Назначение, конструкции и материалы осей и валов.
Назначение осей и валов.
Оси служат для поддержания вращающихся вместе с ними или на них различных деталей машин и механизмов. Вращение оси вместе с установленными на ней деталями осуществляется относительно ее опор, называемых подшипниками. Примером невращающейся оси может служить ось блока грузоподъемной машины (рис. 1, а), а вращающейся оси — вагонная ось (рис. 1, б). Оси воспринимают нагрузку от расположенных на них деталей и работают на изгиб.

Конструкции осей и валов.
Валы в отличие от осей предназначены для передачи крутящих моментов и в большинстве случаев для поддержания вращающихся вместе с ними относительно подшипников различных деталей машин. Валы, несущие на себе детали, через которые передается крутящий момент, воспринимают от этих деталей нагрузки и, следовательно, работают одновременно на изгиб и кручение. При действии на установленные на валах детали (конические зубчатые колеса, червячные колеса и т. д.) осевых нагрузок.валы дополнительно работают на растяжение или сжатие. Некоторые валы не поддерживают вращающиеся детали (карданные валы автомобилей, соединительные валки прокатных станов и т. п.), поэтому эти валы работают только на кручение. По назначению различают валы передач, на которых устанавливают зубчатые колеса, звездочки, муфты и прочие детали передач, и коренные валы, на которых устанавливают не только детали передач, но и другие детали, например маховики, кривошипы и т. д.
Оси представляют собой прямые стержни (рис 1, а, б), а валы различают прямые (рис. 1, в, г), коленчатые (рис. 1, д) и гибкие (рис. 1, е). Широко распространены прямые валы. Коленчатые валы в кривошипно-шатунных передачах служат для преобразования возвратно-поступательного движения во вращательное или наоборот и применяются в поршневых машинах (двигатели, насосы). Гибкие валы, представляющие собой многозаходные витые из проволок пружины кручения, применяют для передачи момента между узлами машин, меняющими свое относительное положение в работе (механизированный инструмент, приборы дистанционного управления и контроля, зубоврачебные бормашины и т. п.). Коленчатые и гибкие валы относятся к специальным деталям, их изучают в соответствующих специальных курсах. Оси и валы в большинстве случаев бывают круглого сплошного, а иногда кольцевого поперечного сечения. Отдельные участки валов имеют круглое сплошное или кольцевое сечение со шпоночной канавкой (рис. 1, в, г) или со шлицами, а иногда профильное сечение. Стоимость осей и валов кольцевого сечения обычно больше, чем сплошного сечения; их применяют в случаях, когда требуется уменьшить массу конструкции, например в самолетах (см. также оси сателлитов планетарного редуктора на рис. 4), или разместить внутри другую деталь. Полые сварные оси и валы, изготовляемые из ленты, расположенной по винтовой линии, позволяют снижать массу до 60%.
Оси небольшой длины изготовляют одинакового диаметра по всей длине (рис. 1, а), а длинные и сильно нагруженные – фасонными (рис. 1, б). Прямые валы в зависимости от назначения делают либо постоянного диаметра по всей длине (трансмиссионные валы, рис. 1, в), либо ступенчатыми (рис. 1, г), т.е. различного диаметра на отдельных участках. Наиболее распространены ступенчатые валы, так как их форма удобна для установки на них деталей, каждая из которых должна к своему месту проходить свободно (валы редукторов см. в статье «Зубчатые редукторы» рис. 2; 3; и «Червячная передача» рис. 2; 3). Иногда валы изготовляют заодно с шестернями (см. рис. 2) или червяками (см. рис. 2; 3).

Участки осей и валов, которыми они опираются на подшипники, называют при восприятии радиальных нагрузок цапфами, при восприятии осевых нагрузок — пятами. Концевые цапфы, работающие в подшипниках скольжения, называют шипами (рис. 2, а), а цапфы, расположенные на некотором расстоянии от концов осей и валов, — шейками (рис. 2, б). Цапфы осей и валов, работающие в подшипниках скольжения, бывают цилиндрическими (рис. 2, а), коническими (рис. 2, в) и сферическими (рис. 2, г). Самые распространенные — цилиндрические щшфы, так как они наиболее просты, удобны и дешевы в изготовлении, установке и работе. Конические и сферические цапфы применяют сравнительно редко, например для регулирования зазора в подшипниках точных машин путем перемещения вала или вкладыша подшипника, а иногда для осевого фиксирования оси или вала. Сферические цапфы применяют тогда, когда вал помимо вращательного движения должен совершать угловое перемещение в осевой плоскости. Цилиндрические цапфы, работающие в подшипниках скольжения, обычно делают несколько меньшего диаметра по сравнению с соседним участком оси или вала, чтобы благодаря заплечикам и буртикам (рис. 2, б) оси и валы можно было фиксировать от осевых смещений. Цапфы осей и валов для подшипников качения почти всегда выполняют цилиндрическими (рис. 3, а, б). Сравнительно редко применяют конические цапфы с небольшим углом конусности для регулирования зазоров в подшипниках качения упругим деформированием колец. На некоторых осях и валах для фиксирования подшипников качения рядом с цапфами предусматривают резьбу для гаек (рис. 3, б;) или кольцевые выточки для фиксирующих пружинных колец.

Пяты, работающие в подшипниках скольжения, называемых подпятниками, делают обычно кольцевыми (рис. 4, а), а в некоторых случаях — гребенчатыми (рис. 4, б). Гребенчатые пяты применяют при действии на валы больших осевых нагрузок; в современном машиностроении они встречаются редко.

Посадочные поверхности осей и валов, на которых устанавливают вращающиеся детали машин и механизмов, выполняют цилиндрическими и гораздо реже коническими. Последние применяют, например, для облегчения постановки на вал и снятия с него тяжелых деталей при повышенной точности центрирования деталей.
Разность между диаметрами соседних ступеней осей и валов для снижения концентрации напряжений должна быть минимальной. Торцы осей и валов для облегчения установки на них вращающихся деталей машин и предубеждения травмирования рук делают с фасками, т. е. слегка обтачивают на конус (см. рис. 1…3). Радиусы закруглений галтелей и размеры фасок нормализованы ГОСТ 10948-64.
Длина осей обычно не превышает 2…3 м, валы могут быть длиннее. По условиям изготовления, транспортировки и монтажа длина цельных валов не должна превышать 6…7 м. Более длинные валы делают составными и отдельные части их соединяют муфтами или с помощью фланцев. Диаметры посадочных участков осей и валов, на которых устанавливаются вращающиеся детали машин и механизмов, должны быть согласованы с ГОСТ 6636-69 (СТ СЭВ 514-77).
Материалы осей и валов.
Оси и валы изготовляют из углеродистых и легированных конструкционных сталей, так как они обладают высокой прочностью, способностью к поверхностному и объемному упрочнению, легкостью получения прокаткой цилиндрических заготовок и хорошей обрабатываемостью на станках. Для осей и валов без термообработки используют углеродистые стали Ст3, Ст4, Ст5, 25, 30, 35, 40 и 45. Оси и валы, к которым предъявляют повышенные требования к несущей способности и долговечности шлицев и цапф, выполняют из среднеуглеродистых или легированных сталей с улучшением 35, 40, 40Х, 40НХ и др. Для повышения износостойкости цапф валов, вращающихся в подшипниках скольжения, валы делают из сталей 20, 20Х, 12ХНЗА и других с последующей цементацией и закалкой цапф. Ответственные тяжелонагруженные валы изготовляют из легированных сталей 40ХН, 40ХНМА, 30ХГТ и др. Тяжелонагруженные валы сложной формы, например, коленчатые валы двигателей, делают также из модифицированного или высокопрочного чугуна.
конструктивные особенности, классификация и производство

При создании различных механизмов, имеющих в своём составе вращающиеся детали, часто используют валы. Давайте разберемся, что называется валом, в чем его отличие от оси, из чего состоит деталь вал, его классификация и материалы, используемые при производстве валов.
Определение, конструктивные особенности
Вал — деталь механизма, выполненная из металла, имеющая сечение определенной формы и передающая крутящий момент на другие элементы, вызывая их вращение.
Ось, отличается от вала тем, что служит только для их опоры. Если оси подразделяются на подвижные и статические, то валы всегда вращающиеся. Геометрическая форма оси, может быть только прямой.
Вал составляют следующие участки:
- Опорный.
- Промежуточный.
- Концевой.
Кольцевое утолщение называется буртиком. Промежуточная часть между разными диаметрами для фиксации одеваемых деталей носит название – заплечик.
Участок где происходит изменение диаметра вала называется галтелью. С Целью увеличения прочности кривизна галтели меняется плавно. Различают 2 вида кривизны: постоянная и переменная. Увеличение значения кривизны галтели и изготовление специальных отверстий повышает надежность вала на одну десятую часть.
В зависимости от распределения величины нагрузок, отражённого в специальных графиках (эпюрах) определяют длину и форму вала. Также этот параметр зависит от условий сборки и метода изготовления.
Размеры посадочных мест для крутящихся элементов расположенных на концах валов жестко стандартизированы по ГОСТам.
Материалы
В зависимости от внешних сил, которым подвергается деталь вал в процессе эксплуатации, осуществляется подбор материала для его изготовления.
Для этой цели используют легированные стали с высоким содержанием углерода, так как обладают улучшенными механическими характеристиками и износостойкостью. Получают данные детали методом прокатки.
Основную массу валов производят из легированной стали марки 45Х, со средним содержанием углерода. Для валов, подвергающихся высоким напряжениям используют стали 40ХН, 40ХНГМА, 30ХГТ и другие, которые подвергаются процессу закалки с высоким отпуском.
Кроме того, для коленчатых тяжелых валов в качестве материала используют высокопрочные чугуны, образованные путем вкрапления в металлическую решетку шарообразных включений углерода и содержащие в составе Mg, Ca, Se, Y.
Классификация валов
По назначению:
- Валы передач, на которых расположены детали механизма передач (шестеренки, муфты, шкифы).
- Коренные, которые несут другие части.
По форме оси:
- Прямые.
- Кривошипные.
- Гибкие.
Прямые делятся на:
- Гладкие.
- Ступенчатые.
- Червячного типа.
- Фланцевые.
- Карданные.
По форме сечения:
- Гладкие.
- Пустотелые.
- Шлицевые.
Производство
Существуют несколько этапов изготовления:
- Проведение проектных и конструкторских работ и расчетов с привлечением специального программного обеспечения.
- Выбор и закупка необходимого материала, отвечающего требуемым характеристикам. Оснащение дополнительным производственным оборудованием, при необходимости.
- Формовка.
- Сварка и шлифовка.
- Динамическая балансировка.
- Нанесение защитного покрытия.
Первый этап обычно выполняются в конструкторском бюро. По окончанию работы оформляется проектная документация, содержащая расчеты и обработанные данные, в строгом соответствии с которыми будет осуществляться производство данного типа детали.
На втором этапе, производится выбор материала заготовки, отвечающего требуемым эксплуатационным характеристикам и перевооружение производства технологическим оборудованием.
Третий этап выполняется с использованием токарного оборудования, где заготовка подвергается механической обработке и обретает свою геометрию и размер. При этом, изменению подвергаются все поверхности заготовки.
На четвертом этапе производится скрепление отдельных элементов заготовки путем их сварки и изготовления необходимых отверстий и канавок. Затем, с помощью современных методов измерения, происходит шлифовка и доведения до их конечных размеров.
На следующем этапе, проверяют балансировку деталей, подвергая их динамическим испытаниям, так как от этого зависит полнота передачи энергии вращения другим элементам механизма. Нарушения балансировки может привести к нарушению эксплуатации оборудования на котором будет установлен вал.
Последний — шестой этап характеризуется нанесением специального слоя на его поверхность. Выбор способы и вида покрытий зависит от условий эксплуатации.
Тонкий слой резины на поверхности валов предохраняет от действия реакционных сред. Стойкость к коррозии обеспечивается электродуговым металлическим напылением этих деталей.
Методом хромирования добиваются увеличения износостойкости и уменьшения трения данного типа деталей.
Деталь — вал получило широкое использование во многих направлениях промышленности: автомобилестроении, станкостроении, железнодорожной, текстильной, деревообрабатывающей промышленности.
Подробно рассмотрев те вопросы, которые были поставлены выше, можно заключить:
- Вал отличается от оси своей функциональностью и геометрией.
- Вал состоит из 3-х участков (цапфы, шейки, шипа).
- Существуют различные типы классификации валов по назначению и формам.
- Материалом для детали выступают легированные стали различных марок, реже высокопрочные чугуны с шарообразными вкраплениями углерода.
- Изготовление вала включает в себя несколько этапов и требует специальных знаний и значительных затрат энергоресурсов.
- Для увеличения времени эксплуатации валов на этапе производства их поверхность покрывают специальными материалами.
- Вал широко применяется во многих механизмах в различных областях деятельности человека.

60. Валы и оси. & 61. Назначение и классификация
ОБЩАЯ ХАРАКТЕРИСТИКА ВАЛОВ И ОСЕЙ
Назначение и классификация. Валы служат для поддержания вращающихся деталей и передачи вращающего момента от одной детали к другой (в осевом направлении) Их условно разделяют на: простые валы (валы) — работают в условиях кручения, изгиба и растяжения (сжатия), их применяют в передачах: зубчатых, ременных и др.; торсионные валы (торсионы) — работают лишь в условиях кручения и передают вращающий момент, соединяя обычно два вала на индивидуальных опорах; оси — поддерживающие валы, работающие лишь в условиях изгиба. В зависимости от распределения нагрузок вдоль оси вала и условий сборки прямые валы выполняют гладкимиилиступенчатыми, Гладкие валы более технологичны. Коленчатые валы используют в поршневых двигателях и компрессорах Для передачи вращающего момента между агрегатами со смещенными в пространстве осями применяют специальные гибкие валы. Такие валы обладают высокой жесткостью при кручении и малой жесткостью при изгибе. В зависимости от расположения, быстроходности и назначения различают валы входные, промежуточные, выходные, тихо- или быстроходные, распределительные.
62. Особенности конструирования.
Конструктивная форма вала (оси) зависит от нагрузки, способа фиксирования насаживаемой детали и условий сборки (разборки).
Для осевого фиксирования деталей (подшипников, зубчатых колес и др.) на валах выполняют упорные буртики или заплечики .
63. Материалы валов.
Для изготовления валов используют углеродистые стали марок 20, 30, 40, 45 и 50, легированные стали марок 20Х, 40Х, 40ХН, 18Х2Н4МА, 40ХН2МА и др., титановые сплавы ВТЗ-1, ВТ6 и ВТ9 . Выбор материала, термической и химико-термической обработки определяется конструкцией вала и опор, условиями эксплуатации. Быстроходные валы, в подшипниках скольжения, требуют высокой твердости цапф (посадочных хвостовиков), поэтому их изготовляют из цементируемых сталей 12Х2Н4А, 18ХГТ или азотируемых сталей 38Х2МЮА . Валы-шестерни также изготовляют из цементируемых легированных сталей марок 12ХНЗА, 12Х2Н4А и др.
64. Расчёт валов на прочность и жёсткость
Вал принадлежит к числу наиболее ответственных деталей машин, нарушение его формы, или разрушение влечет за собой выход из строя всей конструкции. Для обеспечения работоспособности и надежности валы и оси должны удовлетворять основным критериям : прочности и жесткости (деформативности).
65. Нагрузки на валы и расчётные схемы
66. Расчёт на прочность.
В предварительном
(проектном) расчете диаметр входного
вала d приближенно может быть найден по
известному значению крутящего момента
из условия прочности
Где Т – крутящий момент в расчётном сечении вала; [τk] — допускаемое напряжение на кручение. [τk] — =12…20 МПа для стальных валов; Р — передаваемая мощность, кВт; п — частота вращения вала, мин -1. Иногда при проектировании диаметр входного хвостовика вала (минимальный диаметр вала) принимают конструктивно (из практики проектирования) равным 0,8…1,0 d вала приводного двигателя. Наименьший диаметр промежуточного вала принимают обычно равным внутреннему диаметру подшипника. Оценку прочностной надежности вала в конструкции выполняют обычно в форме определения запасов прочности
67. Статический
запас прочности. Рассчитывают
по наибольшей кратковременной нагрузке
(с учетом динамических и ударных
воздействий), которая не может вызвать
усталостного разрушения (например, по
нагрузке в момент пуска установки). Валы
могут быть нагружены постоянными
напряжениями, например от неуравновешенности
вращающихся деталей. Валы работают в
основном в условиях изгиба и кручения,
а напряжения от осевых сил малы, поэтому
эквивалентное напряжение в точке
наружного волокна: где
σн и τк — наибольшие напряжения от изгиба
моментом Ми и кручения моментом Т.
σн=Mк/Wн;
τк=T/Wk Здесь Wн и WK — осевой и
полярный момент сопротивления сечения
вала,
Так
какWk = 2WН,
то с учетом этих соотношений можно
записать
Запас
прочности по пределу текучести
σТ – предел текучести материала вала.
Обычно принимают допускаемый запас
прочности [nT]:=1,2…1,8. Сечение (опасное сечение), в котором следует
определить запас nT),
находят после построения эпюр изгибающих
и крутящих моментов. Если нагрузки
действуют на вал в разных плоскостях,
то сначала силы проецируют на координатные
оси и строят эпюры моментов в координатных
плоскостях. Затем геометрически суммируют
изгибающие моменты, очерчивая эпюру
прямыми линиями, что идет в запас
прочности. Если угол между плоскостями
30°, то считают, что силы действуют в
одной плоскости. Переменные напряжения
в валах вызываются переменной или
постоянной нагрузкой. Постоянные
по величине и направлению силы передач вызывают во вращающихся валах переменные
напряжения изгиба,
изменяющиеся по симметричному циклу с
амплитудой и средними напряжениями:
В расчетах валов условно принимают, что
вращающий момент и касательные напряжения
от кручения изменяются по пульсационному
циклу, которому соответствуют амплитуда
и среднее напряжение:
Условие
прочностной надежности в этом случае
имеет видn≥[n].Допускаемые
значения запаса прочности при переменных
напряжениях назначают на основе
предшествующего опыта расчетов и
эксплуатации [n]≥2,0.
Высокооборотные валы в ряде конструкций
работают в условиях изгибных, крутильных
и изгибно-крутильных колебаний, вызывающих
появление переменных напряжений. Эти
напряжения могут быть опасными для
прочности вала на резонансных режимах
работы. Для предотвращения резонансных
колебаний валов проводят их расчет на
колебания. Для
повышения сопротивления усталости
валов используют различные конструктивные
и технологические методы.
Основной конструктивный метод повышения
надежности валов — снижение концентрации
напряжений в опасных сечениях путем
увеличения радиусов галтелей и др.
Существенное значение имеет правильный
выбор материала и режима термической
обработки заготовки (вала). Для повышения
сопротивления усталости валов производят
упрочняющую обработку зон концентрации
напряжений (выточек, галтелей, шпоночных
канавок, резьбы и др.) путем обдувки
дробью, лучом лазера и т. п.
68. Расчёт жёсткости вала. Упругие перемещения валов оказывают неблагоприятное влияние на работу связанных с ними соединений, подшипников, зубчатых колес и других деталей : увеличивают концентрацию контактных напряжений и износ деталей, снижают сопротивление усталости деталей и соединений, точность механизмов и т. п. Большие перемещения сечений вала от изгиба могут привести к выходу из строя конструкции вследствие заклинивания подшипников. Изгибная и крутильная жесткость валов существенно влияет на частотные характеристики системы при возникновении изгибных и крутильных колебаний. При проектировании валов следует проверять прогибы и углы φ поворота сечений, зависящих от требований, предъявляемых к валу, и особенностей его работы. Допустимые величины φ Максимальный прогиб вала не должен превышать (0,0002… 0,0003) L (L — расстояние между опорами), а допустимый прогиб под колесами составляет: 0,01m — для цилиндрических и 0,005 m — для конических, гипоидных и глобоидных передач ( m — модуль зацепления). Допустимые относительные углы закручивания валов Ө зависят от требований и условий работы конструкции и лежат в пределах 0,20…1° на 1 м длины вала.
69. Общие сведения о подшипниках скольжения. Подшипник скольжения является парой вращения. Состоит из опорного участка вала (цапфы) и собственно подшипника 2, в котором скользит цапфа. Их используют в качестве опор валов и осей в случаях, когда применение подшипников качения затруднено или невозможно по ряду причин: 1)высокие вибрационные и ударные нагрузки; 2) низкие и особо высокие частоты вращения; 3)работа в воде, агрессивных средах, 4)при отсутствии или недостаточном смазывании ; 5)необходимость выполнения диаметрального разъема; 6)отсутствие подшипников качения требуемых диаметров и др. Благодаря бесшумности , указанным выше достоинствам, а также по конструктивным и экономическим соображениям опоры скольжения находят широкое применение в паровых и газовых турбинах, двигателях внутреннего сгорания, центробежных насосах, центрифугах, металлообрабатывающих станках, прокатных станах, тяжелых редукторах и пр. По виду трения скольжения различают: 1)подшипники сухого трения — работают на твердых смазках или без смазки; 2)подшипники граничного (полужидкостного) трения; 3)подшипники жидкостного трения; 4)подшипники с газовой смазкой. По виду воспринимаемой нагрузки подшипники подразделяют на: 1)радиальные — воспринимают радиальную нагрузку; 2)упорные — воспринимают осевые силы ; 3)радиально-упорные — воспринимают радиальные и осевые нагрузки. Обычно их функции выполняют упорные подшипники, совмещенные с радиальными. Цапфу, передающую радиальную нагрузку, называют шипом — при расположении ее в конце вала и шейкой — если она находится в середине вала. Цапфу, передающую осевую нагрузку, называют пятой, а подшипник — подпятником. Рабочая поверхность подшипников и цапф может быть цилиндрической, конической и шаровой формы . Конические и шаровые подшипники применяются редко.
70. Особенности работы подшипников скольжения. Условия работы подшипников скольжения определяются основными параметрами режима работы (удельной нагрузкой р и угловой скоростью ω цапфы), наличием и типом смазочного материала, физико-механическими характеристиками контактирующих поверхностей. Для однотипных подшипников с одинаковым соотношением размеров (диаметра d и длины l цапфы) потери на трение пропорциональны коэффициенту трения f=2Tf/(Frd), где Tf — момент трения в подшипнике; Fr — радиальная сила (опорная реакция). В подшипниках сухого трения коэффициент трения обычно не слишком значительно меняется в зависимости от параметров режима работы. В подшипниках граничного трения влияние параметров режима работы весьма существенно. Коэффициент граничного трения может достигать значений 0,2…0,3. Граничное трение сопровождается износом контактирующих поверхностей. Описанные условия работы типичны для низкоскоростных подшипников с периодической или недостаточной подачей смазки и недопустимы для высокоскоростных подшипников. С увеличением ω коэффициент трения резко уменьшается в связи с переходом трения в полужидкостное и наличием одновременно граничной и жидкостной смазки .Коэффициент полужидкостного трения ниже, чем при граничном трении. Однако режим характеризуется нестабильными условиями смазывания, так как повышение температуры в зоне контакта уменьшает вязкость и вызывает разрушение граничной пленки и повышение коэффициента трения. Поэтому работа подшипника с высокой угловой скоростью в режиме полужидкостного трения также опасна. Начиная с угловой скорости ω=ωкр при которой коэффициент трения f = fmin, вал отходит от подшипника («всплывает»), смещается в направлении вращения, занимая новое положение с меньшим эксцентриситетом цапфы и подшипника. Последующее увеличение приводит к увеличению коэффициента трения в связи с увеличением толщины слоя смазки и ростом гидравлических потерь. При этом вал удерживается на «масляном клине» — осуществляется режим жидкостного трения. Так как непосредственный контакт отсутствует, то трение в подшипнике определяется законами гидродинамики. Коэффициент жидкостного трения не превышает 0,005, и износ практически отсутствует, потери на трение и тепловыделение невелики. Условия смазывания носят устойчивый характер.
Конструктивные элементы валов и осей
Содержание страницы
1. Валы
Валы – детали машин, предназначенные для обеспечения взаимодействия размещенных на них деталей механических передач. Взаимодействовать могут подвижные детали с подвижными, например, шестерни в зубчатой передаче, а также подвижные детали с неподвижными. Например, опоры с подшипниками качения, которые воспринимают нагрузку от валов, передают ее неподвижному корпусу и таким образом дают возможность работать передаче. Это взаимодействие обеспечивает передачу крутящего момента вдоль осевой линии вала.
Валы машин, которые кроме деталей передач несут рабочие органы машины, называются коренными. Коренной вал станков с вращательным движением инструмента или изделия называется шпинделем. Вал, распределяющий механическую энергию по отдельным рабочим машинам, называется трансмиссионным. В отдельных случаях валы изготовляют как одно целое с цилиндрической или конической шестерней (вал-шестерня) или с червяком (вал-червяк).
По форме геометрической оси валы бывают прямые и гибкие (с изменяемой формой оси). Простейшие прямые валы имеют форму тел вращения.
На рис. 1 показаны прямые валы: гладкий (а), ступенчатый (б) и коленчатый (в). Ступенчатые валы являются наиболее распространенными. Для уменьшения массы или для размещения внутри них других деталей валы иногда делают с каналом по оси. В отличие от сплошных такие валы называют полыми.
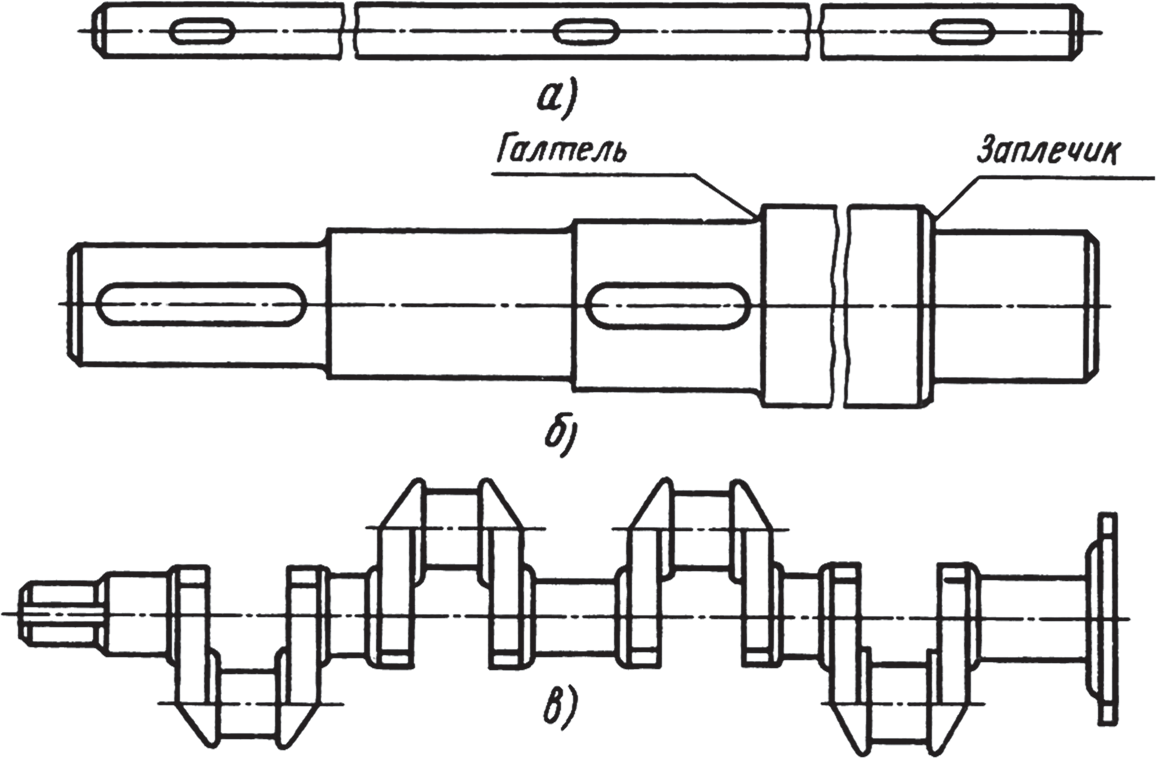
Рис. 1. Валы
2. Оси
Ось – деталь машин и механизмов, служащая для поддержания вращающихся частей, но не передающая полезный крутящий момент. Оси (рис. 2) бывают вращающиеся (а) и неподвижные (б). Вращающаяся ось устанавливается в подшипниках. Примером вращающихся осей могут служить оси железнодорожного подвижного состава, примером невращающихся – оси передних колес автомобиля.
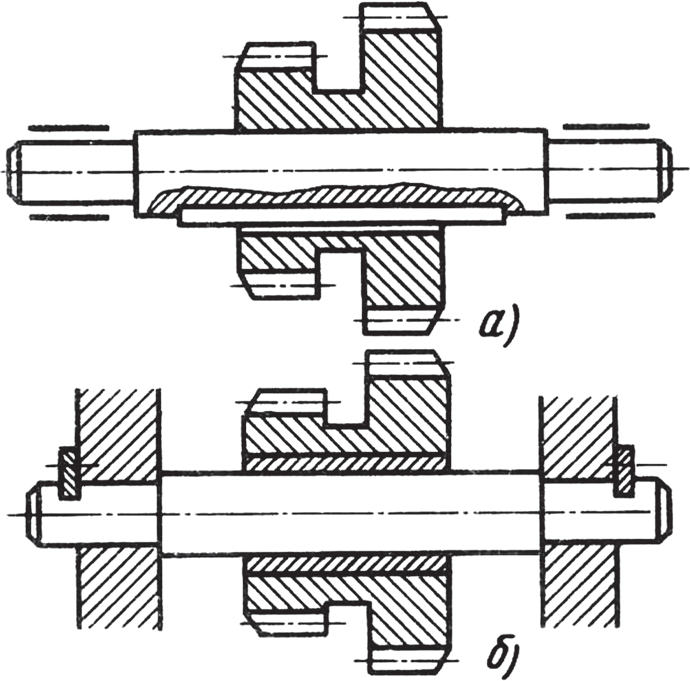
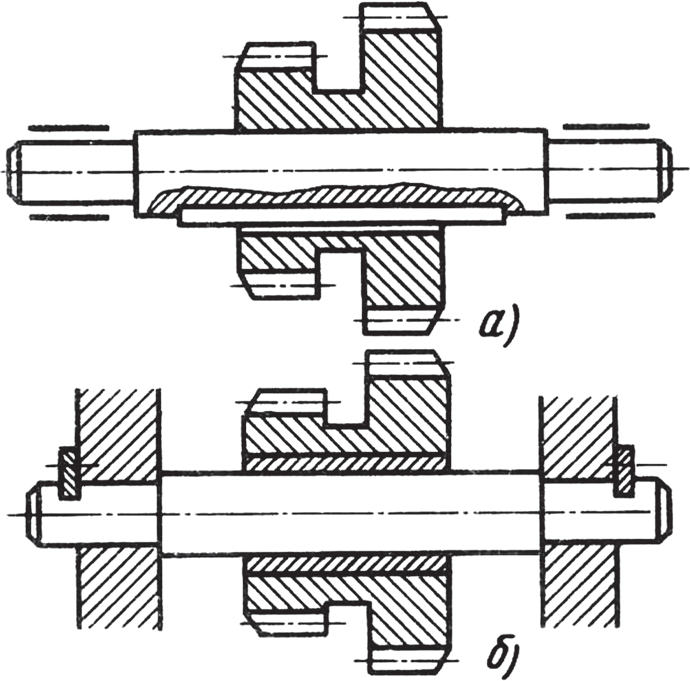
Рис. 2. Оси
Из определений видно, что при работе валы всегда вращаются и испытывают деформации кручения или изгиба и кручения, а оси – только деформацию изгиба (возникающими в отдельных случаях деформациями растяжения и сжатия чаще всего пренебрегают).
Опорная часть вала или оси называется цапфой. Концевая цапфа называется шипом, а промежуточная – шейкой (рис. 3, а). Опорой для них служат радиальные или радиально-упорные подшипники скольжения или качения. Шейка в отличие от шипа, который несет только радиальную нагрузку FA, несет радиальную нагрузку FB и передает крутящий момент с концевой головки на промежуточную и, следовательно, работает еще и на кручение. Поэтому диаметр этой шейки должен быть больше диаметра головки d В, размер которого определяется расчетом, и диаметра шипа. Участки вала и оси, на диаметрах поверхностей которых закрепляются детали, воспринимающие или передающие нагрузку, называют головками или подступицами.
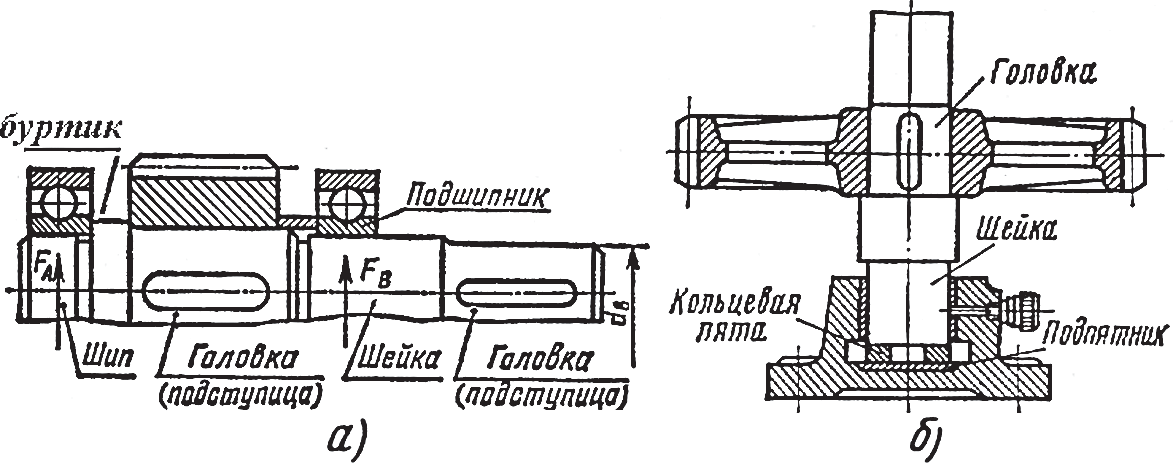
Рис. 3. Элементы валов
Концевая цапфа, предназначенная нести преимущественно осевую нагрузку, называется пятой (рис. 3, б). Опорами для пят служат подпятники – упорные подшипники скольжения или качения.
По форме цапфы могут быть цилиндрическими, коническими, шаровыми и плоскими (пяты).
Кольцевое утолщение вала (между шипом и головкой) (рис. 3, а), составляющее с ним одно целое, называется буртиком. Переходная поверхность от одного сечения вала к другому, служащая для упора насаживаемых на вал деталей (от шипа к буртику для упора подшипника), называется заплечиком (рис. 3, а).
3. Материалы валов и осей
Требованиям работоспособности валов и осей наиболее полно удовлетворяют углеродистые и легированные стали, а в ряде случаев – высокопрочные чугуны. Выбор материала, термической и химико-термической обработки определяется конструкцией вала и опор, техническими условиями на изделие и условиями его эксплуатации. Для большинства валов применяют стали марок Сталь 45, Сталь 40Х и др., а для ответственных конструкций – Сталь 40ХН, Сталь З0ХГТ и др. Рабочие поверхности валов из этих сталей подвергают термической обработке (улучшению, поверхностной закалке ТВЧ и др.).
Быстроходные валы, вращающиеся в подшипниках скольжения, требуют высокой твердости цапф, поэтому их изготовляют из цементируемых сталей марок Сталь 20Х, 12Х2Н4А, 18ХГТ или азотируемых сталей марок Сталь 38Х2МЮА и др.
Обычно валы подвергают токарной обработке, термической обработке с последующим шлифованием и отделочной обработке посадочных поверхностей и цапф. Для этого посадочные поверхности и галтели подвергают суперфинишной обработке или полировке.
Концевые участки валов выполняют цилиндрическими (рис. 4) или коническими (рис. 5). Посадка деталей на конус обеспечивает легкость сборки и разборки, высокую точность базирования, возможность создания любого натяга. Поэтому консольные концы валов редукторов серийного производства, как правило, делают конусными. Поскольку цилиндрические концы валов проще в изготовлении, то при единичном и мелкосерийном производствах они имеют преимущественное распространение.
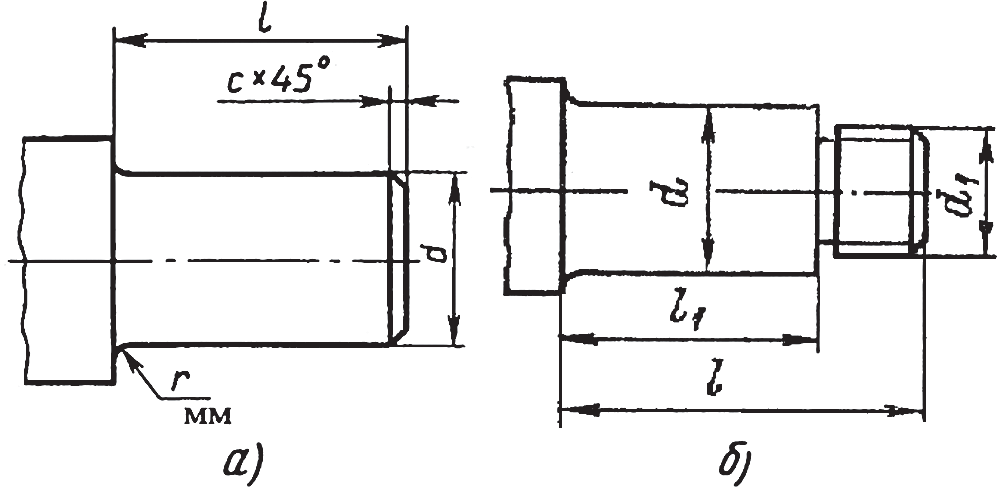
Рис. 4. Концы валов цилиндрические: а – шейка; б – шейка с наружной резьбой
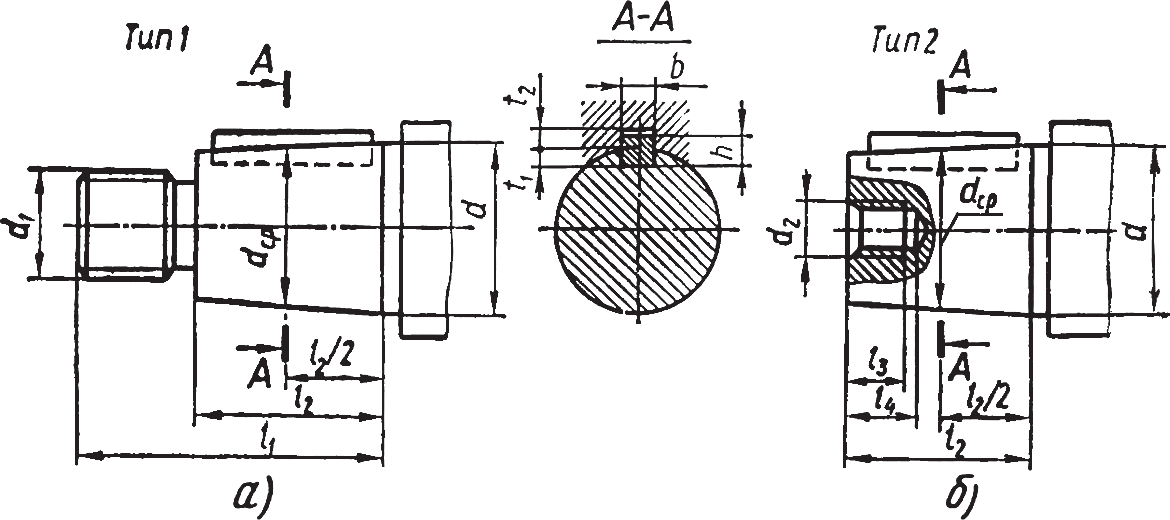
Рис. 5. Концы валов конические с конусностью 1:10: а – с наружной; б – с внутренней резьбой
На торцах валов располагают центровые отверстия с углом конуса α=60° (рис. 6), которые используют в качестве технологических баз при изготовлении валов и осей и при проверке погрешностей, которые образуются при обработке и эксплуатации валов и осей (а), а также применяют для монтажных работ, транспортирования и хранения в вертикальном положении (б). Фаска под углом 120° защищает резьбу и конусную поверхность центрового отверстия от забоин (см. в конце табл. 1).
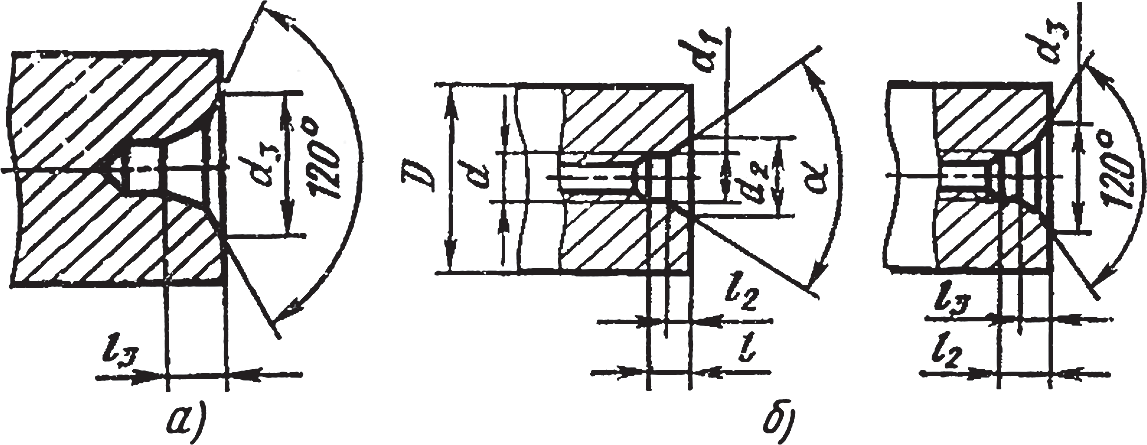
Рис. 6. Центровые отверстия на торцах валов
Форма вала по длине определяется конструктивно с учетом распределения нагрузок, т. е. эпюрами изгибающих и крутящих моментов, условиями сборки и технологией изготовления. Однако следует стремиться к форме профиля вала, приближающегося к форме бруса с равнопрочными сечениями или равного сопротивления изгибу.
Поверхности валов, предназначенные для установки деталей, передающих вращающий момент в машинах, механизмах и приборах, выполняют по форме и по размерам с допусками, которые обеспечивают сопряжение валов с этими деталями.
Требования к шероховатости поверхности деталей и посадки деталей на валах приведены в табл. 1 и 2.
Таблица 1. Рекомендуемая шероховатость на различных участках вала
Поверхности посадочных мест валов, мм | Шероховатость, Ra | ||
квалитет точности | Шот | Шдо | |
11-й | 30 | 500 | 6,3 |
12-й | 6 | 80 | 2,5 |
9-й | 80 | 500 | 2,5 |
11-й | 3 | 30 | 2,5 |
7-й и 8-й | 6 | 80 | 1,25 |
6-й | 10 | 120 | 0,63 |
Шейки валов с манжетными уплотнениями | 0,32 | ||
Шейки валов с фетровыми уплотнениями | 1,25-0,63 | ||
Рабочие поверхности шпоночных пазов | 3,2-6,3 | ||
Нерабочие поверхности шпоночных пазов | 6,3-10 | ||
Фаски, отверстия из-под сверла, торцы | 10-20 |
Таблица 2. Посадки деталей на валах
Закрепляемые детали | Режим работы | |
нормальный | тяжелый | |
Зубчатые колеса до Ш120 мм | H7/p6 | H7/r6 |
Зубчатые колеса св. Ш80-500 мм | H7/r6; H8/s7 | H7/p6; H8/u8 |
Зубчатые колеса при частом демонтаже | H7/n6; H7/m6; H7/k6 | |
Муфты св. Ш80-500 мм | H7/n6; H7/m6; H7/k6 | H7/p6; H7/r6 |
Валы и оси конструктивно связывают через подшипники вращающиеся детали с корпусными деталями. Предварительные размеры шеек валов определяют расчетом, затем после определения способа соединения вращающихся деталей с валом (шпоночным, шлицевым или др.) уточняют размеры посадочных мест и конструкцию валов.
В местах изменения диаметра вала или оси делают переходы. Конструктивно они должны быть выполнены так, чтобы прилегание детали к буртику или торцу переходной поверхности было плотным, без зазора. Если переход от цилиндрической поверхности к вертикальной торцевой поверхности буртика или к торцу переходной поверхности выполнен по радиусу, то такой переход называют галтелью (рис. 7, а), а если с проточкой, в виде канавки, то называют поднутрением (рис. 7; б, в).
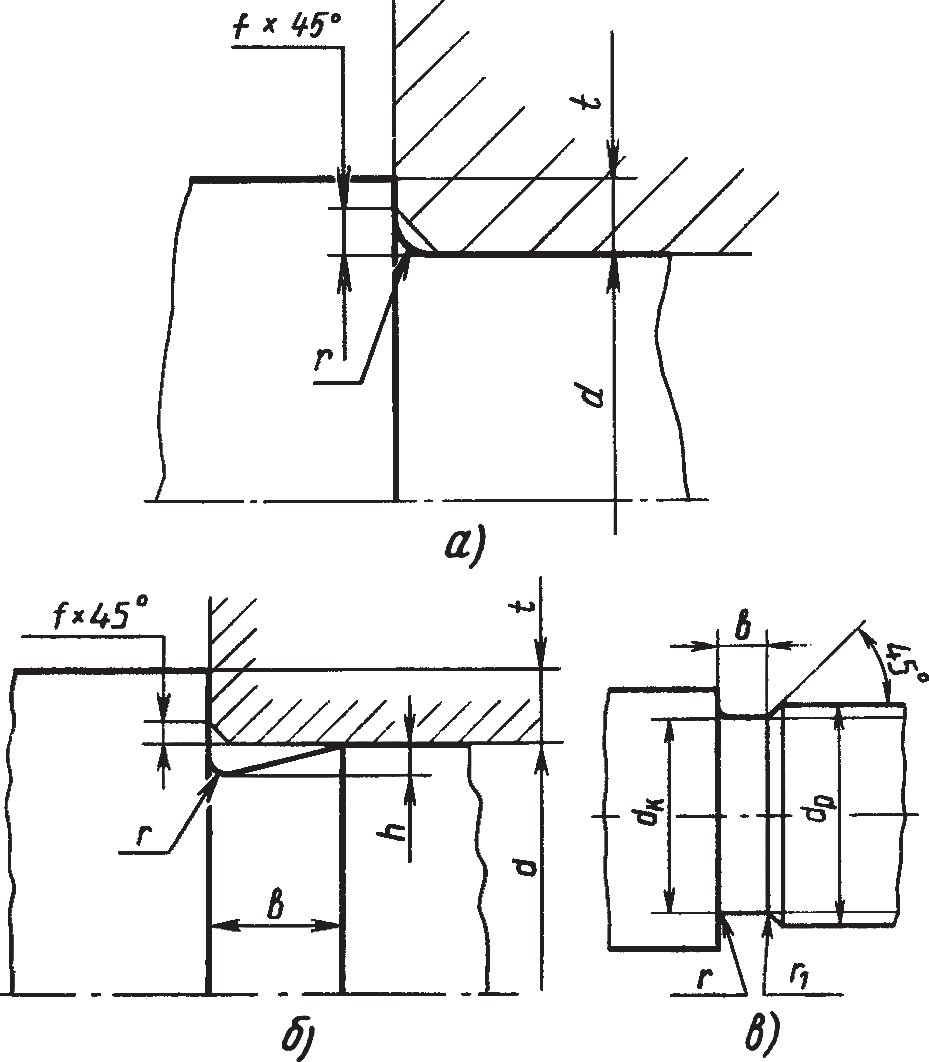
Рис. 7. Конструктивные переходы в местах изменения диаметров вала
Просмотров: 582
60. Валы и оси. & 61. Назначение и классификация
ОБЩАЯ ХАРАКТЕРИСТИКА ВАЛОВ И ОСЕЙ
Назначение и классификация. Валы служат для поддержания вращающихся деталей и передачи вращающего момента от одной детали к другой (в осевом направлении) Их условно разделяют на: простые валы (валы) — работают в условиях кручения, изгиба и растяжения (сжатия), их применяют в передачах: зубчатых, ременных и др.; торсионные валы (торсионы) — работают лишь в условиях кручения и передают вращающий момент, соединяя обычно два вала на индивидуальных опорах; оси — поддерживающие валы, работающие лишь в условиях изгиба. В зависимости от распределения нагрузок вдоль оси вала и условий сборки прямые валы выполняют гладкимиилиступенчатыми, Гладкие валы более технологичны. Коленчатые валы используют в поршневых двигателях и компрессорах Для передачи вращающего момента между агрегатами со смещенными в пространстве осями применяют специальные гибкие валы. Такие валы обладают высокой жесткостью при кручении и малой жесткостью при изгибе. В зависимости от расположения, быстроходности и назначения различают валы входные, промежуточные, выходные, тихо- или быстроходные, распределительные.
62. Особенности конструирования.
Конструктивная форма вала (оси) зависит от нагрузки, способа фиксирования насаживаемой детали и условий сборки (разборки).
Для осевого фиксирования деталей (подшипников, зубчатых колес и др.) на валах выполняют упорные буртики или заплечики .
63. Материалы валов.
Для изготовления валов используют углеродистые стали марок 20, 30, 40, 45 и 50, легированные стали марок 20Х, 40Х, 40ХН, 18Х2Н4МА, 40ХН2МА и др., титановые сплавы ВТЗ-1, ВТ6 и ВТ9 . Выбор материала, термической и химико-термической обработки определяется конструкцией вала и опор, условиями эксплуатации. Быстроходные валы, в подшипниках скольжения, требуют высокой твердости цапф (посадочных хвостовиков), поэтому их изготовляют из цементируемых сталей 12Х2Н4А, 18ХГТ или азотируемых сталей 38Х2МЮА . Валы-шестерни также изготовляют из цементируемых легированных сталей марок 12ХНЗА, 12Х2Н4А и др.
64. Расчёт валов на прочность и жёсткость
Вал принадлежит к числу наиболее ответственных деталей машин, нарушение его формы, или разрушение влечет за собой выход из строя всей конструкции. Для обеспечения работоспособности и надежности валы и оси должны удовлетворять основным критериям : прочности и жесткости (деформативности).
65. Нагрузки на валы и расчётные схемы
66. Расчёт на прочность.
В предварительном
(проектном) расчете диаметр входного
вала d приближенно может быть найден по
известному значению крутящего момента
из условия прочности
Где Т – крутящий момент в расчётном сечении вала; [τk] — допускаемое напряжение на кручение. [τk] — =12…20 МПа для стальных валов; Р — передаваемая мощность, кВт; п — частота вращения вала, мин -1. Иногда при проектировании диаметр входного хвостовика вала (минимальный диаметр вала) принимают конструктивно (из практики проектирования) равным 0,8…1,0 d вала приводного двигателя. Наименьший диаметр промежуточного вала принимают обычно равным внутреннему диаметру подшипника. Оценку прочностной надежности вала в конструкции выполняют обычно в форме определения запасов прочности
67. Статический
запас прочности. Рассчитывают
по наибольшей кратковременной нагрузке
(с учетом динамических и ударных
воздействий), которая не может вызвать
усталостного разрушения (например, по
нагрузке в момент пуска установки). Валы
могут быть нагружены постоянными
напряжениями, например от неуравновешенности
вращающихся деталей. Валы работают в
основном в условиях изгиба и кручения,
а напряжения от осевых сил малы, поэтому
эквивалентное напряжение в точке
наружного волокна: где
σн и τк — наибольшие напряжения от изгиба
моментом Ми и кручения моментом Т.
σн=Mк/Wн;
τк=T/Wk Здесь Wн и WK — осевой и
полярный момент сопротивления сечения
вала,
Так
какWk = 2WН,
то с учетом этих соотношений можно
записать
Запас
прочности по пределу текучести
σТ – предел текучести материала вала.
Обычно принимают допускаемый запас
прочности [nT]:=1,2…1,8. Сечение (опасное сечение), в котором следует
определить запас nT),
находят после построения эпюр изгибающих
и крутящих моментов. Если нагрузки
действуют на вал в разных плоскостях,
то сначала силы проецируют на координатные
оси и строят эпюры моментов в координатных
плоскостях. Затем геометрически суммируют
изгибающие моменты, очерчивая эпюру
прямыми линиями, что идет в запас
прочности. Если угол между плоскостями
30°, то считают, что силы действуют в
одной плоскости. Переменные напряжения
в валах вызываются переменной или
постоянной нагрузкой. Постоянные
по величине и направлению силы передач вызывают во вращающихся валах переменные
напряжения изгиба,
изменяющиеся по симметричному циклу с
амплитудой и средними напряжениями:
В расчетах валов условно принимают, что
вращающий момент и касательные напряжения
от кручения изменяются по пульсационному
циклу, которому соответствуют амплитуда
и среднее напряжение:
Условие
прочностной надежности в этом случае
имеет видn≥[n].Допускаемые
значения запаса прочности при переменных
напряжениях назначают на основе
предшествующего опыта расчетов и
эксплуатации [n]≥2,0.
Высокооборотные валы в ряде конструкций
работают в условиях изгибных, крутильных
и изгибно-крутильных колебаний, вызывающих
появление переменных напряжений. Эти
напряжения могут быть опасными для
прочности вала на резонансных режимах
работы. Для предотвращения резонансных
колебаний валов проводят их расчет на
колебания. Для
повышения сопротивления усталости
валов используют различные конструктивные
и технологические методы.
Основной конструктивный метод повышения
надежности валов — снижение концентрации
напряжений в опасных сечениях путем
увеличения радиусов галтелей и др.
Существенное значение имеет правильный
выбор материала и режима термической
обработки заготовки (вала). Для повышения
сопротивления усталости валов производят
упрочняющую обработку зон концентрации
напряжений (выточек, галтелей, шпоночных
канавок, резьбы и др.) путем обдувки
дробью, лучом лазера и т. п.
68. Расчёт жёсткости вала. Упругие перемещения валов оказывают неблагоприятное влияние на работу связанных с ними соединений, подшипников, зубчатых колес и других деталей : увеличивают концентрацию контактных напряжений и износ деталей, снижают сопротивление усталости деталей и соединений, точность механизмов и т. п. Большие перемещения сечений вала от изгиба могут привести к выходу из строя конструкции вследствие заклинивания подшипников. Изгибная и крутильная жесткость валов существенно влияет на частотные характеристики системы при возникновении изгибных и крутильных колебаний. При проектировании валов следует проверять прогибы и углы φ поворота сечений, зависящих от требований, предъявляемых к валу, и особенностей его работы. Допустимые величины φ Максимальный прогиб вала не должен превышать (0,0002… 0,0003) L (L — расстояние между опорами), а допустимый прогиб под колесами составляет: 0,01m — для цилиндрических и 0,005 m — для конических, гипоидных и глобоидных передач ( m — модуль зацепления). Допустимые относительные углы закручивания валов Ө зависят от требований и условий работы конструкции и лежат в пределах 0,20…1° на 1 м длины вала.
69. Общие сведения о подшипниках скольжения. Подшипник скольжения является парой вращения. Состоит из опорного участка вала (цапфы) и собственно подшипника 2, в котором скользит цапфа. Их используют в качестве опор валов и осей в случаях, когда применение подшипников качения затруднено или невозможно по ряду причин: 1)высокие вибрационные и ударные нагрузки; 2) низкие и особо высокие частоты вращения; 3)работа в воде, агрессивных средах, 4)при отсутствии или недостаточном смазывании ; 5)необходимость выполнения диаметрального разъема; 6)отсутствие подшипников качения требуемых диаметров и др. Благодаря бесшумности , указанным выше достоинствам, а также по конструктивным и экономическим соображениям опоры скольжения находят широкое применение в паровых и газовых турбинах, двигателях внутреннего сгорания, центробежных насосах, центрифугах, металлообрабатывающих станках, прокатных станах, тяжелых редукторах и пр. По виду трения скольжения различают: 1)подшипники сухого трения — работают на твердых смазках или без смазки; 2)подшипники граничного (полужидкостного) трения; 3)подшипники жидкостного трения; 4)подшипники с газовой смазкой. По виду воспринимаемой нагрузки подшипники подразделяют на: 1)радиальные — воспринимают радиальную нагрузку; 2)упорные — воспринимают осевые силы ; 3)радиально-упорные — воспринимают радиальные и осевые нагрузки. Обычно их функции выполняют упорные подшипники, совмещенные с радиальными. Цапфу, передающую радиальную нагрузку, называют шипом — при расположении ее в конце вала и шейкой — если она находится в середине вала. Цапфу, передающую осевую нагрузку, называют пятой, а подшипник — подпятником. Рабочая поверхность подшипников и цапф может быть цилиндрической, конической и шаровой формы . Конические и шаровые подшипники применяются редко.
70. Особенности работы подшипников скольжения. Условия работы подшипников скольжения определяются основными параметрами режима работы (удельной нагрузкой р и угловой скоростью ω цапфы), наличием и типом смазочного материала, физико-механическими характеристиками контактирующих поверхностей. Для однотипных подшипников с одинаковым соотношением размеров (диаметра d и длины l цапфы) потери на трение пропорциональны коэффициенту трения f=2Tf/(Frd), где Tf — момент трения в подшипнике; Fr — радиальная сила (опорная реакция). В подшипниках сухого трения коэффициент трения обычно не слишком значительно меняется в зависимости от параметров режима работы. В подшипниках граничного трения влияние параметров режима работы весьма существенно. Коэффициент граничного трения может достигать значений 0,2…0,3. Граничное трение сопровождается износом контактирующих поверхностей. Описанные условия работы типичны для низкоскоростных подшипников с периодической или недостаточной подачей смазки и недопустимы для высокоскоростных подшипников. С увеличением ω коэффициент трения резко уменьшается в связи с переходом трения в полужидкостное и наличием одновременно граничной и жидкостной смазки .Коэффициент полужидкостного трения ниже, чем при граничном трении. Однако режим характеризуется нестабильными условиями смазывания, так как повышение температуры в зоне контакта уменьшает вязкость и вызывает разрушение граничной пленки и повышение коэффициента трения. Поэтому работа подшипника с высокой угловой скоростью в режиме полужидкостного трения также опасна. Начиная с угловой скорости ω=ωкр при которой коэффициент трения f = fmin, вал отходит от подшипника («всплывает»), смещается в направлении вращения, занимая новое положение с меньшим эксцентриситетом цапфы и подшипника. Последующее увеличение приводит к увеличению коэффициента трения в связи с увеличением толщины слоя смазки и ростом гидравлических потерь. При этом вал удерживается на «масляном клине» — осуществляется режим жидкостного трения. Так как непосредственный контакт отсутствует, то трение в подшипнике определяется законами гидродинамики. Коэффициент жидкостного трения не превышает 0,005, и износ практически отсутствует, потери на трение и тепловыделение невелики. Условия смазывания носят устойчивый характер.
Валы и оси Общие сведения
14
ПРИКЛАДНАЯ МЕХАНИКА И
ОСНОВЫ КОНСТРУИРОВАНИЯ
Лекция 8
ВАЛЫ И ОСИ
А.М. СИНОТИН
Кафедра технологии и автоматизации производства
Зубчатые колеса, шкивы, звездочки и другие вращающиеся детали машин устанавливают на валах или осях.
Вал предназначен для поддержания сидящих на нем деталей и для передачи крутящего момента. При работе вал испытывает изгиб и кручение, а в отдельных случаях дополнительно растяжение и сжатие.
Ось – деталь, предназначенная только для поддержания сидящих на ней деталей. В отличие от вала, ось не передает вращающего момента и, следовательно, не испытывает кручения. Оси могут быть неподвижными или вращаться вместе с насаженными на них деталями.
Разновидность валов и осей
По геометрической форме валы делятся на прямые (рисунок 1), коленчатые и гибкие.
1 – шип; 2 – шейка; 3 – подшипник
Рисунок 1 – Прямой ступенчатый вал
Коленчатые и гибкие валы относятся к специальным деталям и в настоящем курсе не рассматриваются. Оси, как правило, изготавливают прямыми. По конструкции прямые валы и оси мало отличаются друг от друга.
По длине прямые валы и оси могут быть гладкими или ступенчатыми. Образование ступеней связано с различной напряженностью отдельных сечений, а также условиями изготовления и удобства сборки.
По типу сечения валы и оси бывают сплошные и полые. Полое сечение применяется для уменьшения массы или для размещения внутри другой детали.
Элементы конструкции валов и осей
1 Цапфы. Участки вала или оси, лежащие в опорах, называются цапфами. Они подразделяются на шипы, шейки и пяты.
Шипом называется цапфа, расположенная на конце вала или оси и передающая преимущественно радиальную нагрузку (рис. 1).
Рисунок 2 – Пяты
Шейкой называется цапфа, расположенная в средней части вала или оси. Опорами для шеек служат подшипники.
Шипы и шейки по форме могут быть цилиндрическими, коническими и сферическими. В большинстве случаев применяются цилиндрические цапфы (рис. 1).
Пятой называется цапфа, передающая осевую нагрузку (рисунок 2). Опорами для пят служат подпятники. Пяты по форме могут быть сплошными (рисунок 2, а), кольцевыми (рисунок 2, б) и гребенчатыми (рисунок 2, в). Гребенчатые пяты применяют редко.
2 Посадочные поверхности. Посадочные поверхности валов и осей под ступицы насаживаемых деталей выполняют цилиндрическими (рисунок 1) и реже коническими. При прессовых посадках диаметр этих поверхностей принимают примерно на 5% больше диаметра соседних участков для удобства напрессовки (рисунок 1). Диаметры посадочных поверхностей выбирают по ГОСТ 6336-69, а диаметры под подшипники качения – в соответствии с ГОСТами на подшипники.
3 Переходные участки. Переходные участки между двумя ступенями валов или осей выполняют:
— с канавкой со скруглением для выхода шлифовального круга по ГОСТ 8820-69 (рисунок 3, а). Эти канавки повышают концентрацию напряжений, поэтому рекомендуются на концевых участках, где изгибающие моменты небольшие;
Рисунок 3 – Переходные участки вала
— с галтелью переменного радиуса (рисунок 3, в), которая способствует снижению концентрации напряжений, а потому применяется на сильно нагруженных участках валов и осей.
Эффективными средствами для снижения концентрации напряжений в переходных участках является протачивание разгрузочных канавок (рисунок 4, а), увеличение радиусов галтелей, высверливание в ступенях большого диаметра (рисунок 4, б).
Рисунок 4 – Способы повышения усталостной прочности валов
Описание конструкции и назначения детали
Дан вал-шестерня – чертеж ДМ-09.01.00.01 (рисунок 1). Вал-шестерня является деталью цилиндрического редуктора привода ленточного конвейера, который был взят из курсовой работы по дисциплине детали машин. Он соединяется с валом двигателя посредствам муфты и служит для передачи движения от двигателя к приводу конвейера. Для соединения вала и полумуфты используется шпоночное соединение и посадка H6/к6.
Валом называют деталь, предназначенную для поддержания установленных на ней шкивов, зубчатых колес, звездочек, катков и т. д., и для передачи вращающего момента.
Форма валов и осей разнообразна и зависит от выполняемых ими функций. Иногда, валы изготавливаются совместно с другими деталями, например, шестернями, кривошипами, эксцентриками. На данном валу установлена шестерня.
По геометрической форме вал является прямым (рисунок 1). Ещё валы бывают кривошипные, коленчатые, гибкие, телескопические и карданные.
Рисунок 1 – Вал-шестерня
Длина вала составляет 332 мм. На валу нарезано 25 зубьев шестерни быстроходной ступени. Ширина шестерни составляет 50 мм, модуль равен 3 мм, делительный диаметр шестерни 75,73 мм. Шестерня взаимодействует с зубчатым колесом соседнего вала. Cлева относительно шестерни расположен буртик для контакта с внутренним кольцом подшипника. Его диаметр 50 мм.
Диаметры участков для установки подшипников равны 45 мм. Участок для установки правого подшипника имеет длину 70 мм, позволяющую установку дистанционного кольца. Длина левого участка для установки подшипника равна 29мм. На границах участков для установки подшипников выполнены канавки для выхода шлифовального круга.
На крайнем участке диаметром 40 мм расположен шпоночный паз под шпонку 12×8×56мм ГОСТ 23360-78. На торцах вала необходимо снять фаску 2мм×45°, для облегчения установки вращающихся деталей и предупреждения травмирования рук.
Требования к точности и шероховатости всех функциональных и не функциональных поверхностей указаны на чертеже. Необрабатываемые поверхности могут сохранять штамповочные уклоны и радиусы.
Материалом для изготовления вала-шестерни служит сталь 40Х ГОСТ 4543-71. В таблицах 1 и 2 показаны химические и механические свойства данной стали.
Таблица 1 – Химический состав стали 40Х ГОСТ 4543-71
Элемент | С | Si | Mn | Ni |
Содержание, % | 0,36-0,44 | 0,17-0,37 | 0,5-0,8 | до 0,3 |
Элемент | S | P | Cr | Cu |
Содержание, % | до 0,035 | до 0,035 | 0,8-1,1 | до 0,3 |
Таблица 2 – Механические свойства стали 40Х ГОСТ 4543-71
HB | [σВ], МПа | [σТ], МПа | [σ-1], МПа |
269-302 | 736-805 | 490-510 | 373 |
[σР], МПа | [σИ], МПа | [τК], МПа | [τС], МПа |
191 | 216 | 162 | 176 |
Подсчет массы и технические условия изготовления детали
При расчете массы детали не будем учитывать канавки, скругления и фаски (рисунок 2). При определении объема шестерни будем использовать делительный диаметр.
Объем участка A:;
Объем участка B:;
Объем участка C:;
Объем участка D:;
Объем участка F:;
Объем участка E:;
Объем шпоночного паза равен половине объема шпонки.
.
Рисунок 2 – Чертеж детали
Полный объем детали:
Плотность стали 40Х: .
Масса детали: .
Конструкция вала в целом является технологичной, т.к. используются только простые поверхности, что не составит трудностей в изготовлении. При разработке единичных рабочих техпроцессов изготовления подобных валов в условиях серийного или массового производства в качестве информационной основы вполне могут быть использованы типовые технологические процессы производства деталей данного класса.