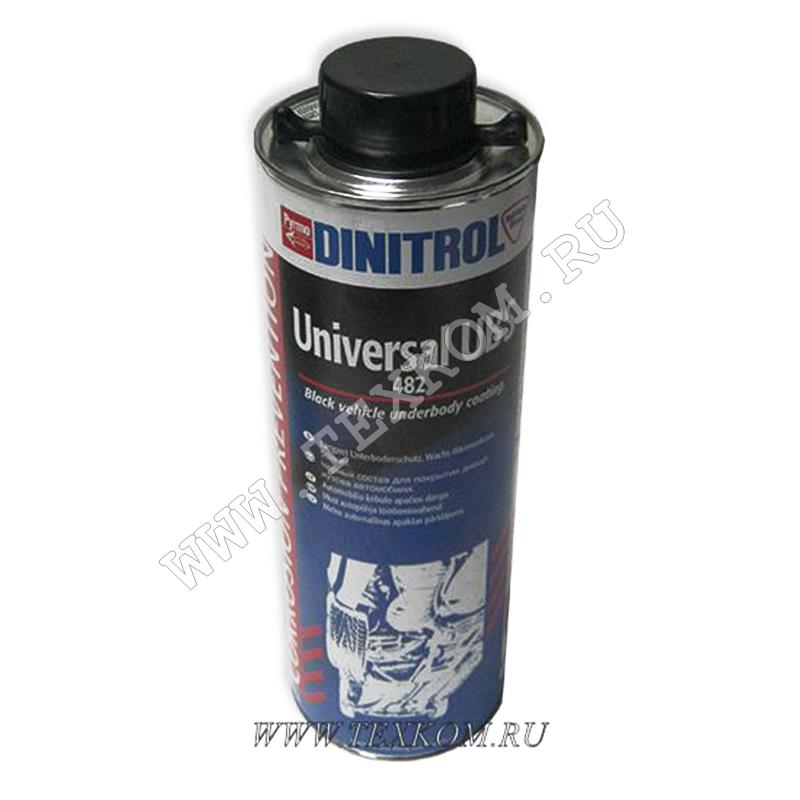
Коррозия металлической детали может:
- Изменение внешнего вида поверхности
- Ослабить его свойства
- Повреждение прилегающих частей
Помимо изменения цвета и внешнего вида, может ослабить структуру / разрушить саму структуру .
В покрытиях преобладает электрохимическая коррозия . Это комбинация двух проводников (электродов) с водным раствором электролита. Металл с более отрицательным потенциалом будет анодом и подвергнется коррозии, тогда как металл с более положительным потенциалом будет катодом.Затем в растворе электролита происходит окислительно-восстановительная реакция.
Но коррозия также может происходить в той же металлической системе, где на поверхности существуют разности потенциалов. Эти различия в потенциале могут происходить из-за неоднородного химического состава, например:
- Отличия в слое покрытия
- Загрязнение
- Царапины
- Точечные отверстия…
В чугуне коррозия возникает, когда различные части поверхности, образующие анод и катод, подвергаются воздействию раствора электролита.Без электролита коррозия сильно снижается. Другими словами, соленая атмосфера (как и морские условия) более агрессивна, чем незагрязненная. В чистой воде коррозии нет.
Помимо этой реакции коррозии, на коррозию покрытия могут влиять многие другие факторы, например:
- Качество поверхности : Неоднородная поверхность увеличивает риск коррозии. Обработанная поверхность предотвратит это. Перед нанесением покрытия поверхность должна быть очищена от загрязнений.
- Адгезия слоя покрытия : Покрытие образует защитный барьер на металлической поверхности. Отсутствие адгезии будет слабым местом с высоким риском развития коррозии. Требуется идеальная поверхность смачивание …
»Ознакомьтесь с советами: адгезия в красках и покрытиях! - Качество слоя покрытия : Проколы, кратеры и другие дефекты поверхности также ослабят защиту металла.
Когда возникает коррозия?
Риск коррозии присутствует на протяжении всего срока службы покрытия, от хранения самой жидкой краски (коррозия в банке) до нанесения (мгновенная ржавчина) и много лет спустя (долговременная коррозия):
Хранение Внутренняя коррозия. Критично для покрытий на водной основе. | Внутренняя коррозия Во время хранения краска непосредственно контактирует с железной банкой, вызывая коррозию. |
Применение Вспышка ржавчины краской на водной основе. Кроме того, нанесение краски на поверхность, загрязненную ржавчиной, может стать источником коррозии. | Вспышка ржавчины Краска на водной основе наносится непосредственно на металл. Появляется вскоре после нанесения из-за миграции ржавчины через пленку. |
Старение краски и основания Агрессивная среда, загрязнение, атмосферные воздействия могут ослабить пленку краски и увеличить риск развития коррозии. | Старение — долговременная коррозия Защитный барьер краски разрушается и появляются слабые места. Кроме того, незащищенные части подложки могут подвергнуться коррозии. |
Стратегии контроля / снижения коррозии
Контроль коррозии включает естественные химические реакции между металлической подложкой и окружающей средой. Есть несколько решений для контроля и уменьшения развития коррозии:
- Изменение свойств металла : Предварительная обработка улучшает коррозионную стойкость металла.
- Переход на неметаллические материалы : Но это не может удовлетворить все требования к конечному продукту…
- Подача электрического тока для питания электронов : Дорого и не всегда возможно!
- Используйте расходуемый анод.
: Состав краски, богатый защитными пигментами на основе цинка.
- Используйте антикоррозионные пигменты. : Самый распространенный раствор, антикоррозионные пигменты, которые со временем химически пассивируют металлическую поверхность (особенно хроматы, фосфаты и молибдаты).И может действовать как жертвенный пигмент в сочетании с оксидом цинка, как ингибитор коррозии фосфат цинка. Но некоторые из этих пигментов вредны для окружающей среды.
- Используйте органический ингибитор коррозии. : На основе различных структур, таких как амин, кислота, полимеры, соли, эти продукты образуют защитный барьер на поверхности металла и нарушают химическую реакцию, предотвращая развитие ржавчины. Пассивирующий слой предотвращает окисление металла.
Понять, каков механизм работы органических ингибиторов коррозии, можно по рисунку ниже:
Как работают ингибиторы коррозии?
Ингибитор коррозии может образовывать защитный слой на поверхности металла за счет:
- Химическая адсорбция
- Ионная комбинация
- Окисление основного металла (особенно алюминия)
Ингибитор контроля коррозии может образовывать комплекс с потенциально коррозионным компонентом и нейтрализовать реакцию коррозии.
Мы можем обобщить риск коррозии и способы повышения коррозионной стойкости со стороны состава:
Риск коррозии | На основе растворителей | Водный | |
Контейнер для хранения | Паровая фаза | ★ | ★ ★ ★ |
Мокрая фаза | – | ★ ★ | |
Применение | – | ★ ★ ★ | |
Долговременная коррозия | ★ ★ ★ | ★ ★ ★ |
Раствор против коррозии | На основе растворителей | Водный | |
Контейнер для хранения | Паровая фаза | — | Ингибиторы мгновенной коррозии |
Мокрая фаза | – | Ингибиторы ржавчины | |
Применение | – | Ингибиторы ржавчины | |
Долговременная коррозия | Антикоррозийные пигменты Ингибиторы коррозии | Антикоррозийные пигменты Ингибиторы коррозии |
Предварительная обработка основания для обеспечения антикоррозийных свойств
Когда покрытия используются в качестве средства уменьшения коррозии, важно, чтобы покрытие очень плотно прилегало к поверхности.

Конверсионные покрытия
Конверсионное покрытие действует как отличная основа для красок и в то же время обеспечивает отличную защиту от коррозии. Конверсионное покрытие представляет собой слабокислый водный раствор (на водной основе) химикатов. Фосфаты железа или цинка являются наиболее распространенными химическими веществами в составе, хотя другие химические соли также добавляются для выполнения различных функций.Металл обычно погружают в емкость с раствором. При погружении металл очень немного растворяется, и фосфат фактически оседает на чистом металле.
Праймеры Wash
На поверхность перед нанесением покрытия наносятся грунтовки Wash:
- Для пассивирования поверхности и временного обеспечения коррозионной стойкости
- Для создания клеевой основы для следующего покрытия
Гальваническое покрытие (OEM-процесс)
При нанесении гальванических покрытий используется электрический ток для нанесения органического покрытия, при котором на металлические поверхности равномерно наносятся тонкопленочные грунтовки и однослойные покрытия.
Процесс нанесения гальванического покрытия включает четыре этапа:
- Очистка подложки
- Конверсионное покрытие
- Уплотнение
- Сушка и охлаждение
Основные праймеры
Грунтовки используются для «герметизации» поверхности, чтобы растворители или вода верхних покрытий могли испаряться, поскольку они были разработаны для защиты от кислорода, влаги и коррозионных соединений на поверхности металла.
Типы ингибиторов коррозии и критерии выбора
Ингибиторы ржавчины
Покрытия на водной основе более чувствительны к коррозии, поскольку в них участвует… вода.Кроме того, многие катионы металлов (например, Fe 2+ , Железо II) растворимы в воде.

Покрытия на водной основе, наносимые на металл, когда слой краски еще влажный — типичная жертва мгновенной коррозии. Покрытия на водной основе при контакте с металлом создают высокий риск мгновенной ржавчины и коррозии внутри банки. Следовательно, становится необходимым использовать ингибитор ржавчины .
Большинство ингибиторов ржавчины содержат нитрит натрия (токсичные ингибиторы коррозии) . Также доступны безнитритные ингибиторы. Их следует использовать в более высоких дозах (до 1,5% от общей рецептуры).
Более экологичные версии без нитритов и боратов заменяют водорастворимые / диспергируемые и основанные на нитритах натрия. Большинство продуктов, представленных на рынке, имеют уровень дозировки от 0,2% до 1,5% (форма доставки от общего состава), что оказывает значительное влияние на коррозию в банке и мгновенное ржавление.
ПРИМЕЧАНИЕ: Ингибитор коррозии на основе кальция обеспечивает лучшую совместимость с водой. Он может способствовать диспергированию пигмента при использовании на стадии измельчения пигмента. Хотя некоторые эмульсионные смолы могут быть чувствительны к Ca 2+ .
Ингибиторы / протекторы коррозии длительного действия
Помимо антикоррозионных пигментов , жидкие органические ингибиторы коррозии также обеспечивают долговременную защиту от коррозии с помощью ингибиторов . Жидкие ингибиторы коррозии работают совместно с антикоррозийными пигментами.
Поскольку реакция коррозии представляет собой окислительно-восстановительный химический процесс, сначала можно выбрать требуемый вариант металлического ингибитора коррозии, используя стандартный химический восстановительный потенциал. Эта шкала является первым подходом, поскольку значения основаны на измерениях в водном растворе при 25 ° C, что не является идеальным случаем для всех покрытий!
Тогда выбрать металлический вариант ингибиторов коррозии становится несложно:
- Первым выбором будет ингибитор коррозии на основе бария.
- Для антикоррозионных пигментов на основе цинка: Ингибитор коррозии на основе цинка
- В случае новых и менее токсичных пигментов ингибиторов коррозии: Ингибитор коррозии на основе магния
- Ингибитор коррозии на основе аминов и полимеров для безметалловой альтернативы
При выборе долгосрочного ингибитора коррозии на тип и дозировку агента влияют:
- Тип защищаемого металла
- Эффективность защиты во времени при заданном условии
- Наличие и эффективность антикоррозионных пигментов
- Формулировка глобальной стоимости
- Ограничения по охране окружающей среды, здоровья и труда
Также доступно множество пигментов с их антикоррозийными свойствами.Давайте посмотрим:
Барьерные пигменты
Многие пигменты действуют в основном за счет «пассивной защиты», усиливая барьерный эффект покрытия. Широко используются слюда, алюминий, стеклянные чешуйки и слюдяной оксид железа (MIO). Их эффективность зависит от того факта, что они имеют пластинчатую, чешуйчатую форму и обычно выравниваются более или менее параллельно поверхности покрытия. Это снижает водопроницаемость и ионную проницаемость, заставляя ионы или молекулы воды проходить непрямой путь от поверхности к подложке, как показано на рисунке ниже:
Пластинчатый расширитель (вверху) демонстрирует барьерный эффект, снижающий проникновение влаги,
с частицами, близкими к сферическим (внизу) для сравнения
- Тальк , который обычно классифицируется как «наполнитель», а не как первичный пигмент, также часто встречается в антикоррозионных красках, поскольку он одновременно очень инертен и имеет пластинчатую форму.
- MIO — высокоэффективный антикоррозионный пигмент. В настоящее время существует тенденция смешивать этот материал с неламеллярным MIO, который можно легко получить за десятую часть цены.
- Из других распространенных барьерных пигментов слюда почти полностью инертна.
Алюминиевая чешуйка чувствительна к влаге и щелочам. Хлопья нержавеющей стали находят применение в некоторых случаях, но они относительно дороги. Стеклянные хлопья популярны в толстослойных покрытиях для тяжелых условий эксплуатации.
Пигменты активной защиты
Фосфат цинка занял прочную позицию в качестве активного пигмента в антикоррозионных грунтовках. Считается, что он имеет три защитных механизма:
- Формирование защитной анодной пленки
- Донорство фосфат-иона субстрату
- Образование антикоррозионных комплексов с некоторыми связующими
Модификации фосфата цинка включают, например: фосфат алюминия-цинка, фосфат молибдата цинка и гидрат силикофосфата цинка.
Модифицированные кальцием силикагели представляют собой экологически безопасные ингибиторы коррозии. Пигмент — это не содержащие тяжелых металлов, нетоксичные, микронизированные, аморфные частицы, которые предлагают альтернативу антикоррозионным агентам, не отвечающим требованиям государственных органов. Модифицированный кальцием силикагель является слабощелочным (pH 9-10) и производится посредством реакции ионного обмена на поверхности силикагеля между слабокислотными силанольными группами и гидроксидом кальция. Модифицированный кальцием силикагель представляет собой пористое твердое вещество, имеющее низкую плотность и большую площадь поверхности по сравнению с антикоррозийными пигментами на основе тяжелых металлов.
Следовательно, количество модифицированного кальцием силикагеля, необходимого для обеспечения антикоррозионной защиты, значительно меньше по сравнению с антикоррозийными агентами, содержащими тяжелые металлы. Модифицированный кальцием силикагель защищает металлические поверхности благодаря механизму диффузии ионов кальция и растворимых частиц кремнезема. И развить катодную и анодную площадки и подавить процесс коррозии. Модифицированный кальцием силикагель обычно используется для рулонных покрытий и тонкопленочных покрытий.
Фосфосиликат кальция-стронция — это относительно новый не содержащий цинка антикоррозионный пигмент, который считается более экологически чистым, чем ингибитор коррозии фосфат цинка.Обработка поверхности фосфосиликата кальция-стронция специально разработанными органическими соединениями улучшает смачивание и совместимость с различными составами покрытий. Кроме того, фосфосиликат кальция-стронция также можно использовать в широком спектре воды и Системы покрытий на основе растворителей .
Фосфат алюминия , используемый в качестве антикоррозионного пигмента, представляет собой триполифосфат алюминия (Al 5 P 3 O 10 ). Триполифосфат алюминия считается экологически чистым пигментом и доступен для использования в качестве недорогого антикоррозийного пигмента с середины 1980-х годов.Триполифосфат алюминия может использоваться в широком спектре систем покрытий на основе растворителей, а также в покрытиях на водной основе. Также было обнаружено, что он полезен в термостойких покрытиях.
Перестановки и комбинации
Можно считать, что ряд элементов и соединений обладают некоторым защитным действием от коррозии. И это привело к развитию широкого спектра пигментов, которые, как выясняется при исследовании, содержат один и тот же относительно небольшой набор защитных материалов в различных комбинациях.Можно кратко упомянуть некоторые дополнительные примеры (обязательно неполные):
- Молибдаты эффективны, но дороги, и поэтому обычно встречаются в форме соединений, которые включают другие антикоррозионные элементы, такие как молибдат цинка, молибдат цинка и фосфат молибдата цинка. .
- Триполифосфат алюминия (также доступен в формах, модифицированных ионами цинка или силикатом) — ион триполифосфата способен хелатировать ионы железа в дополнение к защитному эффекту самого фосфата.
- Силикаты могут быть найдены в форме комбинаций, таких как боросиликат кальция, фосфосиликат кальция-бария, фосфосиликат кальция-стронция-цинка, фосфосиликат стронция, фосфосиликат бария.
- Оксиаминофосфатная соль магния продается коммерчески, но рекомендуется только для использования в грунтовках на основе растворителей. Имея относительно низкий удельный вес 2,2, его можно использовать с меньшим весом, чем пигменты на основе цинка.
Проводящие полимеры
По своей природе проводящие полимеры, из которых наиболее широко известен полианилин, представляют собой действительно современную разработку. И среди их многочисленных применений было обнаружено, что они обладают двойным антикоррозийным действием:
- Каталитическая реакция со сталью дает тонкий, плотный слой оксида Fe 2 O 3 , который имеет барьерный эффект, аналогичный тому, который слоя Al 2 O 3 , который образуется естественным образом на алюминии
- Механизм катодной защиты, аналогичный тому, который обеспечивается ингибитором коррозии цинком
Таким образом, полианилин должен находиться в прямом контакте с металлической подложкой, чтобы быть эффективным.Было показано, что он хорошо работает в качестве тонкопленочной предварительной обработки под другими антикоррозийными красками, и был коммерциализирован в виде грунтовок. Утверждается, что эти грунтовки превосходят грунтовки с высоким содержанием цинка при перекрытии эпоксидными смолами и способны защищать поверхность даже тогда, когда повреждение покрытия распространяется до царапины шириной 2 мм.
Кроме того, в патенте заявлено, что этот уровень защиты может быть повышен за счет включения жертвенных анодных частиц металла или металлического сплава вместе с собственно проводящими полимерами, такими как полианилин.Таким образом, в одном покрытии наносятся как барьерная, так и анодная система защиты.
Испытания ингибиторов коррозии
Для получения лучших результатов следует тестировать разные ингибиторы коррозии, используемые в разных дозировках. Конечно, стойкость и свойства краски не должны изменяться при использовании этого ингибитора коррозии.

Обычно до 3,0 — 4,0% от общей рецептуры
Жидкие ингибиторы коррозии работают совместно с антикоррозийными пигментами.Они также улучшают долговременную коррозионную стойкость.
Чтобы обеспечить наилучшие характеристики, они должны быть идеально диспергированы:
- Предпочтительно добавлять на стадии диспергирования пигмента для обеспечения идеальной гомогенизации. В случае последующего добавления требуется достаточное перемешивание.
- На водной основе может потребоваться предварительная смесь с нейтрализующим амином и / или коалесцирующим растворителем.
Что касается основания, подготовка поверхности и особенно смачивание и адгезия жидкой краски имеют решающее значение.Загрязненная, грязная и пористая поверхность увеличивает чувствительность к коррозии. Шероховатая поверхность после шлифовки улучшит адгезию краски.
Для проведения лабораторных испытаний настоятельно рекомендуется использовать несколько стандартизированных панелей
для испытаний на коррозию.
После приготовления состава и полного отверждения краска должна быть испытана с использованием другого метода коррозии, например:
Циклические испытания
- Циклические испытания QUV
- Конденсация QUV (ASTM G154)
- Цикл-УФ-свет * -4 часа с последующим циклом конденсации-4 часа
- Цикл-камера конденсации поддерживает 100% относительной влажности, 50 ° C * Люминесцентные УФ-лампы
- QUV Prohesion (ASTM G85 A5)
- Цикл, воздействие панелей во влажный / сухой периоды
- Циклическое испытание на коррозию, состоящее из одной недели в QUV и одной недели в цикле износостойкости *
- УФ облучение
* Цикл протезирования — образцы, подвергшиеся воздействию раствора электролита (0.05% NaCl + 0,35% сульфата аммония) при 35 ° C в течение одного часа, затем сушат при 40 ° C в течение одного часа, цикл повторяется - Конденсация QUV (ASTM G154)
- Xenon Arc Exposure (ASTM D2568, G26)
Имитирует полный спектр солнечного излучения — УФ, видимое и инфракрасное излучение.
Статические испытания
- Испытание в солевом тумане (ASTM B-117)
5% раствор хлорида натрия распыляется с помощью сопла в закрытую камеру для создания статического тумана. Панели подвешиваются в нем на установленный период времени.Температура поддерживается постоянной (95 ° F). Слабая корреляция с ожидаемым сроком службы покрытия. - Испытание на контролируемую влажность (ASTM D2247)
Оценивает влияние влаги на коррозию. Образцы подвергаются воздействию относительной влажности 100%. - Испытание на погружение (ASTM D870)
Образцы погружают в ванну с деионизированной водой при 100 ° F. - Спектроскопия электрохимического импеданса (EIS)
Сигнал малой амплитуды подается на ранее погруженную панель с краской в диапазоне частот.EIS измеряет разрушение покрытия из-за воздействия электролита. Оценка скорости коррозии (от 30 минут до 24 часов после погружения) выполняется быстро. - Испытание на нитевидную коррозию (ASTM D2803)
Панели с разметкой, помещенные в коррозионную атмосферу (солевой туман на 4-24 часа) или погруженные в солевой раствор Панели, подверженные воздействию влажности (77oF и относительная влажность 85%)
Другие методы тестирования
- Внешний вид
- Тест на влажность (ASTM D2247)
Могут быть выполнены другие испытания на коррозию, такие как ускоренное атмосферное воздействие с использованием определенных приборов или специальные испытания на распыление, чтобы воспроизвести состояние загрязненной атмосферы.
Цель достигается, когда уровень коррозии ниже предельного уровня по прошествии необходимого времени
Антикоррозионные преимущества органических-неорганических гибридных покрытий
Термин « гибридных покрытий » правильно используется в связи со многими различными системами, в которых присутствуют две (или более) системы связующих с различными свойствами и механизмами отверждения.

Некоторые из наиболее часто используемых гибридных покрытий включают:
- Силикатные покрытия с высоким содержанием цинка
- Эпоксидно-силоксановые гибридные покрытия
- Золь-гель покрытие
Покрытия с высоким содержанием цинка — Классическим примером являются силикатные покрытия с высоким содержанием цинка, содержащие небольшие количества органических связующих материалов (в частности, алкилсиликатного типа).Эта форма гибридного покрытия используется для обеспечения превосходной защиты от коррозии.
Органосилоксановые покрытия для тяжелых условий эксплуатации — Было обнаружено, что гибридные эпоксидно-силоксановые гибридные покрытия обеспечивают лучшую внешнюю долговечность, чем даже двухкомпонентные полиуретановые покрытия. Связующие могут иметь очень низкую вязкость, что позволяет наносить покрытия с содержанием летучих органических соединений около 120 г / л и толщиной пленки до 200 мкм. Они также обладают высокой устойчивостью к граффити, инертны к большинству ядерных излучений, огнестойки и устойчивы к коррозии.
Золь-гелевые покрытия — Золь-гелевые покрытия из модифицированного уретаном полисилоксана обладают отличной адгезией к металлам, таким как алюминий. Кроме того, они эффективно противостоят химическому воздействию за счет образования плотно упакованной сшитой сети. Было обнаружено, что они полезны в качестве защитных покрытий на таких элементах, как теплообменники, которые имеют множество плотно упакованных металлических «ребер», на которые трудно нанести покрытие, и для которых желательны небольшие пленки.
Ингибиторы коррозии для покрытий, имеющиеся в продаже
Типы антикоррозионных покрытий и их применение
ВведениеВ этой главе рассматриваются основные типы покрытий, которые в настоящее время доступны для использования, и содержится общая информация о составе покрытий.Он предназначен для предоставления основной информации о покрытиях и не является исчерпывающим руководством по выбору антикоррозионных покрытий. Если требуется информация о конкретном продукте или покрытиях, подходящих для определенных областей, следует проконсультироваться с производителем покрытия.
Покрытия часто делятся на две большие категории:
1) продукты для применения в новостройках и;
2) продукты, подходящие для технического обслуживания и ремонта, которые будут включать как капитальный ремонт, так и обслуживание на борту (OBM).
Типы антикоррозионных покрытий, используемых для OBM, часто представляют собой однокомпонентные продукты, поскольку это позволяет избежать трудностей с измерением и смешиванием небольших количеств продуктов из двух упаковок, хотя небольшие количества продуктов из двух упаковок иногда доступны от производителей красок. Ремонт, проводимый экипажем находящихся в эксплуатации судов, редко бывает успешным в долгосрочной перспективе из-за трудностей подготовки поверхностей к достаточно высоким стандартам.
Как правило, краски предназначены либо для определенных участков резервуаров и для определенных функций для достижения наилучших характеристик, либо для всех областей доступны универсальные покрытия с минимальными эксплуатационными характеристиками.Во всех случаях необходимо соблюдать баланс между стоимостью, производительностью и сложностью обслуживания. Например, антикоррозионные покрытия, используемые на внешней стороне жилого помещения, имеют другие требования к характеристикам, чем антикоррозионные краски, используемые в балластных цистернах морской воды, поскольку коррозионное напряжение, оказываемое на последние, намного выше. Балластные цистерны также намного труднее обслуживать из-за трудностей доступа, и поэтому использование высокоэффективного (и часто более дорогого) покрытия является предпочтительным для поддержания стали в хорошем состоянии.
Напротив, трюмы навалочных судов страдают от истирания из-за удара груза и повреждения грейфером, что часто приводит к коррозии. Грузовые трюмы, используемые в качестве балластных цистерн в ненастную погоду, могут быть особенно подвержены коррозии в местах повреждения, и для этого грузового трюма иногда используется другое покрытие. Это также относится к грузовым танкам для нефтеналивных судов с обозначением класса «Чистые продукты», где любой грузовой танк может использоваться для тяжелого погодного балласта.
Состав краски
Краска может быть описана как жидкий материал, который можно наносить или растекать по твердой поверхности, на которой он впоследствии высыхает или затвердевает, образуя сплошную липкую пленку.Краски в основном состоят из трех основных компонентов и множества добавок, которые включены в незначительных количествах. Основными компонентами являются:
• Связующее (также называемое наполнителем, средой, смолой, пленкой или полимером)
• Пигмент и наполнитель
• Растворитель
Из них , только первые два образуют окончательную сухую пленку краски. Растворитель необходим только для облегчения нанесения краски и начального образования пленки, но неизбежно, что на практике всегда остается некоторое количество растворителя в зависимости от уровня вентиляции.
Связующие Связующие — это пленкообразующие компоненты краски, которые определяют основные характеристики покрытия, как физические, так и химические. Краски обычно называются по их связующему компоненту (например, эпоксидные краски, краски на основе хлорированного каучука, алкидные краски и т. Д.). Связующее образует прочную непрерывную пленку, которая отвечает за адгезию к поверхности и способствует общей стойкости покрытия к окружающей среде.Связующие, используемые при производстве красок, делятся на два класса: термореактивные и термопластичные. После высыхания термореактивное покрытие будет отличаться по химическому составу от краски в банке. После отверждения термоотверждаемые покрытия не подвержены воздействию растворителей.
В случае термопластичного покрытия сухая пленка и влажная краска отличаются только содержанием растворителя и химически, они остаются практически одинаковыми. Если первоначально использованный растворитель наносится на термопластичное покрытие, оно размягчается и может быть повторно растворено в этом растворителе.
Сшитые (термореактивные) покрытияЭти покрытия обычно поставляются в двух отдельных упаковках, которые смешиваются вместе непосредственно перед нанесением. В жидких красках, содержащих растворитель, сушка считается двухэтапным процессом. Обе стадии на самом деле происходят вместе, но с разной скоростью.
Первый этап: растворитель уходит из пленки в результате испарения, и пленка становится сухой на ощупь. Этап 2: Пленка постепенно становится более химически сложной с помощью одного из следующих четырех методов:1) Реакция с кислородом воздуха, известная как окисление.
2) Реакция с добавлением химического отвердителя.
3) Реакция с водой (влажность в атмосфере).
4) Искусственное отопление.
Это преобразование краски известно как высыхание или отверждение. Пленки, сформированные указанными выше способами, химически отличаются от исходных связующих и не будут повторно растворяться в исходном растворителе.
Эпоксидные смолы Эти смолы особенно важны, и их разработка для использования в качестве связующих была одним из самых значительных достижений в технологии антикоррозионных покрытий. Скорость сшивания или отверждения зависит от температуры. При температуре ниже 5 ° C скорость отверждения стандартных эпоксидных смол значительно снижается, и для получения оптимальных свойств пленки необходимо полное отверждение. Эпоксидные смолы со специальными отвердителями затвердевают или затвердевают при температуре до –5 ° C. Важно строго соблюдать рекомендации производителя покрытия по температуре нанесения, чтобы покрытия были эффективными в эксплуатации.
Выбор отвердителя очень важен, так как в случае основы он определяет свойства пленки.Существует широкий выбор как смол, так и отвердителей, что позволяет создавать продукты, подходящие для большинства областей применения. Эпоксидные смолы используются как под водой, так и над водой и демонстрируют хорошую стойкость ко многим морским средам, включая катодную защиту с использованием цинка или других анодов, но они имеют тенденцию к мелу на солнечном свете. Этот процесс происходит, когда связующее разрушается ультрафиолетовым светом с образованием рыхлой и рыхлой поверхности с частицами пигмента, остающимися на поверхности.
Полиуретановые смолыЭто полимеры, образующиеся в результате реакции между гидроксильными соединениями и соединениями, содержащими изоцианаты. В двухкомпонентных системах специальная полиэфирная или полиэфирная смола со свободными гидроксильными группами взаимодействует с высокомолекулярным изоцианатным отвердителем. Возможная проблема с этими материалами заключается в их чувствительности к воде при хранении и применении. Транспортировка и хранение должны осуществляться в строгом соответствии с рекомендациями производителей.Из-за их плохих свойств отверждения при низких температурах при нанесении необходимо соблюдать рекомендации производителя.
Полиуретановые смолы обладают превосходной химической стойкостью и стойкостью к растворителям и превосходят стандартные эпоксидные смолы по кислотостойкости. Эпоксидные смолы более устойчивы к щелочам, чем полиуретаны. Финишные покрытия из полиуретана очень твердые, обладают очень хорошим блеском, сохраняют блеск и могут не желтеть. Однако в некоторых случаях на них может быть трудно нанести следующий слой после старения, и для достижения оптимальной адгезии требуются очень чистые поверхности.Изоцианатный отвердитель также представляет потенциальную опасность для здоровья при распылении, которую можно преодолеть с помощью соответствующих средств защиты.
Эти типы включают силикаты, которые почти всегда используются вместе с цинковой пылью. Существуют неорганические силикаты на водной основе на основе силиката лития, калия или натрия и неорганические силикаты на основе растворителей, обычно основанные на этилсиликате.Покрытия на основе этих смол очень твердые, коррозионно-стойкие и термостойкие. Они требуют хорошей подготовки поверхности и часто ремонтируются с использованием органических покрытий. Цинк в неорганических смолах может растворяться в кислотных или щелочных условиях, но покрытия хорошо работают при нейтральном pH и часто используются в качестве покрытий для резервуаров.
Термопластические покрытия Эти типы связующих для красок представляют собой простые растворы различных смол или полимеров, растворенных в подходящих растворителях, и обычно поставляются в виде одной упаковки, что делает их особенно подходящими для работ по техническому обслуживанию. Сушка происходит просто за счет потери растворителя при испарении. Это называется физической сушкой, поскольку никаких химических изменений не происходит. Таким образом, полученная пленка всегда легко растворяется в исходном растворителе, а также может размягчаться при нагревании. Поскольку эти покрытия по определению требуют присутствия значительных количеств растворителя, они исчезают с рынков, где регулируется содержание летучих органических соединений, особенно в США и ЕС. Общие типы связующих в этой категории включают:
Хлорированные каучуковые смолы обладают хорошей кислотостойкостью и водостойкостью на хорошо подготовленных поверхностях.Их температурная чувствительность может привести к различным дефектам пленки при использовании в очень жарком климате. Кроме того, белые и бледные цвета имеют ярко выраженную тенденцию к желтизне при воздействии яркого солнечного света. Краски на основе хлорированного каучука высыхают при низких температурах и обеспечивают хорошую межслойную адгезию как в свеженанесенных, так и в старых системах, что делает их пригодными для технического обслуживания.
Виниловые смолыВиниловые смолы основаны на пленкообразующих полимерах, состоящих из поливинилхлорида, поливинилацетата и поливинилового спирта в различных соотношениях.Используемые типы пластификаторов — трикрезилфосфат или диоктилфталат. Твердые материалы большего объема могут быть получены путем смешивания виниловой смолы с другими материалами, такими как акриловые смолы. Обычно свойства пленки и погодоустойчивые характеристики также показывают хорошие характеристики низкотемпературной сушки и межслойной адгезии. Каменноугольная смола может быть добавлена для повышения водостойкости.
Пигменты и наполнители Пигменты и наполнители используются в красках в виде тонких порошков.Они диспергированы в связующем до размеров частиц примерно 5-10 микрон для отделочных красок и примерно 50 микрон для грунтовок.
Металлический цинк широко используется в грунтовках, придающих коррозионную стойкость стали. Первоначальная защита осуществляется гальваническим воздействием. Однако, когда покрытие подвергается воздействию атмосферы, происходит прогрессирующее накопление продуктов коррозии цинка, в результате чего образуется непроницаемый барьер с небольшой гальванической защитой или без нее.Для обеспечения хорошей гальванической и барьерной защиты требуется высокий уровень цинка, около 85% цинка в сухой пленке по весу. В качестве смол можно рассматривать эпоксидные смолы и силикаты. Очевидно, что для правильного функционирования цинк должен находиться в тесном контакте со стальной подложкой, и поэтому важна хорошая чистота поверхности перед нанесением.
(2) Алюминиевые пигментыМеталлические алюминиевые чешуйки обычно используются в качестве антикоррозийного пигмента и действуют как антикоррозийные средства, создавая обходной путь для воды и ионов вокруг пластинчатых чешуек, а также поглощая кислород для дают оксиды алюминия, которые блокируют поры в покрытии.Там, где алюминий находится в контакте со сталью, также будет работать ограниченный механизм катодной защиты, хотя при использовании на цистернах и продуктовозах содержание алюминия в сухой пленке не должно превышать 10 процентов, чтобы избежать возможной опасности искры при скоплении горючих газов.
(3) Фосфат цинкаЭто также широко используемый антикоррозионный пигмент, и считается, что при нормальных условиях воздействия защита обеспечивается за счет барьерного эффекта, поскольку для обеспечения адекватной защиты от коррозии необходимы высокие уровни пигментации. защита.Фосфат цинка может быть включен практически в любое связующее, и из-за его низкой непрозрачности или прозрачности можно производить краски любого цвета.
Барьерные пигменты Наиболее распространенными типами этих пигментов являются алюминий (листовой алюминий) и слюдяной оксид железа (MIO). Оба имеют форму частиц, которые называются пластинчатыми (пластинчатыми). Эти материалы можно использовать в сочетании, при этом алюминий осветляет почти черный оттенок MIO. Пигментированные пленки MIO обладают долговечностью, но для этого необходимы высокие уровни MIO, порядка 80% от общего пигмента.Алюминий уже много лет используется в качестве основного пигмента в красках. Пластинчатая форма делает пленку более водонепроницаемой. Стеклянные хлопья также используются в качестве барьерного пигмента.
Как следует из названия, они в основном регулируют или «расширяют» пигментацию краски до тех пор, пока не будет достигнута требуемая объемная концентрация пигмента (PVC). Пигменты-наполнители представляют собой неорганические порошки с различными формами и размерами частиц.Хотя они вносят незначительный вклад в непрозрачность цвета краски или не вносят ее вообще, они могут оказывать значительное влияние на физические свойства. К ним относятся текучесть, степень блеска, противоосадочные свойства, способность к распылению, водо- и химическая стойкость, механическая прочность, твердость и твердость (твердый объем, задерживающая тиксотропия). Смеси наполнителей часто используются для получения желаемых свойств. Они относительно недороги по сравнению со смолами, антикоррозийными пигментами и красящими пигментами.
Растворители используются в красках в основном для облегчения нанесения. Их функция заключается в растворении связующего и снижении вязкости краски до уровня, подходящего для различных методов нанесения, таких как кисть, валик, обычное распыление, безвоздушное распыление и т. Д. После нанесения растворитель испаряется и не играет никакой роли. Дальнейшая часть в финальной лакокрасочной пленке. Жидкости, используемые в качестве растворителей в красках, можно описать одним из трех способов:
(1) Настоящие растворители — жидкость, которая растворяет связующее и полностью с ним совместима.
(2) Скрытый растворитель — жидкость, которая не является настоящим растворителем. Однако при смешивании с настоящим растворителем смесь обладает более сильными растворяющими свойствами, чем один настоящий растворитель.
(3) Растворитель-разбавитель — жидкость, которая не является настоящим растворителем. Обычно используется в качестве смеси с истинным растворителем / смесями скрытого растворителя для снижения стоимости.
Связующие допускают только ограниченное количество разбавителя. В лакокрасочной промышленности используется множество растворителей, отчасти это связано с рядом различных свойств, которые необходимо учитывать при выборе растворителя или смеси растворителей.Помимо коммерческих факторов, таких как цена и доступность, свойства включают токсичность, летучесть, воспламеняемость, запах, совместимость и пригодность. В некоторых странах использование некоторых типов растворителей запрещено. Это особенно верно в США, где Закон об опасных веществах, загрязняющих воздух (HAPS) определяет сроки удаления многих растворителей и наполнителей с покрытий. При реализации этого закона, скорее всего, будут затронуты свойства нанесения, время высыхания и окна перекрытия.
Антикоррозийные краски За некоторыми исключениями (например, противообрастающие краски, косметические эффекты, антипирены и т. Д.), Большинство покрытий, наносимых на сосуд, используется для защиты от коррозии. Существует много типов антикоррозионных покрытий, но эпоксидные краски обычно покрывают большую часть судна, особенно когда они используются в балластных цистернах морской воды. В последние годы ведутся споры о терминологии, используемой для эпоксидных покрытий, и обычно используются следующие термины:
(1) Чистая эпоксидная смола
Чистые эпоксидные покрытия обычно рассматриваются как краски, содержащие только эпоксидные полимеры, сшивающий агент, пигменты, наполнители и растворители.Покрытия содержат большое количество эпоксидного связующего, и поэтому ожидается, что они обеспечат максимально возможные характеристики покрытия с точки зрения защиты от коррозии, длительного срока службы и низких эксплуатационных расходов. Кроме того, некоторые продукты также обладают устойчивостью к истиранию. К чистым эпоксидным покрытиям могут быть добавлены другие пигменты, такие как алюминий, для обеспечения дополнительных антикоррозионных свойств. Эпоксидно-фенольные покрытия могут использоваться в грузовых танках, где требуется высокий уровень дополнительной устойчивости груза, например, на нефтепродуктах и химовозах.Особая осторожность требует подготовки поверхности; может потребоваться отверждение покрытия путем нагревания резервуаров. Производители покрытий сообщат конкретные требования для каждого резервуара.
(2) Модифицированная эпоксидная смола
Эта группа, также известная как эпоксидная мастика, не содержащая смол эпоксидная смола и отбеленная эпоксидная смола, охватывает широкий спектр продуктов и обеспечивает антикоррозионные свойства. В эксплуатации могут быть эффективны модифицированные эпоксидные смолы. Однако, поскольку существует множество возможных модифицированных составов эпоксидных смол, невозможно сделать обобщения об их антикоррозионных характеристиках.Модифицированные эпоксидные смолы могут содержать неэпоксидные материалы, которые способны образовывать поперечные связи в конечную пленку. Они также могут содержать инертные материалы, твердые или жидкие, которые не участвуют в образовании пленки, но остаются как пигменты или наполнители в конечном покрытии. Если эти материалы растворимы в воде (или в грузе), они могут выщелачиваться в течение длительного периода времени, оставляя пористую или хрупкую пленку с пониженными антикоррозийными свойствами.
(3) Каменноугольная смола эпоксидная
Каменноугольная смола является продуктом природного происхождения.Угольные гудроны доступны в широком диапазоне типов от жидких до твердых. Включение каменноугольных смол в покрытие приводит к очень темно-коричневому или черному цвету покрытия, который можно немного осветлить, добавив пигмент в виде чешуек алюминия для более светлых красок. Однако маловероятно, что эпоксидные смолы из каменноугольной смолы будут достаточно светлыми для использования в соответствии с требованиями IMO PSPC 4.4, таблица 1, пункт 1.2, для окончательного покрытия. Светлый верхний слой из эпоксидной смолы без содержания смолы может быть использован поверх первого слоя на основе смолы.Однако «просачивание» смолы может обесцветить верхнее покрытие. Некоторые компоненты покрытия могут вымываться в течение длительного времени, в результате чего покрытие становится более хрупким и менее защищенным. Эпоксидные смолы каменноугольной смолы имеют долгую историю эксплуатации и в целом хорошо себя зарекомендовали. С 1990-х годов они были выведены из эксплуатации в балластных цистернах из-за проблем со здоровьем и безопасностью нанесения покрытий, а также из-за рекомендаций по нанесению светлых покрытий для облегчения осмотра балластных цистерн.
(4) Эпоксидная смола, не содержащая растворителей
Краски, не содержащие растворителей (иногда называемые 100% -ными твердыми частицами), как следует из названия, формулируются и наносятся без необходимости в дополнительных растворителях, тем самым преодолевая проблемы остатки растворителей в покрытии. Вязкость, необходимая для распыления краски, получается путем выбора низкомолекулярного сырья или путем нагревания и использования многокомпонентных систем. Типичные области применения включают балластные и грузовые танки. Иногда они используются там, где удаление летучих органических компонентов (ЛОС) затруднено из-за плохой вентиляции, хотя следует отметить, что ЛОС для систем без растворителей не обязательно равен нулю. Типичные области применения покрытий, не содержащих растворителей, включают внутреннюю часть трубопроводов, некоторые резервуары и другие области, где не может быть обеспечена соответствующая вентиляция, или для областей, где действуют строгие меры контроля ЛОС.
ECO Friendly Corrosion Control — Texas Technologies, Packaging Solutions
Для простоты применения и повышения экологической безопасности компания Cortec упаковала CLP на основе EcoAir Biobased в аэрозольный баллончик с пневматическим приводом, который распределяет смазочный материал без использования легковоспламеняющихся или озоноразрушающих пропеллентов.
EcoAir Biobased CLP содержит 89% биосодержащих веществ, сертифицированных USDA, и обеспечивает отличное проникновение, смазывание и предотвращение ржавчины для промышленного, торгового и домашнего использования!
Продукты CLP (очистка, смазка, защита) традиционно изготавливаются из опасных минеральных масел и других растворителей на нефтяной основе. EcoAir® Biobased CLP от Cortec предлагает отличную экологически чистую альтернативу в виде EcoAir® Biobased CLP, продукта на биологической основе в аэрозольном баллончике с пневматическим приводом.
Используя основу масла канолы, EcoAir® Biobased CLP содержит 89% биологических компонентов, сертифицированных Министерством сельского хозяйства США.Он обеспечивает отличную проникающую способность, смазку и предотвращает ржавчину при промышленном, производственном и бытовом использовании. Его можно использовать для многих функций, таких как откручивание ржавых деталей и защита компонентов оборудования от износа и коррозии.
EcoAir® Biobased CLP оставляет после себя очень стойкий слой, устойчивый к коррозии до 24 месяцев. При необходимости слой легко удалить обычными моющими средствами.
Для простоты применения и дополнительной экологичности Cortec® упаковал свою жидкость CLP на биологической основе в аэрозольный баллончик с пневматическим приводом, который распределяет смазочный материал без использования легковоспламеняющихся или озоноразрушающих пропеллентов.EcoAir® Biobased CLP можно распылять в любом направлении, даже в перевернутом виде. После того, как продукт будет полностью разлит, пустая банка может быть переработана. *
EcoAir® Biobased CLP имеет множество практических применений для MRO (техническое обслуживание, ремонт и эксплуатация) в магазине или дома, чтобы выполнять его чистку, смазку и защиту функции:
- Очистка — Разбавляет и удаляет грязь и сажу
- Смазывает
- Работает как отличный пенетрант и смазка
- Ослабляет замерзшие и ржавые болты и другие компоненты
- Продлевает срок службы деталей машины за счет снижения трения и износа
- Защищает — Обеспечивает защиту от коррозии нескольких металлов.
EcoAir® Biobased CLP можно распылять на углеродистую сталь, оцинкованную сталь, нержавеющую сталь, алюминий и алюминиевые сплавы.Типичные области применения:
- Механическая обработка на заводе
- Смазка прутка и цепи
- Смазка фланца
- Обслуживание замков и шарниров
- Освобождение пресс-формы
EcoAir® Biobased CLP устойчив к замерзанию и поставляется в упаковке 10 унций нетто ( 284 г) перерабатываемых стальных банок, по 12 банок в картонной коробке. Срок годности 24 месяца.
Предотвращение коррозии в системах жидкостного охлаждения
Возможные проблемы с коррозией
Коррозия может вызвать множество проблем, наиболее серьезной из которых является перфорация, которая может привести к утечке охлаждающей жидкости.Другие проблемы могут включать снижение теплопередачи, вызванное отложением на поверхности, которое происходит, когда металл реагирует с кислородом, хлоридом и / или ингибиторами в хладагенте и осаждается обратно на поверхность металла, создавая слой, который действует как барьер для теплопередачи. Кроме того, проблемы включают засорение сажевых фильтров и повреждение механических уплотнений.
Когда медь корродирует, она чаще разрушается из-за общей коррозии, чем из-за точечной коррозии. Общая коррозия часто поражает медь под воздействием аммиака, кислорода или жидкостей с высоким содержанием серы.Другой источник коррозии, влияющей на медь, — растворенные соли в жидкости, такие как хлориды, сульфаты и бикарбонаты.
Для алюминия точечная коррозия является наиболее распространенной формой коррозии. Точечная коррозия обычно вызывается присутствием галогенид-ионов, из которых хлорид (Cl-) наиболее часто встречается в контурах жидкостного охлаждения. Точечная коррозия алюминия в растворах галогенидов, открытых для воздуха, происходит потому, что в присутствии кислорода металл легко поляризуется до своего питтингового потенциала, и происходит проникновение естественного защитного оксидного слоя или пленки.Эта пленка устойчива в водных растворах при pH от 4,0 до 8,5. Пленка является самообновляющейся, и случайное истирание или другое механическое повреждение поверхностной оксидной пленки быстро восстанавливается. Aavid настоятельно рекомендует использовать ингибитор при использовании воды с алюминием для поддержания чистой поверхности теплопередачи.
Нержавеющая сталь обычно используется в агрессивных средах, но, как и алюминий, она чувствительна к высоким концентрациям хлоридов (> 100 ppm) в окислительной среде. Точечная коррозия остается одной из наиболее распространенных и разрушительных форм коррозии в сплавах нержавеющей стали, но ее можно предотвратить, обеспечив контакт материала с кислородом и защиту от хлоридов там, где это возможно. Нержавеющие стали с высоким содержанием хрома, особенно молибдена и азота, более устойчивы к точечной коррозии.
Исследование синтеза и трибологических свойств антикоррозионной бензотриазольной ионной жидкости
Антикоррозионная бензотриазольная ионная жидкость (IL, BTAP 4444 ) была синтезирована нейтрализацией 1H-бензотриазола (BTAH) гидроксидом терабутилфосфония (P 4444 OH).Были измерены физико-химические и трибологические свойства BTAP 4444 , и результаты показали, что он обладает хорошими смазочными свойствами для пар трения сталь / сталь, сталь / медь и сталь / алюминий в плане снижения коэффициента трения и объема износа, особенно когда он работали для пары трения сталь / медь как при комнатной температуре (RT), так и при 100 ° C. Хорошие характеристики были также обнаружены с точки зрения его антикоррозионной способности, термической и гидролизной стабильности и вязкостно-температурных характеристик по сравнению с коммерчески доступным синтетическим маслом поли-альфа-олефином (PAO 10) и традиционным тетрафторборатом IL-1-бутил-3-метилимидазолия. (bmimBF 4 ).Целью разработки BTAP 4444 является повышение антикоррозийной способности смазки IL, связанной с введением азотной гетероциклической структуры, 1H-бензотриазола, который обычно используется в качестве антикоррозионного ингибитора коррозии в машиностроении. Результаты коррозионных испытаний подтверждают наше предположение, а BTAP 4444 демонстрирует превосходную антикоррозионную способность для всех используемых пар трения, включая контакты сталь / сталь, сталь / медь и сталь / алюминий.
Эта статья в открытом доступе
Подождите, пока мы загрузим ваш контент… Что-то пошло не так. Попробуй еще раз?Антифриз и антикоррозионная жидкость WATERDOS FKN-28 5 кг для систем отопления и солнечных батарей
Защита от замерзания и коррозии для закрытых систем центрального отопления, охлаждения и солнечных систем
Цель использования WATERDOS FKN-28
Waterdos FKN 28 имеет проверенная формула защиты от замерзания и коррозии для замкнутых водяных систем центрального отопления, отвечающая требованиям VDI 2035.Он также идеально подходит для контуров охлаждения, солнечных коллекторов и тепловых насосов. Waterdos FKN 28 содержит компоненты, стабилизирующие жесткость и очищающие (диспергаторы) жидкости.
Преимущества антифриза и антикоррозионной жидкости WATERDOS FKN-28
- эффективная антикоррозионная защита чугуна, чугуна, чугуна, меди, алюминиево-медного сплава, припоя за счет создания защитного слоя на поверхности металлическая поверхность, как в однородных, так и в смешанных системах по используемым материалам.
- содержит анодные и катодные ингибиторы, замедляющие химические реакции окисления.
- очень хорошие буферные свойства (допустимый диапазон 7,0-8,5 pH)
- диспергирование коррозионных частиц, позволяющее поддерживать чистоту поверхности оборудования и сама жидкость
- , стабилизирующая жесткость воды (исключающая отложение кальция)
- Отсутствие гидразина и нитратов, что более экологично
- нейтрально к применяемым уплотнениям (EPDM, NBR, PB, PP, PTFE, VPE, гидравлический пенька, бутилкаучук, полиакрилат и поликарбонат)
WATERDOS FKN-28 свойства антифриза и антикоррозийной жидкости
Waterdos FKN-28 — жидкость желтого цвета с плотностью 1. 12 ± 0,03 г / см3 (при температуре 20 ° C) и pH (1%) 8,6 ± 0,2 и температуре замерзания -150 ° C
WATERDOS FKN-28 для замены антифриза и антикоррозийной жидкости и дозировка
Дозировка Waterdos FKN 28 зависит от качества воды на входе и требуемой защиты от замерзания. Обычно дозировка составляет 20-50% от емкости устройства (см. Таблицу). Дозирование происходит вручную с помощью входной заслонки, ручного насоса или электронасоса (по возможности перед циркуляционным насосом системы).
Перемешивание жидкости зависит от используемого в системе гидравлического оборудования и может занять до 14 дней. Для эффективного и беспроблемного использования, по крайней мере, один раз в год, перед сохранением антифриза и антикоррозионных свойств необходимо проверять содержание смешанной жидкости на предмет уровней pH, плотности и содержания ингибитора. В случае отклонения от необходимого значения необходимость заполнения зазоров жидкости в системе обязательна. Если используется более крупная замкнутая система или промышленные системы, рекомендуется проконсультироваться с инженерами.
Объем [%] | Вес FSK [%] | Плотность [г / см3] | Защита [° C] |
1,03 | -10 | ||
25 | 30 | 1,04 | -14 |
30 | 33,5 | 1,04 | -18 |
35 | 39 | 1,05 | -22 при более низкой температуре.разрыв не происходит |
40 | 44,5 | 1,06 | -27 при более низкой температуре. разрыв не происходит |
45 | 50 | 1,06 | -33 при более низкой температуре. разрыв не происходит |
50 | 55,5 | 1,07 | -40 при более низкой температуре. разрыв не происходит |
* Значения приведены для подготовки Waterdos FKN-28 плотностью — 1115 г / см3 при 20 ° C.![]() |
Советы по установке WATERDOS FKN-28
Не всегда можно избежать кондиционирования, щелевой коррозии и эрозии. По причинам химической коррозии максимальная концентрация жидкого концентрата не может превышать 20%.
Прямой контакт меди с алюминием не допускается.
При замене среды установки с воды и антифриза на воду следует обратить внимание на полное удаление антифриза (смыть).В противном случае существует опасность разложения остатков органических кислот и их коррозионного действия. Также следует применять ингибитор Waterdos и, по крайней мере, в течение одного года проводить измерение содержания воды для определения pH и наличия ингибитора.
Когда pH падает ниже 7, обычная практика заключается в промывке системы ингибитором Passivator NEU 04 с последующим повторным наполнением.
Предел WATERDOS FKN-28 составляет прибл. Концентрация смеси воды 68%, что соответствует заданной температуре замерзания прибл.-68 ° С.
Сравнение 5 коррозионно-стойких металлических покрытий
Легкие металлы стали популярным выбором во многих отраслях промышленности. Такие металлы, как алюминий, титан и теперь даже магний, стали жизненно важными для автомобильной, аэрокосмической и многих других областей применения. Сочетание их изобилия, исключительного отношения прочности к весу и универсальности означает, что они являются предпочтительным выбором для инженеров по всему миру.
Некоторые легкие сплавы обладают превосходной коррозионной стойкостью даже в необработанном виде, но неизбежно потребуется обработка поверхности готового продукта для обеспечения рабочих характеристик, долговечности и качества.Магний известен своей плохой коррозионной стойкостью, но менее известно то, что некоторые алюминиевые сплавы, такие как 2xxx, 7xxx и другие высокопрочные семейства, содержащие медь или другие переходные металлы, также подвержены такой же чувствительности.
Выбор правильного метода защиты от коррозии важен для успешного проектирования и производства компонентов. Каждый метод имеет уникальный набор преимуществ и потенциальных проблем. Мы собрали это сравнение различных методов лечения, чтобы помочь вам найти наиболее подходящее решение для ваших нужд.
1. Анодирование
Анодирование — самый популярный метод улучшения коррозионной стойкости алюминия. Вообще говоря, он включает в себя четырехэтапный процесс для достижения защиты.
Первый этап включает погружение материала в ванну с проводящим раствором — обычно кислотную ванну с низким pH — и подключение сплава к аноду электрической цепи. При подаче электрического тока на поверхности металла происходит реакция окисления:
2Al (S) + 6OH — (водн.) — 6e — Al 2 O 3 (s) + 3H 2 O (l)
Это вызывает утолщение естественного оксида на поверхности металла, создавая защитный внешний слой оксида алюминия.Толщина покрытия может быть изменена за счет увеличения времени нанесения покрытия, что обеспечивает широкий спектр применения:
- При легком нанесении может обеспечить хорошую предварительную обработку для окраски или
последующих покрытий - При окрашивании можно получить особые цветовые эффекты.
- При нанесении тонким слоем (обычно <20 мкм) он является полупрозрачным, что
сохраняет металлический эстетический вид, при желании
Выбор толщины покрытия играет ключевую роль в определении коррозионной стойкости.В наружных условиях или при интенсивном внутреннем стрессе (например, при постоянном контакте с жидкостью) рекомендуется минимум 20 мкм. Если для слоев требуется толщина 10 мкм, более высокое напряжение может повредить материал, растрескивая защитный оксидный слой и становясь пористым.
Кроме того, механизм роста и столбчатая микроструктура вызывают растрескивание по всей толщине в углах, что ограничивает защиту кромок, обеспечиваемую слоями анодирования. Уплотнения с горячей водой могут использоваться для обеспечения более надежной защиты, но более эффективные уплотнения могут быть достигнуты за счет использования опасных химических растворов, таких как ацетат никеля или бихромат натрия.
В конечном счете, для материалов, требующих определенных эстетических качеств, при сохранении высокой устойчивости к коррозии при контакте с жидкостями, анодирование — не лучший метод повышения коррозионной стойкости.
2. ПЭО
Плазменное электролитическое окисление (ПЭО) включает использование плазменных разрядов для преобразования металлической поверхности легких металлов. Он образует твердый и плотный адгезионный оксидный слой.
Компоненты погружаются в ванну, и электрический ток используется для «выращивания» однородного слоя оксида на поверхности.ПЭО состоит из трех этапов:
- Окисление подложки (как в процессе анодирования)
- Соосаждение элементов из электролита в покрытие
- Модификация полученного слоя плазменным разрядом
Хотите узнать больше о методологии PEO Keronite? Щелкните ниже, чтобы загрузить бесплатный технический документ.
PEO образует твердые, плотные и износостойкие покрытия для легких металлов, таких как алюминий, титан и магний.По сравнению непосредственно с анодированными покрытиями, PEO образует покрытия с более высокой твердостью, химической пассивностью и выгодной нерегулярной структурой пор, которая обеспечивает высокую устойчивость к деформации и более прочную адгезию.
Помимо превосходных физических и химических характеристик, процесс ПЭО может осуществляться экологически безопасным методом благодаря доброкачественным электролитам, доступным для использования, и нетоксичным побочным продуктам процесса окисления. Электролиты не содержат кислот, аммиака, тяжелых металлов и хрома, а используемые щелочные растворы с низкой концентрацией не представляют опасности и легко утилизируются.
Это означает более экологичное решение, чем альтернативы, а также ряд других преимуществ.
3. Хроматное конверсионное покрытие
Усиление контроля над производственными процессами со стороны государственных органов и регулирующих органов привело к постепенному отказу от использования хроматных конверсионных покрытий как метода защиты от коррозии, хотя это один из наиболее эффективных методов.
Химические составы конверсии хромата сильно различаются, но многие из них включают применение растворов хромовой кислоты, натрия, хромата или дихромата калия для очистки металлических поверхностей вместе с другими добавками.Использование таких добавок вызывает окислительно-восстановительные реакции на поверхности, оставляя на металле подложки пассивную пленку, содержащую оксид хрома (IV) и гидратированные соединения. Это обеспечивает высокую коррозионную стойкость и хорошо сохраняет последующие покрытия.
Высокая защита от коррозии обусловлена способностью соединений хрома (VI) восстанавливать защитную оксидную пленку на поврежденном участке покрытия, подверженном воздействию атмосферного кислорода. Это называется самовосстановлением. Аналогичный механизм используется для создания нержавеющей стали: хром, добавленный к сплаву, естественным образом образует очень тонкий пассивный слой оксида хрома на поверхности, предотвращая окисление железа.Он быстро восстанавливается, если поверхность повреждена, а подповерхностный хром подвергается воздействию атмосферы. Хромат также можно использовать в качестве добавки к краскам или в качестве герметика при анодировании, повышая их защиту от коррозии.
Однако в настоящее время известно, что соединения шестивалентного хрома, используемые при обработке с конверсией хромата, обладают повреждающими и канцерогенными свойствами. Побочные продукты хроматных конверсионных покрытий очень опасны, и поэтому неудивительно, что материалы, использующие этот процесс, занимают жесткую позицию.
Сегодня его использование запрещено во многих отраслях промышленности и строго регулируется. Он по-прежнему широко используется в аэрокосмической отрасли, не склонной к риску, но требует все большего изменения. К сожалению, он остается лучшим методом химической пассивации алюминия благодаря своим самовосстанавливающимся свойствам. В 1980-х годах начались интенсивные исследования, чтобы найти альтернативы самовосстановлению без содержания хрома, но они еще не соответствуют его общему уровню защиты. Инженеры ищут альтернативы, такие как анодирование или обработка на основе ПЭО, для повышения производительности в суровых условиях.
4. Краски
Растворы для поверхностных покрытий, такие как краски, грунтовки и другие полимерные системы, кажутся безграничными как по наличию, так и по разнообразию. Самым привлекательным преимуществом работы с красками является то, что их можно раскрашивать, обрабатывать или наносить разными способами.
Полимерные финишные покрытия также доступны в таком разнообразии и способах нанесения. Могут быть внесены альтернативные химические составы и добавки, которые обеспечивают такие свойства, как блеск, дополнительную твердость, смазывающую способность, определенные текстуры, температурную стабильность и химическую стойкость, и это лишь некоторые из них.
Краскипредставляют собой относительно недорогой метод повышения коррозионной стойкости. Однако задействованные процессы крайне неэффективны; Во время нанесения до 50% покрытия может испариться, а при отверждении в печи образуются вредные побочные продукты, которые опасны и дороги в утилизации в больших объемах.
Обладая превосходной химической и особенно коррозионной стойкостью, как и другие полимерные углеводороды, краски мягкие (их твердость оценивается сравнением грифеля карандаша), что означает, что они легко царапаются и истираются.
5. Порошковые покрытия
Порошковые покрытия, как и краски, представляют собой еще один относительно недорогой вариант. Хотя преимущества порошковых покрытий во многом такие же, как и у красок, но более толстые защитные слои можно наносить более эффективно и быстрее.
Покрытия толстые, что добавляет объемные слои (обычно вверх до 80 мкм), которые существенно повышают коррозионную стойкость материала. Стоимость этой дополнительной защиты заключается в увеличении толщины, а также в том, что эстетические эффекты не столь привлекательны и неодинаковы для разных материалов.
Заключение
В этой статье мы попытались дать краткий обзор покрытий из легких материалов для улучшения коррозионной стойкости легких сплавов.