Хромирование — Википедия

Хроми́рование — диффузионное насыщение поверхности стальных изделий хромом, либо процесс осаждения на поверхность детали слоя хрома из электролита под действием электрического тока. Слой хрома может наноситься для декоративных целей, для обеспечения защиты от коррозии или для увеличения твердости поверхности[1].

Деталь, подвергаемая хромированию, как правило, проходит через следующие шаги:
- Очистка для удаления сильных загрязнений.
- Тонкая очистка, для удаления следов загрязнений.
- Предварительная подготовка (варьируется в зависимости от материала основы).
- Помещение в ванну с насыщенным раствором и выравнивание температуры.
- Подключение тока и выдержка до получения нужной толщины
Используемые при хромировании реагенты и отходы процесса чрезвычайно токсичны, в большинстве стран этот процесс находится под строгим регулированием.
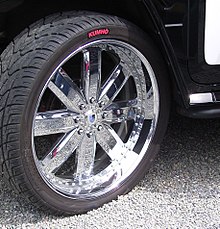
В промышленности хромирование используется для снижения трения, повышения износостойкости, повышения коррозионной стойкости. Этот процесс обеспечивает повышенную устойчивость стали к газовой коррозии (окалиностойкость) при температуре до 800 °C, высокую коррозионную стойкость в таких средах, как вода, морская вода и азотная кислота. Хромирование сталей содержащих свыше 0,3—0,4 %С, повышает также твёрдость и износостойкость. Твердость хрома составляет от 66 до 70 HRC. Толщина хромового покрытия обычно составляет от 0,075 до 0,25 мм, но встречаются и более толстые, и более тонкие слои. Поверхностные дефекты при хромировании усиливаются и поверхность подлежит последующей обработке, так как хромирование не дает эффекта выравнивания. [2]
Хромирование деталей пар трения, работающих в жёстких условиях (поршневые кольца, зеркало цилиндра ДВС), как показала практика, требует создания покрытия с порами сравнительно крупного размера, способными удерживать масло. Без этого противоизносные и противозадирные свойства покрытия даже хуже, чем у нехромированной детали. Для расширения естественных канальцев на поверхности покрытия используется кратковременное электрохимическое травление обратным током (деталь-анод).
Хромирование используют для деталей паросилового оборудования, пароводяной арматуры, клапанов, вентилей патрубков, а также деталей, работающих на износ в агрессивных средах.
Чёрное хромовое покрытие, полученное в ванне специального состава (не путать с декоративной виниловой плёнкой), отличается большим светопоглощением в сочетании с гладкостью и используется там, где необходимо отсутствие бликов (оптические приборы, автомобильные детали в поле зрения водителя и т.п.)
В отдельных случаях хромирование применяется для ремонта деталей путём наращивания сопрягаемой поверхности в случае прослабленной посадки. В настоящее время может использоваться как «гаражная» или «холодная» альтернатива плазменному напылению металла, аналогичного материалу детали.
Типичными являются следующие растворы для хромирования:
- Шестивалентный хром, чей основной ингредиент — хромовый ангидрид.
- Трехвалентный хром, чей основной ингредиент — Сульфат хрома или хлорид хрома. Ванны с трехвалентным хромом используются довольно редко из-за ограничений, накладываемых на цвет, яркость и толщину покрытия.[источник не указан 3828 дней]
Типичное содержание ванны с шестивалентным хромом:
Нарушение состава и температуры ванны легко приводит к разнообразным дефектам покрытия (пятна, матовость, отслаивание), разрушению свинцовой футеровки ванны. При превышении плотности тока на краях и углах деталей могут образовываться наросты-дендриты разнообразной формы — «сувениры из гальванического цеха».
Нанесение хрома на самопассивирующиеся металлы (алюминий, титан) затруднено и требует тщательной предварительной очистки травлением или производится по подслою другого металла (медь, никель). Может потребоваться подключение источника тока до помещения детали в ванну.
Хромирование стали по подслою улучшает антикоррозионные свойства покрытия, перекрывая естественные микропоры хрома; в то же время подслой никеля образует с хромом гальваническую пару и может корродировать сам по себе вплоть до отслаивания хрома. Для закрытия пор хрома может применяться насыщение поверхности плёнки лаками или маслами, в том числе при повышенной температуре или под вакуумом.
Полученный на деталях слой хрома, как правило, сравнительно хрупок, и для улучшения его свойств может применяться термообработка в виде длительной выдержки при температуре порядка 200°C.
Электролитическое хромирование пластмасс производится по предварительно напылённому или осаждённому слою другого металла, например, меди.
После того, как шестивалентный хром в 90-е годы XX века был признан канцерогеном, в различных странах началась разработка методик его замены. Так, в США и Канаде начала работу Hard Chrome Alternаtive team, HCAT. В 2003 году была принята и в 2006 году вступила в силу директива RoHS, которая существенно ограничила применение хромирования в Европе. Результатом стала замена хромирования на другие способы обработки, например, высокоскоростное газопламенное напыление во многих применениях.
- Ю.М. Лахтин, В.П. Леонтьева. Материаловедение. — М.: Машиностроение, 1990.
Гальваническое хромирование: суть процесса, основы проведения
Гальваническое хромирование — это один из способов создания на поверхности изделий тонкого устойчивого слоя из чистого хрома, который почти в два раза тверже железа, имеет приятный серебристый цвет и отлично полируется. Хромовые покрытия применяют в защитных и в декоративных целях.
Гальваническому хромированию подвергают поверхности трения для создания устойчивого к коррозии антифрикционного слоя, который к тому же хорошо удерживает масло. Этот металл имеет прекрасное сцепление со сталью, никелем и медью, а также практически не окисляется и не отслаивается в процессе эксплуатации. Помимо прочего, хромовая гальваника применяется при изготовлении стойких к атмосферным воздействиям оптических отражателей, которые по своим качествам ничем не уступают амальгамированным.
Одной из главных особенностей гальванического хромирования является работа с пассивным анодом, т. е. покрывающий деталь хром поступает не из анодного металла, а из раствора хромовых кислот, что требует постоянной регенерации электролита. А основной недостаток этого технологического процесса — высокая токсичность соединений хрома и связанные с этим повышенные требования к системам промвентиляции, утилизации электролита и водоочистки.
Суть гальванического хромирования металла
В большинстве гальванических процессов источником покрывающего металла является анод. В отличие от этого при хромировании анионы возникают непосредственно из электролита, основой которого является раствор хромовых кислот, образующихся при растворении хромового ангидрида в воде. В такой технологии катодом обычно является обрабатываемая деталь, а в роли нерасходуемого пассивного анода выступают пластины или облицовка ванны, выполненные из инертного к кислотам электролита металла. Пассивные аноды в хромовой гальванике обычно изготавливают из свинца или его сплавов (с оловом и сурьмой). Хромовая кислота обладает сильными коррозионными свойствами, поэтому при производстве оборудования для хромирования применяют кислотостойкие материалы.

Выделение анионов хрома в объеме электролита в процессе хромирования происходит неравномерно, поэтому гальванические ванны оснащают специальными устройствами, обеспечивающими постоянную подачу перемешанного электролита в зону катода (к поверхности металла хромируемой детали). Кроме того, в связи с постоянным убыванием хрома электролит необходимо периодически регенерировать, добавляя в него хромовый ангидрид и расходуемые в процессе хромирования реагенты. Вид поверхности и механические свойства хромового покрытия напрямую зависят от компонентов электролитического раствора, степени его нагрева и плотности тока.
Варьируя эти показатели, можно добиться различных видов поверхности хромированного металла: от молочного и матового до зеркально-блестящего, – а также широкого диапазона значений твердости, плотности и пористости осажденного хрома.
Методика хромирования металла своими руками
Тому, кто собирается освоить хромирование металла в бытовых условиях, в первую очередь необходимо четко усвоить, что этот химический процесс связан с применением особо токсичных веществ, опасных для здоровья и наносящих вред природной среде. Поэтому ни о какой гальванике в домашних условиях не может быть и речи. Для хромирования необходимо подобрать нежилое помещение и по возможности оборудовать его хотя бы какой-нибудь вентиляцией. Также стоит заранее позаботиться об утилизации отработанного раствора и промывочной воды. Все работы следует выполнять в спецодежде и с применением средств индивидуальной защиты, используемых на химпроизводствах.
Оборудование для хромирования металла достаточно несложно изготовить самому. В большинстве случаев в его состав входят:
- стеклянная или пластиковая емкость;
- теплоизоляция и герметичная крышка рабочей емкости;
- нагревательный элемент с терморегулятором;
- источник питания мощностью 1 кВт и напряжением 10÷12 В;
- свинцовый анод с клеммой;
- приспособление для подвешивания и зажим для крепления детали с клеммой;
- емкости для травления и промывки, провода, подставка и прочее второстепенное оборудование.
Компоновка такого комплекта для хромирования зависит от размеров и особенностей входящих в него элементов и делается «на глазок», с дополнениями и изменениями по ходу изготовления. О токовых режимах лучше заранее почитать в специализированных изданиях или пообщаться со знающими людьми на профильных форумах. Там же можно обсудить вопрос влияния хрома на свойства стали и других металлов, т. к. у хромированной детали несколько изменятся механические характеристики.
Подготовка поверхности к хромированию
Подготовка металла к хромированию ничем не отличается от приготовлений к любому другому гальваническому процессу. В первую очередь необходимо убрать остатки покрытий и ржавчину с хромированной поверхности. Первое выполняется с помощью металлических щеток и наждачной бумаги или же (если есть такая возможность) абразивоструйной обработкой. Для удаления ржавчины с металла можно также использовать механические методы, но лучше воспользоваться ортофосфорной кислотой.
Хромирование алюминия и его сплавов требует особого подхода к предварительной обработке поверхности этих металлов, т. к. на них всегда присутствует устойчивая оксидная пленка. Последовательность их подготовки к гальванике выглядит так:
- Промывка всей поверхности металла в бензине.
- Удаление следов бензина в горячей мыльной воде.
- Травление в смеси азотной и плавиковой кислот (соотношение пять к одному).
- Ополаскивание в холодной воде.
- Помещение изделия в гальваническую ванну.
Все операции следует выполнять в непрерывной последовательности, а погружать металл в электролит нужно под током.
Приготовление электролита
Основными компонентами всех электролитов для хромирования металлов являются хромовый ангидрид и серная кислота. В промышленных гальванических растворах применяют различные добавки, но для домашнего мастера на первое время достаточно этих двух. При приготовлении электролита сначала в воде разводится серная кислота из расчета 1.5–2.5 г/л, а затем добавляется хромовый ангидрид в количестве 150–250 г/л. Точную пропорцию можно подобрать только экспериментально, оценивая результат хромирования поверхности металла (см. также ниже о возможных дефектах).
Возможные дефекты
При осмотре всех плоскостей металла после гальванического хромирования могут быть обнаружены специфические недостатки, которые чаще всего связаны с составом электролита и плотностью тока, но могут иметь и другие причины. Если хром не оседает на металл, то это может быть связано с недостаточной плотностью тока, избытком серной кислоты, завышенной температурой раствора или окислением анода. Если хромовое покрытие отслаивается от металла, то причиной этого может быть плохая очистка его поверхности и колебание токовых параметров в процессе хромирования. При превышении плотности тока на выступающих частях детали могут образовываться наросты, а поверхность хромированного металла становится матовой и неровной. При слишком маленькой плотности тока покрытие становится жестким и имеет «молочный» вид.
При гальваническом хромировании также важно пространственное положение детали. Оно должно обеспечивать свободный уход водорода, образующегося на поверхности металла, т. к. скопление это газа приводит к образованию неровностей и каверн.
Опасность для здоровья
При хромировании металлов основная опасность для здоровья персонала и окружающей среды исходит от хромового ангидрида (оксид шестивалентного хрома), который является главным компонентом во всех электролитах, а при растворении в воде образует не менее опасные хромовые кислоты. Все эти реагенты являются канцерогенами и очень токсичны (относятся к первому классу опасности). Оксиды и соли хрома малолетучи, но при использовании горячих электролитов могут захватываться парами воды. Другими токсичными веществами, образующимся в процессе гальванического хромирования, являются хроматы свинца и сульфаты бария.
А как вы относитесь к хромированию металлов в домашних условиях? Ведь в Интернете размещено множество статей, описывающих, как легко и просто это делается даже без особых навыков. Выскажите, пожалуйста, свое мнение в комментариях к этой статье.
Технологический процесс хромирования
Технологические операции при ремонте (восстановлении) деталей хромированием выполняют в следующей последовательности.
Механическая обработка. Поверхности деталей, подлежащие хромированию, шлифуют до выведения следов износа и получения необходимой геометрической формы.
Промывка деталей в органических растворителях и протирка ветошью. В качестве растворителей применяют бензин, керосин, трихлорэтан, бензол и др.
Монтаж деталей на подвеску. Необходимо следить, чтобы детали одинаково отстояли от поверхности анода. Ванну следует загружать однородными деталями, укрепленными на одинаковых подвесках. Подвески и контакты должны быть изготовлены из одинаковых материалов. Контактные крючки рекомендуется изготавливать из бронзы и меди. В качестве материала для подвесок, применяют сталь, сечения подвесок рассчитывают, исходя из плотности тока 0,7… 1,0 А/мм2. Ежедневно аноды очищают от окислов и налета электролита.
Обезжиривание. Рекомендуется применять электролитическое обезжиривание в растворе следующего состава: едкий натр (NaOH)—30… 50 г/л; кальцинированная сода (iNa2C03)—25…30 г/л и жидкое стекло (Na2Si03) — 10 … 20 г/л.
Температура электролита — 60… 70°, плотность тока — 5….15 А/дм2. Время выдержки на катоде — 2… 3 мин, а на аноде — 1…2 мин. После обезжиривания детали сначала промывают горячей водой (60… 80°), а затем холодной. Обезжиривание считается законченным, если после промывки вода равномерно смачивает поверхность. После обезжиривания производится изоляция1 поверхностей, не подлежащих хромированию. Для изоляции можно применять перхлорвиниловый лак, лак АК-20, целлулоид,, винипласт, плексиглас, хлорвиниловые трубки или хлорвиниловую» изоляционную ленту.
Декапирование — это процесс обработки деталей в хромовом* электролите, состоящем из 100 г хромового ангидрида (СгОз) и 2…3 г серной кислоты (H&SO4) на 1 л воды.
Декапирование (травление) стальных деталей проводят в течение 30… 90 с при плотности тока 25… 40 А/дм2. А для деталей из серого чугуна лучшие результаты, в смысле прочности сцепления, достигаются при плотности тока 20… 25 А/дм2 и продолжителыюсти декапирования 25… 30 сек. Температура электролита во всех случаях должна быть 55… 60 °С.
Процесс хромирования. После анодного декапирования детали загружают в ванну хромирования и прогревают их при выключенном токе в течение 5… 6 мин, а затем дают полный ток согласно режиму хромирования. При хромировании чугунных деталей вначале в течение 3… 5 мин дают «толчок тока» при плотности, в 2…2,5 раза превышающей выбранную по режиму. Колебания температуры электролита могут быть в пределах ±1 °С. Не допускаются перерывы тока в процессе электролиза, так как они вызывают отслаивание хромового покрытия. Продолжить процесс после перерыва тока можно, если хромируемую поверхность подвергнуть анодному травлению при плотности тока 25… 30 А/дм2 в течение 30… 40 с, а затем изменить направление тока. В этом случае осаждение хрома следует начинать при катодной плотности тока 20… 25 А/дм2 и постепенно увеличивать до нормальной.
Аноды для хромирования изготавливают из чистого свинца или сплава, состоящего из 92…93% свинца и 7… 8% сурьмы. Аноды из чистого свинца в большей степени покрываются нерастворимой и непроводящей пленкой хромовокислого свинца, чем аноды из сплава свинца и сурьмы. В большинстве случаев аноды изготавливают плоскими и цилиндрическими. При хромировании деталей сложной конфигурации очертания анода определяются формой катода. Расстояние между анодами и деталями рекомендуется делать 30… 35 мм, но не более 50 мм. Расстояние деталей от днища ванны должно составлять не менее 100… 150 мм, а от верхнего уровня электролита — не менее 50… 80 мм. Уровень электролита должен быть ниже верхних кромок ванны на 100…150 мм. При завешивании деталей в ванну необходимо, чтобы все участки анодов были одинаково удалены от противоположных участков катода. При этом толщина слоя хрома откладывается равномерно по всей поверхности детали.
Глубина погружения анодов и деталей (катодов) в ванну должна быть одинаковой, так как при различной глубине на краях хромируемых деталей образуются утолщения, искажающие форму. Скорость осаждения слоя хрома при плотности тока 40… 100 А/дм2 составляет 0,03… 0,06 мм/ч.
По окончании процесса хромирования детали выгружают из ванны и вместе с подвесками промывают в холодной воде (в сборнике электролита) 15… 20 с. Окончательно детали моют в холодной проточной воде.
Обработка после покрытия. Промытые и очищенные от изоляции детали иногда подвергают термической обработке при температуре 150—200°С в течение 2…3 ч, а затем механической.
Для шлифования применяют круги мягкие или средней твердости с размером зерна от 60 до 120. Шлифование ведут при интенсивном охлаждении жидкостью и при скорости круга 20…30.м/с и выше. Скорость вращения детали—12…20 м/мин.
Режимы электролиза. Процесс осаждения хрома и свойства хромовых покрытий зависят от режима, при котором осаждается хром на поверхности металла, т. е. от катодной плотности тока и температуры электролита. Наиболее ясное представление о примерных границах режимов электролиза, обеспечивающих получение серого, блестящего и молочного осадков хрома, дает диаграмма плотности тока и температуры (DK—t), изображенная на рисунке 19.
Серый осадок хрома появляется на катоде при низких температурах электролиза (35…50 °С) и широком диапазоне плотностей тока. Осадки блестящего* хрома обладают высокой твердостью (6000… 9000 Н/мм2), высокой износостойкостью и меньшей хрупкостью.
Рис. 19. Зоны хромовых осадков.
Молочный хром получается при более высоких температурах, электролита (выше 70 °С) и широком интервале плотностей тока. Молочные осадки отличаются пониженной твердостью (4400..-6000 Н/мм2), пластичностью и повышенной коррозионной стойкостью.
Пористое хромирование. Пористое хромирование применяется при ремонте деталей, работающих на трение в паре с различными металлами и сплавами при высоких удельных давлениях и окружных скоростях или при повышенных температурах. К таким деталям относятся гильзы цилиндров двигателей внутреннего сгорания, коленчатые валы и др.
Пористые хромовые покрытия можно получать механическим,, химическим и электрохимическим способами.
При механическом способе на поверхность детали до хромирования наносят углубления в виде пор или каналов. Такую подготовку обеспечивают накаткой специальным роликом, дробеструйной обработкой и другими способами. После хромирования воспроизводятся неровности, полученные при подготовке.
Химическим способом получают пористость путем травления поверхности в соляной кислоте.
Наибольшее распространение получил электрохимический способ получения пористого хрома. Этот способ заключается в анодной обработке хромированных деталей в электролите того же состава. В зависимости от режимов хромирования пористость хромовых покрытий бывает двух типов — канальчатая и точечная.. При ремонте гильз цилиндров, втулок, коленчатых валов и подобных им деталей применяется канальчатый тип пористости. Такук> пористость и наименьший износ в условиях трения можно получить при хромировании в электролите, состоящем из 250 г Сг03 и 2,5 г h3S04 на 1 л воды, при температуре электролита ¦60+1 °С и катодной плотности тока 55… 60 А/дм2. Травление ведут при плотности анодного тока 35 …45 А/дм2 в течение 8 мин в том же электролите.
Точечная пористость образуется при хромировании в универсальном электролите при плотности тока 45… 55 А/дм2 и температуре 50… 55 °С. Анодную обработку проводят так же, как и при канальчатой пористости, т. е. при плотности тока 35… 45 А/дм2 в течение 8 мин.
Хромирование в саморегулирующемся электролите. В последнее время разработан новый хромовый электролит, называемый скоростным саморегулирующимся, его состав: хромовый’ ангидрид — 225… 300 г/л, кремнефтористый калий — 20 г/л и сернокислый стронций — 6 г/л.
В таком электролите выход по току при хромировании составляет 17… 22%. Саморегулирующимся он назван потому, что при электролизе в нем автоматически поддерживается необходимая концентрация анионов, вводимых в хромовый электролит. Это происходит в результате избыточного количества труднорастворимых солей кремнефтористого калия и сернокислого стронция, растворимость которых изменяется в зависимости от концентрации хромового ангидрида и температуры электролита.
Чтобы получить износостойкое покрытие в саморегулирующемся электролите, рекомендуют соблюдать следующие режимы хромирования: плотность тока 50… 100 А/дм2, температура электролита 45… 55°С. Молочные осадки можно получить при температуре электролита 55… 70 °С и плотности тока 20… 35 А/дм2. Микротвердость покрытий из саморегулирующегося электролита составляет 3000… 13 000 Н/мм2.
Недостаток такого электролита — сильное взаимодействие его со сталью и другими металлами, в результате чего происходит растравливание обрабатываемых поверхностей. Поэтому загружать детали в ванну необходимо только при включенном токе. Аноды для хромирования в саморегулирующемся электролите рекомендуется применять из сплава: 90% свинца и 10% гост олово. Чтобы приготовить саморегулирующийся электролит, в ванне хромирования растворяют нужное количество хромового ангидрида и доливают воду до рабочего уровня. Предварительно хромовый ангидрид подвергают анализу на содержание серной кислоты, которую удаляют из электролита путем добавления в него углекислого бария или стронция. На 1 г серной кислоты вводят 2,2… 2,3 г углекислого бария или 1,53 г углекислого стронция. После осаждения серной кислоты в электролит вводят нужное количество сернокислого стронция и кремнефтористого калия и нагревают до температуры 50…60°С. Нагревание длится 15… 16ч при периодическом перемешивании через каждые 2… 3 ч. После этого электролит готов к эксплуатации.
Корректируют электролит путем систематического добавления хромового ангидрида. Вместе с хромовым ангидридом вводят углекислый стронций. Кремнефторид калия и сернокислый стронций в количестве 1 г/л добавляют, когда поверхность отхромированных деталей приближается к 1 м2.
Контроль хромовых покрытий. В производственных условиях качество покрытий следует проверять внешним осмотром и замером размеров хромированных поверхностей. При внешнем осмотре необходимо обращать внимание на блеск, отслоение и плотность осадка, равномерность и отсутствие шелушения и другие видимые дефекты. Дефекты покрытий получаются в результате неисправностей в работе ванн хромирования, например отслаивание покрытия возникает в результате недостаточного обезжиривания и декапирования, а также при наличии перерывов тока в процессе хромирования. Шелушение осадков появляется при недостаточном контакте детали с подвеской или при повышенной плотности тока. Неравномерное покрытие может быть при образовании пленки хроматов свинца на анодах, недостатке серной кислоты, избытке трехвалентного хрома. Во избежание перечисленных выше дефектов, необходимо откорректировать электролит и устранить другие неполадки в работе ванн хромирования.
Оборудование. Схема расположения оборудования участка восстановления деталей хромированием приведена на рисунке 20.
Источники тока — выпрямители с напряжением 12 В ВАКГ-12/6-3000, ВАГГ-12/600М, ВАС-600/300 и другие, а также низковольтные генераторы АНД 500/250, 750/375, 1000/500, 1500/750. Ванны для гальванического участка изготавливают из листовой стали толщиной 4… 5 мм. Облицовка для ванн промывки и обезжиривания не требуется. Внутреннюю поверхность ванны хромирования облицовывают свинцом.
Рис. 20. Расположение оборудования
на участке восстановления
деталей хромированием:
1 — выпрямитель; 2 — электрощитг;
3 — ванна для электрохимического обезжиривания;
4 — ванна для горячей промывки;
5 — ванна для холодной промывки;
6 — ванна для декапирования;
7 — ванна для хромирования;
8 — ванна для улавливания электролита;
9 — шкаф сушильный; 10— стеллаж ремфонда;
11 — электротельфер;
12 — сборник-нейтрализатор;
13 — стол для монтажа и демонтажа.
Материалы. Ориентировочный расход материалов в граммах на 1 дм2 восстановленной поверхности для средней толщины покрытия 0,1 мм при хромировании в универсальном электролите приведен в таблице 13.
Себестоимость восстановления 1 дм2 поверхности хромированием в универсальном электролите при толщине покрытия 0,1 мм ориентировочно составляет 44,8 коп., 0,2 мм — 52,0 коп., 0,3 мм—-58,6 коп.
Электролитическое железо имеет светло-серый цвет, обладает достаточно высокой твердостью и износостойкостью. Химический состав электролитического железа зависит от состава исходных материалов, используемых при электролизе.
При обычном осаждении с применением стальных растворимых анодов содержание примесей в покрытиях находится в пределах: 0,035 …0,06% С; 0,03 …0,05% S; 0,05 …0,01% Р, 0,0009… 0,023% Si; до 0,01% Мп.
В электролитических осадках железа имеются также примеси таких металлов, как Mg, Со, Ni и другие, обусловленные содержанием этих металлов в анодах и электролитах. Кроме этого, электролитическое железо содержит значительное количество водорода, выделяющегося на катоде вместе с железом. Атомный вес железа 55,85 г. Электрохимический эквивалент 1,042 г/А-ч.
Составы электролитов. На ремонтных предприятиях наибольшее распространение для железнения получили горячие хлористые электролиты, состоящие из двух компонентов: хлористого железа и соляной кислоты. В ремонтной практике чаще всего применяют четыре вида хлористых электролитов, отличающихся концентрацией железа.
Малоконцентрированный электролит содержит 200 …250 г/л хлористого железа (FeCl2-4h30). При температуре 60… 80 °С и плотности тока 30… 50 А/дм2 электролит обеспечивает получение плотных, гладких мелкозернистых осадков железа с твердостью 4500… 6500 Н/мм2, толщиной 1,0… 1,5 мм. Выход железа по току составляет 85… 95%. Скорость осаждения железа равна 0,4… 0,5 мм/ч на сторону. Электролит допускает колебание кислотности при электролизе от 0,8 до 1,5 г/л, которое незначительно отражается на механических свойствах покрытий. Недостатком этого электролита является постепенное увеличение концентрации железа в процессе электролиза в результате несоответствия между скоростью растворения анодов и скоростью осаждения железа на катоде, что вызывает затруднения при обслуживании ванны железнения.
Среднеконцентрированный электролит оптимальной концентрации содержит 300…350 г/л хлористого железа (FeCl2-4h30). Катодный выход железа из этого электролита при температуре 75 °С и плотности тока 40 А/дм2 составляет 96%. В этом электролите анодные и катодные выходы железа по току становятся примерно одинаковыми, концентрация железа остается почти неизменной и электролит длительное время по концентрации железа не требует корректировки. В настоящее время этот электролит нашел широкое применение на ремонтных предприятиях.
Среднеконцентрированный электролит содержит 400 …450 г/л хлористого железа. Электролит используется для восстановления деталей, имеющих достаточно высокие износы и сравнительно невысокую твердость. Электролит дает возможность получать гладкие плотные покрытия толщиной до 2 мм и твердостью 2500… 4500 Н/мм2. Электролит также находит применение для восстановления посадочных отверстий в корпусных, деталях.
Высококонцентрированный электролит содержит 600… 680 г/л хлористого железа. Электролит при температуре 95… 105°С и плотности тока 5…20 А/дм2 позволяет получать мягкие (120… 200 кг/мм2), вязкие покрытия толщиной 3… 5 мм..
Электролиты более высокой концентрации рекомендуется применять в случаях, когда к восстанавливаемым деталям не предъявляются повышенные требования по твердости рабочих поверхностей.
За последнее время разработаны холодные электролиты, позволяющие применять более высокие плотности тока и обеспечивающие высокую производительность процесса.
Хлористый марганец МпС12-4Н20 Аскорбиновая кислота Двухлористое железо FeCl2-4h30 Хлористый марганец МпС12-4Н20 Хлористый калий КС1 (или) NaCl Аскорбиновая кислота Двухлористое железо FeCl2*4h30 Сернокислое железо FeS04*7h30 Двухлористое железо FeCl2-4h30 Метилсульфатное железо Fe (Ch4OSO3) 2*4Н20
Хлористые электролиты без добавок, приведенные в таблице* позволяют получать качественные износостойкие покрытия толщиной 0,6… 1,0 мм и обеспечивать восстановление широкой номенклатуры изношенных деталей до нормальной работоспособности и номинальных размеров. Электролит, в состав которого» входят двухлористое железо и йодистый калий, обеспечивает по-пучение качественных осадков, железа’ при условии применения асимметричного переменного тока.
Присутствие аскорбиновой кислоты в электролитах позволяет вести электролиз в широких пределах значений pH от 1,8 до 6,0, что значительно упрощает регулирование кислотности электролита. Электролит, состоящий из двухлористого железа и метил-сульфатного железа, по сравнению с хлористым менее агрессивен и более устойчив к окислению. Покрытия, полученные из этого электролита, имеют меньшее количество трещин, обладают более равномерной структурой.
Приготовление и корректирование электролита. Для приготовления хлористого электролита используют двухлористое железо (Fe€l2-4h30).
Соляная кислота (НС1) применяется в виде водного раствора разной концентрации с плотностью от 1,14 до 1,20. Приготовление электролита производится в следующем порядке. В ванну заливают проточную или дистиллированную воду комнатной температуры и добавляют соляную кислоту из расчета 0,5 г/л воды. В подкисленную воду засыпают двухлористое железо, выдерживая требуемую концентрацию, и перемешивают до полного растворения. После растворения двухлористого железа электролит должен отстояться в течение 1 … 2 ч, пока не примет светло-зеленый цвет. Затем электролит проверяют на кислотность. Нормальная кислотность должна быть pH 0,8… 1,2. При необходимости добавляют недостающее количество кислоты в соответствии с ее плотностью, приведенной ниже.
Плотность кислоты, г/см3 1,14 1,15 1,16 1,17 1,18 1,19 1,20 Количество кислоты, г/л 20 19 18 17 16 15 14 Количество кислоты, см*/л……. 18 16,6 15,5 14,6 13,6 12,6 11,6
Приготовленный таким образом электролит следует проработать током при плотности 30 А/дм2 и соотношение поверхностей анодов и катодов Sa : SK = 2 : 1 в течение двух часов.
Удельный вес электролита (плотность) г/см8 1,12 1,15 1,17 1,20 1,23 1,26 1,29 1,32 1,35
Концентрация железа, г/л … 200 260 300 350 400 450 500 550 600.
Контроль кислотности электролита можно осуществлять с помощью индикаторной бумаги «Рифан» с pH 0,3 …2,2 или потенциометров ЛПУ-01, ЛПМ-60.
Хромирование – особенности технологии и методов металлизации хромом + Видео
1 Особенности металлизации хромированием
Несмотря на цивилизованность современного человека, он, как и его предки много веков назад, любит красивые блестящие вещи. Блестящие детали кузовов автомобилей и мотоциклов, хромированные аксессуары в ванных комнатах и кухнях, золоченые и посеребренные статуэтки, оцинкованные покрытия домов — эти красивые вещи становятся с каждым годом все востребованнее.
Процесс металлизации, в зависимости от наносимого металла, бывает таким:
- покрытие цинком;
- хромирование;
- алитирование, нанесение алюминия.
Металлизация цинком применяется для улучшения антикоррозийных характеристик стальных и металлических изделий и конструкций, что увеличивает их срок службы.
Металлизация изделий
Рекомендуем ознакомиться
Алитирование применяют для придания высоких антикоррозионных свойств оборудованию, работающему при высоких (до 900 °С) температурах. Это детали и механизмы, используемые для крекинга газа и нефти, элементы газовых турбин, печная арматура и другое оборудование.
Хромирование металлических и других поверхностей применяют для получения красивых декоративных покрытий. С помощью технологии металлизации хромом устраняют небольшие дефекты на поверхностях деталей и улучшают свойства основного материала. Улучшаются следующие характеристики:
- повышение антикоррозийных свойств;
- увеличение твердости металла;
- улучшение защитных характеристик от эрозии;
- повышение жаропрочности;
- усиление износостойкости;
- улучшение внешнего вида;
- возможность получения покрытий с заданными характеристиками.
2 Технология хромирования металлов
Нанесение слоев хрома на металлические поверхности называется химическим хромированием. Покрытие хромом выполняют для декоративности деталей и улучшения функциональных характеристик изделий. Процесс хромирования выполняется следующими методами:
- Гальванический метод нанесения хромированного покрытия.
- Химический способ.
- Нанесение слоев хрома напылением.
Гальваническое хромирование
Нанесение хрома на поверхности деталей гальваническим методом бывает 2 видов: диффузное и электролитическое. Для ведения обоих видов гальваники необходимо иметь специальные резервуары с кислотоупорным покрытием, оборудованные водяными рубашками.
Электролитический метод
Процесс электролитического нанесения хрома основан на методе электролиза металлов. Суть его состоит в прохождении электрического тока через электролит. Электролит представляет собой раствор, в который входят соли хрома, кислота или щелочь. При прохождении электрического тока из раствора хромового ангидрида и серной кислоты выделяются катионы хрома, которые осаждаются на обрабатываемой поверхности.
Гальванический процесс хромирования ведут при следующих средних параметрах:
- хромовый ангидрид — 250 г/л;
- серная кислота — 2,5 г/л;
- температура — 50 °С для декорирования деталей и 55-60 °С для получения функциональных поверхностей;
- плотность тока — 25 А/дм² для декорирования и 60 А/дм² — получается функциональная хромируемая поверхность.
Гальваническое хромирование
Качественная гальваника зависит от температуры электролита и плотности тока. Эти параметры влияют на внешний вид и характеристики нанесенного слоя.
Важно помнить: увеличение температуры снижает выход хрома по току, увеличение плотности тока увеличивает выход хрома по току.
Низкая температура технологического процесса и постоянная плотность тока дают серое покрытие, неизменная плотность тока и высокие температуры дают молочный оттенок покрытия.
Диффузный метод
Термическая обработка стали хромированием придает поверхности материала улучшенные свойства: прочность, твердость, вязкость, упругость, износостойкость, жаро- и коррозионную стойкость. При определенных температурах на поверхность обрабатываемых деталей воздействуют реагенты, и методом диффузии поверхностный слой насыщается хромом. Метод диффузии применяется для насыщения поверхностного слоя кремнием, углеродом, азотом, алюминием.
Термо хромирование порошковое проводят смесями, включающими в себя феррохром и шамот. Смесь смачивается соляной кислотой. Другой вид обработки методом диффузии — конденсация паров хлорида хрома CrCl₂.
Химическая металлизация
Хромирование металлов и диэлектриков проводят химическим способом. Реагенты для проведения метода:
- хлористый хром;
- гипофосфат натрия;
- лимоннокислый натрий;
- уксусная ледяная кислота;
- 20 % раствор едкого натра;
- вода.
Реагенты для химической металлизации
Реакцию ведут при температуре 80 °С. Перед нанесением хромового покрытия на стальные детали на них предварительно наносят слой меди. По окончании процесса обработанные изделия моются в воде и тщательно высушиваются. Применяя кислощелочной раствор, проводят химическую металлизацию диэлектриков.
Еще один вид химической металлизации — вакуумное хромирование или PVD-процесс. При этом методе происходит конденсация паров хрома на поверхности обрабатываемых деталей в вакуумных камерах. В безвоздушном пространстве установки нагревают металл до температуры испарения, и он в виде тумана оседает на поверхность изделия. Слой металла настолько тонкий, что его покрывают лаком для защиты от царапин. Этим методом проводят хромирование алюминия.
Каталитическое хромирование
Каталитическое напыление основано на реакции «серебряного зеркала». Реагентами в этом процессе выступают комплексные соли серебра в щелочных растворах аммиака. В качестве восстановителя применяют растворы инвертного сахара, гидразина или формалина.
Одновременное напыление серебра и восстановителя образует на обрабатываемой поверхности белоснежное зеркальное металлическое покрытие.
Каталитическое напыление
Данное покрытие характеризуется высокой отражательной способностью. Следующий этап каталитического напыления — нанесение защитных лаков с добавлением красящего светостойкого тонера хром. Тонер хром получают смешиванием фиолетового, синего и черного цветов в соотношении 3:1:1.
Технология хромирования реакцией «серебряного зеркала» включает следующие процессы:
- Анализ и подготовка материала, поверхность изделия очищается, промывается, для улучшения адгезии поверхность шлифуется шлифовальной бумагой зернистостью Р500-600.
- Нанесение глянцевой основы. На подготовленную поверхность наносят черную базу. Черное глянцевое покрытие позволит исключить желтизну зеркальной поверхности. Режимы сушки нанесенных лаков: при температуре 20-25 °С, без применения сушильного оборудования — 8 часов, в окрасочно-сушильных устройствах при температуре 60 °С — 45 минут.
- Сушка изделий.
- Травление поверхности деталей для лучшей адгезии серебра и промывание дистиллированной водой.
- Процесс сенсибилизации. Сенсибилизация — обработка поверхности активатором, в результате чего на ней появляется защитная пленка.
- Металлизация поверхности изделия серебром.
- Нанесение защитного лака. Защищает обработанные поверхности от потускнения и механического износа.
3 Гидрофобизация хромовых поверхностей
Гидрофобизация — процесс уменьшения способности материала увлажняться, смачиваться водой или водными растворами. При этом сохраняются характеристики паро- и газопроницаемости материала. Гидрофобизацию проводят с помощью обработки хромовых поверхностей растворами солей жирных кислот. Молекулы кислоты адсорбируются на обрабатываемой поверхности и препятствуют проникновению капель воды в хромированный слой, что улучшает его антикоррозионные свойства.